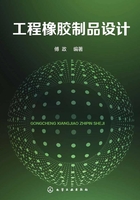
1.3 强度性能破坏
橡胶材料强度的测试一般是拉伸强度或撕裂强度等标准测试,而橡胶制品多数是在长期加载的复杂环境下产生了强度性能的破坏,这类标准测试只是材料的质量控制测试,难以作为预测制品破坏行为的参数。断裂力学认为,裂纹的存在与裂纹扩展特性决定了强度性能的破坏。
1.3.1 断裂能
裂纹扩展实质上是不断产生新的自由表面积的过程,其裂纹端部必定消耗相当的能量,消耗能量的多少与材料的性质、裂纹端部的应变和裂纹扩展的速率等因素有关。在热力学系统中,当裂纹开始扩展时,外力做功的增量dU,一方面使系统内势能(可逆弹性能)增加dUe,另一方面使裂纹扩展而消耗,故可导出断裂参数(G):
(1-11)
式中,B是试样厚度;C是裂纹长度。
参数G是裂纹扩展形成单位新面积时消耗能量的临界值,包括键断裂和黏弹损失消耗的能量,故称为断裂能,而橡胶文献中一般称为撕裂能,是材料抵抗裂纹扩展能力的量度。G值越高表明裂纹扩展的阻力越大,断裂强度越高。对于橡胶材料:
G=G0+Ψ
式中,G0表示本征撕裂能;Ψ是黏弹损耗和塑性形变消耗的能量。
本征撕裂能G0取决于分子链中化学键的强度和硫化胶中交联键的强度。Ψ实质上是与填料、裂纹扩展速率、温度和总应变等因素有关的损耗函数。据报道,纯NR硫化胶的G0值约为58J·m-2,含炭黑的硫化胶的G值可达13000J·m-2左右,说明硫化橡胶的G值很大程度上取决于破坏过程中的损耗函数Ψ值。
为了研究裂纹的扩展特性,实验中一般采用图1-7中的试样,测试材料的撕裂能G值。

图1-7 计算G的试样
(1)条形拉伸试样
G=2kcU0 (1-12)
式中,k为系数,k=3λ-1/2;λ是切口开始扩展时的拉伸比;c为裂纹长度;U0为拉伸区域的应变能密度,可由应力-应变曲线下面积求算。
(2)裤型试样
(1-13)
式中,F为外力;B为试样厚度,B值应小于其宽度值。
(3)纯剪切试样
G=U0h0 (1-14)
式中,h0为初始高度;U0为试样纯剪切区内应变能密度。
应指出,由于G值对试样切口敏感度不同,三种试样的测试结果并非完全一致,存在一定的偏差,其中拉伸试样的切口敏感度较大,应采用同一种试样数据进行分析。
1.3.2 影响断裂能的因素
影响G值的因素颇多,如橡胶种类、填料、老化以及应变形式等。
非结晶型橡胶的G值依赖于撕裂速率和温度,如图1-8所示。非结晶橡胶的强度破坏随着黏弹能量耗散增大而增大。结晶型橡胶在相当宽广的范围内G值对速率和温度的依赖性较小,如图1-9所示,高应变时产生的诱导结晶阻滞了裂纹的扩展。

图1-8 未填充的非结晶性SBR硫化胶的撕裂能

图1-9 未填充的结晶性天然硫化胶的撕裂能
补强类填料可以较大幅度提高G值,主要原因是在裂纹的端部产生钝化效应。这种钝化作用与补强剂的粒径、结构和化学活性有关,粒子越细、结构性和活性越高,G值越高,可理解为在裂纹端部产生了各向异性结构或结晶的缘故。
实验证明,不含防老剂的试样,在真空条件下裂纹扩展所需的G值是空气条件下G值的2倍左右。说明制品使用过程中裂纹的扩展主要是应力活化氧化的过程。
臭氧侵蚀对G值的影响较明显。臭氧极易与双键作用,裂纹扩展可以在G值较低的情况下发生,特别是制品在形变状态下,表面的裂纹密度随应变的增大而增大。实验证实,臭氧浓度约为10-8的条件下,含有抗臭氧剂的样品,其裂纹扩展速率大约为0.1mm/年。
含有骨架材料的制品,在剪切形变或压缩形变下的裂纹扩展特征并不相同。在简单剪切中,裂纹倾向于向界面处扩展,破坏经常发生在界面处或靠近界面处。在压缩形变下,压缩应力可以使裂纹产生闭合作用,裂纹扩展往往出现在制品的边缘。研究发现,剪切或压缩状态下的裂纹扩展速率接近于拉伸状态下的速率,所以后者的数据可供前者参考。
制品若处于膨胀状态时,会产生空化现象,此时制品内部的空洞(孔隙)会突然扩展达到临界状态,并引起断裂破坏。这种现象会在深海油井的钻探中出现,从水平面到海床垂直距离大于500m的钻探为深水钻探,超过500m为超深水钻探,这种环境下与密封制品表面接触的气体在压力下溶解渗透到制品中,当从海床返回时,压力从高压力值突然下降,内部气泡会迅速膨胀发生爆炸性解压断裂破坏。