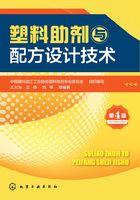
2.3 塑料助剂与塑料改性
2.3.1 概述
2.3.1.1 几个概念性问题
塑料助剂:是指由树脂加工成塑料制品的过程中所需要的各种辅助化学品。
塑料助剂门类庞杂、功能各异。根据功能和作用的不同,通常包括稳定化助剂、加工体系助剂和功能赋予剂三大体系。伴随塑料工业发展,塑料树脂结构的增加,成型加工技术的进步和应用领域对制品性能要求的提高,极大地促进了塑料助剂门类的扩大和产耗量的提高。
塑料改性:在把现有合成树脂加工成塑料制品的过程中或是在已有塑料制品的基础上,利用化学或物理方法改变塑料制品的一些性能,以达到预期目的,这个过程就是塑料改性。
塑料改性的含义很广泛,在改性过程中,即可以发生物理变化,也可以发生化学变化。塑料改性的应用范围也很广泛、几乎所有塑料的性能都可通过改性方法得到改善,如塑料的外观、透明性、密度、精度、加工性、力学性能、化学性能、电磁性能、耐腐蚀性能、耐老化性、耐磨性、硬度、热性能、阻燃性、阻隔性及成本性等方面。
塑料的改性是继聚合方法之外又一个获取新性能树脂的简捷而有效的方法。
2.3.1.2 塑料助剂的作用
众所周知,塑料制品的成型过程基本上是由配合、塑炼、成型等工序完成的。在这一过程中,树脂、助剂、加工设备(包括模具)是不可或缺的基本要素。相比之下,助剂在塑料配方中的用量微不足道,但其对制品加工和应用性能的改善和提高作用举足轻重。可以说,在聚合物树脂结构确定之后,助剂的选择和应用是决定制品成败的关键。
在大多数塑料改性的过程中,也必须添加一定量塑料助剂来达到目的,而塑料助剂在此起到举足轻重的作用。
2.3.1.3 塑料改性
为了满足不同用途的要求,除了积极发展新的合成树脂品种外,还应该在现有树脂的基础上,通过一些方法来达到目的。这也是充分发挥材料原有优点,克服其缺点,赋予制品以特殊性能的过程。这就是塑料改性的目的。
(1)塑料优缺点
①塑料的优点。大多数塑料质轻,比强度高;化学稳定性好,不易锈蚀;具有一定的韧性,即耐冲击性好;绝缘性好,导热性低;容易加工,加工成本低。
②塑料的缺点。耐热性差,易燃;易应力变形,尺寸稳定性差;强度不高;低温脆性;耐溶剂性差。
(2)塑料改性分类 按不同方式可有许多分类方法。
①按方法性质分(一般分法)。

②按制品性能、工艺分法分。发泡改性、交联改性、拉伸改性、大面积复合改性、填充改性、共混改性等。
③可分为表面改性(表面性能、外观等)及本体改性(强度等方面)。
(3)塑料改性的目的和意义
①投入少,见效快,效果好(事半功倍)。聚合物改性技术通常比合成一种新树脂容易得多(开发新品种要受到原料来源、合成技术、成本等多种限制),尤其是物理改性,在一般聚合物成型加工厂都能进行,且容易见效。
②可使聚合物制品价格大大降低。
③改善聚合物的性能,如力学性能、耐摩擦性、热性能、耐老化性、电性能等。填充改性,一般能改善耐低温性能、耐蠕变性、增加硬度等;增强改性可提高力学性能;共混改性可提高韧性。
④赋予制品以新的性能,如阻燃、导磁、发光等性能。
(4)聚合物改性的缺点
①使某些性能受到损害,如填充有时会使制品光泽、耐蚀性、绝缘性变差。
②加工困难。
③设备磨损严重,动力消耗大。
④产品力学性能各向异性。
在实际工作中,应根据制品性能要求,树脂本身优缺点,采取适当途径扬长避短,充分发挥效用。在这里就塑料改性和大家一起探讨一下塑料助剂的选择及作用。
2.3.2 塑料填充改性
在塑料成型加工过程中加入无机或有机填料的过程称为填充改性。是在塑料基体(母体)中加入模量高得多的非纤维类的材料(一般为微粒状)。
通常很多人认为填充改性是为了降低成本而进行的,实际上很多塑料制品如果没有填充助剂的加入的话,很难得到符合应用的效果。
填充改性的目的和效果如下。①改善力学性能,主要增加材料的模量,提高热变形温度和尺寸稳定性。②改善一些加工性能,突出的是减小成型收缩率。③改善塑料的着色性或印刷性。④赋予塑料某些特殊性能,如导电、导磁、阻燃、发光、杀菌等。⑤降低成本,以重量计,降低成本;以体积计,填充少量(20份以下)时降低成本作用并不明显,因填料的加入使制品密度增大。
2.3.2.1 填料的分类
通常把与塑料基体间界面相互作用小,力学性能改进效果小的添加材料称为填充材料(简称填料)或填充剂。填料可分为无机填料和有机填料两大类。
(1)无机填料


有机填料以状态来分类:

2.3.2.2 填料性质
填料性质主要指其组成、相对密度、粒径大小、粒子形状、颜色及特点(如刚性、着色性、导电性、导热性、尺寸稳定性、介电性、电绝缘性、耐化学药品性和耐水性、润滑性、耐热性、填充性等)。
较重要的填充材料有以下几种。
(1)CaCO3
①天然矿物经机械粉碎而成,粒径2~10μm,比表面积2~7m2/g;
②沉降型(合成),可达0.1μm,比表面积25~80m2/g。
价廉,色白,用途最广。
(2)硅酸盐类
①滑石,片状,对设备磨损小,易加工;刚性好,尺寸稳定性好,耐高温蠕变性好。
②石棉、云母——电绝缘性、热绝缘性;硅灰石、煅烧陶土。
(3)炭黑 耐老化、电性能好
(4)Al(OH)3、Mg(OH)3阻燃性好
(5)木粉、纸浆
(6)玻璃微球(珠)
2.3.2.3 塑料用填料特性
填料特性包括填料的几何特征和表面物理化学特性。

粒度:过筛目数——孔数,粒度分布:各个不同筛间的分布,用粒度分布仪测定。
物化特征:表面物理、化学性能,填料与塑料表面黏附能力。
有时表面具有成键能力会形成共价键,但一般情况下为范德瓦耳斯力(分子间作用力),主要是极性吸附。
可用广义的酸碱理论(路易斯)来分类进行估计。

共价键形成:如玻璃纤维经偶联剂处理后,有可能形成共价键结合。
表面形态和物化特性决定了填料的性质,有人将两者总结在一起,用“吸油值”来考察填料的特性,如不同温度下的吸油值;不同压力下的吸油值。
2.3.2.4 填充塑料形态的形成
混合过程如图2-5所示。

图2-5 填料在树脂中的混合过程与形态的形成
三种状态:A——理想状态;B——填料的聚集体;C——附聚:吸附树脂,并聚集起来。
A形态:当填料之间结合力较小,而填料与树脂结合比较好,同时填料量较少时易形成。
B形态:填料量较大,或填料间结合力较大,与树脂的亲和力较小的情况下易形成(填料堆砌坚固)。
C形态:填料量多时,易形成该种状态。
在填充过程中存在两种相反的倾向:剪切力使填料与树脂混合扩散(分散);填料间的亲和力使填料凝聚(聚集),如油、水的混合。因此,无限延长加工时间,并不会无限增加分散程度。
2.3.2.5 影响填充改性的因素
(1)填料形状 填料的形状对填充复合物性能影响较大,薄片状、纤维状对复合物的力学性能有利,但不利于成型加工。圆球状则相反。
(2)粒径 粒径大小及粒径分布对填充复合物性能影响很大,粒径越小,拉伸强度越大。
(3)填料的表面
①表面物理结构。非晶填料——表面凸凹少,基本属于光滑表面,如玻璃;结晶填料——由于存在熔点,在冷却时表面发生急剧变化,表面形成许多凸凹不平;表面物理结构特性:比表面积、微孔分布、各种物质吸附量。
②表面化学结构。表面化学结构与内部不同,尤其是表面官能团的存在会与空气中的氧气或水反应,与内部性质差别较大。
③表面处理。亲水表面→疏水表面(疏水化),可采用物理方法或化学方法等进行处理。机械研磨法,碱腐蚀法,涂覆法,表面化学反应法,如采用脂肪酸及其盐或酯、脂肪酰胺等对CaCO3进行涂覆。
④TiO2。紫外光照射,将Ti4+→Ti3+,有机物改性。
(4)硅烷偶联剂处理 炭黑:表面富化学活性,可采用化学试剂处理,如用HNO3、H2O2、O3等氧化剂处理,产生—CO—、—OH、—COOH;或用苯乙烯等在其表面进行自由基引发接枝聚合。
其他方法,如微胶囊化处理;比较重要的方法是偶联剂处理法。
2.3.3 偶联剂
偶联剂:指能够在特定条件下产生活性基团,并与黏结界面两侧的黏结物发生化学结合,从而增加界面的结合强度的一类化合物。是一种重要的、应用领域日渐广泛的处理剂,主要用作高分子复合材料的助剂。偶联剂分子结构的最大特点是分子中含有化学性质不同的两个基团,一个是亲无机物的基团,易与无机物表面起化学反应;另一个是亲有机物的基团,能与合成树脂或其他聚合物发生化学反应或生成氢键溶于其中。偶联剂被称作“分子桥”,用以改善无机物与有机物之间的界面作用,从而大大提高复合材料的性能,如物理性能、电性能、热性能、光性能等。
偶联剂的种类繁多,主要有硅烷偶联剂、钛酸酯偶联剂、铝酸酯偶联剂、双金属偶联剂、磷酸酯偶联剂、硼酸酯偶联剂、铬络合物及其他高级脂肪酸、醇、酯的偶联剂等,近年来还有稀土偶联剂、复合偶联剂。目前应用范围最广的是硅烷偶联剂和钛酸酯偶联剂。
2.3.3.1 硅烷偶联剂
硅烷偶联剂是人们研究最早、应用最早的偶联剂。由于其独特的性能及新产品的不断问世,使其应用领域逐渐扩大,已成为有机硅工业的重要分支。它是近年来发展较快的一类有机硅产品,其品种繁多、结构新颖,仅已知结构的产品就有百余种。
硅烷偶联剂的通式为RnSiX4-n,式中R为非水解的、可与高分子聚合物结合的有机官能团。
式中 R——有机基团,是可与合成树脂作用形成化学键的活性基团。
X——易于水解的基团,水解后能与玻璃表面作用。
n——1、2或3,绝大多数硅烷处理剂n=1。
根据高分子聚合物的不同性质,R应与聚合物分子有较强的亲和力或反应能力,如甲基、乙烯基、氨基、环氧基、巯基、丙烯酰氧丙基等。X为可水解基团,遇水溶液、空气中的水分或无机物表面吸附的水分均可引起分解,与无机物表面有较好的反应性。典型的X基团有烷氧基、芳氧基、酰基、氯基等;最常用的则是甲氧基和乙氧基,它们在偶联反应中分别生成甲醇和乙醇副产物。由于氯硅烷在偶联反应中生成有腐蚀性的副产物氯化氢,因此要酌情使用。表2-4列出了偶联剂商品名称、化学名称及其适用的树脂基体。
表2-4 偶联剂结构及其对树脂基体的适用性

近年来,相对分子质量较大和具有特种官能团的硅烷偶联剂发展很快,如辛烯基、十二烷基,还有含过氧基、脲基、羰烷氧基和阳离子烃基硅烷偶联剂等。
目前国内已有生产的常用偶联剂有沃兰、A-151、KH-550、KH-560、KH-570、KH-590、ND-42、B-201、B-202等。
硅烷偶联剂对玻璃、二氧化硅、陶土、硅酸盐、碳化硅等有显著效果;对滑石粉、黏土、硅灰石、氢氧化铝、铁粉稍差;对石棉、钛白、铁红效果不大;对碳酸钙、硫酸钡、炭黑效果更小。
2.3.3.2 钛酸酯偶联剂
依据它们独特的分子结构,钛酸酯偶联剂包括4种基本类型:①单烷氧基型,这类偶联剂适用于多种树脂基复合材料体系,尤其适合于不含游离水、只含化学键合水或物理水的填充体系;②单烷氧基焦磷酸酯型,该类偶联剂适用于树脂基多种复合材料体系,特别适合于含湿量高的填料体系;③螯合型,该类偶联剂适用于树脂基多种复合材料体系,由于它们具有非常好的水解稳定性,这类偶联剂特别适用于含水聚合物体系;④配位体型,该类偶联剂用在多种树脂基或橡胶基复合材料体系中都有良好的偶联效果,它克服了一般钛酸酯偶联剂用在树脂基复合材料体系的缺点。
钛酸酯偶联剂——对二氧化硅、碳酸钙、硫酸钙、氢氧化铝、氢氧化镁、金属粉、云母、钛白、铁红等效果较好。
2.3.3.3 铝酸酯偶联剂
铝酸酯偶联剂是由福建师范大学研制的一种新型偶联剂,其结构与钛酸酯偶联剂类似,其分子结构如图2-6所示。

图2-6 铝酸酯偶联剂与淀粉形式的三方双锥络合物模型
铝酸酯偶联剂在改善制品的物理性能,如提高冲击强度和热变形温度方面,可与钛酸酯偶联剂相媲美;其成本较低,价格仅为钛酸酯偶联剂的一半,且具有色浅、无毒、使用方便等特点,热稳定性能优于钛酸酯偶联剂。
2.3.4 塑料增强改性
近年来,塑料已作为结构材料广泛应用于工农业及国防等各领域,已由“代用材料”转为“必用材料”。
随着科学技术的不断发展和社会的不断进步,许多方面如交通运输(汽车、轮船、飞机等)、机电(电机叶片、机电设备骨架、轴承、轴瓦等)、石化、国防军工、航天等技术部门,对材料的要求提出了更高的要求。制造质轻、高强度、坚固、加工成型方便的新型材料,是材料学科面临的紧迫的任务。
在高分子方面,发展新品种;现有的高分子材料改性——提高物理力学性能指标。
增强改性:在高分子树脂中添加增强性填料(增强性材料)而提高材料力学性能的复合改性方法。
增强塑料:高分子树脂与增强性填料(增强材料)相结合而提高了机械强度的一种有机复合材料。
玻璃纤维及其制品如玻璃布、碳纤维等材料——增强材料。
棉布、纸张、无机粉料等材料——填料。
增强材料与填料相比:具有增强作用。广义上讲,增强改性也属于填充改性,是其中的特例。
20世纪60年代以来,填充改性得以迅速发展,为区别起见,国外将以玻璃纤维作填料的材料称为玻璃纤维增强塑料。
玻璃纤维增强塑料,我国俗称“玻璃钢”,具有较高的强度、良好的耐热性能、电性能、耐腐蚀性等,具有成本低、加工方便等优点,所以自问世以来,应用日益广泛,发展十分迅速。
玻璃纤维增强塑料的品种繁多,过去主要是热固性塑料,20世纪60年代后期,热塑性玻璃纤维增强塑料也得到发展。
2.3.4.1 增强塑料的特点
(1)比强度高 单位重量的强度——比强度。如玻璃纤维相对密度:2.25~2.9,与铝(2.7)相当;碳纤维为1.85;高分子树脂为0.9~1.4(PTFE为2.1~2.3);FRTP相对密度为1.1~1.6;只为钢铁(7.8)的1/6~1/5,表2-5列出了几种典型金属与FRTP的比强度。
表2-5 几种典型金属与FRTP(玻璃纤维增强塑料)的比强度比较

通常,FRP的强度、刚性随纤维含量的增大而提高,伸长率及允许变形降低,抗蠕变性能改善,动态载荷下耐疲劳特性成倍增加。高分子树脂为脆性时,增强后冲击强度成倍提高;高分子树脂为韧性时,冲击强度不变或有所下降。
(2)良好的热性能 热塑性塑料耐热性差,热变形温度低,通常在50~100℃范围使用;增强性热塑性塑料耐热性好,热变形温度高,通常在100℃以上使用。如PA6,热变形温度为50℃,FR-PA6的热变形温度在190℃以上。热变形温度是指一定载荷下(18.5kg/cm2),在一定升温速度下,试样达某一变形量的温度。FR-P,耐低温性能也大大改善,如FR-PC。
(3)其他性能 电绝缘性好;化学稳定性高;耐老化性好;加工性能好。
2.3.4.2 增强材料的种类与性质
增强材料是一门新的边缘科学,目前使用和开发的增强材料很多,主要以玻璃纤维为主。一些新的无机增强材料的研究开发迅速。
(1)玻璃纤维 玻璃纤维性能优异,增强效果好,产量大,价格低廉,仍是目前主要的增强材料(与其他增强材料相比,使用量上占绝对优势)。
①分类
a.按化学成分分类 通常使用的玻璃纤维为硅酸盐类,化学成分复杂。因原料、配比、生产方法等不同而异。
通常按碱含量(指碱金属氧化物K2O、Na2O的百分含量)来划分。
无碱玻璃纤维:碱含量小于1%,相当于E玻璃纤维。
中碱玻璃纤维:碱含量8%~12%,相当于C玻璃纤维。
高碱玻璃纤维:碱含量14%~15%,相当于A玻璃纤维。
特种成分玻璃纤维:添加特种氧化物的玻璃纤维。高强(S-玻璃纤维)、高弹性模量(M-玻璃纤维)及高温、抗红外、光学、导电等玻璃纤维。
无碱玻璃纤维(E玻璃纤维):含碱量小,具有稳定的化学性、电绝缘性、力学性能,用于增强塑料、电气绝缘、橡胶增强等。
中碱玻璃纤维(C玻璃纤维):含碱量高,耐水性差,不适合做电绝缘材料;化学稳定性较好,耐酸性比E玻璃纤维好,虽然力学性能小于E玻璃纤维,但来源丰富,价廉。适用于机械强度要求不高的一般增强材料。
高碱玻璃纤维(A玻璃纤维):机械强度、化学性能及电绝缘性都较差。主要用于保温、防水、防潮材料。
特种玻璃纤维:特殊行业使用。
b.按直径粗细分类 初级玻璃纤维,单丝直径在20μm以上;中级玻璃纤维,单丝直径为10~20μm;高级玻璃纤维:单丝直径为3~9μm;超级玻璃纤维,单丝直径在3μm以下。
直径越细,强度越高,扭曲性越好;直径越细,表面裂纹较少且小,因而拉伸强度随直径减小急剧上升。增强塑料用玻璃纤维通常直径为6~15μm,为高、中级玻璃纤维,拉伸强度在10000~30000kgf/cm2(1kgf/cm2=0.1MPa)之间。超级玻璃纤维,由于产量低,成本高,不宜采用,用于高级绝缘基材。
从强度及成本考虑,今后中级玻璃纤维作增强材料将占较大比例。
c.按玻璃纤维长度分类 连续玻璃纤维:漏板法拉制的长纤维;定长玻璃纤维:吹拉法制成的300~500mm,用于制毛纱、毡片等;玻璃棉:离心喷吹法、火焰喷吹法制成的长度小于150mm,棉絮状,用于保温吸声材料。增强塑料主要使用连续长纤维。
d.其他 如以形态分为玻璃纤维、玻璃布、玻璃棉等。
②玻璃纤维主要性能
a.相对密度 2.5~2.7,与铝相当(纯铝为2.702),碳钢为7.82。
b.拉伸强度 在纤维中,玻璃纤维为拉伸强度较高的品种,表2-6列出了玻璃纤维与其他纤维拉伸强度的比较。
表2-6 玻璃纤维与其他纤维拉伸强度的比较

c.弹性 玻璃纤维为完全弹性体。拉伸时伸长与载荷成正比,无屈服点,直至断裂。小于纤维断裂的力除去时,纤维恢复原状,具有优良的尺寸稳定性。伸长率3%;有机纤维<弹性模量<金属。
d.耐热性优异 300℃以下,性能不变;大于300℃,强度逐渐下降;370℃时,强度为原强度的50%;高温会软化,熔化,不燃,不冒烟。
e.耐水、耐化学药品 除HF、强碱、热浓磷酸外,耐所有有机溶剂、酸碱。
无碱玻璃纤维:耐水优、耐酸性差,弱碱尚可。
有碱玻璃纤维:对水敏感性大,耐酸优于无碱玻璃纤维。
f.电性能较好
(2)碳纤维 与玻璃纤维比较,具有高强度、高弹性。
碳纤维特点:弹性模量很高,湿态条件下力学性能保持率很好,蠕变性小,有导电性,热导率大,耐磨性好,表2-7列出了碳纤维与E玻璃纤维的物理力学性能。
表2-7 碳纤维与E玻璃纤维的物理力学性能

注:1kcal=4.184kJ。
制造:有机纤维高温烧制而成,如用人造丝(1000℃)、聚丙烯腈(1500℃)、沥青、木质素、聚乙烯醇等烧制。
碳晶须:C 99.84%;H 0.15%。拉伸强度为60~300kgf/mm2;弹性模量为30000~42000kgf/mm2。
(3)其他增强材料 目前,增强材料向着ABCS方向发展(A——Al、B——硼、C——碳纤维、S——钢丝。)。
硼纤维的比强度高、弹性模量极高,1960年美国首先制成,1966年用于喷气机、宇航等方面。
金属纤维:钨、钼、铍、耐热镍合金钢等。
不锈钢纤维:ф8μm以下。
钨——ф100μm钨丝,将金属硼蒸发沉积于钨丝上。
金属纤维越细,性能越好;但越难加工,成本越高,成本随直径减小成几何基数增长。
另外,石棉纤维也曾用于增强材料,但由于其环境等问题逐渐被弃用。
晶须是一类性能优良的增强材料,它具有完整晶态,其强度不受晶粒界面、空穴、缺陷等因素的影响,直径很小,相当于玻璃纤维的1/100。长径比大,如蓝宝石晶须(Al2O3)长径比为100:1~5000:1,伸长率大,高温强度高,用于空间、尖端技术,直升机、海底结构件、汽车车身、人体、牙齿、骨骼等增强材料。
另外,目前开发出的晶须品种有氧化锌晶须、钛酸钾晶须、碳酸钙晶须、硫酸钙晶须等诸多品种。
随着各种晶须的开发,成本的降低,应用领域的扩大,晶须将在各个领域的技术发展中显示出巨大的应用前景。
2.3.4.3 玻璃纤维的表面处理
玻璃纤维有许多优点,但它也存在许多缺点。如玻璃纤维表面光滑、有吸附水膜、与高分子树脂黏合力差;另外,它还存在性脆、不耐磨、僵硬、伸长率小等缺点。
纺织品布面不易平整、拉伸变形、不柔软等。
玻璃纤维在加工时,为使其润滑,常加有助剂。
由于上述原因,玻璃纤维的表面处理技术是发展玻璃纤维增强塑料及玻璃纤维工业的关键。
(1)玻璃纤维的表面性质 要对玻璃纤维进行表面处理,首先要了解玻璃纤维的表面性质。
玻璃具有连续的主体结构,其中每个阳离子按其配位数,被一些氧的阴离子所包围。在玻璃中大多数阳离子很小,并对周围环境施加压力。在玻璃主体中,这些力量基本上处于平衡状态。但在玻璃表面,其情况就显然不同,阳离子在该处不能获得所需数量的氧离子,因此就产生一种表面力。这种表面力与玻璃的表面张力、摩擦力及表面吸湿性等性质,有着密切的关系。
玻璃表面的不平衡状态,产生了具有强烈吸附类似状态的极性分子的倾向。而大气中的水汽,就是最容易遇到的极性分子,因而玻璃表面就牢固地吸附着一层水分子,厚度约为水分子的100倍。
湿度(RH)越大,吸附水层就越厚;玻璃纤维越细,表面积越大,吸附水层就越厚。吸附过程异常迅速,RH60%~70%时,2~3s即达平衡。吸附力强,欲除去,需在500℃和负压情况下才能除去。
水膜的影响如下所述。
①影响玻璃纤维与高分子树脂的黏结强度(形成弱边界层)。
②水会渗入玻璃纤维表面的裂缝中,使玻璃水解成硅酸胶体,降低玻璃纤维强度。
③含碱越高,水解性越强,强度降低得越厉害。
另外,为了满足纺织要求,拉丝时采用石蜡乳化型浸润剂(含油脂类和一些亲水性化学物质),是影响界面黏合的因素(弱边界层)。表面处理有热-化学处理法,前处理法,迁移法等。迁移法是将表面活性剂掺和到树脂中使用,主要用于缠绕、模压成型。
(2)玻璃纤维的热化学处理法 除去浸润剂,然后再用表面活性剂处理。
洗涤法:用溶剂洗涤;用碱洗涤。烘烧法;高温热处理法。
高温热处理法用得较多:420~580℃加热烘箱中烘1min左右,处理后浸润剂残留量0.1%~0.2%,强度损失20%~50%(图2-7)。

图2-7 热化学处理流程示意
热处理温度越高,时间越长,浸润剂残留量越低,保留强度相应降低。
通常,要求电性能高的,热处理温度要求高一些。
必须紧接着进行化学浸渍处理。
另外,玻璃纤维冷却时会大量吸收水分;化学处理液应在水沸点以上。
(3)玻璃纤维的化学处理(前处理) 玻璃纤维增强塑料的物理性能及其他性能,不仅取决于玻璃纤维及高分子树脂的自身结构和性能,而且在很大程度上取决于界面上两相相互作用。
为增大玻璃纤维与高分子树脂之间的黏结力,必须在玻璃纤维与高分子树脂之间架个“桥”。
表面处理剂起到这个“桥”的作用:表面处理剂的一端与玻璃表面作用;另一端与高分子树脂作用或缠绕,黏结力提高。
前处理法:拉丝作业时,就对玻璃纤维表面施以含有表面处理剂和成膜剂的浸润剂(成束剂)。
a.玻璃纤维——表面处理剂——成膜剂——高分子树脂。
b.玻璃纤维——表面处理剂兼成膜剂——高分子树脂。
c.玻璃纤维——表面处理剂——成膜剂——官能团-高分子树脂。
a是普遍采用的方法;b采用甲硅烷基氮杂酰胺作为兼有成膜剂和偶联剂的作用,是一种新方法。
极性树脂:a、b均可;非极性树脂:效果不明显,必须研究新的表面处理剂、成膜剂以及与树脂之间的反应性。
新表面处理剂:甲基硅烷过氧化物、阳离子硅烷。
①有机络合物处理剂。有机络合物处理剂最常用的是沃兰(Volan)——甲基丙烯酸二氯化铬络合物。
②有机硅烷处理剂。有机硅烷处理剂应用广泛,效果比有机络合物更好,其通式为:RnSiX4-n。
R:有机基团,单价脂肪基、脂环基、芳基、芳脂混合基、杂环基等。如脂肪基——甲基、乙基、丙基、辛基等;脂环基——环戊基、环己基等。
2.3.5 聚合物共混改性
聚合物共混(polymer blends):采用化学或物理的方法将两种或多种聚合物混合到一起,成为一种多组分的聚合物,起到改善原有聚合物性能的改性方法。
橡塑共混体系是多组分多相复合体系,其性能取决于各组分的性能、相界面状态和体系形态结构。
橡塑共混物会由于体系相容性差、相界面结合不好,而致使其最终性能下降。
成型加工性:与熔体的流变行为有关。
力学性能:与体系的结构形态有关。
所谓相容:在理论上,均相是判定共混体系相容的依据;在工程上,共混物具有期望的力学性能。
工程上并不要求达到分子水平的均匀相容,只要求组分有部分相容性。
相容性理论基础:热力学平衡(溶液热力学或统计热力学理论)在众多的聚合物共混体系中,能以任意比例相容的聚合物为数很少,大多数属于部分相容。
共混体系是组成和构型不同的均聚物或共聚物的物理混合体系。组分之间只能相互影响分子链的构象和超分子结构,而不能影响组成和构型。共混体系相容性首先取决于组分的分子排列:分子量、分子量分布、化学结构;其次还与分子链的取向、排列以及分子链间的相互作用、聚集态、高次结构等因素有关。共混组分间的溶度积参数差越小,混合焓越小,达到热力学相容的概率越大,体系的相容性越好。
溶度积参数可以通过查阅资料、计算得到,还可以用实验的方法进行测定。目前已获得应用的增韧方法有:共混弹性体增韧材料;添加非弹性体刚性增韧材料;形态控制增韧;交联增韧;低发泡塑料增韧。
上述方法中最有效的增韧材料仍为共混有机弹性体,近年来刚性增韧材料发展也比较快,而其他方法往往不单独使用,往往与前两者结合起来应用。
2.3.5.1 常用弹性体增韧材料的选用
(1)塑料与弹性体的相容性要好
①极性相近原则。
塑料的极性:纤维系塑料>PA>PF>EP>PVC>EVA>PS> HDPE、LDPE、LLDPE等。
弹性体的极性:PU胶>丁腈胶>氯丁胶>丁苯胶>顺丁胶>天然胶>乙苯胶。
②溶度参数相近原则。通常情况下,塑料与弹性体的溶度参数差一般要小于1.5;当然对于不相容体系可以进行增容的方法进行共混改性。
(2)不同弹性体可协同选用 两种以上弹性体协同选用往往具有协同作用。如PP中选用EPDM和ABS复合加入,具有协同作用。
(3)按制品的需要选取 制品要求阻燃——选CPE;制品要求透明——选MBS;制品要求耐候——选ACR及EVA、ASA,不选MBS及ABS;制品要求低成本——选MPR、CPE反EVA。
(4)弹性体与刚性材料协同选用 主要是防止在增韧同时,刚性及耐热性下降太大。如PP中EPDM与滑石粉协同加入等。再如,MBS及CPE中协同加入AS。
2.3.5.2 塑料添加刚性材料的增韧方法
刚性非弹性体增韧材料的增韧效果远不如弹性体增韧材料,但其优势在于:可增韧与增强同时进行。虽然其增韧幅度往往不如弹性体增韧幅度大,但它具有弹性体增韧无可比拟的优点,即刚性增韧材料可同时进行增韧与增强,在改善冲击强度的同时,又改善拉伸强度等其他性能,这是一种两全其美的改性方法。
非弹性体刚性增韧材料分为无机刚性增韧材料和有机刚性增韧材料两大类。增容剂及其在聚合物共混物中的应用。大多数聚合物之间相容性较差,这往往使共混体系难以达到所要求的分散程度。即使借助外界条件,使两种聚合物在共混过程中实现均匀分散,也会在使用过程中出现分层现象,导致共混物性能不稳定和性能下降。遇到相容性不好甚至很差的两种聚合物怎么办?解决这一问题的办法可用所谓“增容”措施。
2.3.6 不相容聚合物体系的增容
增容作用有两方面涵义:一是使聚合物之间易于相互分散以得到宏观上均匀的共混产物;二是改善聚合物间相界面的性能、增加相间的粘合力,从而使共混物具有长期稳定的优良性能。
产生增容作用的方法有:
①在聚合物组分之间引入氢键或离子键;
②进行化学改性——嵌段、接枝等化学反应,成为共价键;
③形成互穿网络聚合物;
④加入大分子共溶剂;
⑤加第三组分——相容剂(增容剂)的方法。
相容剂(增容剂)是指与两种聚合物组分都有较好相容性的物质。增容剂是广义的表面活性剂。它可降低两组分间界面张力,增加相容性。其作用与胶体化学中的乳化剂以及高分子复合材料中的偶联剂相当。
2.3.6.1 非反应型增容剂的作用原理
应用最早和最普遍的增容剂是一些嵌段共聚合和接枝共聚物,尤以前者更重要。在聚合物A(PA)和聚合物B(PB)不相容共混体系中,加入A-b-B(A与B的嵌段共聚物)或A-g-B(A与B的接枝共聚物)通常可以增加PA与PB的相容性。其增容作用可概括为:
①降低两相之间界面能;
②在聚合物共混过程中促进相的分散;
③阻止分散相的凝聚;
④强化相间黏结。
嵌段共聚物和接枝共聚物都属于非反应型增容剂(又称亲和型增容剂),它们是依靠在其大分子结构中同时含有与共混组分PA及PB相同的聚合物链,因而可在PA及PB两相界面处起到“乳化作用”或“偶联作用”,使两者相容性得以改善。非反应型增容作用模型示意如图2-8所示。

图2-8 非反应型增容作用模型示意
2.3.6.2 反应型增容剂的作用原理
反应型增容剂的增容原理与非反应型增容剂有显著不同,这类增容剂与共混的聚合物组分之间形成了新的化学键,所以可称之为化学增容。它属于一种强迫性增容。反应型增容剂主要是一些含有可与共混组分起化学反应的官能团的共聚物,它们特别适用于那些相容性很差且带有易反应官能团的聚合物之间共混的增容。反应增容的概念包括:外加反应性增容剂与共混聚合物组分反应而增容;也包括使共混聚合物组分官能化,并凭借相互反应而增容。在PE/PA共混体系中外加如羧化PE就属第一种情况;若使PE羧化后与PA共混就为后一种情况。增容剂在聚合物共混体系中应用实例如下。
(1)在聚烯烃系列共混物中的应用 PE、PP、PS等聚烯烃之间的性能具有互补性但却缺乏良好的相容性,因此采取增容措施非常必要:
①加20% EPR;
②PS/LDPE共混物中加入PS-LDPE接枝共聚物;
③加(PB-b-PS)共聚物在PE/PS共混体系中起到良好的增容效果;
④将AS与PS的嵌段共聚物作为ABS/PS共混物的增容剂。
(2)其他聚合物共混物中的应用 为了提高PBT、PPO、PPS(聚苯硫醚)等耐高温树脂与其他聚合物的相容性,改善其综合性能,扩充它们的应用领域,常需借助于增容剂。用带有环氧基的PS接枝共聚物增容PET/PPO这一完全不相容体系,得到较好效果。PPS性能优越,但价格昂贵,与其他树脂共混时相容性差。加入增容剂情况才有使用价值,例如使用5份含环氧基的反应型增容剂。PPS/PPO(70/30)共混物的拉伸强度提高了约50%,断裂伸长率增加了60%左右。
2.3.7 塑料功能助剂的应用现状和发展趋势
据统计,2001年全球塑料助剂的消费量达到了7900kt,销售额146亿美元。其中,功能助剂占据了80%左右。一些新型功能助剂发展时间不长,消费量较低。却带来了助剂产业新的突破点和增长点,丰富完善了整个助剂体系,其高技术含量和巨大的增幅显示了强大的生命力。同时,传统的助剂也正努力寻找新的替代品。
单一结构对应单一性能,仍是助剂分子结构研究和设计的理论基础,但复合化、高分子量化、环保化等新思路逐渐占据了新型研发的主线。一剂多功能化和单剂单功能高效能化成为现代助剂研发的趋势。
在注重功能体现的同时,人们将更多的目光投在了前期的加工适用性、配方设计和后期的回收、无害化处理等问题上,这使得助剂研究的结构更为合理,发展更为平衡。此外,科研院所、高校的基础理论性研究如何与现代企业结合,更快更好地投入到工业化生产,加大应用研究的投入力度也是助剂专家和企业家需要考虑和面对的问题。
我国助剂工业起步较晚,发展迟缓,难以适应目前的发展趋势,必须借助行业发展,探索一条具有中国特色的助剂工业之路。在消化、吸收、仿制国外先进品种和技术的基础上,针对不同行业要求和特点,开发出高效、多功能、复合化、低(无)毒、低(无)污染、专用化的助剂品种,提高规模化生产和管理能力,改变目前助剂行业规模小、品种少、性能老化且雷同、针对性(专用性)差、性能价格比明显低于国外同类产品、创新能力低下、污染严重、无序竞争的局面,创造一个投入产出比明显高于其他化工产品的新产业。
2.3.7.1 传统助剂的改进
(1)复合化 复合化的目的是找到一种助剂使之具有多功能性,同时满足多种功能的需求。新型的复合化技术是以经典理论和应用技术研究为基础,将显示协同效应或不同功能的助剂组分配合在一起,构成一种复合品种或母料,这无论对助剂开发或应用都具有事半功倍的效果,也是复合化技术备受瞩目的重要原因。
助剂的复合化包括混合型助剂和浓缩母料。前者系各种助剂的混合物,后者则是将助剂和分散剂等以较高浓度附着在载体树脂上,加工时稀释一定倍数。复合技术的共同特点是助剂的应用简单方便。因此,复合化技术已渗透到了塑料助剂的各个领域。与早期简单的复合助剂相比,当代助剂的复合化技术已有质的飞跃,协效组分的作用显得十分关键和突出。其各种组分之间的协同机理的研究和协效组分的开发将是未来助剂复合化技术发展的关键。
(2)高分子量化 高分子量化可提高助剂自身的热稳定性、耐水解能力、提高助剂与基材树脂的相容性,进而提高助剂在塑料制品中的耐迁移性、耐抽提性,且不致过度恶化基材的基本物理力学性能。高分子量化也是降低助剂自身毒性的有效手段。高分子量的抗氧剂1010比低分子量的1076的耐水解能力、耐迁移性、耐抽提性有明显改善。聚合型抗静电剂可实现永久抗静电。齐聚溴代碳酸酯、齐聚磷酸酯等高分子量阻燃剂对除阻燃性之外的其他基本物理力学性能的恶化程度均明显降低。受阻胺光稳定剂(HALS)高分子量化不仅可提高热稳定性、与树脂的相容性、耐迁移性、耐抽出性,而且能降低毒性,延长塑料制品的使用寿命,扩大其使用范围。
(3)环境友好化 各种合成高分子材料制品的深入广泛应用,给人类赖以生存的环境带来诸多压力。近年来,全球卫生、安全、环保等方面的法规日益严格,要求塑料制品从选材、配方组分、加工工艺及其过程、使用,到废弃处理、分类回收、再生循环、环境可消纳性、燃烧产物及其毒性等环节或因素都必须考虑环境负荷。
“绿色”建筑塑料已成为21世纪建材工业的发展方向,高效、多功能、无毒、无公害是塑料助剂发展的总趋势。寻找铅、镉替代品的工作日益紧迫。目前,已出现了大量具有较高性价比的钡/锌、钙/锌类复合稳定剂、稀土类热稳定剂和价格较高的有机锡类稳定剂。
无卤阻燃剂的开发逐渐升温。PVC树脂燃烧发烟量较高,抑烟性成为提高PVC制品消防安全性能的关键因素。在开发阻燃剂的同时,抑烟剂的开发也同样具有重要意义。
酚类抗氧剂BHT分子量低、易挥发和萃取,近年来更是出现了致癌性的报道。以维生素E为基础的系列产品大大缓解了BHT所带来的压力。该系列产品是将维生素E与亚磷酸酯、甘油、聚乙二醇、高孔率树脂载体等组分配合而成的固体。基于人们对卫生安全和生态保护意识的进一步增强,这类“绿色”助剂将具有广阔的市场潜力和环保价值。
2.3.7.2 新型助剂
(1)成核剂 加入到聚乙烯、聚丙烯、聚酰胺、聚酯、聚醚等结晶性聚合物中,改变树脂的结晶行为,加快结晶速度,增加结晶密度和促使晶粒尺寸微细化,缩短成型周期,或全面或部分提高制品透明性、表面光泽、拉伸强度、刚性、热变形温度等物理力学性能。
(2)接枝高聚物、特种共聚物作相容剂 高分子共混是进行材料改性的最简单易行的手段。相容剂就是伴随这种处理方式而产生的。所谓相容剂就是能使共混的两种树脂在加工熔融过程中,在其帮助下能形成热力学相容状态,从而结合几种共混材料的优点,实现高性能化和功能化。
相容剂一般为接枝高聚物或特种共聚物,即将两种性能差异较大的分子链段用化学方法结合在一起,分子链段性能差异越大,其相容效果就越好。如将极性的马来酸酐接枝在聚烯烃大分子链上,对于PP/PA合金就有良好的相容作用。至今为止,高分子相容剂是以界面活性剂的概念为基础发展起来的,主要目的是通过对两种或两种以上具有不同性质的高分子共混体系的微观相态结构起到调整和控制作用,以提高其材料的性能,从机能特征角度可以将其概括为结构型相容剂。目前这类相容剂在应用中还存在着制备成本高、作用效率低、兼容性差等问题,而且对某些特殊高分子材料体系,至今还没有发现作用效果好的相容剂种类。
今后的相容剂的发展必然要以全面迎合和促进高分子材料日新月异的进步为目标,从结构型相容剂向功能型相容剂、兼容型相容剂、高效型相容剂和特征相容剂等方向转变。从广义上讲,高分子材料制备技术所能涉及的复合(分散)相尺度已从微米时代进入到纳米时代,而且高分子分子设计、材料性能与结构设计、工艺设计等方面的理论与实践的进步,将使相容剂在发展方向上的转变成为历史之必然。
(3)纳米粉体/纤维粉体 无机粉体的超细化技术派生出两个分支,一是无机粉体粒度的纳米化,二是无机粉体向增强纤维方向发展。各种纳米技术使无机粉体纳米化成为现实,各种纳米无机粉体/聚合物复合材料研究成果的问世使纳米无机粉体进入了功能添加剂行列,而不再仅仅是超细化的无机填充剂。镁盐晶须、类纤维状硅灰石的工业化生产,拓宽了应用领域,自身功能得到提升。纳米无机相材料蒙脱土为填充材料,采用插层复合技术制备了具有高强度和耐热性、高阻隔和自熄性的纳米复合材料,如尼龙6纳米塑料、PET纳米塑料、超高分子量聚乙烯黏土纳米复合材料、纳米无规共聚聚丙烯、纳米聚乙烯高阻隔膜等,经测试,性能均大大高于一般填充材料,且某些性能极为突出。目前,已有部分产品实现了工业化。
2.3.7.3 稀土类助剂成为新的研发热点
稀土元素由于其特殊的外电子层结构,使得其化合物具有光、电、磁以及界面效应、屏蔽作用和化学活泼性等多种特殊功能,被成功用于制作光、电、磁性材料和催化剂等。稀土元素被引入到高分子材料助剂结构以后,助剂的功效发生了令人耳目一新的变化。
20世纪90年代,我国率先将稀土化合物商品化地用于PVC热稳定改性。由于它不仅具有热稳定剂的作用,还表现出偶联、加工改性、增亮增艳等功能,具有较高的性能价格比。
稀土化合物作为PP的晶型改性剂,作为LLDPE的流变改性剂和作为无机粒子的表面处理剂等方面都具有独特的功能,对聚烯烃的增韧增刚、提高热变形温度和改善加工性能都具有明显作用。利用稀土化合物的荧光性质也已制成发光塑料,利用磁性稀土材料制成了磁性塑料,利用稀土化合物的光转换性质制成了发光塑料等。将轻稀土化合物与传统无卤阻燃剂结合,开发无卤稀土阻燃剂,并应用于聚烯烃,可在满足阻燃性能要求的同时,提升阻燃材料的综合性能,克服传统的无机非卤阻燃剂劣化被阻燃基材物理力学性能的弊端。此外,稀土改性母料或专用料,可应用于各种特定目标产品,如汽车、家电、管材等。