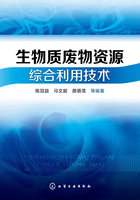
3.3 生物质燃油制备与利用
生物质热裂解是指生物质在完全没有氧或缺氧条件下加热,产物经快速冷却,使中间液态产物分子在进一步断裂生成气体之前冷凝,从而得到高产量的生物质液体油。生物质热解的最终产物包括生物油、木炭和可燃气体。三种产物的比例取决于热裂解工艺和反应条件。目前,以生物油为主要产物的热裂解技术已经成熟,并进入了示范及商业化阶段。
3.3.1 生物质热解方法
按热解温度来分,热裂解技术可以分为低温、中温和高温;按升温速率来划分,热解可以分为慢速、常规、快速和闪速。如果反应条件合适,可获得原生物质80%以上的能量,生物油产率可达70%以上。生物质热解的主要工艺类型见表3-17。
表3-17 生物质热解的主要工艺类型

3.3.1.1 快速热解
快速热解是在缺氧或无氧条件下使生物质快速加热到中间温度(400~600℃),利用热能将生物质大分子中的化学键切断,从而得到低分子量的物质,并将所产生的蒸气快速冷却为生物油,它可将所有生物质成分,包括木质素,转化为液体产品。
快速热解可使质量和能量的约70%转化成液体产品。生物油即热解油包含许多与水互溶的含氧有机化学品和与油互溶的组分。与慢速热解相比,快速热解的整个传热反应过程发生在极短的时间内,强烈的热效应直接产生热解产物,再迅速淬冷,通常在0.5s内急冷至350℃以下,最大限度地增加了液态产物。
与传统的热解工艺相比,快速热解能以连续的工艺和工厂化的生产方式处理低品位木材或农林废物(如锯末、稻壳、树枝以及其他有机废物),将其转化为高附加值的生物油,可比传统处理技术获得更大效益,因此物质快速热解液化技术得到了国内外的广泛关注。
3.3.1.2 慢速热解
传统的慢速热解又称干馏工艺、传统热解,该工艺具有几千年的历史,是一种以生成木炭为目的的炭化过程。低温干馏的加热温度为500~580℃,中温干馏温度为660~750℃,高温干馏的温度为900~1100℃。干馏工艺是将木材放在窑内,在隔绝空气的情况下加热,可以得到原料质量30%~35%的木炭产量。传统的生物质慢速热解,是一种以得到固体产物为目标的生物质利用方法,一般得到的液体产物产率较低。
热解的速率对生物油的组成有着很大的影响,高加热速率有利于产生更多的液相产物;低加热速率有利于气、固相产物的生成。
总体来说,慢速热解是一种以生成焦炭为主要目的的热解过程,在慢速热解条件下焦炭产率可达30%~35%。有研究者以固体废物作为原料进行了慢速热解,CO和CO2的含量占到了2/3以上,在热解终温>500℃时,H2和CH4含量开始逐渐增加。在P.T.Williams[67]的松木慢速热解实验研究中,他发现在低温区木质生物质的主要热解产物是水、CO2和CO,在高温区则是油、水、H2以及气相烃类化合物。
近几年来,科研工作者对慢速热解又有了新的应用。张巍巍[68]等将慢速热解方法作为生物质气化的前处理工艺,通过慢速热解方法解决生物质在气流床气化过程中能量密度低、物料运送难度大及焦油含量高等问题,以提高气化合成气的热值。
3.3.1.3 真空热解
真空热解液化技术是指在一定的真空度下将生物质迅速加热到500~600℃,将热解蒸气迅速凝结成液体,尽可能地减少二次裂解,从而得到以液体产物为主的技术。液态产物生物油可直接作为燃料使用,也可通过精制提炼后作为化石燃料的替代品,进一步处理后的生物油还是重要的化工原料。生物质经真空热解液化技术后同时可得到部分固体焦和少量气体燃料。
该方向的研究最早于1992年,1993年在加拿大魁北克拉瓦尔大学的研究人员[69]对白杨进行了真空热解的研究。反应在2m高、0.7m内径、六段加热的反应器中进行,原料由反应器顶部进料,顶部温度为200℃,内部温度可达400℃,系统压力为1kPa。Pakdel等[70]于1996年以甘蔗渣为原料,制备了真空热解生物油。加拿大Manuel等[71]于2002年进一步研究了甘蔗渣的真空热解工艺,并对热解得到的真空热解生物油的物化性质进行了深入的研究。Manuel等[71]分别在间歇式和连续式中试真空热解反应器中,在真空度8kPa的压力下研究了生物质的真空热解。应用真空热解的方法,在两种不同的反应器中制备得到的生物油产率质量分数分别为34.4%和30.1%,产碳率质量分数为19.4%和25.7%。与快速热解生物油相比较,该生物油含有较少的灰分(0.05%),相对较低的黏度(4.1mm2/s 90℃),相对较高的热值(22.4MJ),含有少量的甲醇可溶物。Manuel等[71]在80℃下做了加速老化试验,表明该生物油与其他方法制备的生物油有着很相似的热平衡常数,并对真空热解得到生物油的含水量、运动黏度、闪点、密度、热值、灰分含量、金属含量等进行了分析。国内在该方向的报道不多,徐莹[72]等研究了以松木粉为原料的真空热解生物油的物化性质及特点,并与其他热解方式进行比较。
真空热解液化技术的特点是:体系内压力低,热解蒸气停留时间短。生物质的热解是一个固相转变成气相、体积增大的过程,真空条件有利于热解反应的进行。真空热解过程中体系压力的降低相应地降低了热解产物的沸点,因而有利于热解产物分子的蒸发,同时缩短了热解产物在反应区的停留时间,可以降低二次裂解生成气体的概率,有利于液体产物的生成。
采用真空热解技术的目的在于通过真空,即压力的降低来达到在较低温度下使生物质中的聚合有机物快速热解为需要的挥发性组分的目的,进而将其冷凝为具有高热值的热解燃料油。
3.3.2 生物质快速热裂解液化机制与工艺特点
3.3.2.1 生物质快速热裂解液化技术的机制
生物质主要成分是纤维素、半纤维素与木质素,它们的热解速率、机制与途径各不相同。纤维素和半纤维素热解后主要产生挥发分,木质素主要产生焦炭。纤维素由若干个D-吡喃式葡萄糖单元通过以β-苷键形成的氧桥键C—O—C组成。氧桥键较C—C键弱,受热易断开而使纤维素大分子断裂为挥发性小分子。半纤维素由两个或两个以上单糖(丁糖、戊糖、己糖等)通过氧桥键C—O—C聚合组成,稳定性较纤维素差,在225~325℃下氧桥键断裂,裂解为挥发分。木质素具有最好的热稳定性,它由苯基丙烷通过C—C键与氧桥键C—O—C结合形成,在250~500℃下,连接单体的氧桥键与单体苯环上的侧链键断裂,形成苯环自由基,同时其他小分子与自由基极易发生缩合反应,生成更稳定的大分子,进而转变为焦炭。
研究人员经过多次实验发现,在反应器中的热量传递由外传递到生物质颗粒内部,颗粒外层首先发生一次热解,产生挥发分与炭,其中挥发分中的可凝气体经冷凝后产生一次生物油。当热量传递到颗粒内部,内层颗粒热解为挥发分和炭,挥发分从内层通过外层传质到炉内气相主体中。在挥发分的传质过程中,挥发分发生二次热解生成不可凝气体与可凝气体,可凝气体冷凝后生成二次生物油[73]。
3.3.2.2 生物质快速热裂解液化工艺特点
生物质快速热裂解技术的一般工艺流程包括物料的干燥、粉碎、热裂解、产物炭和灰的分离、气态生物油的冷却和生物油的收集。
(1)黑体后干燥
为了避免原料中过多的水分被带到生物油中,对原料进行干燥是必要的。一般要求物料含水率在10%以下。
(2)黑体后粉碎
为了提高生物油产率,必须有很高的加热速率,故要求物料有足够小的粒度。不同的反应器对生物质粒径的要求也不同,旋转锥所需生物质粒径小于200μm;流化床所需生物质粒径要小于2mm;传输床或循环流化床所需生物质粒径要小于6mm;烧蚀床由于热量传递机制不同可以采用整个的树木碎片。但是,采用的物料粒径越小,加工费用越高,因此,物料的粒径需在满足反应器要求的同时与加工成本综合考虑。
(3)黑体后热裂解
热裂解生产生物油技术的关键在于要有很高的加热速率和热传递速率、严格控制的中温以及热裂解挥发分的快速冷却。只有满足这样的要求,才能最大限度地提高产物中油的比例。在目前已开发的多种类型反应工艺中,还没有发现最好的工艺类型。
(4)黑体后产物炭和灰的分离
几乎所有生物质中的灰都留在了产物炭中,所以分离了炭的同时也分离了灰。但是,炭从生物油中的分离较困难,而且炭的分离并不是所有生物油的应用中都是必要的。因为炭会在二次裂解中起催化作用,并且在液体生物油中产生不稳定因素,所以,对于要求较高的生物油生产工艺,快速彻底地将炭和灰从生物油中分离是必需的。
(5)黑体后气态生物油的冷却
热裂解挥发分由生产到冷凝阶段的时间及温度影响着液体产物的质量及组成,热裂解挥发分的停留时间越长,二次裂解生成不可冷凝气体的可能性越大。为了保证油产率,需快速冷却挥发产物。
(6)黑体后生物油的收集
生物质热裂解反应器的设计需保证温度的严格控制外,还应在生物油收集过程中避免由于生物油的多种重组分的冷凝而导致的反应器堵塞。
生物质快速热裂解技术作为一种高效的生物质能量转换技术是目前世界上生物质能研究开发的前沿技术,具有独特的优势。它能以连续的工艺和工业化生产方式将生物质转化为高品位的易储存、易运输、能量密度高且使用方便的液体燃料,可作为可再生替代液体燃料在锅炉中直接燃烧、与煤混燃、乳化代替柴油或精制后作为动力燃料,还可以作为化工原料从中提取具有商业价值的化工产品。生物油S、N含量低,是清洁无污染的液体燃料,生产原料广泛,不与粮食争地,原料收集面积小,便于运输,大大降低了成本,也是国家政策大力支持的产业[74~76]。
3.3.3 快速热解反应器
针对生物质快速热解获取高产率生物油所需的反应条件,各国研究机构已开发出了多种类型的热解技术和热解反应器,对各种反应器的结构特性以及工作原理进行了详细介绍。各种热解技术的应用状况各异[78]。
1)携带床反应器(entrained flow reactor)研发单位主要有美国的GTRI和比利时的Egemin公司。Egemin公司在1991年将其热解技术规模放大并实现了商业应用,但在运行过程中发现,依靠流化载气向生物质颗粒传递热量,在热量传递速率方面存在很大问题,最后Egemin中止了该项技术的深入研究。GTRI则一直没有对其技术进行规模扩大。
2)涡流反应器(vortex reactor)研发单位主要有美国SERI(即现在的NREL)、英国Aston大学和德国Pytec。NREL开发的涡旋反应器小试装置显示出了较好的热解效果,但在规模扩大过程中没有克服如何保持颗粒在反应器内的高速运动这一技术难题,NREL在1997年之后停止了该项技术的研究。Aston大学和Pytec在烧蚀式热解原理的基础上,研发了移动刮板式热解反应器,目前尚不知其技术的成熟程度如何。烧蚀反应器(见图3-14)是快速热解研究最深入的方法之一,它能够热解相对于其他的反应器来说较大颗粒的生物质。关于烧蚀反应器的很多开拓工作是由NREL和Nancy的CNRS完成的,其中NREL是在涡旋反应器里完成的。

图3-14 烧蚀反应器
3)真空式热解反应器(vacuum pyrolysis reactor)研发单位主要有加拿大Pyrovac。真空热解技术实际上是中速至慢速热解,生物油产率较低(35%~40%)。在2000年Pyrovac成功建立了日处理93t生物质原料的工业示范装置,但由于真空热解所得到的生物油黏度大、使用困难、缺乏相应的应用市场,在2002年之后这项技术也没有继续深入开发。
4)奥格热解反应器(auger reactor)研发单位主要有加拿大Renewable Oil International(ROI)。ROI是一家致力于开发先进的快速热解生物炼制技术,将木材和其他生物质转化为高价值产品的公司,其公司的技术具有能源自给自足,成本低廉,可使用大部分生物质原料生产等特点。ROI已经完成了日处理5t生物质原料的中试装置,正在筹建日处理25t和100t原料的工业示范装置。该热解工艺不需要使用流化载气,设备造价比较低,具有较好的开发前景。
5)螺旋热解反应器(screw pyrolysis reactor)研发单位主要有德国Forschungszentrum Karlsruhe。这项技术对生物质进行快速热解后并不对产物进行气固分离而是直接冷凝,从而得到生物油和焦炭的浆状混合物,作为气化合成气原料。目前这项技术还没有进入工业示范研究。
6)鼓泡流化床反应器(bubbling fluidizing bed)研发单位主要有加拿大Dyna Motive、西班牙Union Fenosa、英国Wellman等。其中,Dyna Motive已建立了日处理100t木屑的鼓泡流化床工业示范装置(图3-15),生物油产率超过60%,油品用于燃气轮机发电。

图3-15 鼓泡流化床反应器
7)旋转锥反应器(rotating conereactor)研发单位主要有荷兰Twente大学和BTG。BTG已在马来西亚建立了日处理50t棕榈壳的旋转锥工业示范装置(见图3-16),生物油产率超过60%,油品用于锅炉燃烧发电。

图3-16 旋转锥反应器
8)循环流化床反应器(circulating fluidizing bed)(图3-17)研发单位主要有加拿大ENSYN、希腊CRES和CPERI、意大利ENEL、芬兰VTT等。ENSYN开发了多种不同结构的循环流化床热解装置,这是目前世界上唯一的已经实现商用的热解技术,其中规模最大的装置日处理50t原料,出售给美国Red Arrow公司。但Red Arrow公司并不是利用该装置生产生物油作为燃料使用,而是从生物油中提取高附加值的食品添加剂,反应条件与常规的获得最大生物油产率的反应条件有所不同,主要是大大缩短了气相滞留时间(数百毫秒),经过化学提取后的残油作为燃料油燃烧使用。然而美国Manltowoc一发电厂对该装置生产的生物油与煤共燃发电试验表明,生物油的燃烧特性较差,这说明ENSYN目前使用的热解技术还不能得到品质较好的生物油。

图3-17 循环流化床反应器
3.3.4 热解的影响因素
影响快速热解生物油产率和组分的因素有很多,可以分两大类:一类是与物料特性有关的,如物料组成、粒径、含水率等;另一类与反应条件有关,如升温速率、反应温度、滞留时间、压力和催化剂等。
3.3.4.1 原料对产物的影响
不同种类的生物质原料会对生物油成分造成很大的影响,不仅会导致组分含量的差异,还会导致物质组成上的差异,这主要是由生物质本身成分不同造成的。不同的生物油,组分含量虽有所差别,但有许多组分在每种生物油中都有所存在,不同的组分也通常属于同一个化学族类。
生物油主要组分包括小分子有机酸、芳香族化合物以及醛、酮等物质,其中酚类及其衍生物含量较高,一般都是带有甲基、甲氧基、羟基和烯基等官能团的有机化合物。而在生物油热解中产生的芳香族化合物,通常被认为不是产出自快速热解过程,而是在反应停留时间中由一次挥发分二次热解所得的。
3.3.4.2 热解温度对产物的影响
生物质种类不同,热解过程温度范围也有所不同。大体上来说,生物质的热解主要发生在750℃以下,在122~202℃时发生预热解,375~527℃为主要热解阶段,热解温度对各相产物产率的影响结论较为一致,随着热解温度的升高,一次和二次分解反应加剧,固相产物减少;液相产物先增加后减少;由于液相产物的二次裂解和固相产物的二次分解,气相产物增加。因此,为得到较高的生油产量,反应温度宜选取在500℃左右,温度过低有可能导致生物质的不完全热裂解,而当温度过高时,气体产量增加同时生物油产量减小,这主要是由于气相生物油的二次裂化或重整加剧使得生物油产量有所减小的缘故。而且气相产物分子的平均自由历程很大,使得相互之间碰撞的可能性变得很小,从而降低了气相生物油重整的概率,因此二次反应主要以二次裂化反应为主。
Wang等在研究垃圾热解时发现,300~550℃为主要热解阶段,超过550℃为炭化阶段。Wagenaar[79]等发现,在450~550℃下生物油收集率达到最高;当温度超过550℃后,有大量的热解气体产生,生物油产率下降的非常快,而焦炭产率变化不大,原因是在自由空间内,过高的温度使得二次热解较容易发生,促使生物油产率快速下降。王树荣[80]等以花梨木为生物质原料,经粉碎、干燥后,在循环流化床内进行快速热解。研究发现伴随着温度升高,焦炭产率逐渐下降到一个稳定值,而生物油产率在500~550℃达到最大。
3.3.4.3 加热速率对产物的影响
加热速率对热解产物产量和特性也有较大影响,升温速率越慢,生物质颗粒越容易被炭化,这会使产物中碳含量大大增加,同时产生一定量的副产物。所以如果想要获得高产率的生物油,就必须提高升温速率,升温速率增加,物料达到所需温度的时间变短,从而降低二次热解发生的概率。较快的加热速率可以使反应器内部与生物质颗粒快速达到所需热解温度,促进了生物质的快速热解,提高了生物油的产率,但也会导致热解不完全。
Debdoubi等对细茎针草进行热解发现,随着加热速率的提高,气、固相产物产量减少,液相产物产量增加[81]。在不同加热速率下,保证液相产物产量最大的热解温度有一定差别。当加热速率为50℃/min和150℃/min时,该温度为500℃;当加热速率为250℃/min时,该温度为550℃。对树皮慢速热解而言,450℃时液相产物产量最大;对油菜籽快速热解而言,550℃时液相产物产量最大。Guerrero等在不同加热速率下对桉木进行热解,并对所得焦炭比表面积进行测试发现,当热解温度为900℃时,由于挥发分迅速析出会造成生物质颗粒内较大的压力,使焦炭形成较多开放性微孔,快速热解所得焦炭比表面积大于慢速热解所得焦炭。Cetin等对辐射松热解所得焦炭进行研究发现,焦炭活性随着加热速率的提高而增加,但高加热速率会导致颗粒的塑性形变。此外,Demirbas研究了不规则加热速率下生物质热解产物的分布规律[82]。
3.3.4.4 生物质物料预处理对产物的影响
生物质快速热解之前,需要进行粉碎处理。文献发现[76],当进料粒径<1mm时,热解反应为反应动力学控制;当粒径>1mm时,反应为传热与传质控制。平均热解速率随原料粒径上升而下降,生物质热解达到最大失重速率时所对应的温度有增大趋势。由于生物油分为水相和油相,而水相是生物油不稳定的最关键因素。所以通过对原料颗粒的干燥,可使水分在原料颗粒中低于10%,很大程度降低生物油含水率,进而提高生物油的稳定性;酸洗预处理脱灰可以使生物质热解的挥发分产量增加,生物油产量提高,气体产量降低,脱灰增大了其有效比表面积,提高了生物油的热值;焙烧预处理在近些年也引起了研究者的关注,研究证明,经过低温(<300℃)焙烧可以部分脱除生物质中的氧含量,从而得到低氧含量的生物油[76]。
3.3.4.5 其他因素对产物的影响
热解温度和升温速率是影响热解的两个主要因素,除这两个因素外,影响热解生物油产率和组分的因素还有催化剂、颗粒尺寸、吹扫气流、热解压力等。
催化剂的种类繁多,其催化效果与其孔径大小、尺寸分布、孔道结构、金属的负载等因素有关,在大部分研究中所使用的催化剂都可以使催化热解所得液相产物中氧含量减少,热值提高,Ates等[77]对玉米棒芯进行催化热解发现,催化剂能降低同等热解效果的反应温度。随着催化剂用量的增加,生物质热解脱水效应增强,从而使液相产物的含水量增加,同时固相产物随催化剂用量增加而增加。再加上催化剂在反应过程中会发生不可避免的结焦,能否找到适合热解的催化剂也是热解工艺能否大规模工业化的一大影响因素。
颗粒尺寸和吹扫气量对热解产物也存在着一定的影响,在早期的研究中,研究者已发现对传统热解而言,颗粒尺寸越小,反应越快,而增加吹扫气流量,可以使生成的热解生物油和不凝性气体及时逸出反应器,缩短了挥发分在固定床内的停留时间,减小了二次反应发生的可能性,热解生物油产量增加。但是过分减小颗粒尺寸,增大吹扫气量会导致成本增加,反应不充分等问题。另外研究者在研究热解压力对固相产物特性影响时发现,随着热解压力的提高,焦炭孔径变大,孔壁变薄,但在1000℃下,颗粒发生熔融,焦炭微孔减少,比表面积减小[75]。
3.3.5 生物油组分与特性
生物油是指通过快速加热的方式在隔绝氧气的条件下使组成生物质的高分子聚合物裂解成低分子有机物蒸气,并采用骤冷的方法,将其凝结成液体,它具有原料来源广泛、可再生、便于运输、能量密度较高等特点,是一种潜在的液体燃料和化工原料。
作为燃料,生物油可用于窑炉、锅炉等产热设备,将生物油用于柴油机也具有很大应用前景,对减少柴油消耗、缓解高品质燃料油供应紧张有重要意义。
3.3.5.1 生物油的理化性质
生物油的组成和理化性质受多个因素影响,如原料种类、含水量、反应器类型、反应参数、产物收集方法等,但不同途径制得的生物油仍具有一些共同的性质,如水分含量高、含颗粒杂质、黏度大、稳定性差、有腐蚀性等,这与传统石化燃料(柴油、汽油)有很大不同,也给生物油用于柴油机带来了很多困难。表3-18和表3-19是各类生物油的典型理化特性。
表3-18 生物油的典型性质

表3-19 各种生物油的元素组成与理化特性

(1)黑体后物理性质
木质纤维素生物质热解制取的生物油,其相对密度变化不大,约为1.2。生物油黏度变化较大,40℃时生物油的黏度一般为20~200mPa·s。如K.Sipila[83]等快速热解稻草、松木,硬质木材,在50℃时,三种生物油的黏度分别为11mPa·s、46mPa·s和50mPa·s,且在室温条件下,前65天可以观察到生物油黏度显著增加,此后生物油黏度变化不大;徐宝江等快速热解松木屑,温度为40℃时,生物油的黏度约为64mPa·s;廖艳芬等快速热解木材获得的生物油,黏度为150mPa·s。含水率对生物油的黏度影响较大,含水率大的生物油,其黏度一般较小。此外,如果生物油含有较多的极性基团(一般是含氧基团)和较大的分子,分子间作用力大,则黏度增大。
(2)黑体后化学性质
生物油来源于生物质,但不同生物质在不同热解条件下制取的生物油的元素组成可能差别很大。一般木质纤维素中氧的质量分数在40%左右,其热解产生的生物油中氧的质量分数一般也在40%左右,这种生物油的典型元素组成为:w(C)=53%,w(H)=6%,w(O)=40%和w(N)=0.2%。而藻类生物质含有较多的脂类、可溶性多糖和蛋白质,所以,藻类生物质制取的生物油含氧量低,w(O)约为17%。在快速热解工艺中,裂解产物的二次反应被减至最小,生物质的许多官能团被保留,因此从生物质转化为生物油的过程中氧元素的含量变化不大。所以,快速热解虽然获得了较高的生物油产量,但由此获得的生物油也存在含氧量高的缺点。中速、慢速热解工艺由于裂解产物的二次裂解,许多含氧官能团断裂,氧元素进入不可凝气体,由此得到的生物油含氧量较快速热解工艺低。如A.A.Zabaniotou等[84]利用木材为原料[w(O)达51.1%],在温度为400~700℃,加热速率120~165℃/s的条件下,获得了w(O)=30%的生物油。
目前,对生物质热解油组成进行分析的方法主要有GC,TG,GC-MS,GPC,HPLC,CNMR,HNMR,FTIR和CE等。热解油中的沥青质通过n-正己烷沉淀,可溶组分通过柱层析分别用正己烷、甲苯和甲醇可以转化为脂肪族、芳香族和极性组分。芳香组分和极性组分可以利用红外吸收光谱法分析,通过气相色谱配合火焰离子检测器,可以分析不同沸点的脂肪组分。GC-MS被证明是研究不同气氛下热解产物的一种较好的工具。
生物油的化学成分非常复杂,获知其详细化学组成非常困难。目前采用的方法是将生物油的复杂化学组成进行分类,然后再鉴别各类的主要成分。生物油大致是由酸、醛、醇、酯、酮、糖、苯酚、邻甲基苯酚、丁香醇、呋喃、木质素衍生取代酚、提取物衍生萜和水等组成的混合物,其组成很复杂,多达数百种。王树荣等[85]利用色谱-质谱分析了生物油的组成,发现不同种类的生物油中主要组分的相对含量大都相同,如糠醛、二甲氧基苯酚、2-甲氧基-4-甲基苯酚、丁子香酚、雪松醇、2-呋喃酮等在每种生物油中都占有很大的比例。生物油中带有酮、醛取代基的苯酚类物质种类最多。色谱-质谱分析还证明了大量存在的醛类和酮类化合物使生物油具有亲水性,并使其含水量高且水不易去除。在K.Sipila等[83]对水萃取木质纤维素生物质如稻草和松木等热解制取的生物油进行了分析,他们将生物油分为溶于水的组分(水相)和不溶于水的组分(油相)两大类,并定量测定了水相主要成分的组成,结果发现水相占据生物油质量的60%~80%,水相主要由水、小分子有机酸和小分子醇组成。以源于稻草的生物油为例,水相中的水占生物油质量的19.9%,甲酸占1.85%,乙酸占7.41%。张素萍等[87]也用此法测定了源于木屑的生物油的组成,水相中含量较多的成分为水[w(H2O)=66.1%],乙酸质量分数为17.9%,羟基丙酮质量分数为11.4%,油相用正庚烷萃取,对正庚烷的萃取物进行柱色谱分离后分析,发现甲基呋喃占正庚烷的萃取物质量的14.17%,苯乙醇占12.38%,检验出的酚类占51%。对正庚烷不溶物用13CNMR进行分析,发现脂肪碳的含量远远大于芳香碳的含量,烷氧基碳的含量较高。戴先文等[86]快速热解木粉,发现生物油中酚和有机酸的含量较大,烷烃占生物油质量的31.04%,芳烃占13.47%。易维明等利用等离子加热的方法快速热解玉米秸粉,发现乙酸占生物油质量的25.99%,羟基丙酮占生物油质量19.24%(换算后的数值)。由此可见,快速热解木质纤维素一类生物质获得的生物油,成分随具体工艺条件和原料而变化,含量较多的成分有水(质量分数在20%左右)、小分子有机酸、酚类、烷烃、芳烃、含碳氧单键和碳氧双键的化合物如甲基呋喃、羟基丙酮等[87]。
如前文所述,不同生物油尽管在组分上有所不同,但在主要成分的相对含量上大都表现出相同的趋势,如糠醛、二甲氧基苯酚、2-甲氧-4-甲基苯酚、2,6-二甲氧基苯酚、2-呋喃酮和左旋葡聚糖等在每种生物油中都占有较大比例。经过多年的研究,已对市政污水污泥、城市垃圾、工业废油、废皮革制品、新闻用纸、优良纸、废纸浆、腰果壳、棉籽块、软木材的树皮、向日葵壳、榛果壳、桉木废物、阿月浑子树以及白杨锯屑、云杉锯屑、橡树锯屑、亚麻块、绿藻、微藻、水曲柳、花梨木、芒、橄榄、大豆、稻草秸秆、油菜秸秆、芝麻秆、玉米秸秆、高粱渣、小麦壳和水稻等多种生物质热解油的组成和性质进行了研究。
生物油含水量较高,其主要来自于生物质原料本身、热解反应和生物油存储时的脱水反应。水一方面降低了生物油的热值和火焰温度,另一方面降低了生物油的黏度,增强了生物油的流动性,使其有利于在发动机内喷射燃烧。Shihadeh等[73]对美国国家可再生能源实验室(NREL)和Ensyn Technologies Inc.CA(ENSYN)制备的生物油进行了比较,发现NREL的热解步骤改善了生物油的化学和气化性质,得到的生物油含水量低、相对分子质量小,因此其点火等性能比ENSYN制备的生物油好。
生物油含有较多的小分子有机酸,pH值较低,一般为2.5左右。强酸性使生物油的腐蚀性很强,高温下腐蚀性更强,因此对于容器的抗腐蚀性要求很高。如果把生物油用作车用燃料,则需对其进行精制。如K.Sipila等[83]快速热解稻草、松木和硬质木材,三种生物油的pH值分别为3.7、2.6和2.8;戴先文等[86]快速热解木粉,获得的生物油pH值为2.1;任铮伟等快速热解木屑,获得的生物油pH值为2.5。
生物质快速热解过程中还会生成一些碳,这些碳大部分在旋风分离器被分离,但仍会有微量的碳夹杂在生物油中。戴先文等由木粉快速热解获得的生物油,w(C)为2%。
生物油在生产过程中还可能会混入一些灰分,其含量一般占生物油质量的0.1%左右,生物油中的灰分会引起发动机和阀门的腐蚀、反冲启动等问题,当灰分质量分数大于0.1%时,情况更加恶化。灰分对热裂解制取生物油有负面作用,会促进小分子量的气体的生成。灰分主要含碱金属和碱土金属,主要是易沉积、可引起高温腐蚀的Na、K及会导致更坚硬的固体沉积的Ca,它在热裂解反应温度下几乎不分解或挥发,所以其起作用的方式类似于催化剂。生物油含有K、Na、Ca,质量分数分别为2×10-6,6×10-6,1.3×10-5。NREL研究的热蒸气过滤步骤可有效降低生物油中碱金属和碱土金属的质量分数,使之分别达到2×10-6。如K.Sipila等快速热解稻草、松木和硬质木材,三种生物油的w(灰分)分别为0.14%、0.07%和0.09%;戴先文等快速热解木粉制取的生物油中w(灰分)为0.1%;徐保江等[89]快速热解松木屑制得的生物油中w(灰分)为0.2%。生物油的热稳定性比较差,加热到一定温度后,生物油的内部组分将会发生聚合反应,这对生物油的精馏分离等过程非常不利。任铮伟等[88]发现,快速热解木屑制取的生物油加热到120℃左右就形成海绵状胶体,不能用蒸馏法分离,考察了由树皮经过真空热解获得生物油的热稳定性,生物油样品分别在40℃、50℃和80℃储存168h,另外的一个样品在室温下储存1年,然后测量生物油的相分离时间(水相和油相)、黏度和平均分子质量。结果表明:被加热到80℃储存的生物油的性质发生了显著改变,而在40℃和50℃储存的生物油的性质变化不大;在80℃的条件下,生物油迅速出现相分离,放置1周,其相对分子质量的改变相当于生物油在室温下放置1年的改变。实验还发现,如果将生物油的水相部分加入到另外一个生物油样品,则这个生物油样品的热稳定性显著变差,这充分证明了生物油水相的组分是生物油不稳定的原因;此外,如果在生物油中加入甲醇,生物油的稳定性将会得到增强。
3.3.6 生物油精制
生物油精制的目的就是要降低生物油中氧含量,提高H/C,使其性能更接近化石燃油,从而使生物油可以在生活中替代化石燃料。氧主要来源于纤维素、半纤维素和木质素热解产生的酸类、酚类和聚酚类等一些含氧化合物。这些含氧化合物导致生物油热稳定性差,热值低,低挥发性和腐蚀性等,因此需要对生物油进行精制。
生物油的精制方法主要分为两大类:物理处理和化学精制。主要包括催化加氢、催化裂解、添加溶剂、乳化、分子蒸馏及催化酯化。
3.3.6.1 物理处理方法
物理处理方法主要采用乳化或分离等手段来克服生物油的缺点,一般都在比较温和的条件下进行,所采用的设备和操作成本也比较低。通过处理,生物油的物理特性可以得到一定的改善,甚至可以部分应用于发动机。但是,造成生物油诸多缺点的根本原因是其复杂的物质组成和化学结构,所以大多的物理处理很难从根源上解决生物油中存在的问题[81]。
3.3.6.2 化学精制法
化学精制法主要是针对生物油中成分的特性,采用一些有针对性的加工,可以实现生物油的高品位转化。根据生物油的特性,采用两步法精制加工生物油具有一定的意义。生物油的成分多样,且热稳定性不好,首先通过在比较温和条件下对生物油进行提质,从而得到稳定性或者酸性改善的油品;然后在更苛刻的条件下进行进一步的加工精制,从而获取高品质的燃油。
生物油精制常用的工艺包括催化加氢、催化裂化、乳化技术等。
(1)黑体后催化加氢
催化加氢是在高压(10~20MPa)和供氢溶剂存在的条件下,通过催化剂催化作用对生物油进行加氢处理的技术。氧元素以CO2与H2O的形式脱除。催化剂通常使用经过硫处理后的Co-Mo催化剂。对生物油而言,由于生物油中氧含量远高于硫和氮含量,因此,生物油中的催化加氢的主要目的为催化加氢脱氧(HDO)。对生物油的催化加氢精制一般是在加氢催化剂作用下,在高压(10~20MPa)或有供氢溶剂(如甲醇,甲酸等)存在的条件下,使生物油中的氧以CO2或H2O的形式除去。因此,生物油的加氢精制能够有效降低生物油中的含氧量,提高生物油的燃烧性能和稳定性,增加生物油的燃烧热。研究者在一定的压力、温度和氢流量下,以戊酸甲酯和庚酸甲酯为模型化合物进行实验,根据研究结果推测认为脂肪酸甲酯生成烃类有3种途径:第1种是酯生成醇,然后脱水生成烃;第2种是酯水解生成羧酸和醇,再脱羧和脱水生成烃;第3种是酯直接脱羰基生成烃,加氢的最佳工况约为250℃,反应时间2h,冷氢气压力约1.5MPa。
Piskorz[90]等将由快速热解产生的高温气态生物油直接与H2混合后进行加氢反应,不仅可以利用热反应的余热,还可以进一步降低油的含氧量(小于0.5%)。但是,生物油稳定性差,超过80℃后就会发生强烈的聚合反应,导致黏度迅速增加,生物油进入催化剂基体中,覆盖催化剂活性中心,极易导致催化剂失活。Mahfud等[91]使用均相钌催化剂对生物油水溶组分进行催化加氢,试验采用温和的反应条件(4MPa,90℃),并在水/甲苯有机两相体系中催化生物油。反应后,羟丙酮和羟乙醛的含量显著减少,分别转化成丙二醇、乙二醇,含氧量大大降低。
催化加氢技术可以大幅度降低生物油的含氧量,但过程中需要大量的H2,这造成催化加氢的成本非常高。而且由于生物油成分复杂,热稳定性差,催化加氢的效果都不是十分理想。精制后,生物油的产率较低,同时会产生相当量的积炭,这些焦炭类物质易沉积在催化剂表面,覆盖催化剂的活性位点,导致催化剂失活。并且此过程产生焦炭类物质易堵塞反应装置,使催化加氢过程难以进行,Co-Mo等催化剂造价昂贵,易结焦失活,并且需要在高压下进行,反应条件苛刻,所以催化加氢技术目前仍未广泛使用,研究低温高活性的催化剂是生物油加氢产业化的出路。
(2)黑体后催化裂化[92~94]
催化裂化方法主要是在中温、常压下通过加催化剂对生物油进行精制处理,将生物油中所含的大分子脱除裂化为小分子,将氧元素以CO2、CO和H2O的形式脱除。但以CO2、CO的形式脱除好于以H2O的形式,因为H2O的生成必然会降低生物油中的氢元素含量,降低H/C,从而降低生物油中饱和烷烃、环状脂肪烃的含量,使油品下降。催化裂化方法无需还原性气体,操作压力较低,温度适中,易于将裂解和改性两个步骤紧密相连,因此比较简易方便。对于酒精原料的分子筛处理,已进行过商业运行,主要用于将醇类转化为汽油,同时还用于纤维素热解产品的改性,但是对木质素热解产品的处理,沸石分子筛处理还存在着焦化问题。相比于催化加氢,催化裂解是在常压没有氢气的条件下进行的反应,反应所需设备及运行操作成本都比催化加氢低,但效果不如催化加氢,其获得的精制油的产率一般比催化加氢低。
催化裂解技术近些年的变化主要围绕在两个方面:一是由生物油液相加热催化裂解发展为生物质热裂解蒸气在线催化裂解,优点是节约能耗,避免生物油加热时聚合而导致催化剂结焦;二是催化剂的选择由传统的沸石分子筛向介孔分子筛发展,优点是介孔材料作为催化剂使用时,能够一定程度上改善结炭,介孔有助于提高反应物和产物的扩散速率。介孔材料的特点是具有均匀规则的介孔(2~50nm),很大的比表面积(一般≥1000m2/g)和孔道体积,这使得介孔材料在有大分子参加的催化反应中显示出特别优异的催化性能。结合目前的应用情况来看,介孔分子筛的热稳定性(一般都在800℃以上)完全可以满足快速裂解(裂解的温度一般不超过600℃)的要求,但与常规的微孔分子筛晶体相比,一是酸性较弱;二是介孔材料具有较低的水热稳定性(介孔分子筛的水热稳定性是指将其放入冷水或热水中,经过一段时间后,孔壁介孔结构塌陷,变成无定形),这是目前尤其应注意的问题,因为生物质在快速裂解的过程中不可避免的会产生水蒸气。与传统的沸石类分子筛催化剂相比,介孔材料类的催化剂反应后焦炭类产物较少,催化剂失活得到有效的改善。但是,由于介孔材料类催化剂是由纯二氧化硅组成的,缺少酸性的位点,因此在催化裂解前必须引入离子或酸性氧化物,以增加其酸性。然而,酸性强弱对催化反应结果影响非常显著,不同反应或同一反应在不同条件下对催化剂酸性强度要求都不一样,因此,实验过程催化剂的酸性难以掌握,增加了应用推广的难度。
催化剂的结焦失活问题能否解决是催化裂解技术能否进一步普及的关键。目前来看,介孔分子筛催化精制后的目标产物的产率还不能令人满意,选用的介孔分子筛主要是MCM-41、SBA-15、MSU-S等。因此,要进一步寻找廉价简便的合成方法和回收模板剂,降低成本,强化无机孔壁的结构,改善水热稳定性和机械强度,孔结构、孔分布和酸性要可调控,有效地改善结构和性能,合成功能化、多层次(从大孔到介孔到微孔)、多维孔道结构的介孔材料,使介孔分子筛的优势真正地发挥出来是今后生物油裂解精制的重要发展方向。
Williams[95]等认为催化裂化主要通过以下2种途径进行:a.沸石分子筛将生物油催化裂化为烷烃,然后将烷烃芳构化;b.将生物油中的含氧化合物直接脱氧后形成芳香族化合物。目前,催化裂化的催化剂主要使用酸性催化剂,如HZSM-5、NaZSM-5、Y型分子筛以及磷酸铝分子筛等。郭晓亚[96]等采用HZSM-5分子筛催化剂,将生物油与溶剂四氢化萘以1∶1的质量比混合,在固定床反应器内催化裂解,实验结果表明,精制油中的含氧化合物,如有机酸、酯、醇、酮和醛的含量大大降低,而不含氧的芳香烃含量增加。
(3)黑体后乳化
因为稳定性差、黏度高、酸性强等特点,经快速热解制得的生物油不可直接用于柴油机。向生物油中加入表面活性剂(乳化剂)后,可有效地降低生物油表面张力、抑制凝聚,可与柴油形成乳化液,提升稳定性、降低腐蚀性,更重要的是只需将现有柴油机的喷嘴与输油泵更换为不锈钢制品,即可将乳化液作为车用燃油使用。
乳化机制为:生物油水相溶液中水、醛、酸、酮等极性组分稳定地被乳化剂包裹在W/O型乳化液液滴中,生物油水相溶液中少量的乙酸乙酯、芳香类化合物等则溶于非离子乳化剂胶束的亲水基(聚氧乙烯基)中。
Chiaramonti[97]在柴油中添加了质量分数25%、50%、75%的生物油,并对其乳化情况进行了研究,发现乳化油比生物油更稳定。生物油的含量越高,乳化油的黏度越高。当乳化剂添加量的质量分数在0.5%~2.0%时,乳化油的黏度适中。Ikura等[98]考察了生物油-柴油乳浊液的稳定性和腐蚀性,他们先将生物油置于离心机中离心,以除去生物油的重组分,然后将处理后的生物油与柴油混合制成乳化油。实验发现,表面活性剂浓度对乳化油的腐蚀性影响很大,经腐蚀实验测定,浸泡在纯生物油中的钢棒质量损失了72%,而浸泡在生物油质量分数为20%的乳化油体系中的钢棒质量只损失了35%,即后者腐蚀性能更弱。Michio等研究了乳化温度、乳化时间、表面活性剂的用量、生物油在混合油中的浓度以及单位体积输入功5种因素对生物油乳化性能的影响。研究表明,后面3种因素对生物油乳化性能有较大影响;表面活性剂的用量为总质量的0.8%~1.5%和生物油的加入量为10%~20%时,所得乳化油的运动黏度最好;与此同时,乳化油的性能与生物油在混合油中的浓度以及单位体积输入功也有关系。
乳化方法操作简单,不需要进行化学反应。但乳化剂的成本较高,乳化过程需要投入较大的能量,所得乳化油对内燃机的腐蚀性较大。目前,已经报道的生物油乳化技术均未能对生物油中的木质素、水分以及酸类化合物进行处理。生物油中所有的木质素、水分以及酸类化合物都保留在乳化油中,使得制备的乳化油热值较低(水分蒸发吸收热量),燃烧不完全、易产生积炭(木质素低聚物燃烧不充分),同时对内燃机有一定的腐蚀作用(有机酸没有被排除)。因此,该技术目前还有待于进一步的研究,以处理上述问题。
综上所述,目前生物油精制改性技术的研究热点主要集中在催化加氢、催化裂解、添加溶剂及乳化几个方面。每种方法都能够提高生物油的品质,然而每种都有一定的局限性,单独使用某一方法不足以解决生物油所有问题,不能够实现生物油的商业化利用。因此,必须开发新的生物油精制改性技术,提高生物油品质,以使其真正成为化石燃料的替代品。结合上述精制方法的优缺点和生物油的性质特点,一步或多步精制生物油,提高生物油的品质可能是一个有效的方案。
(4)黑体后催化酯化
生物质快速热解产物生物油中有机羧酸含量较高,种类较多,导致生物油的酸性和腐蚀性很强。催化酯化就是在生物油中加入醇类助剂,在固体酸或碱催化剂的作用下发生酯化等反应,从而将生物油中的羧基等组分转化为酯类物质,降低羧酸的腐蚀性,达到提高生物油物化性能的目的。
生物油中含有大量小分子有机酸类化合物,这些酸类化合物在燃烧过程中会造成内燃机的腐蚀;同时,酸类化合物能够促使生物油中的醛酮及木质素低聚物等发生缩聚反应,导致生物油的老化变质;此外,酸类化合物的存在对生物油的储存和运输也提出了更高的要求。因此,必须将生物油中的酸类化合物除去或转化为其他化合物。然而,与醛酮类化合物相比,酸类化合物性质较为稳定、反应活性较弱。对酸的加氢精制条件要求较为苛刻,对设备要求较高,往往需要高温高压(反应温度要求300℃以上,体系H2压力10.0MPa以上)才能进行。因此加氢精制不是处理酸类化合物的理想方法。而催化酯化具有反应条件温和、催化剂成本低(无需贵金属活性中心)等特点,同时,催化酯化反应还有设备要求低(无需高温高压反应釜)、操作简单和成本低廉等优点。此外,酯化反应的产物为酯类化合物,酯类化合物具有易挥发,易燃等特性,能够提高生物油的点火性能和燃烧性能。综合上述3个方面考虑,将生物油中的酸类化合物转化为性质稳定的酯类化合物,是提高生物燃烧性能和油稳定性的有效方法。但是,精制后的生物油的H/C提高不明显,热值还是偏低,不能用于汽车燃料使用。
固体酸催化剂较早实现工业化,此类固体超强酸的酸中心是由金属氧化物与
之间的相互作用所致。常用的固体超强酸有
、
、
、
和
等,催化效果很明显。固体酸催化剂按照组成不同,大致分为5大类:杂多酸、无机酸盐、金属氧化物及其复合物、沸石分子筛和阳离子交换树脂。其中MxOy类氧化物具有催化活性高,对水的稳定性很好,且副反应少,后续处理简单等优点。MxOy经H2SO4处理后可显著提高固体
的酸量,引入氧化物体系确实对原有氧化物产生诱导作用,导致酸性增强。自从1979年日本的Hino[99]获得首例
型固体酸
以来,至今已开发了一系列基于某些金属氧化物的
型固体酸,其中
基于Fe、Ti、Sn、Zr、Hf等氧化物固体酸的研究已被广泛应用。固体酸催化的反应有烷烃异构化、裂化、烷基化、酯化、醚化、聚合、低聚等,这方面的研究还在不断发展中。固体碱则包括担载碱阴离子交换树脂、金属氧化物、金属盐、氧化物混合物以及经碱金属或碱土金属交换的各种沸石等。
传统的酯化反应催化剂中,应用最广泛的是浓硫酸,其缺点是:硫酸同时具有氧化、磺化、脱水和异构化等作用,会导致发生一系列的副反应;反应产物复杂,后续处理烦琐,并有大量废液产生,污染环境;硫酸严重腐蚀反应设备。酯化反应通常受平衡限制,尤其是在液相反应中。必须不断地将产生的水除掉或在某一反应物过剩的情况下操作,这样才可能得到较高的酯产率。基于此,国内外对替代硫酸的新型催化剂进行了大量研究,主要集中在固体催化剂方面。固体催化剂活性高,与异相反应物容易分离,无设备腐蚀和环境污染,且具有易回收,可重复使用,可实现连续生产等优点。
近些年来,用于酯化反应的固体酸催化剂在制备过程中,添加某些贵金属或过渡金属组分,可以改善其催化性能,提高催化活性。金华峰[100]采用共沉淀和浸渍法制备了纳米复合固体超强酸、
,而王绍艳[101]用纳米Fe2O3粉体浸渍硫酸制备了纳米复合固体超强酸
,常铮[102]用纳米磁性材料Fe3O4和固体酸ZrO2进行组装,采用全返混液膜反应法制备出新型磁性纳米固体酸催化剂ZrO2/Fe2O3,实现了以磁性材料为核心将固体酸包覆在其外部的结构模型。梅长松[103]则将磁性材料CF加入ZrOCl2的溶液中,获得钴基磁性固体超强酸催化剂SCFZ,并应用于乙酸和正丁醇的酯化反应。Song等[104]研究了不同固体酸催化剂对生物油性质的影响。结果表明,
催化剂有较好的催化性能,生物油的热值增加了83.22%,动力学黏度下降了95.45%,pH值升高了68.63%,水的质量分数下降了52.23%。也经常有报道用离子交换树脂作酸碱催化剂,这符合绿色化学要求,应用前景广阔。常用的强酸性阳离子交换树脂有D001、D061、NKC-9和732型等,已在试验中显示出了较好的催化性能。
Wang[105]等选取了732和NKC-9型离子交换树脂作为研究对象,以生物油模型物与甲醇反应,其结果是732型树脂和NKC-9型树脂的精制油酸值分别下降了88.54%和85.95%,生物油模型的发热量分别增加了32.26%和31.64%,水质量分数分别下降了27.74%和30.87%,两者的密度降低了21.77%,黏性降低了大约97%。此法精制油的稳定性增强,腐蚀性降低,黏性降低幅度最大,是一种很好的降低黏度和提高生物油热值的方法。王琦[106]等利用间歇式玻璃反应釜,在60℃,油醇质量比为1∶2,催化剂质量分数为20%和全回流条件下,研究了强酸性离子交换树脂催化的生物油酯化精制反应。结果表明,酯化后生物油的含水量和黏度下降,热值提高了42.7%;生物油中低级羧酸均得到不同程度的转化,产物分布发生较大变化,主要生成乙酸乙酯、原乙酸三乙酯等新成分。
随着绿色化学的发展,人们也越来越关注固体碱催化剂。徐莹等[107]以超细γ-Al2O3负载K2CO3为原料制备固体碱进行催化酯化研究,结果表明,添加了K2CO3后的γ-Al2O3酯化效果较好,乙酸转化率显著增加。若添加适量的NaOH,不仅能增强催化剂的耐水性,而且能提高生物油的pH值从而降低生物油的腐蚀性。
通过催化酯化反应能够显著提高生物油的品质,精制后,生物油的pH值上升,稳定性增加,热值提高。但是,固体酸催化剂普遍存在酸性强弱和酸性流失的问题,这主要是由于生物油中存在的水分造成的。一般来说酸性越强催化酯化的效果越好,但酸性越强酸流失的程度就越严重。催化剂酸性的流失不但极大地降低了催化剂的活性,而且导致生物油的pH值下降。所以,在催化酯化过程中选择合适酸性催化剂是至关重要的,一般而言,应当选择具有一定的抗水能力的催化剂。
(5)黑体后分子蒸馏
分子蒸馏是一种特殊的液-液分离技术,它不同于传统蒸馏依靠沸点差分离原理,而是靠不同物质分子运动平均自由程的不同实现分离的。不同种类的分子,由于其分子运动平均自由程不同,逸出液面后与其他分子碰撞的飞行距离也就不同,在大于重分子平均自由程而小于轻分子平均自由程处设置冷凝板,气体中轻分子不断被冷凝,从而打破其动态平衡,促使液相中轻分子不断逸出;相反气相中重分子不能到达冷凝板,很快与液相中重分子趋于动态平衡,表观上重分子不再从液相中逸出,实现了液相中轻、重分子的分离。
郭祚刚[108]等利用分子蒸馏技术将生物油中的水分与酸性组分作为整体对象进行分离,既得到生物油酸性组分富集馏分,又获得了水分含量低、酸性较弱、热值较高的精制生物油Ⅰ(蒸馏重质馏分)与精制生物油Ⅱ(常温冷凝馏分)。同时,他们具体考察了精制前后生物油的pH值、热值和水分等参数的变化规律。Martinello[109]等以分子蒸馏法研究了葡萄籽油的物理精制过程,对原料粗油进行水脱胶、脱蜡和漂白三步预处理,然后再进行分子蒸馏以脱氧。实验以物料流量(0.5~1.5mL/min)和蒸发温度(200~220℃)为变量考察了精制油中游离脂肪酸和生育酚(维生素E)的含量。
(6)黑体后添加溶剂
也有很多研究者希望通过添加溶剂来改善生物油的各项性能。添加溶剂是指在生物油中加入其他性质稳定的化合物,以提高生物油的稳定性和降低生物油的黏度的过程。添加甲醇和乙醇等溶剂不仅可以降低生物油的黏度,还可以降低生物油的pH值,提高生物油的点火性能,是常见的提高生物油稳定性的方法。许多研究者研究了添加剂对生物油改性的作用。结果表明甲醇是优良的生物油改性添加剂,向生物油中添加少量(约10%)的甲醇,就能显著地提高生物油的稳定性。Lopez等[110]分别对纯生物油和生物油与乙醇混合(生物油质量分数为80%,乙醇质量分数为20%)在涡轮机中进行了燃烧试验研究。结果发现,由于混合油黏度较高,需要对燃烧室中的喷嘴进行改进,在燃烧性能方面与标准燃料相比有明显差异。添加醇类虽然改善了生物油的品质,但甲醇等燃料的自燃性都很差,有较高的抗爆性,低温蒸发性差,蒸发潜热高,不利于低温冷启动;而生物油本身的十六烷值很低,因此,添加醇类的生物油作为内燃机燃料应用可能有一定的困难。而且,添加溶剂并不能够降低生物油中的含氧量,不能够提高生物油的燃烧热,此外,添加溶剂的成本往往较高,难以大范围地推广。因此,通过添加溶剂来对生物油进行改性的研究较少。
(7)黑体后其他方法
除了加氢、酯化、乳化等传统的改性方法外,目前又出现了新的工艺,如高压均化处理技术(HPH),Ronghai He等[111]通过HPH方法处理生物油,生物油的平均分子量减小,其组成发生了很大的变化,生物油中的糠醛、左旋葡萄糖、二乙氧基甲基醋酸盐等含量明显增加,醋酸和1,2-二醇明显减少,精制后的生物油在40℃以下放置60d,黏度只增加了13.9%,而原生物油在相同的条件下却增加了56%,说明高压均相反应能够有效改善生物油的品质。
还有一些方法可以对生物油进行提质。萃取法是利用被分离组分在2种互不相溶的溶剂中溶解度的差异而达到分离目的的一种方法;与它类似的还有利用膜达到分离目的的膜分离法,膜分离以半透膜为选择障碍层,在膜两侧施加一定的压差,使不同的溶质在通过液层时具有不同的扩散系数,从而将各溶质分离。膜分离高效、节能、环保、选择性高、富集倍数大且操作简便。但由于生物油的复杂性,因此还没有在真实生物油体系中应用膜分离技术。
由于生物油含氧量的问题长期得不到良好的解决方法,所以有一些新思路被提了出来。一些研究者认为应该将生物有体制改造成结构简单的含氧化合物,这些化合物本身也可以作为燃料使用,并非必须降低生物油含氧量才能使用。为实现品位提升,调控的目标是使长链和结构复杂的分子裂解,醛和酮的不饱和键加氢,正构碳链的异构化,氮和硫原子的加氢脱除以及有机酸和醇的酯化等。这些反应均可在金属/酸碱催化中心上协同完成。Tang等[112]设计了以下模型加氢酯化归并反应:醛+H2+酸酯。将乙醛和丁醛分别与乙酸构成模型体系,在酸性载体HZSM-5和Al2(SiO3)3上负载Pt制成双功能催化剂。在氢压1.5MPa和150℃条件下,醛和酸确实转化生成了乙酸乙酯和乙酸丁酯。这个结果说明,在生物质热解油提质过程中,提质反应的偶合、归并是完全可能的。
此外,将生物油进行分离提取出某种价值较高的化工产品也不失为一种很好的处理方法。如何提取其中含量较少但价值很高的化工产品被很多研究者,尤其是商家所关注。生物油中可提取的化工产品有与醛形成树脂的多酚、食品工业中的添加剂和调味剂、制备除冰剂的挥发性有机酸、左旋葡聚糖、羟基乙醛和可用于制药、合成纤维、化肥工业的物质等。
3.3.7 生物油示范工程与应用
3.3.7.1 国外生物质快速热裂解技术的商业化进程
几种典型热裂解反应器的特性评价见表3-20。
表3-20 几种典型热裂解反应器的特性评价

早在20世纪80年代初期,欧盟就开始使用流化床装置把农林废物转化为燃料油和木炭,并在意大利建造了设计容量为1t/h的欧洲第一个示范工厂,液体产物的产率在25%左右。在同一时期,瑞士的Bio-Altemative公司也建成了一套50kg/h的固定床中试装置,主要用于生产焦炭副产品油,焦油产率仅为20%。虽然这两个项目属于常规热裂解工艺,液体产物产率低,却极大地激发了欧洲对生物质热裂解技术的兴趣。自20世纪90年代生物质热裂解液化技术在欧洲开始蓬勃发展,随着试验规模的扩大和工艺的完善,各种各样的示范性和商业化运行的生物质热裂解装置在世界各地不断地被开发和建设。荷兰Twente大学生物质小组(BTG)研制了一套10kg/h的转锥式反应器模型,并建立了中试和商业装置,此后还研制了容量为200kg/h的改进旋转锥式反应器。希腊可再生资源中心建造了利用生物质热裂解产物焦炭作为热裂解过程中加热燃料的10kg/h的循环流化床反应装置,液体产率高达61%。西班牙的Union Fenosa电力公司于1993年建立了基于加拿大Waterloo大学流化床反应器技术的200kg/h的热裂解示范厂,之后又开发了2~4t/h的商业规模生产线。意大利ENEL从加拿大Ensyn公司购买了一台给料量为10t/d的循环流化床反应器热裂解设备,在北美,一些规模达到200kg/h的快速热裂解商业与示范工厂正在进行。为使生物质热裂解早日实现商业化,由英国Aston大学生物质能研究室Tony Bridgwater教授牵头,由欧盟和国际能源机构(IEA)共同资助的热裂解协作网(PyNe)项目有来自欧美的17个国家参加,研究人员对生物质热裂解基础理论及生物油特性与应用做了大量研究工作,取得了很大进展。实现商业化已成为当今世界生物质快速热裂解技术的发展趋势。荷兰皇家航空公司开通从首都阿姆斯特丹到美国纽约的生物燃油航班。据了解,这个航班使用的生物燃料是以餐厨废油,也就是俗称的“地沟油”为原料,提炼、加工而来的。
而在古巴,研究人员以麻风树种子为原料生产出生物柴油,并在轻型汽车中试用成功。
加拿大Ensyn公司是最早建立生物质快速热裂解商业化运行的公司,自1989年以来开始商业化生产和出售生物油,当前该公司仍在运行的最大设备在2002年建于美国威斯康星州,日处理量75t(图3-18),该反应器为流化床反应器,主要的生物质物料为木材废物,平均产油率在75%,生产的生物油主要用来提取食品添加剂和一些聚合物,然后将剩余的生物油在锅炉中燃烧。

图3-18 Ensyn公司75t/d生物质热裂解示范台
加拿大Dynamotive公司在2001年和2005年相继成功运行了15t/d与100t/d的示范性生物质热裂解试验台以后,于2007年在加拿大安大略省建立了目前世界上最大的生物质快速热裂解工厂,日处理量在200t(图3-19),反应器为流化床。该公司的主要生产流程如图3-20所示,预处理后的干燥物料被送进鼓泡流化床反应器中,加热至450~550℃,热裂解后的气体进入旋风分离器,焦炭得到脱除,剩余的气流进入喷淋冷凝塔内,利用已经制取的生物油喷淋来实现冷凝。剩余的不可冷凝气体被重新送回反应器内,提供整个过程所需要的大约75%的热量。生物油的产率在65%~75%。

图3-19 世界上最大的生物质热裂解装置

图3-20 Dynamotive生物质热裂解工艺流程
澳大利亚近年来在生物质快速热裂解商业化推广上也有很大进展。Renewable Oil公司于2007年利用Dynamotive公司技术建成商业性示范工厂,从生物质物料接收开始,经过物料预处理、储备,再进入热裂解,最后储存生物油。每天处理生物质物料的能力为178t,物料主要以小桉树为主,同时也处理其他木材废料、甘蔗渣或其他生物质。澳大利亚有辽阔的海岸线,土地由于海水入侵,盐渍化严重,需要大量种植生存力强、又能抵抗海水入侵的小桉树,因此这不仅保证了生物质热裂解物料的供应同时又促进了农民种植小桉树的积极性,形成了生态与经济的良性循环。
国内虽然生物质热裂解技术商业化起步较晚(表3-21),但发展迅速,目前也已经出现了几家较大的商业示范公司。安徽易能生物能源有限公司联合中国科学技术大学开展生物质热裂解液化技术研究,2004年8月成功研制出每小时处理20kg物料(时产10kg生物油)的小试装置。2005年8月他们将上述装置改造成自热式的热裂解液化小试装置。2006年4月,该公司又开发出每小时处理120kg物料的自热式热裂解液化中试装置(时产60kg生物油)。目前,该公司已成功开发出500kg/h、1000kg/h生物油生产设备,首期建设用地60亩,项目投资总额为7220万元,在2007年建成20台1000kg/h生物油生产设备并布入网点。
表3-21 我国生物质热裂解生产生物油的一些技术

青岛福波思新能源开发有限公司已经建成每天吞吐24t物料规模的工业生产示范站。该装置使用自身产生的燃气加热,并可依据市场对产品的需求情况,通过调节热裂解温度及物料裂解滞留时间,调整产品(气、炭、油)的产出比率。但是和国外相比,我国生物质热裂解公司规模偏小,且生物油产率均不高(50%左右),并未形成完善的营销管理体系,较多地依靠政府支持。
潍坊金鑫达生物化工有限公司利用自主研发的生物能源技术,以每天潍坊市区内200t剩饭剩菜和150t地沟油为原料,每年生产生物柴油4万多吨,生产完柴油则用沼气发电,沼渣则生产成无公害生物肥,实现了整个餐厨废物的全部资源化利用。
由北京林业大学研制的全国首家自热式流化床生物质快速热解中式生产线落户平泉,并于2012年9月5日投入调试运营生产。这一自热式流化床生物质快速热解中试生产线是北京林业大学木质材料科学与工程研究所常建民教授用八年时间研制成功的,该技术生产线在国内尚属首家,在国际处于领先地位,生产线以农林废锯末、秸秆、柴草、林业“三剩物”为原料,每吨废物可生产出0.6t生物油、0.4t生物炭,其中生物油用于家具胶制作原料,生物炭用于土壤缓释剂、生物肥料等。
武汉阳光凯迪新能源集团实现了用废柴火、秸秆制造燃油的过程,油内含有3种成分,50%为生物柴油、50%为生物航空油和生物汽油。当柴火被收集后,首先蒸发部分水分,随后粉碎成小颗粒送到炼油厂。在专用气化炉里,这些柴火颗粒会通过化学热分解,在高温高压条件下分解成气态,并最终在催化剂作用下合成为液化油品,此时出来的是航空煤油、汽油和柴油的混合物,由于三种油的密度、分子量不一样,还要再通过物理方法,让三种油进一步分离。阳光凯迪采用的化学热分解技术,利用农林废物生产液体燃料,全过程的整体能源转化率超过60%。