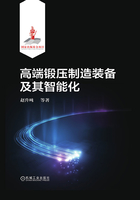
1.3 锻压装备技术的发展目标
目前,制造业已从工厂化、规模化、自动化为特征的工业制造化,转向了多样化、个性化、定制式,更加注重用户体验的协同创新、全球网络智能制造服务。“制造强国战略研究”重大咨询项目提出实施“中国制造2025”的核心是实施制造业的数字化、网络化、智能化。先进而智能的高端装备,是先进制造技术、信息技术和智能技术的集成和融合,通常是具有感知、分析、推理、决策和控制功能的装备的统称,体现了制造业的智能化、数字化和网络化的发展要求。
所规定的材料的塑性成形工艺必须依赖锻压设备来完成工业化生产,而锻压设备必须要满足塑性变形工艺对运动、能量与控制的要求。金属塑性成形是利用材料的塑性,在外力、能量和相应的工模具的约束下,使金属产生永久变形以获得所需形状和性能的一种加工方法。经塑性成形加工的工件有着优良的材料流动纤维、理想的材料强度特性、最少的材料和能量消耗,以及较高的精确度和表面质量。金属塑性成形用来改变材料的形状,尺寸与性能,兼备成形与成性两个方面,因此越来越成为材料加工首选的工艺方法。随着新材料、先进塑性成形工艺的迅猛发展,对锻压设备提出了越来越高的要求。
锻压设备目前正处于“数控一代”(交流伺服电动机驱动的时代)迅猛发展的时期,并将朝着“智能一代”的方向发展。依据制造业的发展趋势,迫切需要锻压设备朝着高效、节能、高可靠、高精度、智能化的方向发展,为新材料、航空航天、机器人、低碳、新能源等高新技术领域装备,汽车、铁路及电力装备的设计制造提供技术支撑。
针对国外先进锻压设备的现状,并充分考虑到我国锻压设备的实际情况,我国锻压设备未来5~10年的发展目标主要体现在以下几个方面。
1.3.1 重型锻压装备的自动控制与工艺、模具一体化的数据库
美国1955年投产的两台4.5万t模锻液压机,苏联1961—1964年投产的两台7.5万t模锻液压机,法国1976年投产的一台6.5万t模锻液压机,经过几十年的工业化生产,其能力得到了充分的发挥,例如空客A380大型客机的锻件已在俄罗斯的7.5万t模锻液压机上实现了稳定高质量的生产。1962年我国自行设计制造了3万t模锻液压机之后又设计制造了1万t多向模锻液压机,此后重型锻压设备的研发停滞不前。直到2012年,4万t、8万t模锻液压机先后在西安、德阳市投产;2011年3.6万t的黑色金属垂直挤压机在包头市投产;太原重型机械集团有限公司(简称太重)生产的1.5万t卧式挤压机2013年投产,2.25万t卧式挤压机2016年在辽宁忠旺公司投产,8000t快锻液压机2007年投产,1.25万t的快锻液压机2012年投产;中国重型机械研究院研制的7m轧环机2011年已在青岛成功应用;青岛锻压机械有限公司(简称青锻)研制的8000t电动螺旋压力机2012年投产;2007—2010年,一重、二重、上重、洛阳中重分别新增150MN、160MN、165MN、185MN自由锻液压机,而其中185MN自由锻液压机,配备750t·m的锻造操作机,使我国的大锻件能力从190t提高到400t,最大钢锭生产能力从360t提高到600t。有效地缓解了我国航空、航天、国防、船舶、电力及机械制造等行业急需大型锻压产品制造能力不足的局面。目前世界上知名的重型锻压设备还未真正批量化应用于工业中,与该类设备最大能力发挥的相关模具、工艺与控制一体化的数据化研发还远远不够,已造成这些重型设备优质资源的浪费。例如西安三角公司的4万t模锻压力机的满负荷工作压制的最大速度可达20mm/s,而目前我国在大型高质量的航空与航海发动机用模锻件的实际工业化生产的工作速度仅为5mm/s,同时滑块的每分钟行程次数也未能满负荷得到发挥。
自2007年以来,中国在重型锻压设备的研发与投产情况已在世界名列前茅,但仔细考究这些投资巨大的设备,其中的油压控制系统硬件与电气控制硬软件不少都是花巨资委托国外厂商(如美国oilgear towler公司)定制。特别是其中的高压、大流量、高精度的液压元件(泵、阀等)与电气控制器件,几乎全部采用国外进口。造成这些关系到国家安全与国计民生的关键设备的心脏部件及其神经控制系统完全依赖国外,因此,急需要开发出具有自主知识产权的高压、大流量、高精度的液压元件与电气控制硬件,并研发出相应的系列化、标准化、智能化、网络化控制软件,既可使这些重型设备的能力得到充分发挥,又可为后续的重型锻压设备的研发奠定坚实的基础。
1.3.2 大中型伺服压力机及其控制系统
目前我国的机械装备正处于“数控一代”蓬勃发展的时期,锻压装备朝着分散多动力、近零传动(近直驱)的全数控方向发展。而这一先进理念在锻压装备中就表现为伺服压力机。鉴于目前小规格伺服压力机的技术水平已趋于成熟,今后主要应在大中型伺服压力机的传动方式、工作机构及其大规格伺服电动机方面进行研究。尤其在公称压力为630t、800t、1000t、1250t、1600t、2000t、2500t、3000t、3500t、4000t、4500t机械式伺服压力机,公称压力为3500t、4000t、4500t、5000t、6300t、8000t液压式伺服压力机,横向旋压力为10t、20t、30t、40t、60t全数控强力旋压机及其各自的数控系统等方面。
1.3.3 高效、高性能精确成形数控压力机
为了进一步降低生产成本,提高劳动生产率,应加大型高速压力机、覆盖件拉深设备、径向锻机、高速落料机的研发力度。尤其要研发出公称压力为100t、125t、160t、200t和滑块行程次数为1000~1250的闭式高速机械压力机,公称压力为1000t、1250t、1600t、2000t、2400t和滑块行程次数为16~20次/min的覆盖件拉深机械压力机,公称压力为630t、800t、1000t和40~60次/min的闭式单动板材落料机械压力机,可锻棒料直径为100mm、130mm、160mm、250mm和锤头打击次数为500~1200次/min的机械式径向锻造操作机,公称压力为20t、30t和冲头次数为1000~1500次/min的回转头机械压力机。
1.3.4 适用于新材料、新工艺的特种压力机
随着像高强度钢板、轻质的铝镁合金板材、轻质多孔材料、光伏玻璃基板覆铜板材、纤维增强复合材料等新型材料,以及诸如板材的锁铆焊、管材的压力复合、对轮旋压、双辊夹持旋压、板材的热成形、多点模成形、内高压成形、半固态成形、电磁成形、爆炸成形、增量式轴向推进滚轧成形等新塑性成形工艺的大量涌现,要满足其工业化生产的要求,急需研发相应的特种设备以适应新的材料、满足新的工艺条件。
1.3.5 行业与国家重大需求的核心关键塑性加工装备
我国近年来的高铁运输装备、核电设备、汽车、船舶、航空航天、发电装备、兵器、家电、通信等领域,需要的核心关键设备无法从国外进口,大大制约了这些领域的发展。锻压装备尤其要强化与海洋与航空领域密切相关的研发,例如核潜艇壳体的环轧与胀形塑性成形设备。考虑到冲压是汽车制造4大工艺之首,应加大适用于汽车节能减排的先进制造装备的研发,以达到节能、降耗、提高生产率、降低成本、改善质量的共同目标,为我国汽车工业可持续发展奠定良好的基础。