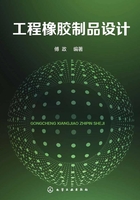
1.6 制品寿命的评估
随着工程技术的不断提高与发展,特别是高新技术的开发应用,对工程橡胶制品的性能要求日趋苛刻,制品服役中的寿命预测评估也日趋重要。制品寿命的预测评估方法包括定性分析预测和定量分析预测。定性分析预测是依据实践和实验以及相关理论进行的寿命评估。定量分析预测主要是依据实验研究寻求制品强度性能、疲劳性能和耐久性能的变化速率,借助物理或数学模型进行辅助分析与计算,得出寿命的预测期望值。一般采用定性与定量相结合进行综合分析的方法对寿命预测评估。大致的程序如下。
① 确定制品的使用性能指标。性能指标(如强度和耐久性)的合理确定,既是保障制品质量的需要,也是制品使用极限的依据。
② 确定制品服役中可能出现的主要破坏过程和破坏程度的限定指标。通过分析制品破坏过程中的性能变化,确定破坏程度的限定指标,例如密封制品不允许渗漏的程度或不合格的裂纹程度;或力学松弛及化学松弛导致的密封力损失等指标。
③ 通过实验设计分析各个破坏过程的特征及性能参数的变化速率。为了对每个破坏过程的特征及其性能变化速率进行单独描述,必须在不同温度和不同时间间隔下进行实验,以测得变化速率,例如强度破坏中的裂纹增长速率、老化过程中的时效硬化、液体环境中的溶胀速率或渗透速率等。在此基础上分析不同过程间的相互作用和影响。实验设计要注意实验条件尽可能接近真实工作条件。若难以达到真实工作条件,可应用橡胶黏弹行为的时-温等效原理,对不同温度或不同频率下测得的数据进行换算。因为温度不变时频率的变化等效于频率不变时温度的某种变化,即改变温度的效应相当于时间(频率)尺度的变化。例如当不能在可能的时间范围内测量出工作温度下的性能速率,可以在升高温度或提高频率的条件下测量其速率。
④ 对各个破坏过程的性能(参数)变化速率综合分析其相互间的作用与影响,评价其对破坏过程的“贡献”大小,在此基础上提出物理或数学模型,并通过实验设计进行验证。
⑤ 在综合定量和定性分析的基础上,结合计算机辅助分析软件(如有限元技术)和制品形状因子的评价,最终实现预测制品在服役中的寿命。
随着设计技术的进步和测试手段的日趋精确与齐全,出现了“智能设计系统”,利用辅助设计软件可以进行产品的设计和仿真实验,预测产品的使用性能及应用效果,对制品的寿命进行评估。