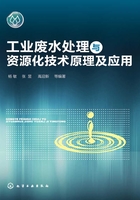
第四节 膜分离技术单元
膜分离技术是通过选择性透过膜对混合物中各组分的选择性渗透作用的差异,借助外界能量或以化学位差为推动力,对双组分或多组分的混合气体或液体进行分离、分级、提纯和富集的新型工业废水处理方法,包括微滤(MF)、超滤(UF)、纳滤(NF)、电渗析(ED)和反渗透(RO)等[61]。我国膜分离技术的发展是从1958年对离子交换膜的研究开始的,20世纪60年代中期开始进行反渗透的研究,70年代进入电渗透、超滤、微滤用膜组件的开发阶段,80年代初开始进行气体分离研究开发。20世纪80年代是我国膜分离技术大发展的10年,在这一阶段初步完成了从实验室到工业化的过渡[66]。图1-9为反渗透、超滤、微滤、正渗透膜分离异同的示意图,表1-2进一步列举了几种主要膜分离过程及其对应的传递机理、推动力、透过物、膜类型[67]。

图1-9 不同膜分离技术的膜孔径与截留对象
(1Å=10-10m=0.1nm)
表1-2 几种主要膜分离技术的特性

膜分离技术作为新的分离净化和浓缩方法,与传统的分离操作(如蒸发、萃取、沉淀、混凝和离子交换等)相比较,操作过程中大多无相变化,可以在常温下操作,具有低耗、高效和不产生二次污染的优点。膜分离技术的应用领域非常广泛,根据相关数据统计显示:美国占50%,日本占18%,西欧占23%。膜的工业应用领域如表1-3所列[67]。在化工、石化、医药、轻工等能耗较高、污染较重的领域广泛推广应用后,不仅能提高相关产品的技术装备水平和产品质量,还有助于减少污染物的排放、节能降耗、降低成本。
表1-3 膜分离技术的工业应用状况

一、微滤与超滤膜分离
微滤与超滤二者都是以“筛分”原理为主的薄膜过滤[68]。筛分原理认为膜有无数个微孔,这些实际存在的不同孔径的孔眼,像筛子一样截留直径大于孔径的溶质和颗粒,从而实现分离的目的。“筛分”是通过比膜孔大的颗粒的机械截留、颗粒间相互作用及颗粒与膜表面的吸附、颗粒间的桥架作用这三种方式来实现的[68]。
1.微滤膜分离法
微滤又称为精过滤或筛网状过滤,是利用孔径为0.1~20μm的选择性透过膜,在给定压力下(50~100kPa)对气相和液相中直径大于50nm的细小悬浮物、微生物、微粒、细菌、酵母、红细胞、污染物等进行截留,仅使溶剂、盐类及大分子物质透过,达到净化和浓缩目的的过程。它属于压力驱动型的膜分离过程,其工作原理是:在膜两侧静压差的作用下,小于膜孔的粒子透过膜,大于膜孔的粒子则被截留在膜的表面上,使大小不同的粒子得以分离[68]。
微滤技术是目前所有膜技术中应用最广、最有经济价值的技术。微滤主要用于悬浮物分离、制药行业的无菌过滤等。在制药工艺中,微滤膜分离技术被用于药物澄清,即去除微粒、细菌、大分子杂质等[66]。Adikane等[69]研究了用微滤膜去除青霉素G发酵液中的菌丝体,青霉素G的回收率可达98%。此外,由于与超滤膜、反渗透膜相比,微滤膜的孔径相对较大,因此,微孔过滤常常作为一种“粗过滤”为反渗透做预处理,以保证反渗透能稳定进行。徐竟成等[70]采用微絮凝过滤-微滤作为反渗透的预处理工艺,用于印染废水二级生化出水回用深度处理,出水浊度<0.2NTU,淤泥密度指数(SDI)稳定在4左右,达到反渗透膜对进水水质的要求。
2.超滤膜分离法
超滤与微滤一样,也是以压力差为推动力,以筛孔作用为主的薄膜过滤。与微滤不同,超滤受膜表面的化学性质影响较大。其原理是:在一定的压力(100~1000kPa)条件下,溶剂或小分子量的物质通过孔径为1~20μm的不对称微孔膜,而直径在5~100nm之间的大分子物质或者微细颗粒被截留,从而实现净化的目的。目前,超滤中普遍采用的膜为:醋酸纤维素膜和聚酰胺膜,聚醚砜膜、聚砜酰胺膜、多孔金属膜、多孔陶瓷膜、分子筛等。超滤膜组件主要结构形式有板框式、管式、卷式、中空纤维式、毛细管式、条槽式等,膜表面积分别为25~50m2/m3、400~600m2/m3、800~1000m2/m3、600~1200m2/m3、200~300m2/m3,其中毛细管式超滤膜组件在投资费用、运行成本、流速控制等方面表现良好[71]。
超滤主要用于浓缩、分级和大分子溶液的净化等。目前国内一些磷肥生产企业采用微滤膜分离法去除磷石膏废水中的含氟化合物[66]。近年来,UF膜法已逐渐应用到中药制剂工艺中,取得了良好的效果。李淑莉等[72]初步研究了聚砜超滤膜对黄芩(根)、黄连(根茎)、黄柏(皮)、金银花(花)、五味子(果)、大青叶(叶)等中药提取液的渗透行为,结果表明各中药有效成分的回收率均高于74%。超滤技术可以在不用加入其他试剂的前提下,纯粹通过物理分离,有效去除乳化油,同时不产生含油污泥,浓缩液仅为初始量的3%~5%,可回收处理或直接焚烧[71]。
超滤膜在使用过程中很容易受到污染:浓差极化、凝胶层的出现及固化与膜堵塞。膜污染的解决方法有物理清洗法和化学清洗法。水洗、反冲洗和气洗是常见的物理清洗方法。常见的化学清洗剂包括酸、碱、氧化剂、酶、表面活性剂等[71]。
二、反渗透与纳滤膜分离
1.反渗透膜分离法
1748年,法国人Nollet发现了猪膀胱在酒精和水之间的选择透过性,在两百多年后的今天,由于他的发现,人类利用反渗透(reverse osmosis,RO)技术将海水转化成淡水。反渗透过程是与自然渗透过程相反的膜分离过程。它主要是依据溶液的吸附扩散原理,以压力差为推动力的膜分离过程。在浓溶液一侧施加外加压力(1000~10000kPa),当此压力大于溶液的渗透压时,浓溶液中的溶剂通过孔径为0.1~1nm的反渗透膜反向流向稀溶液一侧,这一过程称为反渗透。渗透压的选择与溶液性质有关,而与膜自身无关。
反渗透膜通常可去除90%~95%的溶解性固体、95%以上的溶解有机物、生物和胶体以及80%~90%的硅酸。反渗透膜对水中离子和有机物的去除性能,一般有如下规律[73]。
①高价离子去除率大于低价离子。
Al3+>Fe3+>mg2+>Ca2+>Li+
②去除有机物的特性受分子构造与膜亲和性影响。
分子量:高分子量>低分子量
亲和性:醛类>醇类>胺类
侧链结构:第三级>异位>第二级>第三级
③对分子量>300的电解质、非电解质都可有效地去除,其中分子量在100~300的去除率为90%以上。
反渗透技术主要被用于低分子量组分的浓缩、水溶液中溶解性盐类的去除等。农场采用反渗透对牛奶进行浓缩后加工成炼乳等制品[74]。Joachim Danzig等[75]研究了在连续的酶催化反应制备6-氨基青霉烷酸(6-APA)过程中,采用RO膜分离法浓缩青霉素裂解液,随着浓缩倍数的增加膜通量降低,而对6-APA的截留率基本能维持在98.5%以上,但当料液浓度达400mmol时,截留率显著下降,此时的渗透压为44bar(1bar=105Pa)。
2.纳滤膜分离法
纳滤膜是20世纪80年代发明的新型分离膜,是介于超滤膜和反渗透膜之间的、根据吸附扩散原理以压力差为驱动力的膜,又称“超低压反渗透”“疏松反渗透膜”。在外加驱动压力(500~2500kPa)条件下,水溶液中低分子量的有机溶质被截留,而盐类组分可以部分通过纳滤膜。纳滤膜在应用中具有以下2个显著特点:①物理截留或截留筛分效果,截留分子量为200~2000,能截留分子大小约为1nm的溶解组分;②荷电性,对无机盐有一定的截留率,其中单价离子的截留率较低(50%~70%),对二价及多价离子的截留率较高。由于纳滤膜能在截留易透过超滤膜的那部分溶质的同时,使被反渗透膜截留的盐类透过,从而实现有机溶质的浓缩和脱盐,因而被称为当代最先进的工业分离膜[76]。从膜的结构上来看,纳滤膜多是复合膜,即膜的表层分离层和支撑层的化学组成不同。
纳滤与超滤、反渗透类似,均属于压力驱动的膜过程,但其传质机理有所不同,一般认为,超滤膜由于孔径较大,传质过程主要为孔流形式,而反渗透膜通常属于无孔致密膜,溶解-扩散的传质机理能够满意地解释膜的截留性能。而大部分纳滤膜为荷电型,其对无机盐的分离行为不仅受化学势控制,同时也受到电势梯度的影响,其确切的传质机理至今尚无定论。目前,纳滤膜传质机理被认为处于孔流机理和溶解-扩散之间的过渡态,可通过适用于较大孔径的宏观模型来分析纳滤膜的传质过程。目前表述膜的结构与性能之间关系的数学模型有空间电荷模型、固定电荷模型、细孔模型等[77]。
空间电荷模型假设膜由孔径均一且其壁面上电荷均匀分布的微孔组成,微孔内的离子浓度和电场电势分布、离子传递和流体流动分别由Poisson-Boltzmann方程、Nernst-Planck方程和Navier-Stokes方程等来描述。空间电荷模型是表征电解质及离子在荷电膜内的传递等动电现象的理想模型[77]。
固定电荷模型假设膜为一个凝胶相,其中电荷分布均匀、贡献相同。固定电荷模型可以用于表征离子交换膜、荷电型反渗透膜和超滤膜内的传递现象,描述膜浓差电位、膜的溶剂和电解质渗透速率及其截留特性[77]。
细孔模型基于著名的Stokes-Maxwell摩擦模型。Pappenheimer等在基于膜内扩散过程的溶质通量计算方程中引入立体阻碍(steric hindrance)影响因素。Renkin等认为通过膜的微孔内的溶质传递包含扩散流动和对流流动两种类型,并相应地建立了经典统计力学方程。后来Habeman、Sayer、Bohlin和Bean等在对上述方程进行改进时,考虑了溶质的空间位阻效应和溶质与孔壁之间的相互作用[77]。
根据纳滤膜的分离特点,其应用范围主要为3个方面:①对单价盐并不要求有很高的截留率;②欲实现不同价态离子的分离;③欲实现不同分子量有机物的分离。近年来,我国膜技术在抗生素生产中的应用已有一些研究。蔡邦肖[78]选用了不同性能的聚酰胺纳滤膜,对药厂提供的螺旋霉素进行了分离和浓缩,在进料流量55L/h、操作压力1.5MPa条件下,所选用的膜对螺旋霉素几乎全部截留,膜的渗透通量可高达30L/(cm2·h)。苏鹤祥等[79]等在国内率先采用醋酸纤维素反渗透膜改性成纳滤膜,对活性染料进行提纯和浓缩,并实现了工业化。在纳滤膜分离过程中,无机盐、水和低分子物透过膜被除去,而染料被截留得到纯化和浓缩。该工艺不但提高了染料的强度、固色率,而且使染料的色光也得到了改善。在食品工业中,膜分离技术主要用来对料液进行浓缩、脱盐、脱色、调味和脱除杂质。纳滤膜可和超滤膜结合对橘子汁和洋李酸浸液进行浓缩脱盐。对洋李酸浸液,脱盐率达54.5%,有机酸脱除率可达80%,自身可被浓缩到10倍以上[80]。
三、特种膜分离技术
1.电渗析
电渗析技术是在直流电场的作用下,以电位差为推动力,利用离子交换膜的选择透过性把电解质从溶液中分离出来,从而实现溶液的淡化、精制或者提纯的目的[81]。电渗析技术已广泛应用于化工、冶金、造纸、纺织、轻工、制药等工业废水的处理以及许多其他的化工过程,其应用范围还在不断扩大,并已经发展成为一种新型的单元操作[82,83]。
电渗析技术的技术原理(图1-10)是将阴离子、阳离子交换膜交替排列于正负电极之间,并用特制的隔板将其隔开,组成除盐(淡化)和浓缩两个系统,在直流电场作用下,以电位差为推动力,利用离子交换膜的选择透过性,把电解质从溶液中分离出来,从而实现溶液的浓缩、淡化、精制和提纯。电渗析技术具有以下优点[84]:①能量消耗低;②药剂耗量少,环境污染小;③对原水含盐量变化适应性强;④操作简单,易于实现机械化、自动化;⑤设备紧凑耐用,预处理简单;⑥水的利用率高。电渗析也有它自身的缺点:在运行过程中易发生浓差极化而产生结垢;与反渗透(RO)相比,脱盐率较低。

图1-10 电渗析基本排布方式及原理
就过程基本原理而言,电渗析工程至少有以下4个方面的用途[85]。
①从电解质溶液中分离出部分离子,使电解质溶液的浓度降低。例如,海水、苦咸水淡化制取饮用水与工业用水,工业用初级纯水的制备,放射性废水的处理等。这是目前电渗析技术最成熟、应用最广泛的领域。
②把溶液中部分电解质离子转移到另一溶液系统中去,并使其浓度增高。海水浓缩制盐是这方面成功应用的典型例子;又如化工产品的精制、工业残液中有用成分的回收等也属于这方面的应用。
③从有机溶液中去除电解质离子。目前主要用于食品和医药工业,在乳清脱盐、糖类脱盐和氨基酸精制中应用得比较成功。
④电解质溶液中,同电性但具有不同电荷离子的分离和同电性同电荷离子的分离。使用只允许一价离子透过的离子交换膜浓缩海水制盐,是前者工业化应用的实例;后者因无实用的膜,目前尚无应用实例,处于研究开发阶段。
陈玉莲等[82]对含醛废水进行了研究,使乙酸得到了回收,实现了含醛乙酸废水的综合治理,经济效益和社会效益显著。国外也有人[86]用此项技术回收废水中的酸,其电流效率可达80%~90%。另外,电渗析对碱的回收也是非常有效的。如铝制品行业每年排放的碱性废水达2.10×106m3,流失到环境的NaOH达8400t,中和要消耗10290t,造成极大的经济损失,因此要及时处理此类废水。宋德政[87]用电渗析做实验处理铝制品漂洗废水,证明对碱有良好的脱除效果。
脱盐率是电渗析器的重要性能指标,系统脱盐率要以单台或单级的脱盐率为基础进行计算。计算公式如式(1-7)[85]所列:
(1-7)
式中 ε——脱盐率;
cdi、cdo——电渗析器进口、出口浓度,取相同浓度单位。
电流效率是评价电渗析器性能的重要参数,一般表达式[85]为:
(1-8)
式中 Q——淡水流量,L/s;
cdi、cdo——淡水系统进、出电渗析器的浓度,N;
I——电流强度,A;
N——组装膜对数;
F——法拉第常数。
根据国内外部分应用实例汇总的电渗析法处理效果及耗电数据列在表1-4[85]中。
表1-4 电渗析法处理不同水质的效果及耗电情况

2.正渗透
正渗透(forward osmosis,FO)是一种自然界广泛存在的物理现象,是指化学势较高(或渗透压较低)的一侧原料液中的水,通过选择透过性膜流向化学势较低(或渗透压较高)的一侧汲取液的过程[88]。正渗透过程不同于以外加压力为驱动力的反渗透,它是一种仅依靠化学位差作为推动力,低能耗的膜分离过程。
提供化学位的体系为高渗透压的溶液体系,即驱动溶液。驱动溶液由驱动溶质和溶剂(一般为水)组成。理想的驱动溶质应具备以下条件:无毒;分子量较小;在水中稳定且具有较高的溶解度,从而产生较高的渗透压;与正渗透膜化学相容,不改变膜材料的性能和结构;能够简单、经济地与水分离,能够重复使用。已报道的驱动溶质材料有:盐类,如NaCl、MgCl2、Al2(SO4)3、NH4HCO3;糖类,如葡萄糖、果糖等。驱动溶质的分离方法有渗透蒸馏、投加Ca(OH)2、加热、反渗透等。
正渗透过程的核心除了驱动溶液外,还有正渗透膜材料。在正渗透技术中,半渗透膜是核心材料,具有亲水性。膜分为致密层、多孔支撑层和网格支撑3层结构。目前,最好的商业化正渗透膜材料是美国HTI公司的支撑型高强度膜,该膜的分离层材料为三乙酸纤维素(CTA)及其衍生物,没有传统意义上的支撑层,而是将聚酯纤维嵌入无纺布中提供机械支撑。该膜对NaCl的截留率为90%左右。正渗透膜应该具有以下特征:皮层孔隙率低、致密性高、亲水性较好、水通量较高;支撑层尽量薄且孔隙率高;具有较高的机械强度,截留率高;耐酸碱等化学腐蚀能力好,适用pH值范围较宽[89]。
正渗透体系相对于反渗透体系而言,具有一系列的优势[90]:不需外界压力作为推动力,能耗低;膜材料自身亲水性好,可以有效降低膜污染的可能性;正渗透过程回收率高,可实现浓盐水“零”排放,是环境友好型技术,应用广泛;就海水脱盐过程而言,通过选择合适的驱动溶液,其纯水回收率可达到75%,而反渗透纯水回收率仅为35%~50%。
近年来,能源和环境危机将正渗透推向舞台,耶鲁大学的研究人员[91~93]利用HTI公司的正渗透膜材料开发了一种新型的正渗透海水脱盐系统,整个系统分成正渗透和驱动液分离两个相互耦合的过程:①在正渗透过程中,碳酸氢铵/氨水混合驱动溶液将海水中的水“吸”过来;②将稀释的驱动溶液通过适度加热(大约60℃)分解成氨和CO2,并循环使用,得到纯水。据报道,采用6mol/L铵盐(渗透压250×105Pa)为驱动溶液,结合HTI公司的正渗透膜,获得水通量高达25L/(m2·h),盐的截留率大于95%,整个正渗透过程电能消耗为0.25kW·h/m3,低于目前脱盐技术的电能消耗。正渗透过程海水淡化比多级闪蒸节省能量85%,比反渗透节省能量72%。
正渗透技术的应用远不止于海水淡化领域。由于没有外压推动,过程膜污染少,因此正渗透技术在污水的深度处理、液体食品的浓缩方面具有较强的竞争力。最早关于应用正渗透技术处理工业废水的可行性研究报道发表于1974年[94]和1977年[95],其目的是使用这种低能耗的过程处理微重金属污染的工业废水。他们采用序批式系统,以商业化的醋酸纤维反渗透膜为膜单元,以合成海水为汲取液,来浓缩含低浓度铜或铬离子的水,具有一定的可行性。但由于膜通量非常低[0~4.5L/(m2·h)],盐的截留率也不太理想,因此没有开展进一步的研究。
1998年,Osmotek公司建立了一套中试规模的正渗透系统用于浓缩垃圾渗滤液[96]。该系统采用Osmotek的CTA膜,以NaCl为汲取液,对污染物截留率高,出水产率可以达到94%~96%。并且在处理原垃圾渗滤液时,膜通量没有明显降低。在此基础上,Osmotek公司建立了大型装置处理垃圾渗滤液,平均产水率达到91.9%,最终出水平均电导率为35μS/cm,表明正渗透技术处理垃圾渗滤液是较理想的处理方法。采用正渗透系统处理污泥消化液的事例目前已有报道。
Holloway等[97]设计了正渗透和反渗透组合系统处理污泥消化液。采用如下流程:污泥消化液先经过150目格栅预处理,再经过采用三醋酸纤维的正渗透膜,以NaCl为汲取液的正渗透系统,最后稀释的汲取液通过反渗透系统获得出水。由于系统很高的污泥浓度,在运行过程中膜通量明显下降,需要进行膜清洗恢复膜通量。系统对磷酸盐、氨氮和凯氏氮的截留率分别为99%、87%和92%,几乎完全截留色度和恶臭物质,浓缩干化的污泥消化液可用作肥料。
国内在正渗透技术方面的研究仍处于初始阶段,目前青岛海洋大学和南京工业大学两个研究小组在从事该方向的研究[89],研究重点是正渗透膜材料,包括醋酸纤维素类和界面聚合型复合膜。此外,在南京工业大学还开展了新型驱动溶液的研究,目的在于制备可以在低能耗条件下通过简单手段进行分离而且循环使用的驱动溶质。在当今环境和能源危机的情况下,由于正渗透技术的低能耗特点,其发展显得尤为重要[98]。
3.膜蒸馏
膜蒸馏(membrane distillation,MD)技术是采用疏水微孔膜,以膜两侧蒸汽压力差为传质驱动力的膜分离过程。其工作原理为[99]:当不同温度的水溶液被疏水微孔膜分隔开时,由于膜的疏水性,两侧的水溶液均不能透过膜孔进入另一侧,但是由于暖侧水溶液与膜界面的蒸气压高于冷侧,水蒸气就会透过膜孔从暖侧进入冷侧而冷凝。这与常规蒸馏中的蒸发、传质、冷凝过程十分相似,因此此种将膜技术与蒸发过程联合起来的技术被称为膜蒸馏技术。
膜蒸馏技术具有截留率高[理论上能达到100%(因为只有蒸汽能透过膜孔,所以蒸馏液十分纯净)]、操作压力小(几乎是在常压下进行)、温度低(无需把溶液加热到沸点,只要维持膜两侧适当的温差即可)、体积小、可利用废热(工厂的余热等)和自然能源(太阳能、地热、温泉等)等优点[99]。膜蒸馏是一个有相变的膜过程,气化潜热降低了热能的利用率,而且膜蒸馏通量低、易污染是其主要缺点。因此在膜组件的优化设计和膜材料的改进设计时必须考虑潜热的回收,尽可能地减少热能的损耗。Dotremont等[100]利用膜蒸馏技术淡化海水,若干年的中试结果表明,膜蒸馏工艺的通量提升到5L/(m2·h)以上,所需的热能可以通过太阳能和电厂的废热提供,可控制能耗<500mJ/m3,热能利用率>80%,出水电导率<20μS/cm。
目前膜蒸馏的研究对象仅仅限于水溶液,所以膜的疏水性和微孔性是膜蒸馏的必要条件。为了得到较高的通量和较高的溶质截留系数,要求所用的疏水微孔膜具有尽可能大的孔径,但两侧的液体又不能进入膜孔。液体进入膜孔的最低压力可以用式(1-9)[101]描述:
p=2γcosθ/R (1-9)
式中 γ——液体的表面张力;
θ——液体与膜的接触角;
R——膜的孔半径。
为了保证在操作压力下液体不进入膜孔,所用的膜就必须有足够的疏水性和合适的孔径。经研究证明,当采用膜的疏水性足够好时,膜的孔隙率在60%~80%、孔径在0.1~0.5μm较为合适。为了制备疏水性的膜,常采用的疏水性高分子材料有聚四氟乙烯(PTFE)、聚丙烯(PP)、聚乙烯(PE)、聚偏四氟乙烯(PVDF)等。但与亲水性膜相比,材料品种和制膜工艺都十分有限,研究者们尝试采用改性的方法,以期拓宽疏水微孔膜的来源,并取得了一定的进展。Chung等[102]通过对中空纤维膜丝结构的改进,试图将膜通量提高。在膜制备过程中混入乙二醇、PTFE颗粒、黏土颗粒等添加剂,制备单层非对称的PVDF膜,极大地提高了膜的孔隙率;另外,制备的双层(外表面疏水、内表面亲水)膜,在80℃下膜通量可达到40~50L/(m2·h)。
4.膜结晶
膜结晶技术是膜蒸馏与结晶两种分离技术的耦合过程,其原理是通过膜蒸馏脱除溶液中的溶剂浓缩溶液,使溶液达到饱和或过饱和,然后在晶核存在或加入沉淀剂的条件下,使溶质结晶。膜蒸馏技术自1963年报道以来,经过了50年的发展已日趋成熟,并在海水淡化、超纯水的制备、溶液的浓缩与提纯、废水的处理、共沸混合物及有机溶液的分离、果汁与蔬菜汁浓缩和中药浓缩方面得以应用[99]。
膜结晶具有高单位传质面积、可控的过饱和条件、较短的结晶过程、能通过选择合适的膜材料影响结晶成核条件等优点。该技术使得盐在非均相条件下成核,不受浓差极化的影响,能同时回收RO/NF膜产生的浓水中有价值的盐类和淡水。Macedonio等[103]将膜结晶和NF/RO膜技术结合起来处理海水,可达到近95%的淡水产率,浓水中盐的产量约为20kg/m3。同时通过回收析出的晶体、控制液体温度等手段,防止了盐在膜表面和膜孔内结晶。NF膜的截留液中残存的有机物(如腐殖质等)对膜结晶过程和膜污染的影响较大,腐殖质类物质会抑制晶体的析出和生长。