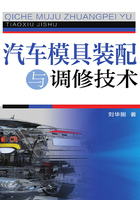
第二节 冲压模具装配
一、装配前模具钳工应做的准备工作
1.读懂装配图
装配钳工必须读懂和熟悉所要装配的模具装配图,因为模具装配图是钳工进行装配工作的主要依据。掌握该模具的结构特点和主要技术要求,了解各零部件的安装部位、功能要求及其在模具中的作用和其加工工艺过程,了解相关零件的连接方式和配合性质,从而确定合理的装配基准、装配方法和装配顺序。
2.清理和检查模具零件
根据模具图零件明细表,清理零件,检查主要工作零件的尺寸和几何精度,查明各部分配合面的间隙以及有无变形和裂纹等缺陷。
3.布置好装配工作场地
将装配工作台案清理干净,并准备好装配时所需的工具、夹具、量具以及一些辅助设备和材料。
4.冲压模具总体装配要求
冲压模具总体装配要求见表1-1。
表1-1 冲压模具总体装配要求

冲压模具的具体装配工艺要求如下:
1)所选用的模架精度等级应满足制件所需的技术要求。例如,上模板的上平面与下模板的下平面一定要保证相互平行,对于冲压制件料厚在0.5mm 以内的冲裁模,长度在 300mm以内时,其平行度误差应不大于 0.06mm;一般冲模长度超过 300mm时,其平行度误差应不大于 0.10mm。
2)模具装配后,上模座沿导柱上下移动时,应平稳且无阻滞现象。导柱与导套的配合精度应符合标准规定的要求,且间隙要均匀。
3)模柄圆柱部分应与上模座上平面垂直,其垂直度误差在全长范围内应不大于0.05mm。浮动模柄凸、凹球面的接触面积应不小于80%。
4)装配后的凸模与凹模的间隙应符合图样要求,且在整个轮廓上间隙应均匀一致,要求所有凸模都垂直于固定板装配基准面。
5)毛坯在冲压时定位应准确、可靠、安全,出件和排料应畅通无阻。
6)应符合装配图上除上述要求以外的其他技术要求。
二、模架的装配
1.模柄的装配
冲裁模采用压入式模柄,如图1-1所示。
模柄与上模座的配合为H7/m6。
2.导柱和导套的装配
冲模的导柱、导套与上、下模座均采用压入式连接,如图1-2所示。

图1-1 模柄的装配和磨平
a)模柄的装配 b)磨平模柄端面
1—模柄 2—上模座 3—等高垫铁 4—骑缝销

图1-2 导柱、导套的装配
a)导柱的装配 b)导套的装配
1—导柱 2—导套 3—上模座4—下模座 5—帽形垫块
导柱、导套与模座的配合分别为H7/r6和R7/r6。
(1)导柱的装配 压入时要注意校正导柱对模座底面的垂直度。导柱装配后的垂直度误差采用比较测量的方法进行检验,如图1-2a所示。
(2)导套的装配 导套的装配如图1-2b所示。将装配好导柱和导套的模座组合在一起,按要求检测被测表面,如图1-3所示。
三、调整冲裁间隙的方法

图1-3 模架平行度的检测
冲模凸、凹模之间的间隙均匀程度,是直接影响冲压件质量和冲模使用寿命的重要因素之一。因此,在制造冲模时,必须保证凸、凹模间隙的大小及均匀一致性。
凸模、凹模间隙要求见表1-2。
表1-2 凸模、凹模间隙要求

工作零件凸模、凹模的装配要求见表1-3。
表1-3 工作零件凸模、凹模的装配要求

在装配冲模时,保证凸模与凹模间隙均匀的方法很多。根据冲模的结构特点、间隙值的大小和装配条件,常采用的方法主要有以下几种。
1.透光法调整间隙
透光调整法的工艺过程如下:
1)分别安装上模或下模,先不要固紧螺钉,且暂不装配销钉。
2)将垫块放在固定板和凹模之间,并用夹钳夹紧。
3)翻转合模后的上、下模,并将模柄夹紧在平口钳上,如图1-4所示。
4)用手灯或手电筒照射(图1-4),并在下模漏料孔中观察。根据透光情况来确定间隙大小和均匀状况。若凸模与凹模之间所透光线在某一方向上偏多,则表明间隙在此方向上偏大,可用锤子敲击相应的侧面,使凸模(上模)向偏大的方向移动,再反复透光观察,直到合适为止。
5)调整合适后,再将螺钉和销钉固紧。
2.垫片法调整间隙
在装配冲模时,利用垫片法控制冲裁模间隙是最简便且常用的方法。其工艺过程如下:
1)分别安装上模与下模,上模的螺钉不要固紧,下模用螺钉及销钉固紧。
2)在凹模刃口四周适当地方,垫入厚薄均匀、厚度等于单边间隙的金属片或纸片2、9,如图1-5所示。

图1-4 透光法调整间隙
1—固定板 2、4—等高垫铁 3—凹模 5—光源 6—凸模

图1-5 垫片法控制间隙
1—凹模 2、9—垫片 3、7—凸模 4—固定板 5、8—等高垫铁 6—导套 10—导柱
3)将上模与下模合模,使凸模进入相应的凹模孔内,并用等高垫铁5、8垫起(图1-5)。
4)观察凸模是否能顺利进入凹模1并与垫片2、9良好地接触。若凸模在某个方向上与垫片的松紧程度相差较大,则表明间隙不均匀。这时,可用锤子轻轻敲打固定板调整到各方向凸模与垫片松紧程度一致为止。
5)调整合适后,再固紧上模。这种方法适用于冲裁材料较厚的大间隙冲裁模,也适用于弯曲模、拉深模、成形模的凸、凹模间隙控制。
3.测量法控制间隙
1)将凹模固紧在下模板上,上模安装后不固紧。
2)使上、下模合模,并使凸模进入凹模孔内。
3)用塞尺在凸、凹模间隙内进行测量。
4)根据测量结果,对间隙进行调整。
5)调整合适后,固紧上模。
4.工艺留量法调整间隙
工艺留量法是将冲裁模装配间隙值以工艺留量的形式留在凸模或凹模上,通过工艺留量来保证间隙均匀的一种方法。具体做法是在装配前先不将凸模(或凹模)刃口尺寸做到所需尺寸,而是留出工艺留量,使凸模与凹模成H7/h6配合。待装配后取下凸模(或凹模),去除工艺留量,以得到应有的间隙。可采用机械加工方法或腐蚀法去除工艺留量。
采用腐蚀法去除工艺留量的腐蚀剂为硝酸20%+醋酸30%+水50%或蒸馏水55%+双氧水25%+草酸18%~19%+硫酸1%~2%(配比为质量分数),腐蚀时应根据留量的大小,注意掌握腐蚀时间的长短,腐蚀后一定要用水清洗干净。
5.镀铜法控制间隙
镀铜法控制凸、凹模间隙,是在凸模刃口部分8~10mm长度上,用电镀法镀上一层厚度等于单边间隙的铜层来保证间隙均匀。装配时,将凸模插入凹模孔内即可。镀层在使用时可自行脱落,装配后可不必去除。
当间隙较大时,不宜采用这种方法,它只适用于间隙较小的冲模。
6.涂层法控制间隙
涂层法控制凸、凹模间隙,是在凸模工作部分涂上一层薄膜材料,使涂层厚度等于凸、凹模单边间隙。涂料一般采用绝缘漆。可用不同黏度的漆或不同的涂抹次数来得到不同的间隙。这种方法操作简便,适合装配小间隙的冲裁模。
无论采用哪种方法来控制凸、凹模间隙,在调整装配后,均须用与冲压件厚度相同的纸片来试冲,根据所切纸片的切口状态、毛刺大小来检验装配间隙的均匀程度,从而确定是否需要调整以及往哪个方向调整。如果切口一致,则说明间隙已调整均匀;如果纸片局部未被切断或产生了很大的毛刺,则表明该处间隙较大,尚需进一步调整。
四、模具零件的紧固
1.机械固定法
凸模(凹模)在固定板上的安装与固定,是冲模装配中的关键工序之一。凸模固定与安装质量的好坏,直接影响冲模的精度和使用寿命。凸模固定在固定板上以后,应满足以下技术要求:
1)凸模(凹模)固定在固定板上,应与固定板型孔装配成H7/m6的配合形式。
2)凸模固定后,凸模的中心轴线一定要垂直于固定板的安装基面,不得歪斜。
3)凸模的安装端面应与固定板的支承面在一个平面上。
利用机械法固定凸模,主要有以下几种方法:
(1)压入固定法 压入固定法是应用最普遍的一种凸模固定方法。常用于冲压材料厚度在6mm以下的冲压件冲模。其凸模的结构形式很多,有带台肩的、铆接的和带挂销的等,分别如图1-6a、b、c所示。凸模与固定板的配合采用H7/n6或H7/m6,配合面的表面粗糙度应符合图样要求。固定板的型孔应与端面垂直,不允许有锥度或成鞍形,以保证组装后凸模与端面垂直和牢固可靠。

图1-6 压入法固定结构
1—凸模 2—凹模嵌套
凸模的压入端应设引导部分。为了便于压入,对有台肩的圆凸模,凸模固定部分压入端应采用小圆角、小锥度或在3mm长度范围内将直径磨小0.03~0.05mm作为引导部分。
对于无台肩的异形凸模,压入端(非刃口端)四周应修出斜度或小圆角;当凸模不允许设引导部分时,应在固定板型孔的凸模压入处修出斜度小于10°、高度小于5mm的引导部分或倒成圆角。
压入的方法如图1-7所示。压入时,将等高垫铁2放在平台1上,把凸模固定板3放在两个等高垫铁2上,再将凸模4放在固定板3的孔中。利用手扳压力机或液压机压入凸模,注意不能用锤击的方法。压入时应将凸模置于压力机的中心,压入时要平稳。当凸模与固定板型孔装合部分压入1/3时,应利用角度尺进行垂直度误差的检查,校正垂直度误差后,再将其全部压入。

图1-7 凸模的压入法
1—平台 2—等高垫铁 3—固定板 4—凸模 5—角度尺
凸模压入固定板后,应将固定板与凸模底面磨平。最后,以固定板底面为基准刃磨凸模刃口面。刃磨小凸模时,应采用小的背吃刀量磨削,以防其变形。
(2)紧固件固定法 紧固件固定常采用螺钉紧固和固定块紧固两种方法。图1-8所示为螺钉紧固凸模的方法,常用于大中型凸模的紧固。在紧固时,首先把凸模放入固定板型孔内,调好位置,使其与固定板端面垂直,并用螺钉固紧,不许松动。
图1-9所示为利用斜压块及螺钉紧固的方法,常用于复合模凸凹模的紧固。在固定时,首先将凸凹模放入固定板型孔内,调好位置,压入斜压块3后再拧紧螺钉2即可。
2.物理固定法
低熔点合金在模具装配中已得到了广泛的应用,主要用于固定凸模、凹模、导柱、导套和浇注导向板及卸料板型孔等。其工艺简单、操作方便,浇注固定后有足够的强度,而且合金还能重复使用,便于调整和维修。被浇注的型孔及零件,加工精度要求较低。该方法尤其是在复杂异形和对孔中心距要求严格的多凸模固定中应用更为广泛。利用这种方法固定凸模,凸模固定板不需加工出精确的型孔,只要加工出与凸模相似的通孔即可,大大简化了型孔的加工,且减少了模具装配中各凸、凹模的位置精度和间隙均匀性的调整工作。

图1-8 螺钉紧固法

图1-9 斜压块及螺钉紧固法
1—模座 2—螺钉 3—斜压块 4—凸凹模
(1)低熔点合金的配方 低熔点合金的配方见表1-4。
表1-4 低熔点合金的配方

(2)合金的配制方法
1)将锑和铋分别打碎成5~25mm的小碎块。
2)按配比将各元素称好,并分开存放。
3)用坩埚加热,依次按熔点高低加入锑、铅、镉、铋、锡金属。每加入一种金属元素,都要用搅拌棒搅拌均匀。待金属全部熔化后,再加另一种金属。
4)所有金属全部熔化后,待其冷却降至300℃后,浇入槽钢或角钢做成的模型内,急冷成锭。
5)使用时,按所需要的量再将合金锭熔化。
(3)浇注固定凸模的要点 由于模具零件浇注固定的位置精度取决于浇注前零件的相对位置精度,为此,浇注凸模时,应先将凸模插入凹模型孔内,以凹模为基准定位。因此,凸模位置的准确程度依赖于作为定位用的凹模的准确度和凸、凹模间隙的均匀程度。因而在浇注前,需用工具显微镜检测凹模各型孔的正确性。在浇注时,采用垫片法或镀铜法来控制间隙的均匀性。
(4)浇注方法 浇注方法如图1-10所示。其工艺过程如下:
1)按凸、凹模间隙要求,在凸模工作部分表面镀铜或均匀涂漆,使其厚度恰好为间隙值。
2)将被浇注凸模的浇注部位及固定板型孔清理干净。
3)将凸模轻轻敲入凹模型孔内(间隙较大时可通过垫入垫片来控制间隙),并校正凸模与凹模,使凸模垂直于凹模基面。
4)将已插入凸模的凹模倒置,把凸模固定端插入固定板型孔中心,同时在凹模6和固定板3中间垫上等高垫铁4,使凸模5端面与平台2平面贴合,如图1-10所示。
5)安装定位后,熔化合金,即可浇注。
6)冷却24h后,用平面磨床将其磨平即可安装使用。
3.化学固定法
化学固定法是指利用黏结剂黏结固定凸模,主要有环氧树脂黏结剂、无机黏结剂及厌氧胶三种。环氧树脂黏结剂和无机黏结剂的配方见表1-5、表1-6,厌氧胶可外购直接使用。

图1-10 浇注固定凸模
1—电炉 2—平台 3—固定板4—等高垫铁 5—凸模 6—凹模
(1)利用环氧树脂黏结剂固定凸模
1)环氧树脂黏结剂的配制方法。
① 称料。将配方中各种成分的原料,按计算数量配比用天平称好。
② 加热。将环氧树脂放在烧杯内加热到70~80℃。
③ 烘干铁粉。在加热环氧树脂的同时,将铁粉在烘箱内烘干,温度一般在200℃左右,以去除铁粉内部的潮气。
表1-5 环氧树脂黏结剂的配方

① 这种固化剂适于作为卸料孔的填充剂,并需要加温固化。
表1-6 无机黏结剂的配方

④ 加填充剂。将烘干的铁粉加入加热后的环氧树脂内,并调制均匀。
⑤ 加增塑剂。在调制的环氧树脂内加入邻苯二甲酸二丁酯,继续搅拌,使之均匀。
⑥ 加固化剂。当调制的环氧树脂的温度降至40℃左右时,将无水乙二胺加入,并继续搅拌,待无气泡时,可以浇注使用。
2)浇注黏结工艺。
① 用丙酮清洗凸模及固定板型孔黏结部位,清除杂物及锈斑。
② 把凸模插入凹模中,调整好间隙(利用凸模镀铜、涂漆或垫片法),并保证凸模与凹模基面的垂直度。
③ 用垫块将凸模与凹模组合垫起,并使凸模固定端伸入固定板相应型孔中,调好位置及间隙,如图1-11所示。
④ 将调制好的环氧树脂黏结剂用料勺均匀地倒入凸模与凸模固定板的缝隙中,使其充满并分布均匀。或将凸模抬起一定高度,待环氧树脂黏结剂全部填满后,再将其插入固定,如图1-11所示。

图1-11 环氧树脂黏结剂固定凸模
1—平台 2—凹模 3—等高垫铁4—凸模 5—垫板 6—固定板
⑤ 浇注时,应边浇注边校正凸模与固定板上、下面的垂直度。
⑥ 自然冷却24h后即可使用。
利用环氧树脂黏结凸模时,要严格控制固化剂加入时的温度。例如,采用乙二胺时,温度应控制在30℃左右;用苯二胺时,温度要控制在60~70℃之间。
(2)利用无机黏结剂固定凸模
1)无机黏结剂的配制方法。
① 将100mL磷酸所需的氢氧化铝先与10mL磷酸置于烧杯内,搅拌均匀,呈乳白色状态。
② 再倒入20mL磷酸,加热并不断搅拌,加热至200~240℃,使之呈淡茶色,冷却后即可使用。
③ 将氧化铜放在干净的铜板上,并缓慢地倒入上述调好的磷酸溶液,用竹签搅拌调成糊状,一般能拉出20mm长丝即可。
2)黏结工艺。
① 利用丙酮或甲苯等化学试剂清洗被黏结表面,去除油污和锈斑。
② 将冲模各有关零件按装配要求进行安装定位,并如图1-12所示摆放好。
③ 将调好的黏结剂均匀地涂于各黏结表面。黏结时,可上下移动凸模以排除气隙,最后确定固定位置并黏结。

图1-12 无机黏结剂固定凸模
1—黏结剂 2—凸模固定板 3—垫板 4—凸模 5—等高垫铁 6—凹模
④ 黏结固化后,经钳工修整,清除多余的溢料,修整后即可使用。
采用无机黏结剂固定凸模时,一定要防止黏结剂受潮。在使用前,一般应将氧化铜在200℃的恒温箱内烘36min以上,排除潮气后再使用。在黏结后固化时,应先在室温下固化2h,再将其放在恒温箱内,加热至60~80℃,在此温度下保温2~3h即可使用。
五、模具的总装
模具装配质量的好坏,对模具的技术状态、使用寿命以及制件的质量都有很大影响,装配工作应在装配工艺规程的指导下进行。由于模具生产属于单件小批量生产,故在装配时,模具零件加工误差的累积会直接影响模具装配精度。鉴于模具零件的加工精度不同,可以采用不同的装配方法。
1.模具的装配方法
模具的装配方法主要有两种:配作装配法和直接装配法。
(1)配作装配法 配作装配法的特点,是由配作来使各零件装配后的相对位置保持正确。因此,零件在加工时,只需对与装配有关的必要部位进行高精度加工,而孔位精度由钳工以配作来保证,即使没有坐标镗床等高精度加工设备,也能制造出高质量的模具。这种方法的缺点是全靠钳工的技术水平来保证模具装配精度,耗费工时较多,是缺少精加工设备的中小型工厂的传统装配工艺。
(2)直接装配法 直接装配法是指模具所有零件的型孔、型面,包括安装螺钉孔、销钉孔都是单件加工完成的。装配时,钳工只要把零件按装配图连接在一起即可。当装配后的位置精度较差时,通过修正零件来进行调整。这种装配方法简便迅捷,便于零件的互换,模具装配精度取决于零件的加工精度,不要求模具钳工有很高的装配技艺。因此,要有先进的模具加工技术和高精度的加工设备及测量装置来保证零件的加工质量,才能实现模具的直接装配。如在模具制造中,使用各种先进的数控机床,引入各种各样的计算机系统,对模具零件进行高精度的加工和检测等。
上述两种模具装配方法相比,尽管直接装配法比配作装配法简便,但当装配最终精度要求较高且生产批量又少的模具时,在一定程度上还需依赖于配作装配法。特别是在一些加工条件较差的中小型工厂中,钳工配作装配还占有相当重要的地位。
2.确定冲模装配顺序的方法
冲模的装配最主要的是保证凸模和凹模的对中,使其间隙均匀。为此,总装前必须认真、妥善地考虑上、下模的装配顺序,否则可能出现不便调整间隙的情况。
上、下模的装配顺序与模具的类型和结构有关。通常是看上、下模的主要零件中哪一个位置所受的限制大,就将其作为装配的基准件先装,再以它为基准调整另一个零件的位置。根据这个道理,一般冲模的装配顺序如下:
1)无导向装置的冲模。由于凸模与凹模的间隙是在模具安装到机床上时进行调整的,故上、下模的装配顺序没有严格要求,可以分别进行装配。
2)有导向装置的冲模。装配时先要选择基准件,如导板、凸模、凹模或凸凹模等。在装配时,先装基准件,再按基准件配装有关零件,然后调整凸模与凹模的间隙,使其间隙均匀,而后再安装其他辅助零件。如果凹模是安装在下模上的,则一般先装下模,再以下模为基准安装上模较为方便。
3)有导向机构的复合模。一般先安装上模,然后借助上模的冲孔凸模及落料凹模孔,找正下模的凸凹模位置并调整间隙,再固紧下模。
4)若上、下模工作件是分别配入上、下模板窝座的导柱模,则分别按图样要求,把工作件配入上、下模板窝座内后,在坐标镗床上,分别以上、下模工作件刃口为基准,镗上、下模座的导套和导柱孔。或者将组装好的上模与下模合模后,调整均匀凸、凹模间隙后再紧固,然后镗导套及导柱孔。
5)有导柱的级进模。对于有导柱的级进模,为了便于调整准确步距,在装配时应先将拼块凹模装入下模板,再以凹模为基准件安装上模。
六、弯曲模和拉深模的装配特点
1.弯曲模
弯曲模的作用是使坯料在塑性变形范围内进行弯曲,由弯曲后材料产生的永久变形获得所要求的形状。
一般情况下,弯曲模导套、导柱的配合要求可略低于冲裁模,但凸模与凹模工作部分的表面粗糙度值要求比冲裁模要小(小于Ra0.63μm),以提高模具寿命和制件的表面质量。在弯曲工艺中,由于材料回弹的影响,常使弯曲件在模具中弯成的形状与取出后的形状不一致,从而影响制件的形状和尺寸精度。影响回弹的因素较多,很难通过设计计算来加以消除,因此在制造模具时,常要按试模时的回弹值调整凸模(或凹模)的形状。为了便于修整,弯曲模的凸模和凹模多在试模合格以后才进行热处理。另外,弯曲属于变形加工,有些弯曲件的毛坯尺寸要经过试验才能最后确定。因此,弯曲模进行试冲的目的除了找出模具的缺陷加以修正和调整外,再一个目的就是最后确定制件的毛坯尺寸。因为这一工作涉及材料的变形问题,所以弯曲模的调整工作比一般冲裁模要复杂得多。
2.拉深模
拉深工艺是使金属板料(或空心坯料)在模具作用下产生塑性变形,变成开口的空心制件的加工工艺。
1)同冲裁模相比,拉深模具有以下特点:
① 冲裁模凸、凹模的工作端部有锋利的刃口,而拉深模凸、凹模的工作端部则要求有光滑的圆角。
② 通常拉深模工作部件的表面粗糙度值(一般为Ra0.32~0.04μm)比冲裁模要小。
③ 冲裁模所冲出的制件尺寸容易控制,如果模具制造正确,冲出的制件一般是合格的。而即使组成拉深模的零件制造得很精确,装配得也很好,但由于材料弹性变形的影响,拉深出的制件也不一定合格。因此,在模具试冲后常常还要对拉深模进行修整加工。
2)拉深模试冲的目的有两个:
① 通过试冲发现模具存在的缺陷,找出原因并进行调整、修正。
② 最后确定制件拉深前的毛坯尺寸。为此,应先按原来的工艺设计方案制作一个毛坯进行试冲,并测量出试冲件的尺寸偏差,根据偏差值确定是否对毛坯进行修改。如果试冲件不能满足原来的设计要求,则应对毛坯进行适当修改,再进行试冲,直至冲压出的试件符合要求为止。