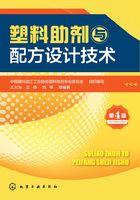
4.2 环保型塑料增塑剂研究进展
(郭海永,梁冰,吕艳艳等)
4.2.1 概述
随着塑料工业的迅速发展,橡塑材料增塑剂的需求量逐年增大。据统计,目前已商品化的有500多种,其中以邻苯二甲酸酯类增塑剂的生产和消费最大,尤其是邻苯二甲酸二辛酯(DOP)和邻苯二甲酸二丁酯(DBP),由于DOP增塑效率高,挥发性低,迁移性小,柔软性和电性能等综合性能优良,除大量用于PVC树脂外,还广泛用于各种纤维素树脂、不饱和聚酯、环氧树脂、醋酸乙烯树脂和某些合成橡胶中。但自邻苯二甲酸二辛酯(DOP)被美国癌症研究所(NCI)怀疑有致癌作用后,DOP的环保问题逐渐引起人们的重视,其使用范围受到一定限制。随着全球范围内环保要求的提高,对添加到橡胶、塑料制品中的增塑剂提出了更高的要求,世界各国针对性地制定了相关的环保战略;2011年2月,欧盟将DEHP、DBP、BBP三种邻苯二甲酸酯直接列入化学品淘汰名单。美国、日本、韩国、澳大利亚、阿根廷等国也已对玩具中邻苯二甲酸酯的含量做出了与欧盟类似的限定。目前我国已成为最大的增塑剂生产国、进口国和消费国,然而国内环保型增塑剂产品只占总量的三成,与欧盟REACH法案、RoHS、WEEE指令和国内塑料制品绿色、安全法规的要求很不适应。
本节将环保型增塑剂按照其化学结构分为七类:环氧类、醇酸酯类、多元醇芳香酸酯类、脂肪族二元酸酯类、对苯二甲酸酯类、低分子量聚酯类、其他类。
4.2.2 环保增塑剂
4.2.2.1 环氧类
环氧植物油具有无毒、多功能、低成本、无污染等优点,在橡塑工业中的应用前景十分广阔。环氧大豆油常温下为无毒无味的液体,是国内外开发应用较早的一种环氧型增塑剂,在塑料、涂料、新型高分子材料、橡胶等工业领域中有广泛的应用。环氧大豆油是美国药物管理局批准的唯一可用于食品包装材料的环氧类增塑剂,目前在许多国家已被允许用于食品及医药的包装材料,同时还具有优良的热稳定性、光稳定性、耐水性和耐油性,已发展成为第三大类增塑剂。
王龙江等以大豆油为原料,大孔强酸型树脂为催化剂,过氧甲酸为环氧化剂将大豆油与双氧水、甲酸(乙酸)反应制得环氧大豆油产品。
徐晓鹏等以葵花油为原料采用无溶剂工艺合成了环氧葵花油,进一步研究了其对聚氯乙烯(PVC)热稳定性、增塑效果的影响。结果表明,反应温度为60℃、反应时间为5h、过氧化氢和葵花油摩尔比为2:1、催化剂用量为原料总质量的3%时,环氧葵花油的环氧值达到了6.78%;环氧葵花油与钙锌稳定剂并用具有协同作用,可以增强橡胶、PVC的长期热稳定性,效果比环氧大豆油更好;环氧葵花油还能使PVC的玻璃化转变温度、硬度、拉伸强度降低,断裂伸长率升高,可以作为PVC增塑剂使用。
刘汝宽等以地沟油为原料经地沟油甲酯的制备、环氧甲酯的制备,制备出合格的脂肪酸甲酯原料,其产品满足GB/T 20828—2007的要求,可以作为制备环氧甲酯的理想原料,为地沟油的高质化利用提供基础数据。通过单因素试验和正交试验,建立了地沟油脂肪酸甲酯为原料制备环氧甲酯产品的最优生产工艺。即温度65℃,反应时间3.5h,H2O2用量30g/50g甲酯。
华东理工大学与江阴市向阳科技有限公司联合研究开发的“新型生物环氧增塑剂(环氧脂肪酸甲酯)”项目产品,是以可再生物质脂肪酸脂类和有机酸为主要原料,在过氧化氢存在的条件下发生环氧化反应合成的一种新型生物环氧增塑剂,其生产工艺包括原材料预处理、酯交换反应、精馏、环氧化反应、水洗脱酸、蒸馏脱水等六个步骤。本项目操作简便安全、对环境没有污染。项目产品具有耐寒、耐水性强等特点,对提高塑料制品的柔韧度、光泽度、热稳定性和光稳定性等有很好的效果,在很多领域可以替代或部分取代DOP、DBP、TBC、ATBC等增塑剂。
4.2.2.2 醇酸酯类
柠檬酸三丁酯(TBC)是一种良好的环保塑料增塑剂,它已经通过美国FDA认证,可作为一种无毒、低毒或生物降解性好的新型橡塑助剂取代传统的邻苯二甲酸酯类增塑。柠檬酸三丁酯一般是以柠檬酸与正丁醇为原料,在催化剂的作用下合成的。传统的生产工艺以浓硫酸为催化剂,该法副反应多,产品纯度不高,设备腐蚀严重。鉴于浓硫酸催化酯化的各种弊端,新型催化剂的研究成为柠檬酸三丁酯合成技术的焦点。目前,应用于合成柠檬酸三丁酯的催化剂主要有对甲苯磺酸、无机盐、杂多酸以及固体超强酸等。
王百军等采用活性炭固载对甲苯磺酸催化合成了环保增塑剂柠檬酸三丁酯(TBC)。考察了酸醇比、催化剂用量、反应时间、反应温度等工艺条件的变化对柠檬酸三丁酯合成的影响。实验得到制备柠檬酸三丁酯最佳工艺条件:酸醇比为1:4.0,催化剂质量浓度为2.2%,催化剂负载量为21.0%,反应温度为120℃,反应时间3.0h。在以上条件下,酯化率可达到98.3%。
李耀仓等以柠檬酸和正丁醇为原料,一水合硫酸氢钠为催化剂合成了柠檬酸三丁酯。通过实验确定了最佳反应条件:0.1mol柠檬酸,醇酸物质的量之比为4.8:1,一水合硫酸氢钠是合成柠檬酸三丁酯的优良催化剂,其用量4.5g,反应时间2.5h,反应温度110~120℃,酯化率达到88.1%,产品为微黄色透明油状液体,折光率为n25=1.4431,沸点为225℃,并用红外对产品进行鉴定。通过TBC和邻苯二甲酸二辛酯(DOP)增塑聚氯乙烯(PVC)进行对比研究结果表明,当m(TBC):m(PVC)=25:100时,TBC增塑PVC材料的拉伸强度、断裂伸长率及低温性能与DOP增塑PVC材料性能相当。
隆金桥等微波固相法合成了MCM-41固定AlCl3固体酸催化剂,并在聚四氟乙烯罐内微波辐射催化合成柠檬酸三丁酯,考察了诸因素对酯化率的影响。结果表明:微波固相法制备的MCM-41固定AlCl3固体酸催化剂表面存在L酸中心,对TBC的合成具有较高的催化活性,催化剂对设备不腐蚀,环境污染少,能重复使用等优点。在醇酸物质的量比为4:1,催化剂用量为0.5g,微波辐射功率为700W,反应时间为10min条件下,酯化率可达到93.4%。
4.2.2.3 多元醇芳香酸酯
多元醇芳香酸酯与DOP相比,具有相容性好,耐寒性好,抗静电性、抗污染性能显著,热稳定性突出,挥发性低,耐光变色性好等特点,并且毒性低,是一类环保型的增塑剂,是DOP的理想替代品,具有很好的市场前景。李志成等在对甲苯磺酸催化下、使用环己烷作带水剂,以苯甲酸和二甘醇为原料合成环保增塑剂二甘醇二苯甲酸酯(DEDB)。研究考察了酸醇摩尔比、催化剂用量、带水剂用量和反应时间等因素对产率的影响。确定了最佳工艺条件:n(苯甲酸):n(二甘醇)=2.0:1.1、催化剂用量(以苯甲酸的摩尔数计)3.0%、环己烷12mL、回流反应时间8h,目标产品的产率为98.0%。
陶绪泉等以间甲基苯甲酸和二甘醇为原料,钛酸四丁酯为催化剂合成了二乙二醇二间甲基苯甲酸酯。考查了催化剂及其用量、反应温度、原料配比等条件对反应的影响,经过试验确定适宜工艺条件:甲苯为带水剂,催化剂用量为总反应物的0.5%,醇酸摩尔比为10:22,回流反应时间4h,反应回流温度210℃,转化率达93.7%。产品结构分别用IR、NMR进行表征,并对其作为PVC增塑剂的增塑性能进行了初步评价,其性能良好,是传统的邻苯二甲酸酯类增塑剂的良好替代品。
张彩琴等以甘油、六氢苯酐为原料,钛酸四正丁酯为催化剂,2-乙基己醇为封端剂,环己烷为带水剂,经脱水缩聚、减压蒸馏制备聚六氢苯酐甘油酯。探究实验得到合成聚六氢苯酐甘油酯的最佳醇酸摩尔比、催化剂和封端剂用量。通过红外光谱分析(FTIR)、热重分析(TG)、高效凝胶色谱分析(GPC)等对聚酯的结构、热稳定性及平均分子量进行了表征,并将该聚酯加入到聚氯乙烯(PVC)中,按照定配方制得PVC试片。结果表明:佳反应条件是六氢苯酐、甘油的摩尔比为1.0:1.4,2-乙基己醇、六氢苯酐的摩尔比为0.8:1.0,催化剂用量为甘油、六氢苯酐和2-乙基己醇总量的1.0%;产品酸值在1.55mgKOH/g左右,平均分子量在4500左右,酯化率达到99.6%;产品呈淡黄色,热稳定性良好;制得PVC试片的拉伸性能和热稳定性较高,聚酯的迁移率较低。
4.2.2.4 脂肪族二元酸酯类
脂肪族二元酸酯类耐寒性增塑剂因其低温性能优良,耐冲击性强,塑化效率高及黏性好等特点,近年来发展较快,需求逐年上升。
刘勇等在邻苯二甲酸酯类增塑剂的基础上通过加成方法使其苯环转变成饱和的环己烷结构制成的新型环保型酯类增塑剂HEXAMOLL DINCH,主要化学成分是1,2-环己二羧酸二(异壬基)酯。研究表明,无论是过氧化物硫化体系,还是硫黄硫化体系,与添加增塑剂DBP、DOP、DBS和DOS的胶料相比,添加HEXAMOLL DINCH的NBR胶料的拉伸强度和拉断伸长率较高,而且高温压缩永久变形性能较好。添加增塑剂HEXAMOLL DINCH的NBR胶料的耐低温性能优于添加邻苯二甲酸酯类增塑剂DBP或DOP的胶料。增塑剂HEXAMOLL DINCH具有优异的耐抽出性能,添加增塑剂HEXAMOLL DINCH的NBR胶料耐ASTM1#油的体积收缩率较小,耐油ASTM3?的体积膨胀率与添加增塑剂DBP、DOP、DBS和DOS的胶料相当。HEXAMOLL DINCH作为环保型无毒增塑剂,完全可以替代邻苯二甲酸酯类增塑剂和开链脂肪族二酸酯类增塑剂,在工业橡胶制品中推广使用,也适用于医疗器具、运动器材、玩具和食品包装等敏感性应用领域。
由赵志正编译的文章叙述了将己二酸二丁氧基乙酯(DEBA)增塑剂加入丁腈橡胶БНКС-18胶料中,制造能在俄罗斯北方高寒地区使用,并与石油接触的橡胶密封件的研制及试验结果。文中着重分析了对橡胶材料产生重大影响的扩散过程(包括介质的渗透及增塑剂的抽出)。结果表明,增塑剂DBEA在制造耐寒橡胶密封件方面的前景十分广阔。
韦晓竹等研究了在实验室条件下,以硫酸、磷酸为催化剂合成三甘醇二异辛酸酯的最佳工艺条件,并初步探讨了和
固体超强酸催化剂的催化效果。结果表明,硫酸催化的最佳反应条件为:m(硫酸)/m(三甘醇)=1.2%,n(异辛酸)/n(三甘醇)=2.15,反应温度220℃,反应时间6h,酯化率达到96.3%;磷酸催化的最佳反应条件为:m(磷酸)/m(三甘醇)=3.0%,n(异辛酸)/n(三甘醇)=2.15,反应温度220℃,反应时间7h,酯化率达到95.2%;
和
固体超强酸催化剂也具有较好的催化效果,进一步研究后有望应用于实际工业生产。
以新型催化剂合成开链脂肪族二元酸酯类增塑剂的改进型实例相对较多,例如合成己二酸二异辛酯、聚己二酸三甘醇酯、混合二元酸二丁酯、丁二酸、己二酸混合二乙酯等。
尼龙酸二异丁酯(DIBA)是一种良好的耐寒增塑剂,具有较好的相溶性,主要用于各种聚氯乙烯、纤维素树脂、氯丁橡胶等的增塑剂,增塑效率高、加工性能优良、可以改善制品的低温柔韧性,降低压缩永久变形。许京伟研究了尼龙酸与异丁醇在质子酸催化下直接酯化并减压蒸馏制备尼龙酸二异丁酯,技术上和工艺上都是可行的。该工艺制备的尼龙酸二异丁酯具有良好的质量。制备尼龙酸二异丁酯工艺的优化条件为:酯化反应在搅拌下进行,催化剂用量为反应总质量的0.35%,n(异丁醇):n(尼龙酸)=2.5:1,反应温度为145~155℃,反应时间4h左右,蒸馏釜压力不宜大于5kPa。
醚酯型增塑剂是一类新型环保无毒增塑剂,此类增塑剂因具有良好的耐高低温性能而备受关注。其分子中不仅含有极性极强的酯基,同时还含有弱极性的醚基,使之与极性高聚物具有良好的相容性。林新花等研究了环保醚酯型增塑剂TP-95和几种常用增塑剂对聚氯乙烯(PVC)的塑化效果、力学性能、耐寒性、耐热性及耐抽出性能的影响。结果表明:与添加的几种增塑剂相比,TP-95具有显著的增塑软化作用;随着增塑剂用量的增加,最低转矩明显下降,塑化时间缩短,塑化效果随之增强;与DOP和TOTM相比,TP-95表现出良好增塑效应及耐寒性;增塑剂用量均为50份时,TP-95的PVC开始热降解温度高于DOP和DOA;在水和环己烷介质中,随着随着增塑剂用量的增加,抽出损失随之增加;在环己烷介质中,TP-95的抽出损失为4.40%,低于TOTM和DOA,具有良好的耐抽出性。
宋林勇等用对甲苯磺酸作催化剂,以己二酸与乙二醇单丁醚为原料,通过酯化反应合成己二酸-乙二醇单丁醚酯增塑剂的最佳反应条件为反应时间180min、醇酸摩尔比2.5、催化剂和带水剂甲苯的质量分数分别是醇与酸总用量的0.5%和30%。己二酸-乙二醇单丁醚酯增塑剂具有良好的耐高低温性能,添加10份可使ACM的脆化温度达到-35.0℃,且在150℃下能保持较好的物理机械性能。
4.2.2.5 对苯二甲酸酯类
对苯二甲酸二异辛酯(DOTP)是20世纪80年代开发的一种性能优异的增塑剂,与目前常用的邻苯二甲酸二辛酯(DOP)相比具有耐热、耐寒、难挥发抗抽出柔软性好及受热后电性能稳定等优点,可广泛应用于耐70℃电缆料(国际电工委员会IEC标准)及其他各种聚氯乙烯(PVC)软质制品中,还可以用作合成橡胶的增塑剂、农用塑料薄膜、冰箱门窗的密封条及润滑剂、涂料的添加剂等,是一种优良的环保材料,具有广阔的发展前景。
刘尚文研究对苯二甲酸与异辛醇在催化剂钛酸丁酯的催化作用下生成对苯二甲酸二辛酯的反应,通过实验分析了原料配比、催化剂用量、反应时间这三个因素对反应的影响,并对结果进行了讨论,找出优化方案。原料配比1:3.5;催化剂用量2.3%;反应时间6h;转化率达到99.193%。
常侠等以对苯二甲酸(PTA)与对苯二甲酸回收料按一定的比例混合为原料在复配催化剂作用下合成增塑剂对苯二甲酸二异辛酯(DOTP)。讨论了不同反应条件对合成工艺的影响,确定了最佳工艺路线为:纯PTA质量分数占总原料的10%,醇酸物质的量之比2.4:1,催化剂用量0.3%,反应时间6h,反应温度220℃;脱色剂用量为5%,脱色温度80℃,脱色时间1h。按此工艺所制得产品体积电阻率气≥9.0×1011Ω·cm。质联用分析结果表明:对苯二甲酸二异辛酯GC含量高达95.94%,与DOP相比性能优良,耐热性高,具有一定的经济效益。
4.2.2.6 低分子聚酯类
高分子量的聚甘油醇脂肪酸酯与很多聚合物树脂不相容。当聚甘油醇脂肪酸酯乙酰化后降低了聚甘油醇脂肪酸酯的氢键,乙酰化后能降低高分子量的黏度,使其与绝大多数聚合物树脂相容。APE所用脂肪酸为月桂酸、12-羟基硬脂酸以及混合物。通常合成工艺首先为酯化或者酯交换:聚甘油醇与脂肪酸酯化反应或者聚甘油与三甘油酯进行酯交换反应。然后将半成品与乙酸进行乙酰化反应得到最终产品。乙酰化聚甘油醇脂肪酸酯(APE)能用于化妆品、食品包装材料、玩具等软制品配方中,性能可与传统邻苯类增塑剂相媲美。
4.2.2.7 其他类
王春平以马来海松酸和正辛醇为原料、对甲苯磺酸为催化剂、正辛烷为带水剂,合成了环保增塑剂马来海松酸三正辛酯。观察了醇酸摩尔比、催化量、反应时间、带水剂用量和反应温度对酯化反应的影响,经单因素实验得到的最佳工艺条件为:n(马来海松酸):n(正辛醇)=1:4.5,催化剂用量为马来海松酸质量的3.6%,带水剂用量为马来海松酸质量的17.5%,反应温度180~200℃,N2保护下反应8.3h,产物为浅黄色透明油状液体,产率92.3%,经HPLC测定酯色谱纯度为99.24%,1 HNMR及FTIR对产物进行了结构表征,元素分析确定了产物分子式为C48H82O6,GPC测得其重均相对分子质量为755。测定其酸值、加热减量、开口闪点、体积电阻、黏度、热重曲线等,结果表明,马来海松酸三正辛酯符合增塑剂的性能要求。
含C6~C20的直链烷基、侧链烷基和环状烷基的吡咯烷酮都可用做PVC的增塑剂。其中以含C8和C12的吡咯烷酮最为常用。石万聪介绍了聚氯乙烯用新型增塑剂烷基吡咯酮的物理性能和应用,并比较了它与增塑剂DINP在PVC压延片材和泡沫塑料中的功效。结果表明,在采用优选配方时,它的功效优于DINP。
刘莹等以脂肪酸甲酯、甲醇、氯气为主要原料,在催化剂存在下,其制备最优反应条件为温度在70~85℃,反应时间在7~8h,氯气流量在50~60mL/min。工艺反应条件温和,对原料的要求较低,产品使用性能可以满足塑料增塑剂产品的使用要求。实验表明,氯代甲氧基脂肪酸甲酯可与其他主增塑剂配合使用,可替代DOP 60%~70%,该产品经用户使用后,反映良好,可用于聚氯乙烯塑料加工,代替部分主增塑剂邻苯二甲酸二丁酯、邻苯二甲酸二辛酯等,其塑料制品加工的可塑性,制品的拉伸强度、伸长率等均比单独使用DOP有不同程度的提高。
莫贯田以主要成分为十八脂肪酸甲酯的生物柴油为主要原料,以氯气为氯化剂,以过氧化苯甲酰为催化剂,合成了氯化脂肪酸甲酯。试验表明,当氯化脂肪酸甲酯氯含量小于或等于22%时,PVC试片进行拉伸、断裂伸长率及材料表面硬度等方面的材料性能,相当或略好于全部使用DOP的试样材料的性能,表明氯化脂肪酸甲酯在PVC材料中可以较大部分的替代DOP。氯化脂肪酸甲酯作为一种价格低廉、性能良好、无毒的的增塑剂,在PVC塑料加工以及相关的领域中有着广泛的应用前景和使用价值。
4.2.3 结论
增塑剂是橡塑料制品加工过程中添加的重要助剂之一。目前欧美对增塑剂的要求日益严格,寻求新型环保增塑剂成为研究领域的热点。国外正在大力推广无毒或环保及可生物降解的增塑剂。国内的环保增塑剂研制明显滞后于功能橡塑制品和国民生活的需要,国内增塑剂的生产正面临两大难题:一是副产品多,收率不高;二是产量低,成本高。随着科技的进步,生产企业应进行相应的产品结构调整,淘汰落后的生产工艺和品种,开发与生产无毒、价廉、环保的助剂是增塑剂行业亟待解决的主要问题,使我国增塑剂在科研开发和应用水平等方面赶上国际先进水平。