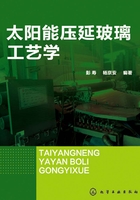
2.3 玻璃原料的选用、运输和储存
2.3.1 玻璃原料的选用原则
原料的选用是玻璃生产中的一个重要问题。对于一个确定的氧化物组分,可以用天然矿物原料引入,也可以用化工原料引入;对于同一种原料,也可能会有多种不同的物理状态。玻璃原料的选择应根据玻璃的成分、玻璃制品的质量要求、原料的来源、价格、供应的可靠程度以及对环境保护的影响程度等进行综合考虑。玻璃原料的选择是否合理,对原料的加工处理、玻璃制品的质量、产量以及生产成本等都有很大的影响。在选择和使用玻璃原料时,一般遵循以下几个原则。
(1)原料质量要符合要求
原料的品位要高,原料的化学成分和矿物组成都要符合规定的要求。原料中引入玻璃的氧化物含量愈高愈好,有害杂质和伴生矿物的含量要少,不能含有难熔矿物,铁的含量在规定的范围内愈低愈好。
对于大规模生产的太阳能压延玻璃来说,要使它的物理、化学性能和力学性能稳定,就必须要求原料的化学成分稳定。一般来说,化工原料的化学成分是比较稳定的,天然矿物原料的化学成分就不太稳定,允许的波动范围一般根据玻璃化学成分所允许的偏差值进行确定。
原料的颗粒组成应符合规定的要求,原料的水分要控制在规定的范围内,并保持稳定,水分波动过大,同样也会影响玻璃成分的稳定。
(2)利于熔化和澄清
选用易于熔化的原料可以节省燃料,提高熔化效率。在选用引入氧化铝的原料时,由于氧化铝熔点高、黏度大、难熔化,如果选用Al2O3分散度较小的原料(如化工氧化铝、高岭土、矾土等),就会因富集的Al2O3不易熔化和扩散,使玻璃的熔化率降低,均匀性变差;如果选用Al2O3分散度较大的长石,就可以避免或减少这种影响。
选用的原料要易于澄清。玻璃的原料不宜直接用氧化物,以氧化物的盐类(如碳酸钠、碳酸钙等)为好。这些盐类在玻璃的熔化过程中分解放出气体,气体的逸出带动玻璃液翻腾,有利于玻璃液的澄清和均化。例如,在选择引入CaO的原料时,一般都选用石灰石或方解石(CaCO3),而不选用生石灰(CaO),只有在小型坩埚内熔化玻璃时,由于原料中产生的气体太多会造成玻璃液满溢,才部分选用生石灰。
(3)对耐火材料的侵蚀要小
选用的原料应尽量不侵蚀耐火材料,如萤石等氟化物是有效的助熔剂,但对耐火材料的侵蚀较大,在熔制条件允许时,最好不用;硝酸钠对耐火材料的侵蚀也比较大,而且价格较贵,除了作澄清剂、脱色剂以及有时为了调节配合料的气体率而少量使用外,一般不作为引入Na2O的原料。对于同一种氧化物,应尽可能选用对耐火材料侵蚀小的原料,如Na2O具有助熔性,也会侵蚀耐火材料,用纯碱作为引入Na2O的原料时,纯碱分解成Na2O,特别是游离态的Na2O对耐火材料的侵蚀也较大;用长石引入的Na2O,其结构形态为硅酸盐或铝硅酸盐,可降低玻璃液中游离态Na2O的浓度,减弱对耐火材料的侵蚀。
(4)少用轻质原料和对人体健康有害的原料
轻质原料易飞扬,易分层,会侵蚀窑炉的上部结构和堵塞格子体,如有条件采用重质纯碱而不采用轻质纯碱;尽量不用沉淀的轻质碳酸镁、碳酸钙等。
在生产彩色玻璃时,对人体有害的白砒、氟化物等尽量不用,可部分或全部用三氧化二锑、焦锑酸盐代替。确需使用硒粉、铅化物等有毒有害原料时,在配料过程中操作者要穿戴好劳动保护用品,对操作环境要进行通风,并定期检查操作者的身体。
(5)少用易对环境造成危害的原料
有些原料虽然对生产玻璃有利,但在长期使用过程中,会对厂区周围环境造成一定的污染,所以尽量少用或不用。例如,芒硝在熔制过程中,其组分中的Na2O进入玻璃成分,大部分的SO2却通过烟囱排到空中,给大气造成污染;萤石等氟化物在熔制过程中,部分氟将成为HF、SiF4、NaF,其毒性较SO2还要大,氟化物能够在人体中富集,因此使用氟化物时应注意它对大气的污染。
(6)选用易于加工处理、价格低廉、运输方便、能大量供应的原料
选用易于加工处理的原料,既可降低设备投资,减少生产费用,又可以降低带入铁杂质的量。如石英砂和砂岩,若石英砂的质量能符合要求就不用砂岩,因为较好的石英砂不需加工处理就可以直接使用,一般的石英砂也只需经过筛分和精选处理就可以使用,而砂岩则要经过破碎、筛分(有些还需要经过煅烧)等加工后才能使用。对于白云石、石灰石,应选用SiO2含量低、硬度小、易于破碎加工的矿物原料。
在不影响玻璃制品质量的前提下,应尽量采用储量大、成本低、运输方便的当地资源,如生产绿色玻璃就可以就近选用含铁量略高的硅质原料等。
2.3.2 玻璃原料的运输
原料从矿山到生产厂内堆场(库房),再到配料仓,直至使用,这整个过程将经过运输→储存→运输→使用几个环节,由于这些环节都是开放式的,且线路长,所以,原料的运输和储存是玻璃生产中不可忽视的一个重要问题。如果原料的运输和储存不当,会使原料发生污染而报废,供应中断,甚至会因储存标识不准确或混料,发生用错料、配错料而严重影响正常生产的情况。
原料应尽可能做到定点供应,所有进厂原料均要求成分基本稳定,颗粒度合乎要求,不能带有杂质。为保证进厂原料符合标准要求,原料采购部门、化验室应定期对原料供应商供料情况进行实地检查;原料在运输进厂前,一定要经过有关部门的化验和鉴定。由矿山和石粉厂进行质量控制的原料,各种原料成分应控制在进厂以前,每批都要附带化验单;以粉料形式进厂的原料,其颗粒也应控制在进厂之前。由本厂进行质量控制的原料,应由本厂进行分析化验。
原料的运输主要依据当地的条件进行,厂外运输可采用火车、汽车、轮船。厂内运输可采用铲车、汽车、皮带输送机、螺旋输送机、气力输送机、斗式提升机等组成的运输体系,完成水平方向和垂直方向的输送。在运输过程中应尽量减少倒运次数,减少粉尘,防止各种原料彼此混杂,造成污染,影响原料的质量。
2.3.3 玻璃原料的储存
凡进厂的原料都应由化验室检验工检验,检验结果报化验室。如果发现有不符合玻璃生产工艺技术指标的原料,应及时通知生产技术和供应部门,由生产技术和供应部门共同对不合格原料进行评审;在未处理合格前不得入库。
原料车间应建立完善的原始记录管理制度。各种原料进厂卸料时必须有原始记录,记录内容为:名称、产地、卸料种类、卸车时间、入仓序号、入仓吨数、外观质量等。进厂原料入仓完毕后,化验室应在一周内对该批原料进行化学全分析,并及时通知外观检验员和相关仓库、堆场管理人员,质量合格后方可使用。
在玻璃工厂的生产过程中,所储存的原料数量根据各种原料的日用量、原料来源的可靠性、原料的运输距离、运输方式、气候条件及资金状况决定,一般储存数日至数十日,以不影响生产为限。若储存量不足,可能会因原料的供应中断而影响生产;若储存过多,则又会积压资金,增加仓储面积和倒运工作量。
原料进厂后不同产地、不同品种、不同品位、不同批次的原料必须分别入库,分类存放,不得混掺、混堆。储存方式取决于原料的物理、化学性质。通常,化工原料特别是纯碱、芒硝、硝酸钠等都应存放在干燥的仓库内。硝酸盐原料遇火有爆炸的危险,要特别注意防火;粉状的矿物原料应放在料仓内,用量大的硅砂也可以存放在堆场内,在露天堆场内存放时要注意防风、防雨、防冻等问题;有毒的原料,如硒粉等必须由专人负责,妥善保管,其包装用纸应当用火烧掉,禁防随地乱丢;易吸水潮解的原料应储存在密闭的容器内,各种着色剂原料也应分别存放在固定的容器内,要特别注意防止和其他原料混杂造成污染。
各种进厂原料和纯碱、芒硝等应进行标识,分别注明产地、品种、品位、批次、进仓(堆场)时间、分析时间、开始使用时间等;已经封仓、化验和正在使用的料仓(堆场)内不得继续堆放原料。
临时堆放的纯碱、芒硝,应码垛整齐,不得歪斜,并进行防潮、防水处理。纯碱进厂期相距15天以上的要分开码垛。硅砂和纯碱使用要贯彻“先来先用、后来后用”的原则。
在原料的储存、加工、倒运和使用过程中,应通过合理、有控制的堆放和取用方式,力求促使原料自身充分混合,以保证原料组成的均匀和稳定。
对以块料进厂的原料通常采用横码竖切法,即在存放原料时应一层一层地向上堆高,而取用时则以垂直方向的断面从各料层均匀切取,即使各料层物料的组成有些波动,但所切取各层物料的混合物还是相对均匀和稳定的。
对以粉料进厂的大宗原料例如硅砂,最佳方法是采用大面积分区堆场“纵撒层叠堆料,横刮分层取料”的均化库,这样不仅可以达到均匀储存硅砂的目的,更重要的是通过合理的堆存和取料作业,使硅砂成分、粒度和水分波动缩小到最小,起到均化的效果,从而使经过均化的原料的化学成分和物理性能的波动得到改善。实践证明,采用均化堆场预均化的原料比未均化的原料,成分波动可由均化前的±10%降低到±1%。采用均化堆场的堆料方法有人字形堆料法、波浪形堆料法和水平堆料法等几种。无论哪一种,都是力图通过堆料时料层的层层重叠和取料时的不同层面切割,以分散集中在一起的波动成分,对于成分有波动的使其波动更小一些,成分无波动的更稳定一些,从而起到原料成分和水分均匀一致化的目的。
对以粉料进厂的小宗原料或场地有限的玻璃厂家来说,多采用轮式装载机或桥式抓斗起重机进行简易堆高式倒料,端面粗放式取料的存储用料方式。此种方式,仅可称为储料,对原料成分的均化、水分和粒度的控制起不到任何有益的作用。这种粗放式的用料方式,在要求生产高质量玻璃的今天,已远远不能满足制备高质量配合料的需求,在有可能的情况下,应进行改进。