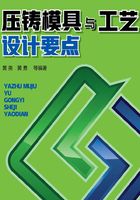
2.3 压铸件结构设计的要点
2.3.1 简化模具结构
①压铸件的分型面上,应尽量避免圆角。图2-9(a)中的圆角不仅增加了模具的加工难度,还降低圆角处的模具强度和寿命。若动模与定模稍有错位,压铸件圆角部分易形成台阶,影响外观。若将结构改为如图2-9(b)所示的结构,则分型面平整,加工简便,避免了上述缺点。

图2-9 避免在分型面上有圆角
②避免模具局部过薄。图2-10(a)所示的盒形件,因侧面有孔而增设的活动型芯,使压铸模的局部厚度过薄,使用时易变形和损坏。如将压铸件侧向的孔向下延伸为如图2-10(b)所示的结构,则可省去活动型芯,并且也消除了模具上的薄弱部分,有利于延长模具的使用寿命。

图2-10 改善结构,便于模具制造
图2-11(a)所示的压铸件,因孔边离凸缘距离过小,易使模具镶块断裂。若将压铸件改为如图2-11(b)所示的a≥3mm的结构,则使镶块具有足够的强度,延长了模具的使用寿命。

图2-11 改善结构,使镶块具有足够强度
③避免在压铸件上设计互相交叉的盲孔。交叉的盲孔必须使用公差配合较高的互相交叉的型芯[图2-12(a)],这既增加了模具的加工量,又要求严格控制抽芯的次序。一旦金属液窜入型芯交叉的间隙中,便会使型芯发生困难。若将交叉的盲孔改为如图2-12(b)所示的结构,即可避免型芯交叉,消除了上述的缺点。

图2-12 压铸件应避免有相互交叉的盲孔
④消除内侧凹,降低生产成本。图2-13(a)所示的压铸件内法兰和轴承孔为内侧凹,抽芯困难,或需设置复杂的抽芯机构,或需设置可溶型芯。这既增加了模具的加工量,又降低了生产率。若将压铸件改为如图2-13(b)所示的消除内侧凹入的结构,即可简化模具,克服了如图2-13(a)所示压铸件带来的缺点。

图2-13 内侧凹结构及消除图
同样,如图2-14(a)所示的压铸件,由于矩形孔尺寸B<A,抽芯困难,结构复杂。若压铸件按图2-14(b)所示进行改进,取矩形孔尺寸B≥A+0.2mm,模具就简化了,无需另设抽芯机构,延长了模具使用寿命。

图2-14 矩形孔尺寸与轴芯
2.3.2 减少抽芯部位
减少不与分型面垂直的抽芯部位,对降低模具的复杂程度和保证压铸件的精度是有好处的。图2-15(a)所示压铸件侧面有三个侧孔,需另设抽芯方向不与分型面垂直的抽芯机构。如图2-15(b)所示,改变三个侧孔结构,使侧孔与大型芯出模方向一致,即与分型面垂直,则不需要另设抽芯机构就可压铸成型。显然,后一种结构省去了抽芯机构,模具得到了简化。

图2-15 侧孔结构与抽芯
图2-16(a)所示压铸件,中心方孔深度深,抽芯距离长,需设专用抽芯机构,模具复杂;加上悬臂式型芯伸入型腔,易变形,难以控制侧壁壁厚均匀。而采用如图2-16(b)所示的H形断面结构后则无需抽芯,简化了模具结构。

图2-16 支撑部位形状与抽芯
图2-17(a)所示压铸件侧壁四孔需设抽芯机构,若按图2-17(b)进行改进,将侧壁圆孔改为与压铸件出模方向一致的U形凹槽后,即可省掉抽芯机构。

图2-17 孔的形状与抽芯
2.3.3 有利于压铸件脱模和抽芯
图2-18(a)所示压铸件,因K处的型芯受凸台阻碍,无法抽芯。若将压铸件的形状做一定修改,变为图2-18(b)所示的结构,K处的型芯即可顺利抽出。

图2-18 压铸件形状与抽芯
图2-19(a)所示水龙头压铸件,因有内侧凹A和B,平直段C以及圆弧R的中心线距离压铸件外廓太近,无法抽芯。可按图2-19(b)所示对压铸件结构进行改进,消除内侧凹,增大圆弧R,使弧状型芯的回转中心处有足够强度,并使弧状型芯退出时在其背后有足够空间,方便了脱模和抽芯。

图2-19 压铸件结构与抽芯
2.3.4 防止变形
图2-20(a)为平板上有不连续的侧壁的压铸件,因温差引起的收缩,截面削弱部位会发生变形,若在削弱部位的两侧面增加加强肋[图2-20(b)],或选择图2-20(c)所示的结构(但侧面需设置抽芯机构),或采用降低开口部位的高度,并增添两条横跨平板的加强肋的结构[图2-20(d)],均可提高开口部位的刚度,防止压铸件变形。

图2-20 压铸件结构与变形
图2-21为用弯曲壁补偿和降低残余应力,防止压铸件变形和裂纹的例子。盒形件内部的直壁J[图2-21(a)],常因承受过大的应力而产生裂纹;若将直壁改成弯曲壁[图2-21(b)]后,弯曲壁能起到补偿作用,防止压铸件变形。

图2-21 防止压铸件变形的结构