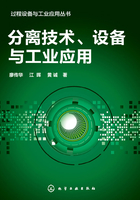
3.3 萃取精馏
萃取精馏和恒沸精馏相似,也是向原料液中加入第三组分(称为萃取剂或溶剂),以改变原有组分间的相对挥发度而达到分离要求的特殊精馏方法。但不同的是要求萃取剂的沸点较原料液中各组分的沸点高得多,且不与组分形成恒沸液,容易回收。萃取精馏常用于分离各组分挥发度差别很小的溶液。
例如,在常压下苯的沸点为80.1℃,环己烷的沸点为80.73℃,若在苯-环己烷溶液中加入萃取剂糠醛,则溶液的相对挥发度发生显著的变化,且相对挥发度随萃取剂量加大而增高,如表3-2所列。
表3-2 苯-环己烷溶液加入糠醛后α的变化

3.3.1 萃取精馏的基本原理
萃取剂的加入,改变了原有组分间的相对挥发度,而在这种情况下,往往改变了原有组分的相互作用,因为溶液为非理想溶液,故组分的活度系数将会发生改变。这可从组分1、2间的相对挥发度看出。
(3-9)
当两组分沸点间的差值较大时,反映在及
数值上的差值亦较大,但由于还有活度系数的影响,也有可能使相对挥发度的数值接近于1。如醋酸甲酯(以组分1代之)和甲醇(以组分2 代之)溶液,在54℃时x1=0.649,
=0.889×105Pa,虽然在常压下组分1的沸点t1=57℃,组分2的沸点t2=64.5℃,沸点差为7.5℃,
=0.659×105Pa,但由于活度系数不同,γ1=1.12,γ2=1.53,当在54℃时,其相对挥发度为:
表明该溶液是恒沸物,不能分离。由此看出,相对挥发度不仅与物系的存在条件有关,而且与物系的性质即活度系数有关。
3.3.2 萃取剂的选择
采用萃取精馏时,分离效果的好坏与萃取剂的选择有很大关系。萃取剂的选择性,指的是改变原有组分间相对挥发度数值的能力,即α12,S与α12的比值越大,选择性越好,此外,还需考虑如下问题。
①萃取剂不与原组分发生化学反应,不形成恒沸液,与原组分容易分离。
②萃取剂的挥发度应低些,即其沸点应较原混合液中纯组分的为高,在塔内呈液相。
③萃取剂对被分离组分的溶解度要大,避免发生分层现象。
④无毒性、无腐蚀性,热稳定性要好。来源方便,价格低廉。
目前,萃取剂主要通过实验来进行选择,基本方法有以下几种。
(1)实验方法
通过测定有萃取剂存在下的气液平衡数据是最准确的选择方法,但实验次数多,操作繁复。常以等摩尔的被分离组分混合液中加入等质量的萃取剂(如混合液及萃取剂各100g)相混合后,通过测定气液两相的平衡组成,并计算其相对挥发度α12,S。相对挥发度越大,萃取剂选择性越强。
(2)按溶剂溶解度的大小
溶剂溶解度的大小直接影响萃取剂的用量、动力和热量的消耗,以C4为例,不同溶剂的溶解度见表3-3。
表3-3 不同溶剂对C4的溶解度

(3)从同系物中选择
按萃取剂的萃取原理,通常希望所选的萃取剂应与塔釜产品形成理想溶液或具有负偏差的非理想溶液。与塔釜产品形成理想溶液的萃取剂容易选择,一般可由同系物或性质接近的物料中选取。对萃取精馏希望α1S值越大越好,所以希望萃取剂与塔顶组分1形成具有正偏差的非理想溶液,且正偏差越大越好。例如甲醇-丙酮(甲醇沸点64.7℃,丙酮沸点56.4℃)溶液具有最低恒沸点,t恒=55.7℃、x(CH3OH)=0.2的非理想溶液,如用萃取精馏分离时,萃取剂可有两种类型,如表3-4所列。
表3-4 两种类型的萃取剂

一种是由甲醇同系物中选取,此时,塔顶蒸出丙酮,塔釜排出甲醇及萃取剂(甲醇同系物);另一种可从丙酮的同系物中选取,此时,塔顶蒸出甲醇,塔釜排出丙酮及萃取剂(丙酮同系物),如用丙酮的同系物作萃取剂时,该萃取剂要克服原溶液中沸点差异,使低沸点物质与萃取剂一起由塔釜排出。
3.3.3 萃取精馏流程
萃取精馏中萃取剂的加入量一般较多,以保证各层塔板上足够的添加剂浓度,而且萃取精馏塔往往采用饱和蒸汽加料,以使加料段和提馏段的添加剂浓度基本相同。
图3-11为分离苯-环己烷溶液的萃取精馏流程示意。原料液进入萃取精馏塔中,萃取剂(糠醛)由塔1顶部加入,以便在每层板上都与苯相结合。塔顶蒸出的为环己烷蒸气。为回收微量的糠醛蒸气,在塔1上部设置回收段2(若萃取剂沸点很高,也可以不设回收段)。塔底釜液为苯-糠醛混合液,再将其送入苯回收塔3中。由于常压下苯沸点为80.1℃,糠醛的沸点为161.7℃,故两者很容易分离。塔3中釜液为糠醛,可循环使用。在精馏过程中,萃取剂基本上不被汽化,也不与原料液形成恒沸液,这些都是有异于恒沸精馏的。

图3-11 分离苯-环己烷溶液的萃取精馏流程
1—萃取精馏塔;2—萃取剂回收段;3—苯回收塔;4—冷凝器
萃取精馏主要应用于以下三种情况。
(1)组分沸点相近的混合溶液分离
如庚烷(沸点98.5℃)与甲基环己烷(沸点100.8℃)在常压下的相对挥发度为1.07,用普通精馏方法分离较困难。当加入70%(质量分数)苯胺作溶剂进行萃取精馏时,相对挥发度增大至1.3,理论板数可减少75%。
(2)非理想溶液的分离
由于溶液的非理想性,随着组成的改变,相对挥发度也有较大的变化,因而在某一组成范围内可能相对挥发度接近于1,而使分离困难。如甲基环己烷(沸点100.8℃)与甲苯(沸点110.6℃)的混合溶液,当甲基环己烷浓度增大时,相对挥发度随之降低,当甲基环己烷为90%(摩尔分数)时,相对挥发度只有1.07,使分离发生困难,但可以苯胺为溶剂用萃取精馏方法分离。
(3)有恒沸点混合溶液的分离
恒沸溶液是非理想溶液的一种特殊形式,如乙醇-水溶液,用普通精馏方法只能得到一个纯组分和一个恒沸物。在恒沸组成时相对挥发度为1,在理论上要分离一个恒沸溶液得到两个纯组分所需理论塔板数应是无穷多,实际上不可能办到。
3.3.4 萃取精馏过程的计算
(1)萃取剂用量的计算
在萃取精馏塔内,萃取剂的挥发度比所处理物料的挥发度低得多,为了使萃取剂在每块塔板上都能起作用,萃取剂就必须从精馏段顶部加入,又因为萃取剂的用量较之欲分离的各组分大得多,故在各塔板的溢流中基本上维护了一个固定的浓度值,一般称为恒定浓度,记为xS。xS可根据所用萃取剂的技术经济等因素来决定。由选定的xS值,进一步作物料衡算便可求出萃取剂的用量。
假设塔内为恒摩尔流,塔顶蒸出的萃取剂量忽略不计,萃取剂在塔内各层板上维持恒定浓度,如图3-12所示,对精馏段进行物料衡算,则由萃取剂的衡算可得出:
S+(L+D)yS=(S+L)xS (3-10)

图3-12 萃取精馏塔内物料衡算
式中 S——萃取剂量,mol/h;
V——精馏段上升蒸汽量(不包括萃取剂),V=L+D,mol/h;
L——精馏段回流量(不包括萃取剂),mol/h;
xS——液相中萃取剂的恒定摩尔分数;
yS——气相中萃取剂的摩尔分数。
萃取剂对被分离组分的相对挥发度β为:
(3-11)
式中 β——萃取剂与待分离组分(组分1和组分2)相对挥发度。一般可按下式计算:
(3-12)
由式(3-10)及式(3-11)两式联解可得出:
(3-13)
由式(3-13)可根据规定的xS值,计算出萃取剂用量S。因为β的数值一般很小,故在近似计算中,也可以把它当成零。
实际上,由于萃取剂的相对量较大,塔内温度越往下越高,因此,越往下蒸汽量也越大,即塔内并非恒摩尔流,而xS值是越往下,其值逐渐减小。所以要作精确计算时,必须结合物料衡算和热量衡算逐板确定。
用推导式(3-13)相似的方法,同理对提馏段可得出:
(3-14)
式中 ——提馏段萃取剂恒定摩尔分数;
——提馏段的液相流量,kmol/h。
当加料为饱和蒸汽时,L=,故xS=
;若加料低于露点温度时,L>
,则xS>
。这样提馏段的相对挥发度α12,S小于精馏段的值。如果要想使整个塔上下有同样的萃取剂的恒定浓度,则可在进料中加入适量的萃取剂。一般萃取精馏多采用饱和蒸汽进料。
(2)回流比的确定
应用解析法先计算出最小回流比,然后根据生产经验,增加某一百分数作为实际操作回流比。由于每块塔板萃取剂浓度很大,并在全塔可以视为恒定浓度,在这种条件下,若要分离的溶液是一个二组分溶液,则在饱和液体进料时,可按下式计算出最小回流比:
(3-15)
在饱和蒸汽进料时,可按下式计算最小回流比:
(3-16)
若加料为多组分溶液时,可按恩德伍德公式进行计算。
(3)萃取精馏塔理论板的确定
根据萃取剂沸点高、挥发度小的特点,由塔顶引入萃取剂后,几乎全部流入釜底,因而萃取剂在塔内各板上的浓度恒定不变,可将萃取过程作为双组分物系处理(以脱溶剂为基准),其理论塔板数的确定可用简捷法。简捷法又分为图解法和简捷计算法。
图解法,即先根据一定的xS画出图3-13所示的y-x图,然后同双组分用作图法求出理论塔板数。应注意的是,因萃取剂浓度对α12,S的影响很大,故根据加料情况不同,若精馏段与提馏段的xS不是同一数值时,就必须用两段不连续的y-x曲线来表示(见图3-14),在改用操作线的同时,也要改用平衡线。在操作线和平衡线之间画阶梯,这样就能确定精馏段和提馏段的理论塔板数。

图3-13 按二组分系统处理的y-x图

图3-14 确定萃取精馏塔理论板数的图解法
简捷法计算理论塔板数较快,但准确性欠缺。当物系缺少准确的平衡数据,不能采用逐板法计算时,仍以此法为宜,并且一般可以满足工程上估算的需要。计算程序与二组分精馏相似,在计算出最小回流比和最小理论塔板数之后,可用吉利兰关联图同时确定出实际回流比R及所需要的理论板数N。
3.3.5 萃取精馏的注意事项
萃取精馏与一般精馏虽然都是利用液体的部分汽化、蒸汽的部分冷凝产生的富集作用,从而将物料加以分离的过程,但由于萃取精馏中加入了大量的萃取剂,因此与一般精馏相比有如下几点需要注意。
①由于加入的萃取剂是大量的(一般要求xS>0.6),因此,塔内下降液量远远大于上升蒸汽量,从而造成气液接触不佳,故萃取精馏塔的塔板效率低,大约为普通精馏的一半左右(回收段不包括在内)。在设计时应注意塔板结构及流动动力情况,以免效率过低。
②由于组分间相对挥发度是借助萃取剂的加入量来调节的,α12,S随萃取剂在液相中的浓度xS的增加而增大。当塔顶产品不合格时,不能采用加大回流的办法来调节,因这样做会使萃取剂在塔内浓度降低,反而使情况更加恶化。一般调节方法有:加大萃取剂用量;减少进料量,同时减少塔顶产品的采出量。这也就是在不改变下降液量的前提下加大了回流比。
③通常萃取剂用量较大,塔内液体的显热在全塔的热负荷中占较大比例,所以,在萃取剂加入时,温度微小的变化,直接影响上升蒸汽量,从而波及全塔。应该以萃取剂恒定浓度与萃取剂温度作为主要被调参数,以保持塔的稳定,当操作条件接近液相分层区时,更要特别注意。
④在决定塔径及设计塔板结构时,除了按照蒸汽量(包括溶剂蒸气在内)计算外,还应注意液流中有较大量的萃取剂。
⑤在萃取精馏塔内,液相中萃取剂的浓度一般为xS>0.6,此时,塔中组分1、组分2的浓度变化范围仅在x1+x2<0.4以内,因此,塔内温度有些变化,由塔顶向下温度会升高,但变化不显著。
在回收段内,由于萃取剂含量迅速下降,仅几块板,即可使xS由0.6~0.8变为xS≈0,这样会引起温度的陡降。塔釜处,由于基本上是萃取剂,因此塔釜温度也可能会急剧上升。