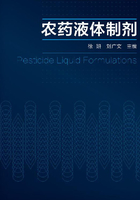
第四节 微乳剂的生产
一、微乳剂的加工工艺
微乳剂加工工艺流程见图1-10。

图1-10 农药微乳剂加工工艺流程图
1,5—均质混合机;2—输送泵;3—溶剂计量槽;4—水计量槽;
6—成品贮罐;7—管道过滤器;8—电子秤
二、微乳剂的加工设备
微乳剂的几种配制方法在加工工艺上都属于分散、混合等物理过程,因此工艺比较简单。分散、混合效果除取决于配方中乳化剂的种类和用量外,工艺上所选取的调制设备、搅拌器形式、搅拌速度、时间、温度等也有一定关系。微乳剂加工主要设备为调制釜,一般来说,当配方合适时,生产乳油的搅拌釜也适用于配制微乳剂,因此可以直接使用乳油的生产线生产,将所有组分按流程投入釜中搅拌成透明制剂即可。均质混合机是比较理想的选择,在剪切机外力的作用下形成微乳液的效果好、制剂稳定、生产周期短,可适用于各种工艺的微乳剂制备。
1. 搅拌釜
搅拌釜是最常用的液体非均匀介质混合与乳化设备,主要由搅拌装置、搅拌容器、轴封三大部分构成。搅拌装置包括传动装置、搅拌轴和搅拌器等。轴封是搅拌轴及搅拌容器转轴处的密封装置。搅拌容器包括罐体、换热元件及内构件等。罐体大多数设计成圆柱形,其顶部结构可设计成开放式或密闭式,底部大多数呈蝶形或半球形。由于平底结构容易造成搅拌时液流死角,影响搅拌效果,一般不采用平底结构。在容器中装有搅拌轴,轴一般由容器上方支承,并由电动机及传动装置带动旋转,轴的下端装有各种形状桨叶的搅拌器。搅拌釜通常还设有进出口管路、夹套、温度计插套以及挡板等附件。搅拌器是搅拌设备的主要工作部件,提供搅拌过程所需要的能量和适宜的流动状态,以达到搅拌过程的目的。搅拌釜中应用最广泛的搅拌器有桨式、推进式、涡轮式和锚式等,根据搅拌目的、物料的黏度、容器的大小等进行选择。
2. 剪切式均质机
(1)结构及工作原理。剪切式均质设备基本上采用定-转子型(stator-rotor)结构作为均质头,定子和转子之间的间隙非常小(一般有0.1mm、0.2mm或0.4mm),在电机的高速驱动下(300~10000r/min,有的可高达15000r/min),由于转子高速旋转所产生的高切线速度和高频机械效应带来的强劲动能,物料在转子与定子之间的间隙内高速运动,形成强烈的液力剪切和湍流,使物料在同时产生的离心、挤压、碰撞等综合作用力的协调作用下,得到充分分散、乳化、破碎,达到要求的效果。
(2)分类。按照剪切方式可分为轴流式、径流式。
① 轴流式:转子由类似涡轮的结构组成,定子则沿轴向开有大小不同的孔,由于转子的高速旋转,在均质头的上下部位形成压力差,流体从底部或顶部被不断地吸入,经过定子、转子之间的间隙,流至定子流道,并以极大的动能冲向上部折流板或容器底,流体被折流回,在均质头内部受到高速旋转的转子与定子的强烈剪切作用,使料液在极短时间内达到微粒化和均质化的要求,见图1-11。

图1-11 轴流式剪切机流型图
② 径流式:转子的开孔可根据物料的性质而定,长孔适合中等固体颗粒的迅速粉碎 及中等黏度的液体的混合,小圆孔适用于一般的混合和大颗粒的粉碎,可处理较高黏度的物料。见图1-12。

图1-12 径流式剪切机流型图
(3)均质机理。物料(液体物料)分散系中分散相颗粒或液滴破碎的直接原因是受到剪切力和压力(黏性力和惯性力)的作用。引起剪切力和压力作用的剪切力和压力在不同的均质设备中有差别,能引起剪切力和压力作用的具体流体力学效应主要有层流效应、湍流效应和空穴效应。层流(laminar flow)效应会引起分散相颗粒或液滴受到剪切和拉长;湍流(turbulent flow)效应是在压力波动作用下引起分散相颗粒或液滴的随意变形;气穴(air pocket)效应是形成的小气泡受到破碎产生冲击波,引起剧烈搅动。
三、微乳剂生产常见问题
1. 透明温度范围窄
一般农药微乳剂用非离子型表面活性剂配制,在水溶液中存在着表面活性剂对温度比较敏感的浊点问题,即透明温度上限;对有些不溶于常规有机溶剂的有效成分,则存在着低温稳定性问题,即透明温度下限。关键在于表面活性剂及助表面活性剂、溶剂等的优选和用量的确定。
① 透明温区是微乳剂研究的主要内容,除了靠表面活性剂调节外,助表面活性剂、溶剂及调节剂等的筛选也非常重要,筛选不当,适应范围窄,原药、表面活性剂等各种原材料的质量或用量出现小的变化会引起产品质量不稳定;
② 水质变化:如果用的是去离子水配制微乳剂,水处理装置出现异常,硬度变大,水中的Ca2+、Mg2+会破坏非离子表面活性剂的亲水亲油平衡,引起微乳剂浊点的降低,从而导致微乳剂透明温度范围变窄。
2. 微乳剂或稀释后的乳液出现结晶不稳定现象
农药微乳剂应可以以任何比例对水稀释,大多数农药品种的微乳剂乳液都非常稳定,但对一些有效成分理化性质较特殊者,稀释后乳液不稳定问题比较突出,一般来说,一定温度下,溶解度越小,越容易析出晶体。乳液不稳定,即微乳油珠在稀释后的微乳液中很快破乳,析出晶体或油层,乳液变浑浊或出现悬浮物。在田间使用过程中,微乳剂乳液不稳定会严重影响药液在靶标上的沉积和黏着,析出的结晶甚至可能堵塞喷头,进而影响药效或产生药害。可从以下方面考虑:
① 溶剂与助表面活性剂的选择,溶剂的选择至关重要,越接近原药起始饱和溶解度的配方,越容易析出晶体。外界温度等环境变化,或者稀释后水溶性表面活性剂会逐渐分散于水相中,当体系的载药量超过当时的溶解度时,就会析出晶体。如使用甲醇作助表面活性剂时,虽然能增加溶解度或者增加透明度,但当微乳剂稀释时,会使液滴的界面膜变薄,易于使液滴聚集变大,粒径增大,分布不均匀,促使农药活性成分很快析出晶体。
② 表面活性剂及用量,不同的农药活性成分需要用不同种类的表面活性剂搭配使用,选择不同的表面活性剂,其外观、乳化效果等差异较大,在选择表面活性剂时,应考虑单体的结构、亲水基与亲油基的比例、与农药及溶剂的配伍性、表面活性剂自身的配伍性等。如亲水性大的体系,用水稀释后,亲水基与水接触,微观结构发生变化,无法增溶原增溶量的药物,析出晶体。选择有合适增溶量,又有合适HLB值的表面活性剂非常重要。
③ 添加结晶抑制剂,如特殊的水溶性聚合物,可以使农药溶液达到过饱和状态,抑制晶体析出,这种过饱和状态也是热力学不稳定体系,随着水的稀释最终仍会析出晶体,但它会延迟有效成分的析晶过程,防止农药使用过程中出现沉淀。
3. 生产包装过程中出现混浊、结晶等现象的原因
① 原材料(原药、水等)中机械杂质较多。
② 原药本身的溶解性不好,溶剂溶解后混浊。
③ 操作不当等造成原药在油相中未完全溶解,尤其是溶解性较差的尼索朗、氟虫腈等,原药未完全溶解就与水相混合,很难将原药完全溶解,产品透明度略差,静置一段时间底部出现白色沉淀,碰到这种问题一般可以通过加热来解决。
④ 北方寒冷天气下生产,气温变化导致溶解度、增溶量变化,导致微乳化困难,需控制生产温度或调整溶剂、助剂进行解决。
4. 经时稳定性不好
微乳剂生产出来检测合格,并在1~2个月内无变化,但经过一定时间的贮存,出现混浊、分层、沉淀、结晶、析油现象,且为不可逆,说明体系稳定性随时间延长发生了变化,此变化极大影响制剂的使用和商品性。原因可能有以下几个方面:
① 表面活性剂选择不当,体系未达到真正的微乳状态。
② 已微乳化的粒子受环境及外界条件影响而聚结沉淀。
③ 由于包装不严或包装与溶剂不匹配,水分及溶剂蒸发,破坏了体系平衡。
5. 产品褪色问题
部分加入警戒色的产品出现褪色或颜色不均一的问题。如2.5%高效氯氟氰菊酯微乳剂、4.5%高效氯氰菊酯微乳剂,现在很多生产厂家加入着色剂,并且采用透明瓶包装,不同包装之间有时能非常明显地看到颜色差异,原因可能有以下几个方面:
① 染料质量不佳,经时褪色。
② 染料会发生光氧化反应,选择耐光牢度好的染料。
③ 染料与溶剂、助剂等不匹配。
6. 安全性问题
乳油中一般含有大量有机溶剂,往往对幼嫩的花果有加重药害的作用;微乳剂中含有大量水,对植株的药害较同样有效成分的乳油轻一些,但微乳剂中一般使用大量表面活性剂,其表面张力较小,具有较好的渗透性,在某些作物、果树的敏感期也有可能会产生药害。
7. 为什么有时候微乳剂药效比普通的乳油差
一般来说,因为微乳剂中有效成分粒子在水中最小,而且其中助剂的用量远高于水乳剂和乳油,有利于发挥药效和增强对有害生物靶标表面的渗透,室内毒力测定较高,药效一般较好。应用于田间,效果可能就不一样了,原因可能有以下两方面:
① 产品质量达不到要求,甚至出现沉淀、结晶等问题,难以保证药效。
② 使用的技术问题,我国传统的常规喷雾方法一般是要喷湿植株全株,直到雾滴滴下为止,而微乳剂含有比乳油更多的表面活性剂,润湿性更好,对于难湿润的植物叶片,较低的表面张力,可以增加药液的持留量;而对于易湿润的植物叶片,降低表面张力,反而增加了药液的流失,减少了持留量,达不到有效的药剂沉积,从而使得药效比不上乳油。
8. 为什么微乳体系多为四元以上体系
① 用离子表面活性剂时,通常要加入助表面活性剂。
② 可能采用复配表面活性剂,因其性能一般优于单一表面活性剂。
③ 水相中可能存在电解质。