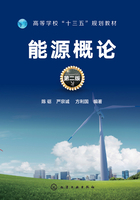
2.6 煤的洁净技术
如何在煤炭的开发、利用过程中减少对环境的危害,同时能从煤炭这一传统的“不清洁”能源获得“清洁”的气体与液体燃料,成为全世界能源科技工作者追求的目标。“洁净煤技术”这一概念也就由此产生了。通过30年的努力,已经形成了许多成熟的洁净煤技术。
洁净煤技术是指在煤炭从开发到利用的全过程中,旨在减少污染物的排放与提高利用效率的煤炭加工、燃烧、转化及污染物控制等新技术。主要包括洁净生产技术、洁净加工技术、高效洁净转化技术、高效洁净燃烧与发电技术和燃煤污染排放治理技术等。研究与开发洁净煤技术的主要目的是攻克煤气化、煤炭液化、洁净煤发电技术和综合利用新技术中的关键技术,大幅度提高煤炭转换过程中的效率和控制污染,提供优质替代燃料,优化终端能源结构,保障能源安全。
本节主要介绍煤炭洗选、加工(型煤和水煤浆等)、转化(煤炭气化和煤炭液化等)、先进燃烧技术(常压循环流化床、增压流化床、整体煤气化联合循环和高效低污染燃烧器等)、烟气净化(除尘和脱氮等)等方面的内容。煤的转化技术属于更复杂的化学过程,下一节再作介绍。
2.6.1 煤炭的洗选和加工技术
开发洁净煤技术,人们首先想到的是在煤被开采出来后将其中对环境有害的物质通过某种方法分离出去,如将煤中的灰分分离出去,就可以降低煤在燃烧或转化过程中排出大量的灰分,从而减少颗粒物的排放污染;将煤中的含硫化合物分离出去,就可以降低燃烧过程中硫分的排放,从而减少二氧化硫污染;将煤中的含氮化合物分离出去,就可以降低燃烧过程中氮的排放,从而减少氮氧化物的污染。
(1)煤炭洗选技术
煤炭洗选技术又称选煤,是利用煤和杂质(矸石)的物理、化学性质的差异,通过物理、化学或微生物分选的方法使煤与杂质有效分离,并加工成质量均匀、用途不同的煤炭产品。选煤方法主要有物理选煤技术、化学选煤技术和微生物选煤技术。目前我国原煤洗选超过50%,而发达国家原煤已全部洗选,洗选效率在95%以上。
物理选煤法主要是根据煤炭和杂质的物理性质(如粒度、密度、硬度、磁性及电性等)的差异进行分选。主要的物理分选方法有重力选煤、重介质选煤、斜槽选煤、风力选煤等。浮选法属于物理净化的另一类方法,它是依据矿物表面物理化学性质的差异进行分选,主要包括机械搅拌式浮选和无搅拌浮选。
一般选煤工艺包括三个过程:即煤的预处理、煤炭的分选、产品的脱水。原煤预处理包括接收、储存、破碎和筛分。第二步进行分选。分选后产品要进行脱水,最后还要对煤泥水进行处理。
煤炭洗选后,可脱除煤中50%~80%的灰分、30%~40%的全硫或60%~80%的无机硫,燃用洗选煤可有效减少烟尘、SO2和NO2的排放。同时由于煤炭的质量提高,可以提高煤炭的利用率。
化学法净化技术是借助化学反应使煤中有用成分富集,除去杂质和有害成分的工艺过程。根据常用的化学药剂种类和反应原理的不同,目前在实验室常用的化学脱硫方法,分为碱处理、氧化法和溶剂萃取法等。化学法可以脱除煤中大部分的黄铁矿硫,其能源热值回收率也很高(大于95%)。此外,化学法还可以脱除煤中的有机硫,这是物理方法无法做到的。
微生物净化法在国内外引起广泛的关注,是因为它可以同时脱除其中的硫化物和氮化物,与物理法和化学法相比,该法还具有投资少,运转成本低,能耗少,可专一性地除去极细微分布于煤中的硫化物和氮化物,减少环境污染等优点。这一方法是由生物湿法冶金技术发展而来的。它是在常温常压下,利用微生物代谢过程的氧化还原反应达到脱硫的目的。微生物用于煤的脱氮,目前研究得很少。
(2)动力配煤技术
煤炭的消费中,绝大部分用于各种类型的锅炉和窑炉,在现有条件下,提高锅炉热效率,保证锅炉正常高效运行,是节省能源,减少污染的一个重要措施。动力配煤技术就是以煤化学、煤的燃烧动力学和煤质测试等学科和技术为基础,将不同类别、不同质量的单种煤通过筛选、破碎,按不同比例混合和配入添加剂等过程,提供可满足不同燃煤设备要求的煤炭产品的一种成本较低、易工业化实施的技术。通过动力配煤,可充分发挥单种煤的煤质优点,克服单种煤的煤质缺点,生产出与单种动力用煤的化学组成、物理性质和燃烧特性完全不同的“新煤种”,达到提高效率、节约煤炭和减少污染物排放的目的。
采用动力配煤技术可以最大限度地利用低值煤或当地现有煤炭资源;使燃煤特性与锅炉的设计参数相匹配,提高设备热效率,节省煤炭;将不同品质的煤相互配合,可以调节煤炭中的硫分、氮及其他矿物质组分的含量,减少有害元素的排放,满足环境保护的要求。
(3)型煤技术
型煤是用一种或数种煤粉与一定比例的黏结剂或固硫剂在一定压力下加工形成的,具有一定形状和一定物理化学性能的煤炭产品。高硫煤成型时可加入适量固硫剂,大大减少二氧化硫的排放。工业层燃锅炉和工业窑炉燃用型煤和燃用原煤相比,能显著提高热效率,减少燃煤污染物排放。我国民用燃煤一般都用型煤。我国民用型煤比烧散煤热效率提高1倍,一般可节煤20%~30%,烟尘和二氧化硫减少40%~60%,一氧化碳减少80%。在工业窑炉中使用可节煤15%,烟尘减少50%~60%,二氧化硫减少40%~50%,氮氧化物减少20%~30%。所以型煤是适合中国国情的,应该鼓励推广使用的洁净煤技术之一。
(4)水煤浆技术
水煤浆技术是一种以煤代油的煤炭利用新方式。国际上称为CWM(coal water mixture)或CWF(coal water fuel)。将65%~70%的煤粉、30%~35%的水及0.5%~1.0%的分散剂和0.02%~0.1%的稳定剂加入磨机中,经磨碎后成为一种类似石油的可以流动的煤基流体燃料。水煤浆具有较好的流动性和稳定性,可以像石油产品一样储存、运输,并且具有不易燃、不污染的优良特性,是目前比较经济和实际的清洁煤代油燃料。
水煤浆一般燃烧率可达96%~98%,综合燃烧效率相当于或略低于燃煤粉锅炉的效率。但其单位热强度和燃烧负荷范围(50%~120%)都优于燃煤粉锅炉,启动点火温度比燃煤粉锅炉低100℃。由于水煤浆是采用洗精煤制备的,其灰分、硫分较低,在燃烧过程中,水分的存在可降低燃烧火焰中心温度,抑制氮氧化物的产生量。另外,水煤浆自煤炭进入磨机后即可以采用管道、罐车输送,不会造成煤炭运输和储存污染,具有较好的环保效果。
2.6.2 高效的燃烧技术
(1)燃煤锅炉的低NOx燃烧技术
煤燃烧产生排放的NOx主要有两个来源:由燃烧空气中游离的氮和氧在高温下反应形成的燃烧型NOx,煤炭中挥发分带来的有机氮化物在燃烧中形成挥发性NOx。
低NOx燃烧技术就是根据NOx的生成机理,在煤的燃烧过程中通过改变燃烧条件或合理组织燃烧方式等方法来抑制NOx生成的燃烧技术。
低过量空气燃烧是其中最简单的方法。使燃烧过程尽可能在接近理论空气量的条件下进行,随着烟气中过量氧的减少,可以抑制NOx的生成,一般可以降低NOx排放15%~20%。还有空气分级燃烧、再燃技术、烟气再循环、低NOx燃烧器等技术都可以抑制NOx的生成。
(2)循环流化床燃烧技术(CFBC)
循环流化床锅炉燃烧技术系指小颗粒的煤与空气在炉膛内处于沸腾状态下,即高速气流与所携带的稠密悬浮煤颗粒充分接触燃烧的技术。具有氮氧化物排放低、可实现在燃烧过程中直接脱硫、燃料适应性广、燃烧效率高和负荷调节范围大等优势,已成为当前煤炭洁净燃烧的首选炉型。CFBC锅炉炉膛温度远低于煤粉炉,固体浓度和传热系数在炉膛底部最大,温度随炉膛高度分布均匀。
CFBC燃烧系统一般由给料系统、燃烧室、分离装置、循环物料回送装置等组成。燃料和脱硫剂一起进入锅炉,固体颗粒在炉膛内,在由底部吹来具有一定风速的气流的鼓动下,以一种特殊的气固流动方式运动,高速气流与所携带的稠密悬浮煤颗粒充分接触,进行流化燃烧。燃煤烟气中的SO2与氧化钙接触发生化学反应被脱除,大部分已燃尽或未燃尽的燃料升至炉膛顶部出口,经过旋风分离器将大颗粒燃料再返回床内燃烧,通过旋风分离器的烟气及微粒则经烟道排至烟囱,如图2-8所示。

图2-8 流化床燃烧锅炉
超临界CFBC是下一代CFBC技术,超临界锅炉的高压蒸汽压力最低为23MPa,最高为35MPa。由于运行时的压力和温度超过了水/汽的临界点,并没有由液态水到饱和蒸汽,然后到过热蒸汽的变化过程,在临界点以上,水以超临界流体形式存在,液态水和饱和蒸汽没有什么区别。当水在23MPa的压力下加热时,液态水的焓值从1977kJ/kg增加到2442kJ/kg,它的物理性质从液态连续变化到气态。超临界CFBC锅炉一般用于大型火力发电锅炉,其生产规模达200MW以上,在锅炉蒸汽温度达到600℃,压力在25MPa以上的超临界操作条件下运行,机组的净效率可以达到40%~41%,是一种具有明显优势的适于在中国大量推广的高效洁净煤发电技术。
2.6.3 燃煤烟气净化技术
烟气净化是指从燃煤烟气混合物中除去颗粒物、气态污染物、有机污染物、痕量重金属这四类主要污染物,将其转化为无污染或是易回收的产物的过程。属于燃烧后的净化措施,包括烟气脱硫、烟气除尘和烟气脱硝三大类技术。
(1)烟气脱硫
烟气脱硫一般分为干法和湿法两类。
①石灰石-石膏湿法 采用廉价的石灰石或石灰浆为脱硫吸收剂,在吸收器内,烟气与石灰浆液接触混合,烟气中的SO2与浆液中的CaCO3反应被脱除,脱硫后的烟气经除雾器除去液滴后排入大气。吸收浆液在多次循环利用后,经脱水后回收或掩埋。这种脱硫方法效率可达到95%以上,适用于任何含硫煤质的烟气脱硫。
②喷雾干燥法 用石灰加水制成消石灰乳作吸收剂,在吸收塔内,吸收剂雾状喷洒,与烟气混合接触,将烟气中SO2转化成CaSO3。喷雾干燥法脱硫工艺技术成熟,系统的可靠性高,脱硫效率可达85%以上。
③电子束法 烟气经过除尘器粗滤并冷却到70℃后进入反应器,在反应器入口处喷入氨水、压缩空气混合物,经过电子束照射后,SOx和NOx在自由基作用下生成硫酸(H2SO4)和硝酸(HNO3),再与共存的氨发生中和反应,最终生成粉状的硫酸铵[(NH4)2SO4]和硝酸铵(NH4NO3)的混合粉体,从反应器底部排出。净化后的烟气排向大气。
④活性炭吸附法 含SO2的烟气通过内置活性炭吸附剂的吸收塔,SO2被活性炭吸附而达到脱除的目的,脱硫效率可达98%以上。吸附了硫的活性炭通过水蒸气再生可以反复使用。
(2)烟气除尘
①旋风分离 旋风分离器是利用旋转的气流对其中的粉尘产生的离心力,将粉尘从气流中分离出来的除尘装置。一般可用来捕集5~15μm以上的颗粒物,除尘效率可达80%以上。其优点是设备结构简单,投资少,操作维修费用低,能应用于高温、高压以及有腐蚀性气体的场合。但对5μm以下的细小颗粒的捕集效果不高。
②布袋除尘 利用织物制作的袋状过滤元件来捕集含尘气体中的固体颗粒物,被捕集了颗粒的烟气排入空中。这种方法除尘效率高,可以达到99%,处理能力大,设备结构简单,造价低,操作维护费用低。缺点是设备体积大,压力损失大,滤袋破损率高,使用寿命短。
③电除尘 在电除尘设备中,使浮游在气体中的粉尘颗粒,在电场力的驱动下,作定向运动,从气体中分离出来。其优点是可以捕集一切细微的粉尘颗粒及雾状液滴,适用范围广,压降小,能耗低。但其缺点是设备体积大,对制造、安装和运行的要求高,对粉尘的特性较为敏感。
(3)烟气脱硝
①选择性催化还原法(SCR) 烟气在有镍、钒等金属元素的催化剂的作用下,在300~400℃的条件下,NOx与加入的NH3产生还原反应,生成N2。当氨/NOx控制在0.9时,脱除效率可达85%以上。
②选择性氨催化还原法(SNCR) 该方法与上面的SCR法类似,但不使用催化剂,在850~1100℃的温度范围内,将NOx还原,其平均脱除效率为30%~65%。
③活性炭法 活性炭可以同时脱硫脱硝。吸附反应在90~110℃条件下进行,吸附后的活性炭可以在解析器中解析再生,这种方法脱硝效率可达85%左右。