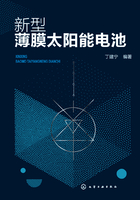
第2章 钙钛矿吸收层制备及优化
2.1 有机-无机杂化钙钛矿吸收层的制备方法
作为钙钛矿太阳能电池的光吸收层,有机-无机杂化钙钛矿薄膜的质量直接影响到钙钛矿太阳能电池的转换效率。结晶度高、光滑、致密的钙钛矿吸收层有助于促进薄膜内部光生载流子的产生和分离;相反地,粗糙、存在明显孔隙的钙钛矿薄膜会导致吸光度和光生电流下降,同时孔隙的存在会使电子传输层和空穴传输层部分接触,增加漏电路径,降低器件的并联电阻。因此合理优化制备工艺、改善钙钛矿薄膜质量,对于提高钙钛矿电池的光伏特性至关重要。目前,有机-无机杂化钙钛矿薄膜的制备方法主要有一步旋涂法、分步液浸法、两步旋涂法、共蒸法、分步气相辅助沉积法等[1],如图2-1所示。

图2-1 钙钛矿薄膜的制备工艺
2.1.1 一步旋涂法
一步旋涂法是将一定比例的PbX2(I-、Br-、Cl-)与CH3NH3I(MAI)混合溶解制成前驱体溶液,经旋涂、加热退火形成钙钛矿薄膜。退火的温度一般在100℃左右,以保证溶剂的挥发,促进晶体的形成。此方法制备的薄膜对成膜条件十分敏感,如前驱体溶液中溶剂的选择[2-6]、溶液浓度[7,8]、退火温度[9,10]等等。
溶剂影响:N,N-二甲基甲酰胺(DMF)和γ-丁内酯(GBL)是一步旋涂法中常用的溶剂。而采用不同溶剂制备出的钙钛矿薄膜形貌存在明显差异。当溶剂为DMF时,倾向于形成针状的钙钛矿晶体[图2-2(a)];而以GBL作为溶剂时,则会倾向于形成团簇状的晶体[图2-2(b)][5,11-13]。不过上述两种溶剂制备的钙钛矿薄膜均很难实现对衬底的完全覆盖,这不仅会降低器件的光吸收,更会导致空穴传输层与电子传输层的直接接触,进而产生严重的电荷复合,最终影响电池的光电转换效率。

图2-2 分别以DMF(a)和GBL(b)为溶剂制备的钙钛矿薄膜形貌
为了改善溶剂体系引起的衬底覆盖情况,丁建宁课题组[14]系统地研究了溶剂对钙钛矿薄膜的形貌和结晶度的影响,进一步发展了制备高质量钙钛矿薄膜的溶剂技术,实现了无须退火的钙钛矿制备工艺。该方法分别采用DMF/DMSO、DMAC(二甲基乙酰胺)/DMSO、DMF/NMP(N-甲基-2-吡咯烷酮)和DMAC/NMP四种溶剂体系作为钙钛矿前驱体的混合溶剂,旋涂工艺如图2-3所示。研究发现4种溶剂体系都能够有效地实现薄膜对衬底的全覆盖。相对于NMP/DMSO和DMAC/DMSO两种混合溶剂,DMF/NMP和DMAC/NMP溶剂体系制备出的钙钛矿薄膜更加平整均匀,钙钛矿晶粒尺寸更大,结晶性更好(图2-4)。更重要的是,利用DMF/NMP和DMAC/NMP溶剂体系的前驱体溶液旋涂薄膜,在滴加反溶剂之前薄膜颜色就已经变黑,这意味着该溶剂体系制备的薄膜无须退火,室温下溶剂就挥发完全,形成结晶度高的钙钛矿薄膜。未进行退火处理,基于DMAC/NMP溶剂体系的钙钛矿太阳能电池效率可达17.38%,而基于DMAC/DMSO混合溶剂的电池只获得了3.81%的效率。

图2-3 一步旋涂法工艺[14]

图2-4 不同混合溶剂制备的MAPbI3薄膜的SEM图[14]:(a)和(e)DMF/DMSO;(b)和(f)DMAC/DMSO;(c)和(g)DMF/NMP;(d)和(h)DMAC/NMP
溶液浓度影响:Snaith等[7]通过改变钙钛矿前驱体溶液浓度和TiO2致密层的厚度,调节钙钛矿薄膜的孔隙填充率。研究发现随着钙钛矿前驱体溶液浓度的增大,太阳能电池的光电流和光电压都有明显的改善。前驱体溶液的组成对薄膜的光电性质也有影响,黄劲松等[8]发现前驱液中PbI2/CH3NH3I的摩尔比从0.35变化到1.0,钙钛矿薄膜的吸收率、PL和XRD均明显变化(图2-5)。

图2-5 不同PbI2/CH3NH3I摩尔比制备的薄膜的(a)吸收光谱;(b)PL光谱;(c)XRD图[8]
退火温度影响:Snaith等[10]在TiO2致密层上制备CH3NH3PbI3-xClx钙钛矿薄膜,通过控制退火温度,来调节钙钛矿晶粒的尺寸大小和表面覆盖率。如图2-6所示,随着退火温度的升高,晶粒尺寸增大;材料表面结构从连续薄膜转变为离散的孤岛分布,降低了材料的表面覆盖率。

图2-6 不同退火温度下钙钛矿薄膜的SEM图[10]
环境湿度影响:杨阳等发现在合适的湿度(约30%)下进行退火,少量的水分可以进入钙钛矿晶界中,促使晶界发生移动,使晶体融合,然后形成晶粒尺寸为500nm左右的无孔洞薄膜[15]。在这一条件下,他们制备结构为FTO/PEDOT:PSS/MAPbI3-xClx/PC61BM/PFN/Al的电池效率达17.1%。另外,研究还发现,旋涂前衬底温度[12]、旋涂速率[17]、冷却速率[18]、退火气氛[16]、退火温度的梯度设定[13,19]等条件的调控都有助于提高钙钛矿薄膜的质量。
2.1.2 分步液浸法
2013年,Grätzel等[11]提出了一种可控性高、重复性好的分步液浸法,首先将PbI2从溶液引入到介孔TiO2中,随后将其浸入CH3NH3I溶液中反应转化成有机-无机杂化钙钛矿(图2-7)。研究发现,两种前驱液发生接触,反应在介孔TiO2内发生,使得更容易控制钙钛矿形态。使用这种技术制备太阳能电池能够大大提高工艺的可重复性,并获得了当时钙钛矿电池的最高转换效率15%。

图2-7 钙钛矿薄膜的SEM截面图[11]
分步液浸法最大的局限性是不利于制备较厚的平面型钙钛矿薄膜[20,21]。实验显示,当在平面衬底上使用分步液浸法时,只能制备约200nm厚的钙钛矿薄膜。厚度一旦增加,CH3NH3I很难扩散到PbI2层较深的位置,导致剩余大量未反应的PbI2,降低了电池的性能[24]。通过改变PbI2薄膜的形貌[22],可使其转化趋于完全。郑灵灵等[23]通过将旋涂的PbI2薄膜放在室温下晾干以取代高温烘干的步骤,可以使PbI2自发形成带有多孔结构的薄膜,为后续的CH3NH3I的渗入提供了充足的空间和途径。采用该方法制备的电池效率达16.5%,与之前相比有了显著提升。然而,此方法制备的电池对迟滞现象的抑制作用并不明显。为了减少器件的迟滞,他们还采用二次生长的方法,将薄膜重复浸泡于CH3NH3I溶液中,不仅能使PbI2完全转化为钙钛矿,而且可形成由较大晶粒组成的致密平整的薄膜。基于此方法的平面电池效率和迟滞分别得到提高和抑制。
2.1.3 两步旋涂法
两步旋涂法,也叫作互扩法,是由黄劲松等提出的[20]。这个方法也可认为是在分步液浸法的基础上衍生出来的,而且二者获得的薄膜形貌也是非常相似的[24,25]。两者的区别在于两步旋涂法是一种精确定量的方法。他们将PbI2和MAI分别溶解在二甲基甲酰胺(DMF)和异丙醇中,作为前驱体溶液。如图2-8所示,通过先旋涂PbI2薄膜,再旋涂适量的CH3NH3I薄膜形成双叠层薄膜,通过退火实现两层薄膜之间的互相扩散和反应,生成单一组分的有机-无机杂化钙钛矿薄膜。其形成机理是PbI2与溶剂DMF形成较弱的配位健,当CH3NH3I旋涂后,PbI2首先与碘离子反应形成PbI3-,之后在甲胺离子的作用下转化生成钙钛矿,而DMF在退火过程中会完全挥发[25]。

图2-8 两步旋涂法的工艺[10]
齐江[26]等采用了两步旋涂法来精细控制钙钛矿薄膜,并制备n-i-p平面结构太阳能电池。首先在电子传输层上旋涂PbI2,然后将碘化甲脒(FAI)、溴化甲胺(MABr)和氯化甲胺(MACl)混合溶液涂覆在PbI2层上,最后通过退火PbI2/FAI准双层扩散形成钙钛矿相。制备的电池效率达21.6%。
2.1.4 气相沉积法
Snaith等[27]首次报道了通过气相沉积法制备钙钛矿太阳能电池的工艺。利用双源共蒸[图2-9(a)]可形成均匀平整的混合卤化物钙钛矿(CH3NH3PbI3-xClx)薄膜及平面异质结p-i-n太阳能电池器件[图2-9(c)]。图2-9(b)所示的是气相和液相法制备的钙钛矿的XRD谱图,晶体结构如图2-9(d)所示。

图2-9 气相沉积制备钙钛矿太阳能电池[27]
(a)双源共蒸的工艺;(b)气相和液相法制备的钙钛矿的XRD图;(c)器件结构;(d)晶体结构
气相沉积法和溶液法制备的薄膜表面形貌和横截面形貌(图2-10)存在着明显差异。气相沉积制备的薄膜表面平整光滑、致密、厚度均匀。相比之下,溶液法制备的薄膜只是部分覆盖衬底,表面起伏比较大。

图2-10 气相沉积法和溶液法制备的钙钛矿薄膜形貌[27]
双源共蒸的气相沉积法对工艺的控制精度要求高,为此,研究者提出了其他的气相沉积方法[29-33],试图让薄膜制备控制更容易。林浩武等[29]提出了分步气相沉积的方法,通过逐层顺序真空升华方式来进行钙钛矿薄膜的沉积:先在衬底上利用蒸发方法制备PbCl2薄膜,再将其放在低温区(65~85℃),将CH3NH3I粉体置于85℃高温区域气化,最后在低温区反应形成CH3NH3PbI3-xClx薄膜。调控PbCl2薄膜的结晶性和表面粗糙度,可影响CH3NH3PbI3-xClx的结晶质量。该方法制备的电池获得了15.4%的转换效率。Longo等[31]开发了闪蒸的方法来制备钙钛矿薄膜。该方法将钙钛矿粉末作为蒸发源,利用较大的电流瞬间蒸发形成200nm左右的钙钛矿薄膜。基于此薄膜的平面型电池获得了12.2%的效率。而采用CVD法[32]同样可以制备出高质量的钙钛矿薄膜。将CH3NH3I粉末置于高温区气化,通过N2气流动,CH3NH3I气体就可以到达放置了PbI2薄膜的低温区段,然后进行反应。钙钛矿薄膜的形貌和生长可以通过装置中的气流速率、温度和压力进行控制。
研究人员采用溶液法和气相沉积法相结合的制备方法[34]获得了粒径达微米级、表面全覆盖且表面粗糙度低的薄膜。该方法首先将PbI2薄膜旋涂沉积在涂覆有致密TiO2层的FTO玻璃上,然后在CH3NH3I气体中,在150℃下反应2h形成钙钛矿薄膜(图2-11),所得到薄膜的厚度约为350nm。电池转换效率为12.1%。

图2-11 溶液法和气相沉积法相结合制备钙钛矿薄膜的工艺流程[34]