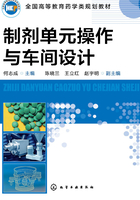
第一节 固体粒子的性质
制剂生产中,固体药物制剂占比约70%~80%,所用的物料几乎全部都是粉体。以粉体为中间体的剂型有散剂(或粉剂)、颗粒剂、胶囊剂、片剂、粉针和混悬剂等。
通常把粒径小于100μm的粒子称作“粉”,把粒径大于100μm的粒子称为“粒”。粒径小于100μm的颗粒之间,容易受到相互引力的作用,所以流动性较差;粒径大于100μm的粒子,因自重远大于粒子间的相互引力,所以流动性较好。粒径小于30μm的粉体称为超细粉体,将组成粉体的颗粒尺寸大于1μm的粉体称为微米级粉体,颗粒尺寸(三维尺寸中至少有一维)小于1μm(1000nm)且大于1nm的粉体称为纳米级粉体。
一、固体的性质
固体物料的粉碎、筛选及造粒设备的选型与该固体的性质、数量及尺寸有关,较重要的固体性质有:硬度、脆性与韧性。
(一)硬度
材料局部抵抗硬物压入其表面的能力称为硬度。物质的硬度对设备操作时的功率消耗及磨损程度均会产生影响。
表1-1是几种物质的莫氏硬度(Mohsl hardness)排序。硬度值低者硬度较小,反之硬度较大。物料按硬度一般可分为三类:硬度值1~3的称为软质物料;硬度值4~7的称为中等硬质物料;而硬度值8~10的称为硬质物料。
表1-1 几种物质的莫氏硬度值

在硬质物料的粉碎中,设备需采取较低的转速及压力润滑,对轴承等部件应采用防尘措施,以防所产生的粉尘落入。
(二)脆性与韧性
脆性与韧性都是固体承受外力的能力指标。脆性是指固体在外力作用下(如拉伸、冲击等)破坏断裂,而之前不发生变形或仅发生微小变形的性质。物质的脆性越大,承受冲击的能力越差,越易于粉碎。脆性较大的物质通常称为脆性物质。韧性是指固体承载冲击的能力。物质的韧性越大,承受冲击的能力越强,粉碎中越不易发生断裂,即越不易粉碎。韧性较大的物质通常称为韧性物质。
固体材料承受外力拉伸时,如将内部单位面积所受的力定义为应力σ(N/m2)、尺寸增量与原尺寸之比定义为应变ε(m/m),则在整个拉伸过程中,σ与ε的关系将如图1-1所示。

图1-1 固体应力与应变的关系
图中OA线段显示出σ与ε呈直线关系,说明在此过程中,物体受力后的变形与所受的外力成正比,即
σ=Eε (1-1)
式(1-1)即虎克定律。其中E为OA线的斜率,称为弹性模量,单位N/m2。弹性模量越大,材料越硬,反之则越软。如图1-1所示,σ变化时,ε循线段OA往返,说明外力去除后物体能够恢复到原来形状,这种变形现象称为弹性变形,线段OA也称为弹性段。
AY和YB两线段分别称为屈服段和强化段,在这两条线段间,外力去除后,物体会产生永久变形而不能恢复原来形状,这种变形现象称为塑性变形。σ-ε线下的面积越大,物料韧性也越大。反之物料韧性则越小。
当材料受力变形达到B点后,就会发生断裂破坏。所以B点之后也称为破坏段。
二、固体粒子的几何特性
(一)粒径的表示
通常情况下,粉体粒子的形态各不相同,也不规则。从不同方向上看,长度不同,大小也不一样。最简单的粒子形状是球形,几何对称、任何方向表现出的形状相同,其大小可直接以直径表示。但对形状不规则粒子,其粒径的定义也不一样。
若在粒子的平面投影外缘作两条平行线,则平行线的间距b称为短轴径;与短轴径相垂直的外缘两平行线间距l则称为长轴径,如图1-2所示,而与该投影面垂直方向的最大高度定义为h;再如该粒子的投影面积为f、粒子体积为V、则粒径的定义及表达式如表1-2所列。

图1-2 短轴径与长轴径
表1-2 固体粒子粒径的名称及表达式

1.大量粒子的粒径
粒径通常采用以下表示方式:
①定方向粒径 以任意定方向外接平行线间的距离表示,如图1-3(a)所示;
②定方向等分面积粒径 以任意定方向分割投影面积为二等分的直线长度表示,如图1-3(b)所示。

图1-3 定方向及定方向等分面积粒径
2.其他方式表达的粒径
依据测定方法的不同,还常使用下列定义的粒径:
①筛分粒径 又称细孔通过相当径,当粒子通过粗筛网且被截留在细筛网时,粗细筛孔直径的算术或几何平均值称为筛分粒径。
②Stokes直径 若所测物料粒子与密度相同的球形物料粒子在同一流体中的沉降速度相等,则该球形粒子的直径称为物料的Stokes直径。
③比表面积直径 单位体积粒子所具有的表面积称为粒子的比表面积,与所测物料粒子具有相同比表面积的球形粒径称为物料的比表面积直径。
(二)粒径的测定
测定粒径的方法有很多,但每种方法都只适用于一定的粒径范围,以下介绍几种常见方法。
1.筛分法(>50μm)
将待筛分的固体粒子置于一套标准筛的最上层进行筛分,然后分别称取停留在每个筛网的粒子质量,并通过各筛的孔径计算其平均粒径。
筛的规格目前多用泰勒制,以每25.4mm(1in)筛网长度上的孔数作为各号筛的名称,并简称为“目”。
我国筛的规格与泰勒制相近,见表1-3。
表1-3 标准筛目数对照

注:m—目(mesh),每25.4mm(1in)筛网长度上的孔数;a—筛孔实际尺寸(直径或方孔边长),μm。
筛号的选择由基筛和筛比所定。基筛是作为基准的筛,筛比是相邻两筛的筛孔实际尺寸之比。按筛孔由大到小,从上到下排列起来,各个筛子所处的层位次序叫筛序。常用的筛比是21/2,称为基本筛序;另一个筛比是21/4,称为附加筛序,在要求筛分粒级较窄时插入基本筛序中使用。
常用标准筛的筛框直径为200mm,高度为50mm,排序由上往下筛孔依次减小。筛分时可用人工或机械颠动。
筛分后,对筛孔实际尺寸为ai的筛来说,如停留粒子占式样质量的百分数为xi,而位于其上方的筛孔为ai+1,则粒子的平均粒径di按下式计算:
(1-2)
通过筛分可做出粒径分布图,并可计算试样的平均粒径。平均粒径的表达方式有两种,一种为调和平均粒径,计算公式为
(1-3)
式中,n——标准筛的总数。
另一种为算术平均粒径,计算公式为
(1-4)
2.显微分析法(1~100μm)
如将固体粉末以液体分散剂固定于玻片上,通过显微镜目测或显微照相,便可得到粒子形状及各方向上之长度。若采用电子显微镜,最小粒径可观测到0.001μm。
设d1,d2,…,dm为各粒级的平均粒径;N1,N2,…,Nm为各粒级的粒子数;ρ为粉末的密度,则各粒级的粒子质量分数为
同理
依此类推。根据式(1-4)可求平均粒径为
3.沉降法(>1μm)
利用粒子在流体中的沉降速度随其粒径的增大而增加的原理来测得粒径的方法为沉降法。其取样方法有以下两种:
①吸管法,即在沉降的悬浮液中某固定高度位置上定时间吸取试样,每个试样均为有代表性的悬浮液样品。
②沉降天平法,粒子沉降在一个浸沉在液体中并可连续称重的天平盘上,将不同时间的沉降质量连续记录,即可得出粒子的粒度及质量分布。
沉降分析法试样的浓度必须足够低,以消除粒子间的相互干扰。此外,液体温度必须均匀(±0.1K左右)以防止液体对流。由于粒径越小粒子的布朗运动越明显,所以沉降法测定的粒径有一定下限。如果采用离心沉降法测量粒径,则最小可测到0.05μm的粒径。
沉降法所测的粒子粒径可由Stokes定律计算:
(1-5)
式中,H——沉降距离,m;μ——液体黏度,Pa·s;ρs,ρ——固体及液体的密度,kg/m3;τ——沉降时间,s。
离心沉降法测定粒径的计算式同式(1-5)。此时重力加速度g需以离心加速度ω2 r代替。其中,ω为转盘的角速度,r为转盘中心至粒子的距离。
4. Coulter计数器法
将粒子悬浮于电解质溶液中并通过一个小孔,连续测量小孔外侧两个电极的电压,因电阻受粒子的影响,故电压值的大小是粒径的函数,通过观察所测电压的变化可知通过小孔粒子的数目及粒径。
5. 光散射法(0.5~50μm)
粒子将入射光以直角散射,所散射的入射光分率与粒子的浓度及其直径的三次方成正比,与入射光波长的四次方成反比。
6.透过法(>1μm)
气体低速通过粒子床时,其流速分别与压降及与粒子比表面积成平方关系的比例常数成正比。依此可求得与粒子具有相同比表面积球体的直径。本法测量的精确性与粒子试样的装量有关。
(三)粒径分布
以粒径d为横坐标,以小于粒径d的粒子质量占总质量的百分数f(d)为纵坐标,可得如图1-4(a)所示的粒径累积质量分数曲线。

图1-4 粒径累积质量分数、粒径频率曲线
d-f(d)曲线是粒子累积质量分数关于粒径的函数,f(d)的取值范围在0~1之间。
若以粒径的累积质量分数曲线的斜率为纵坐标,以粒径d为横坐标,可得如图1-4(b)所示的粒径频率曲线(即导函数曲线)。
如果在d0处的粒子质量最多,此处粒子的质量累增量也最大,d-f(d)曲线在此处出现拐点,对应的d-f'(d)曲线在此将出现峰值。
如以大于粒径d的粒子质量占总质量的百分数f(d')为纵坐标的话,则上述两曲线的形状分别会发生如图1-5(a)、(b)所示的变化。

图1-5 以粒径大于d粒子为准的累积质量分数、粒径频率曲线
显然有f(d)=1-f(d'),f'(d)=-f'(d')。
由粒径频率曲线可看出粒径分布情况,同一粒子的分布曲线通常有一个峰值。对粒子的混合物,可能出现与混合物中组分相同数目的峰值。此外,经粉碎的固体粒子其粒径分布曲线因受物料特性及设备特性的影响,可能会有两个或更多峰值。
三、固体粒子的力学性能
(一)附聚作用
附聚作用使得粒子相互黏附成团簇,对固体的流动性及操作带来很大影响。其机制如下:
①机械的联锁作用 特别容易发生于细长形的固体颗粒,使得大量粒子相互联锁。
②表面引力 在粒子非常细小(<10μm)、单位体积表面很大的情况下,包括范德华力在内的表面力使粒子间产生很大的引力。一般说来,粉碎后新生成表面的引力较大。
③塑性熔接 不规则形状粒子间接触点的面积非常小,单位面积上受到的力就很大。在很高的压力下固体发生熔接。
④静电吸引 在粒子加入设备时可产生静电,粒子表面积累了大量的正负电荷,且颗粒的形状极不规则,这样造成了电荷的聚集。颗粒表现出强烈的表面效应,很容易发生聚集而达到稳定状态。
⑤湿度影响 湿度引起表面张力的变化或是少量固体溶解随后蒸发而起到结合剂的作用。
⑥温度影响 温度波动可引起粒子结构的改变,并引起结合力增大。
(二)摩擦系数
1.剪应力
粒子间发生相对运动时会受到相互间的剪切力。
力学上把物体单位面积所受的剪切力称为剪(切)应力,以反映物体承受剪切力时内部的受力集度。剪应力的测定如图1-6所示。

图1-6 剪应力的测定
粒子充填于两节圆柱形浅箱中,对垂直于剪切面的料面施以一定的垂直压力,再将上箱缓慢地水平拉出。物料被剪断时所受到的拉力即为该粒子的剪切力,而该力与受力面积之比即为剪应力。剪应力随粒子堆积密度的增大而增大。
设剪切面上的剪应力为τ(N/m2)、与之垂直的法向应力为σ(N/m2),则τ与σ之间存在着Coulomb定律:
τ=Kσ+C (1-6)
式中,K——摩擦系数;C——粒子间的附聚力,N/m2。
两者均为表示粉体层状态的参数。
2.休止角
通过小孔由上部将粒子堆积到平面上,大致形成一个圆锥体,圆锥的斜边与水平线的夹角称为动态休止角。实际所形成料堆的斜面并不太规则,无法形成精确的圆锥形。粒径较大的粒子可能由顶部滚落到底部,故料堆顶部的角度较大而底部的角度较小。
休止角的测量也可通过使黏附一层粒子的平板倾斜,然后往平板上加粒子,直到粒子滑落,此时滑动的角度名为静态休止角。
休止角大致在20°~60°左右。易流动固体其值较小、难流动固体其值较大。对附聚作用很强的固体在极端情况下休止角可接近90°。
休止角较低的粒子有助于装填,几乎立即可得到高装填密度的物料。休止角很大的粒子装填时内部结构较松,振动后才可密实。
3.摩擦角
如图1-7所示,将粒子充填在壁面光滑的二维床(即粒子床为扁平形)中,使粒子由底面中心缝隙流出,而留下外侧静止的物料。

图1-7 摩擦角
物料中间会形成倒锥形的中空,锥体的底角即静止物料斜面与水平面的夹角α称为摩擦角。摩擦角对料斗的设计很重要。如测量料仓中料堆对地面随高度的压力变化,会发现压力大致随高度呈直线增加,到达某一个临界点以后压力成定值。典型曲线如图1-8所示。曲线的不连续点为
式中,Lc——料层临界高度,m;dL——料罐宽度,m。

图1-8 粒子对粒柱底部的压力
对于超出Lc的粒子,其重量由同料斗壁面产生的摩擦力支撑。由此可见,料斗的设计必须考虑能够承受住固体作用于壁面的压力。
4. 壁面摩擦系数
粒子与壁面、粒子与粒子间摩擦系数的测量方法相同,只需以固体平面代替下层静止粒子箱即可实现。
此法所测得的是静摩擦系数,即粒子与固体间将发生剪断时的值。粒子处于流动场合时,摩擦状态与此不同。动摩擦系数一般小于静摩擦系数。
(三)固体粒子的流动性
料斗内的物料在理想情况是呈活塞状出料,所有粒子的停留时间均相同。
而由料斗锥形底通过出料口向外出料时,通常很难得到均匀的出料速率,因固体粒子可产生架桥现象,有时在料斗内形成拱状。此外,还会经常遇到料斗中心物料卸出而周壁物料滞留的现象。其结果造成部分粒子在料斗内停留时间过长。
一般来说,粒子在细高料斗中比短粗料斗中的流动性要好,故多采用小锥角的长锥形底的料斗。光滑的壁面可改善料斗的出料特性。
固体粒子的出料速率除了受料斗底部出料口尺寸的影响以外,还与出料口附近粒子膨胀能力有关,只有上部物料压向粒子的力超过出料口附近粒子所能承受的剪切力时才有可能出料。
料层深度超过料斗出口直径4倍以上时,固体的出料速率与料斗中的料层深度无关。出料速率正比于出料口的有效直径,成2.5次方的关系。有效直径是开孔的实际直径减去1~1.5倍的粒子直径。
由Brown提出的粒子小孔流出速率公式如下
(1-7)
式中,w——粒子的质量流速,kg/s;ρs——固体粒子的密度,kg/m3;Deff——开口的有效直径,m;g——重力加速度,m/s2;β——锥形与水平线所夹的锐角,(°)。
在出料口下连接一段与料口直径相同的卸料管可增加粒子的出料速率,对细粉效果更好。如管长与管径之比为50时,粗砂的出料速率可增加15%,而细砂可增加50%。增加细粉出料速率的另一方法是用压缩空气使出料口附近的粒子发生流态化。