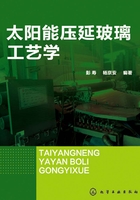
2.5 配料表手工计算
新建玻璃生产线在投产之初、进厂原料成分有较明显变化、因生产中某些原因需要调整玻璃成分或进行工艺参数调整时,就需要重新计算配料表,所以,配料表的计算在生产中是经常性的工作。
配料表计算有手工计算和计算机程序计算两种,它们都是依据已知条件计算出100kg或1000kg玻璃液所需各种原料的干基数量,填入配料成分表中,然后再据此计算出供称量用的配料单,通过配料单进行配料。
手工计算配料表工作量大,计算周期长,而且计算过程容易出错;计算机计算配料表不仅方便快捷,而且结果准确可靠,所以,大多数的工厂已用计算机取代手工计算配料表。由于手工计算配料表是基础,加之一些条件较差的工厂仍在使用手工计算配料表,因此,本书在此仍做较详细的介绍。计算机计算配料表利用安装在计算机上已编好的计算程序,使用时只要输入各种原料成分和已确定的工艺参数,在很短的时间内就可计算出配料表,在此不再赘述。
2.5.1 手工计算配料表条件
(1)玻璃成分(配方)
玻璃成分设计是一项非常重要而复杂的工作,首先,在理论上它涉及玻璃形成的结构状态、玻璃形成相图、成分和性质与结构的关系等方面,可定性地为玻璃成分设计指出方向;其次,在实际生产中它涉及获得原料的难易程度、生产线的熔化、成形、退火工艺条件、玻璃性能要求、制造成本高低等因素。一旦玻璃成分确定后,没有特殊原因,往往长期固定不变。
(2)原料成分
化验室事先对各种要使用的原料进行化验分析,确认符合技术指标要求,其结果作为计算配料成分表的重要依据。
(3)配料参数
① 纯碱飞散率。纯碱飞散率是指纯碱在配料、混合、输送及窑内熔化时所飞散的损失量占纯碱用量的百分数。即:
纯碱飞散率 (%) = (纯碱飞散量/纯碱总用量) ×100%
=[纯碱飞散量/ (纯碱用量+纯碱飞散量)]×100%
纯碱飞散率是一个经验数据。根据使用轻质纯碱和重质纯碱的不同,纯碱飞散率也不相同,一般轻质纯碱飞散率高一些,约1.0%~2.0%,重质纯碱飞散率低一些,约0.25%~0.3%。
② 芒硝含率。芒硝含率在我国有两种定义,第一种是芒硝引入玻璃中的Na2O占芒硝与纯碱引入玻璃中Na2O之和的百分数,即:
芒硝含率 (%) =[芒硝中Na2O量/ (芒硝中Na2O量+纯碱中Na2O量)]×100%
第二种是芒硝引入玻璃中的Na2O占玻璃中Na2O总含量的百分数,即:
芒硝含率 (%) =[芒硝中Na2O量/ (玻璃中Na2O总含量)]×100%
大多数厂家采用第二种方式计算芒硝含率。
以前芒硝含率随熔化要求不同而改变,控制在2.5%~4.5%,但是,考虑到芒硝对熔窑耐火材料有较强的侵蚀作用,并易引起蓄热室格子体的堵塞,同时会从烟囱中排放出大量有害气体二氧化硫,所以,对窑龄要求较长的生产线,并考虑到环境保护的要求,保证熔制条件的情况下,建议芒硝含率按2.0%~2.5%控制。
③ 碳粉含率。碳粉含率是指由煤粉引入的固定碳(C)量占芒硝引入的Na2SO4量的百分数。即:
碳粉含率(%)=[(煤粉用量×煤粉含碳量) /芒硝中Na2SO4量] ×100%
碳粉作为还原剂引入,它的用量与芒硝用量和窑内气氛有关,碳粉含率一般控制在芒硝用量的3.0%~5.0%(目前一些生产线在配料时取消了碳粉)。
④ 碎玻璃(熟料)含率。碎玻璃含率是指在配料时碎玻璃掺入量占总配合料量的百分数。即:
碎玻璃含率 (%) =[碎玻璃量/ (生料量+碎玻璃量)] ×100%
碎玻璃掺入量根据熔化条件和碎玻璃储存量调节,正常情况下控制在15%~20%。
2.5.2 配料表的手工计算
配料表分大料表(配料成分表)和小料表(配料称量单)。
计算大料表时,假定原料为干燥状态,按熔化100kg玻璃液所需各种原料的用量计算;小料表是依据大料表中原料的成分、混合机的大小及各种原料中的含水率,计算出每车混合料所需称量的各种原料的用量。配料操作工根据小料表进行配料称量。
下面以太阳能压延玻璃生产线的配料为例进行计算演示。
2.5.2.1 大料表计算
2.5.2.1.1 已知条件
a. 设计的太阳能压延玻璃成分如表2-26所示。
表2-26 太阳能压延玻璃设计成分表
b. 即将使用的原料成分如表2-27所示。
表2-27 原料化学成分分析表
c. 配料参数。纯碱飞散率=0.25%;芒硝含率=2.5%;碎玻璃含率=18%。
2.5.2.1.2 配料计算
一般向太阳能压延玻璃中引入SiO2的原料有低铁海砂、低铁硅砂(不同产地的硅质原料);引入Al2O3的原料有氧化铝、氢氧化铝和低铁长石。通常使用其中的一种即可满足玻璃成分需要,但有时由于原料供应、成分含量、制造成本、玻璃质量等问题,需要同时使用两种原料进行配料。
为了说明问题,下面对配料计算进行案例演示。
(1)原料用量初步计算
① 硅砂和氧化铝用量初步计算
设硅砂用量为x(kg),氧化铝用量为у(kg),根据表2-26和表2-27列出二元一次方程式:
SiO2:0.995x+0.00012у=72.35
Al2O3:0.001x+0.9867у=0.95
解方程得:
x=72.7135(kg);у=0.56(kg)
根据表2-27计算出由硅砂和氧化铝引入玻璃中各氧化物的量,见表2-28。
表2-28 由硅砂和氧化铝引入玻璃中各氧化物的量 单位:kg
② 方解石和白云石用量初步计算
方解石和白云石主要向玻璃中引入CaO 和MgO。
设方解石用量为x(kg),白云石用量为y(kg),根据表2-26和表2-27及由硅砂、氧化铝原料引入的CaO、MgO量(见表2-28),列出方程式:
CaO:0.5506x+0.3115y=8.82
MgO:0.005x+0.2115y=3.74
解方程得:
x=6.0962(kg);y=17.5391(kg)
根据表2-27,进而计算出由方解石和白云石引入玻璃中各氧化物的量,见表2-29。
表2-29 由方解石和白云石引入玻璃中各氧化物的量 单位:kg
③ 芒硝用量的计算
根据芒硝含率(%)=[芒硝中Na2O/ (芒硝中Na2O+纯碱中Na2O+硝酸钠中Na2O)]×
100%=[芒硝中Na2O/ (总Na2O -芒硝、纯碱和硝酸钠之外原料引入的Na2O)] ×100%
得出:
芒硝用量= (总Na2O-芒硝、纯碱和硝酸钠之外原料引入的Na2O) ×
芒硝含率÷芒硝中Na2O%
已知芒硝含率为2.5%,所以:
芒硝用量= (13.70-0) ×2.5%÷43.22%=0.7925(kg)
根据表2-27计算出由芒硝引入玻璃中各氧化物的量,见表2-30。
表2-30 由芒硝引入玻璃中各氧化物的量 单位:kg
④ 硝酸钠用量计算
太阳能压延玻璃通常使用氧化锑粉做澄清剂,使用氧化锑时须加入硝酸钠做氧化剂。硝酸钠用量一般为氧化锑粉的4~8倍或为芒硝用量的0.9~1.6倍。本案例按芒硝用量的1.2倍计算。
硝酸钠用量=0.7925×1.2 =0.951(kg)
根据表2-27计算出由硝酸钠引入玻璃中各氧化物的量,见表2-31。
表2-31 由硝酸钠引入玻璃中各氧化物的量 单位:kg
⑤ 纯碱用量初步计算
纯碱用量= (总Na2O-纯碱之外原料引入的Na2O) ÷纯碱中Na2O%
=[13.70- (0.3425+0.3444)] ÷58.20%=22.3593(kg)
⑥ 氧化锑用量计算
根据表2-26得知,三氧化二锑含量为0.20%,氧化锑粉用量计算如下:
氧化锑粉用量=0.20/0.995=0.201(kg)
以上计算均未考虑各原料次要成分的影响,应在得出上述数据后重新进行修正计算。
(2)原料用量修正计算
① 硅砂和氧化铝用量的修正计算
由硅砂和氧化铝以外的原料引入SiO2、Al2O3的量见表2-32。
表2-32 由硅砂和氧化铝以外的原料引入SiO2、Al2O3的量 单位:kg
设硅砂用量为x(kg),氧化铝用量为y(kg),列出二元一次方程式:
SiO2:0.995x+0.00012y=72.35-0.0106
Al2O3:001x+0.9867y=0.95-0.0179
解方程得:
x=0.8333(kg);y=72.7028(kg)
修正后,由硅砂和氧化铝引入玻璃中各氧化物的量见表2-33。
表2-33 由硅砂和氧化铝引入玻璃中各氧化物的量 单位:kg
② 方解石和白云石用量的修正
由方解石和白云石以外原料引入玻璃中的CaO和MgO的量见表2-34。
表2-34 方解石和白云石以外原料引入玻璃中的CaO和MgO的量 单位:kg
鉴于方解石和白云石以外原料引入玻璃中的CaO和MgO的量很少,可以忽略不计,故不做修正计算。
(3)原料用量精确修正计算
① 硅砂和氧化铝用量的精确修正计算
鉴于硅砂和氧化铝以外的原料引入SiO2、Al2O3的数量与修正计算相同,不再做精确修正计算。
② 纯碱用量修正计算
鉴于纯碱以外原料引入玻璃中的Na2O与初步计算相同,不再做修正计算。
③ 纯碱飞散率计算
设纯碱飞散量为x,根据公式:
纯碱飞散率 (%) =纯碱飞散量/ (纯碱用量+纯碱飞散量)
得:0.25%=x/ (22.3593+ x)
解得:x=0.056(kg)
④ 将上述计算结果汇总列入原料配料成分表(见表2-35)。
⑤ 原料配料成分表的微调
由于表2-35中实际玻璃成分Al2O3含量低于设计成分,Na2O含量高于设计成分,故进行微调。
表2-35 原料配料成分表(初算)
Na2O含量高出设计成分0.0326,取消纯碱飞散量。
纯碱用量中含Na2O量:13.7326-0.0326=13.70(kg)。
计算出纯碱用量:(13.70-0.3425-0.3444) ÷58.20%=22.3593(kg)。
Al2O3含量低于设计成分0.037,增加氧化铝用量:0.037÷0.9867=0.0375(kg)。
计算出氧化铝用量:0.8333+0.0375=0.8708(kg)。
⑥ 将上述微调结果填入表2-36,得出最终原料配料成分表。
表2-36 原料配料成分表(执行表)
⑦ 玻璃熔成率K的计算
表2-36中配合料的K= (100/121.5312) ×100=82.28%。
⑧ 配合料气体率的计算
表2-36中配合料气体率=[(121.5312-100) /121.5312] ×100=17.72%。
化验室人员应掌握各种原料使用情况,当原料成分有变化时,由化验室提前计算出配料表并及时下达新的配料表。
2.5.2.2 配料称量单的计算
上面计算出的原料配合料成分表只是知道了熔制100kg玻璃液所需各种原料的质量,而在实际生产中,因生产线混合机大小不同、原料含水率的波动等原因,配料量各不相同,因此,要根据原料配合料成分表计算出配料时各种原料的质量,即计算配料称量单。
以表2-36原料配料成分表举例计算配料称量单如下。
已知各原料配料前的含水率如表2-37。
表2-37 原料配料前含水率表
每次进混合机混合的生料量为2500kg,碎玻璃掺入率为18%。
① 碎玻璃掺入量的计算
设碎玻璃掺入量为x,根据公式:
碎玻璃掺入量=碎玻璃掺入率× (生料量+碎玻璃掺入量)
列方程式:x=18%× (2500+x)
解方程得:x=548.78(kg)
② 各原料干基量的计算
根据公式:
干基量倍数=生料量/每100kg玻璃液需用生料干基量
计算出各干基量倍数:2500/121.5312=20.5708
根据干基量倍数20.5708和表2-36中每100kg玻璃液需用生料干基量,得出各原料的干基用量,见表2-38。
表2-38 原料干基用量表
③ 各原料湿基量的计算
根据公式:
湿基用量=干基用量/ (1-原料含水率)
计算出各原料湿基用量,将其填入配料称量单,见表2-39。
④ 混合机加水量计算
为了使原料在混合机内充分混合,保证混合质量,一般在混合原料时要向混合机内加入一定量的热水,加水量根据各原料带入的含水量不同而有所差别。
表2-39 原料配料称量单
计算公式:
加水量=原料干基用量/ (1-含水率) -原料湿基用量
设定配合料含水率为4.1%,将表2-39中的数据带入公式得出加水量。
加水量=2500/ (1-4.1%) -2549.66=57.22(kg)
即要往混合机内加入57.22kg的热水。
将上述各项计算结果填入配料通知单,见表2-40,交付原料控制室进行配料,完成配料计算。
表2-40 配料称量通知单