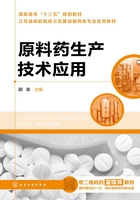
任务三 探索对乙酰氨基酚的反应原理
一、合成路线分析
对乙酰氨基酚自1893年上市以来,逐渐取代非那西丁和乙酰苯胺,现已成为全球应用最为广泛的解热镇痛药物。对乙酰氨基酚的合成有多条路线,但无论使用哪条合成路线制备对乙酰氨基酚,最后一步对氨基苯酚的乙酰化是相同的。
1.以对硝基苯酚钠为原料的合成路线
对硝基苯酚钠是药物、染料及农药的中间体,产量大,成本低,广泛应用于工业生产。以对硝基苯酚钠为原料的工艺路线较为成熟,是以氯苯为起始原料经硝化制得对硝基氯苯,再用碱水解,制得对硝基苯酚钠。对硝基苯酚钠经酸化、铁粉还原、乙酰化反应制得对乙酰氨基酚。

以对硝基苯酚钠为原料的合成路线较为简捷,适用于规模生产。但原料供应容易受染料及农药生产的制约;制备过程中中间体对硝基氯苯毒性大;用铁粉还原后,会产生大量的铁泥和废水,给“三废”防治和处理带来巨大的困难。
2.以苯酚为原料的合成路线
(1)苯酚亚硝化法 较低温度下(0~5℃),向含有苯酚与亚硝酸钠的反应釜中加入硫酸,生成对亚硝基苯酚。用硫化钠还原对亚硝基苯酚即可制得对氨基苯酚。

该路线较为成熟,有一定的实用价值,对氨基苯酚的收率为80%~85%。缺点是使用的还原剂硫化钠成本高,污染较大。
(2)苯酚硝化法 苯酚的硝化反应温度一般控制在0~5℃,硝化反应产物是对硝基苯酚,还原即可制得对氨基苯酚。硝化反应过程中有二氧化氮放出,因此要求有废气吸收装置,设备也需耐酸。
由对硝基苯酚制备对氨基苯酚,主要有三种方法:铁粉还原法、加氢还原法与苯酚偶合法。
①铁粉还原法。铁粉还原法适用范围较广,许多胺类可以由相应的硝基化合物以铁粉在电解质(NH4Cl等)的存在下还原制得。此法同样可用于对氨基苯酚的制备。

但由于制得的成品质量较差,加之在生产过程中有大量的含胺铁泥和废水,会对环境造成严重影响,因此现已被加氢法取代。目前生产上基本不用此法。
②加氢还原法。工业生产中实现加氢有两种不同的工艺,即气相加氢法与液相加氢法。气相加氢法仅适用于沸点较低、容易汽化的硝基化合物的还原;液相加氢法则不受硝基化合物沸点的限制,因此适用范围更广。常用的溶剂包括水、甲醇、乙醇、乙酸、乙酸乙酯、环己烷、四氢呋喃等。选用溶剂时,沸点应高于反应温度并对产物有较大的溶解度,以利于产物从催化剂表面解吸,使活性中心再度发挥催化作用。催化剂一般采用骨架镍、Pd/C、Pt/C、Lindlar催化剂等。为了缩短反应时间,回收催化剂,提高产品质量,可添加一种不溶于水的惰性溶剂,例如甲苯,反应结束后产品在水层中,催化剂留在甲苯层中。

催化加氢反应可在常压或低压下进行,加氢压力一般在0.5MPa以下,反应温度在60~100℃之间,产率在90%以上。加氢还原法的优点是产品质量好、收率高、“三废”少。
③苯酚偶合法。低温下(0~5℃)苯胺、亚硝酸钠、盐酸反应生成重氮盐。苯胺重氮盐与苯酚偶合生成偶氮化合物。偶氮化合物再经还原可得对氨基苯酚和苯胺。还原偶氮化合物也有多种方法,包括化学还原法、电解还原法和催化加氢还原法等。

3.以硝基苯为原料的路线
硝基苯是一种价格低廉、易获取的化工原料,经还原后可直接制得中间体对氨基苯酚。还原方法包括铝粉还原法、电化学还原法或催化氢化法等。
(1)铝粉还原法 铝粉还原法工艺路线短,硝基苯在酸性介质中经铝粉还原得中间产物苯基羟胺。无需分离经Bamberger重排制得对氨基苯酚,副产物氢氧化铝可通过加热过滤回收。该方法的缺点是需要大量铝粉。

(2)电解还原法 本法由硝基苯经电解还原制得中间体苯基羟胺,再重排制得对氨基苯酚。电解还原法一般采用铝为阳极,铜为阴极,硫酸为阳极电解液。早在1979年,Harting Chemicals公司就曾建立电解还原法生产对氨基苯酚的装置。但是电解还原法在工业生产中的应用并不多,大多局限于实验室及中型规模生产。其主要原因是电解设备要求较高,且需要丰富的电力资源作为支撑。电解还原法的优点是收率较高,副产物较少。不考虑成本因素且电力资源较为充沛的情况下,采用电解还原法进行生产是可行的。

(3)加氢还原法 加氢还原法同样是一步制得对氨基苯酚。在酸性介质中,硝基苯在催化剂的作用下加氢生成苯基羟胺,再通过重排即可制得对氨基苯酚。但是在酸性介质中,苯基羟胺能够继续发生加氢反应生成副产物苯胺。这也是该方法的主要副反应,其副产物的生成量约为10%~15%。铁、钴、镍等金属的存在有利于苯基羟胺转化成苯胺,而铝、硼、硅等元素及其卤化物可使硝基苯加速转化成对氨基苯酚,并使苯基羟胺生成苯胺的副反应减少至最小程度。生成的苯胺等副产物可加少量氯仿、氯乙烷除去。

目前,生产上一般以活性炭为载体,以贵金属为催化剂,如钯、铂、铑等,反应可在常压或低压下进行。如果使用活性低的催化剂,则要求反应压力为5~10MPa甚至更高。
在反应条件方面,原料硝基苯应当分批缓慢加入,这样有助于缩短反应时间。如果将原料硝基苯一次性加入,反应时间则需要延长1倍以上。反应温度一般控制在80~90℃,氢气压力较低,仅为0.1~0.2MPa。
此外,添加表面活性剂有利于加快反应速率,提高收率。一般使用在硫酸中稳定且溶于水的季铵盐。在反应物料中加入一些不溶于水的有机溶剂也有利于提高对氨基苯酚的产率和质量。