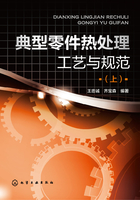
1.6 机械零件复合热处理工艺及特点
1.6.1 复合热处理工艺的概念
近年来,为了节约能源,使零件获得更好的力学性能,国内外开始把各种强韧化热处理、表面合金化、表面淬火、表面功能性覆层、形变强化等工艺进行多种类型的组织和复合,使机械零部件的性能有了很大的提高。因此传统的、单一的热处理方法难以满足满足要求时,采用复合热处理的方法,使零件获得理想的优良性能,同时可以尽量节约资源、降低成本,提高生产效率,并把它开辟为新的热处理技术领域。
复合热处理是指两种或两种以上的热处理复合,或是将热处理与其他加工工艺复合,使各工艺间互相弥补增强,以更大限度地挖掘材料潜力,使零件获得单一工艺无法达到的优良性能与技术要求。例如强韧化处理、表面合金化、表面淬火、表面功能性覆盖、形变强化等工艺进行了多种类型的组合与复合,从而使零件的性能有了很大提高,成为目前国际上开辟的热处理技术领域。因此,复合热处理技术具有十分广阔的应用前景。
1.6.2 复合热处理技术的特点
复合热处理是以使工件获得必要特性的各种单一传统热处理工序为基础,与以提高性能、增加功能为目的而增加的热处理或其他有关工序的组合,或由前后有关的工艺改进而结合在一起的,能提高生产效率、降低成本的具有复合功能的新工艺。故复合热处理实际上是几种热处理工序以适当的顺序和方式组合起来的一种方法。它具有参与组合的几种热处理工序的综合工艺效果。复合热处理还包括热处理与为了提高工件的强度、耐磨性、耐腐蚀性等而增加的有关前后工序的组合,单一的热处理工序,可以组合成多种复合热处理工艺。
复合热处理技术不是几种单一的热处理工艺的简单叠加,而是要根据工件使用性能的要求和每一种热处理工艺的特点将它们有机组合在一起,达到取长补短、优势互补的目的,从而克服了单一热处理工艺所达不到的提高工件综合性能、满足更加复杂的使用要求。或为了降低生产成本、节能环保、提高生产效率目的。复合热处理技术,诸如渗氮+高频淬火(或淬火)、氮碳共渗+高频淬火、渗碳淬火+低温渗硫、调质+硫氮共渗、整体淬火+氧氮化处理等,更能发挥复合热处理技术的优点,是未来热处理技术的重要发展方向之一。
1.6.3 复合热处理的分类和主要内容
(1)多种热处理方法的复合
例如:表面合金化与淬火;渗碳或碳氮共渗后的淬火(重新加热淬火或渗后直接淬火);渗碳或渗氮后用激光进行表面淬火;表面硬化与低温回火下的表面化学热处理;淬火处理+高、中温回火温度下的化学热处理;两种化学热处理方法的复合;化学热处理与涂层(化学沉积或电镀)的复合;化学镀与热处理的复合。
(2)热处理与其他工艺的复合
例如:压力加工与热处理复合的形变热处理;整体或表面强化与表面形变强化(辊压、喷丸);整体或表面强化+表面功能性覆层(电镀、喷涂以及有机树脂涂层等)。其中形变化学热处理是把塑性变形加工工艺与化学热处理(渗氮、渗碳、氮碳共渗、渗硼、渗硫以及渗金属等)结合起来,能够大幅度提高钢铁零件抗磨损、耐疲劳等与表面强化有关的性能。复合热处理的分类与实例见表1-47。
表1-47 复合热处理的分类与实例

①表面合金化+淬火 将零件经过表面合金化处理后,再进行直接的或再加热淬火,可满足零件的硬韧结合,硬而不脆的淬火要求,使零件具有要求的性能。渗碳、碳氮共渗、氮化、渗硼等均为十分重要的合金化方法,目前在汽车、机械、石油、化工、国防、航天航空等领域,进行零件的表面合金化+淬火处理,已经成为延长零件使用寿命与性能的重要措施与手段。
a.氮化(或软氮化)+淬火。该复合处理工艺如图1-36所示,此用于心部也能淬透的钢,其含碳量为0.95%~1.05%,铬含量1.30%~1.65%钢氮化后,再进行整体加热淬火和低温回火。由于表层渗入氮而使钢的Ms点降低,故表层冷却速度快于心部,但比心部马氏体转变要迟,这样就形成了零件表层残留压应力,从而提高了零件的疲劳强度。

图1-36 软氮化+淬火的复合工艺曲线示意图
加热时,在奥氏体过程中,氮化物分解后,使氮原子向心部扩散固溶,淬火则形成固溶于氮、碳的马氏体,零件表面获得残余压应力,故提高了零件耐磨性和疲劳强度,经过该工艺处理后的材料的使用寿命可提高3~6倍。如果材料采用淬火+冷处理+低温回火,将使表层的马氏体转变更充分,表层会残留较大的压应力。
b.氮化(软氮化)+高频淬火。将调质处理后的零件氮化处理,氮化层虽硬但较浅(一般0.2~0.5mm),如果氮化后再进行高频淬火,则使表层氮原子向心部基体扩散,有效消除氮化白亮层,减小脆性;同时通过淬火可得到微细的含氮的马氏体,不仅提高氮化层的深度,也使表面硬度有所提高,从而发挥坚硬的氮化层的潜力。事实证明,采用该复合处理与单独的软氮化或高频淬火相比较,可有效提高表面硬度、疲劳强度,同时增加了硬化层深度,是提高使用寿命的重要工艺方法。
c.氮化+激光熔凝。金属的激光熔凝处理可明显细化晶粒,从而提高晶界所占的体积百分比,利用激光熔凝技术可使材料表面晶粒细化,进而提高晶界的活性和加速扩散速度,达到加速化学热处理过程的目的。
20钢原始组织进行520℃×12h气体渗氮,经回火后在原始区渗氮层的白亮层中可以清晰地分辨出ε相,扩散层中为γ'相(Fe4N)的针状组织,由针状组织的分布判断扩散层深度,见图1-37(a)。激光熔凝工艺改变了20钢的原始组织结构,产生了细板条和针状马氏体,随后进行渗氮处理,回火后经金相观察可看见表面的白亮层ε相,但在激光区的截面内部却没有看到γ'相(Fe4N)的针状组织析出,如图1-37(b),其原因在于激光熔凝处理后的晶粒尺寸细化,γ'相的针状组织很小,故金相观察很难确定激光区的渗氮深度。采用能谱分析通过检测试样截面中的氮含量,可绘出渗氮时间、含氮量与表面距离之间的关系,见图1-38。激光处理区的渗氮不同时间后渗氮化合物层与扩散层的深度比较见图1-39,可以看到原始状态下的20钢,渗氮12h后的渗氮深度,在激光区只需要9h即可达到,在过渡区渗氮12h的深度与基体区渗氮15h的深度相仿。

图1-37 20钢在不同原始状态下气体渗氮12h的金相组织

图1-38 渗氮时间、含氮量与渗氮深度的关系曲线

图1-39 渗氮层深度的比较
事实表明,激光熔凝处理后的渗氮硬度比单纯激光熔凝硬度提高33%,耐磨性提高2倍,比普通气体渗氮提高4倍,比基体摩擦系数降低了26%。这均源于晶粒的细化增加了氮在晶界的扩散速度,缩短了渗氮时间,使表层的氮浓度增加,形成了γ'相和ε相,提高了表面耐磨性。
d.渗硼+淬火。该工艺改变了基体组织、性能及表面应力状态,避免了高硬度的“蛋壳状”单一渗硼层的出现,文献指出,40Cr采取渗硼→空冷、渗硼→淬火→回火等复合处理工艺,在滚动→滑动时的磨损曲线见图1-40,渗硼空冷、渗硼+淬火+高温回火后获得的基体组织分别为粗片状珠光体、回火索氏体,其硬度与强度均很低,承受压缩负荷能力较小,渗硼层易被压碎,渗硼+淬火+低温回火处理后,尽管工作表面硬度高、有压应力存在,但在负荷作用下容易萌生疲劳裂纹并扩展,只有渗硼+淬火+中温回火后获得了回火托氏体组织,硬度在40~42HRC,硬度与强度均得到提高,同时渗硼层表面残余压应力存在,从而有效发挥了表面的耐磨性。另外,电镀+热扩散处理也具有良好的效果。

图1-40 40Cr钢渗硼复合处理后的磨损曲线
②表面硬化+回火温度下的表面化学热处理 将钢铁零件淬火后,零件在不同温度下进行回火处理时与化学热处理(如软氮化、硫氮共渗、渗硫等)有机结合,可有效节约能源和缩短周期,从而获得优良性能的组合。
a.表面硬化+低温回火下的表面化学热处理。
·渗碳淬火+低温渗硫。渗碳淬火后,在回火过程中同时渗入硫原子,可增加工件表层耐磨、耐咬合性能,故将180℃低温渗硫+低温回火合并进行。
·氮化+低温渗硫。氮化后可获得极高的硬度,190℃低温渗硫,可使工件表层兼有耐磨与润滑性的有机结合,从而具有优良的表面应能。
·氮化(软氮化)+高频淬火+低温渗硫。将低温渗硫与高频淬火后的低温回火工艺结合,赋予了零件高的耐磨性和耐疲劳性,同时具有强韧和减磨的复合特性,从而有效发挥硬化表层的潜力。
b.淬火处理+在高、中温回火温度下的化学热处理。
·调质处理+软氮化(硫氮共渗)。考虑到软氮化与硫氮共渗温度均在520~570℃范围,而钢的调质处理回火温度大多在此区域,因此调质处理过程中进行软氮化,可在强韧的基体上形成耐磨、耐疲劳的表面层,硫氮共渗还具有良好润滑性,故提高了零件的使用寿命。
·分级淬火+软氮化。将奥氏体化后的零件淬入含有活性碳、氮原子的浴槽中进行马氏体分级淬火处理,在分级保温过程中,同时进行低温碳氮共渗的综合热处理工艺。该工艺使表面形成了具有耐磨、抗腐蚀、抗疲劳等性能的渗层,如W6Mo5Cr4V2刨刀经过820℃预热+1230~1235℃淬火加热,在560℃分级淬火并复以软氮化,随后在该温度下回火并复合进行软氮化三次,表面硬度可达到66~68HRC,处理后的该类零件的使用寿命可提高数倍。