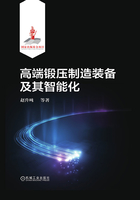
7.1 快锻液压机的工作原理、特点及主要应用领域
7.1.1 快锻液压机的工作原理
快锻液压机是自由锻造液压机技术发展的主要方向,它不仅体现在快锻(精整)时的频次(60~100次/min),更主要体现现代锻造液压机的快速性、功能和效率上,包括活动横梁(上砧)的工作速度(含空程和锻造速度)、锻造工件的尺寸精度、机械化程度高和节能效果显著等方面。在大型自由锻工艺中,占用工时最多的工序是镦粗和拔长,快速精整工序占用工时并不多。因此,应适当提高工作速度和具有一定的锻造频次和快速精整功能。
其次,如果以加工对象定义的话,快锻液压机更多地适用于锻造温度窄的高合金钢锻件、轴类、棒类锻件,如车轴、圆棒材等的专业化生产,而且大多为中小型吨位的单缸或多缸结构压机。锻造频次或精整频次常常以确定的压入深度和回程量来计算的。对于不同吨位的、不同工艺对象的自由锻液压机是不可能实现大压下量和满吨位快锻的。
现代的快锻液压机主要采用立式、液压泵直接传动方式,有上压式和下拉式两种结构(见图7-1和图7-2),下拉式因其活动部分(整体机架)质量大,惯性大,在10~30MN快锻液压机或厂房高度受限制的情况下采用,本章主要介绍立式上压式快锻液压机。

图7-1 185MN上压式快锻液压机

图7-2 下拉式快锻液压机
1.快锻液压机的基本系列
快锻液压机的主参数(公称力)系列按GB/T 321规定的优先数R10的圆整值作为公比,近似于等比数列排列,见表7-1。
表7-1 主参数(公称力)系列(单位:MN)

①使用时,该数值作为相应公称力的可选择参数。
2.主要技术参数及定义
(1)公称力 代表液压机规格名义上能产生的最大力,它反映了液压机的主要工作能力。单位为MN,在数值上等于主(侧)缸柱塞的总面积(m2)与液压系统的最大工作压力(MPa)的乘积(取整数)。
(2)液压系统最大工作液压力 液压系统中液体的最大单位工作液压力,即液体的最大压强。工作液压力不宜过低,否则设备重量、占地面积增加,成本增高;反之,工作液压力过高,则密封、液压元件寿命会有影响。目前国内液压机所用的工作液压力为25~50MPa,多数用31.5~35MPa的工作液压力。
(3)最大回程力 液压机活动横梁在回程时除了要克服各种阻力和运动部件的重力外,还要考虑满足快锻频次所需的加速度。
(4)开口高度 亦称净空高,指活动横梁或整体机架处于上极限位置时,上砧垫板下平面至移动工作台上平面的距离。
(5)立柱横向净空距 两个(四个)立柱内侧允许工件进出的净空距离。
(6)横向偏心距 锻件的受压中心至液压机移动工作台中心线之间的距离。一般指常锻工况最大锻造力下所允许的最大偏心距离。
(7)最大行程 最大行程是指活动横梁能够移动的最大距离。
(8)工作速度 亦称加压速度,指在常锻工况下,上砧单位时间内的压下行程。
(9)空程速度 上砧在接触工件前单位时间内的下降行程。
(10)回程速度 上砧在加压锻造后向上单位时间内的行程。
(11)压下量 即压缩量,锻件被压缩前后高度方向的差值。
(12)行程控制精度 在自动锻造过程中,液压机的上砧行程设定位置与实际位置的差值。
7.1.2 快锻液压机的特点
快锻液压机适合于黑色金属直形和台阶形钢棒、转轴、环件、衬套、饼件和各类特定的自由锻件生产,是大型锻件镦粗开坯和自由锻件生产必不可少的压力加工设备,具有如下特点。
1.预应力组合机架结构
基于现代锻造压机高精度和快速性的工艺要求,压机的整体结构刚性和导向精度非常关键,决定着压机的整体性能。压机本体由两个(四个)坚固的长方形空心立柱作为机架,拉杆置于空心立柱中,在拉杆全长上将上、下横梁和立柱预紧固成一个预应力结构组合机架,上下梁开档内侧之间不再需要设置和紧固螺母。承受工作负荷时能够达到很好的平衡和稳定性,结构紧凑,具有较高的整体结构刚性、抗疲劳强度、承载能力和安全可靠性。
2.双球铰柱塞式工作缸结构
主工作液压缸为柱塞式,与上横梁组合构造,上传动方式,更换密封易接近。柱塞与活动横梁的联结均设计为双球铰节结构,允许偏心锻造范围大,偏心锻造所产生的偏载力可经立柱传递到上横梁,液压缸导套与密封处不会承受由于偏心锻造所产生的水平力,从而延长了密封寿命。
3.全封闭立柱平面导向方式
活动横梁为特殊的五件组合式构造设计,将两个空心立柱四周封闭,在立柱外围四周多个平面上导向,上下导向面间距长,工作时自动贴合立柱,导向面压低,导向精度高,导板调整更换方便,抗偏载能力强,拉杆永无磨损。
4.“宜人化”的锻造操作环境
配有工作台移动装置、型砧横向移动装置、上砧快速夹紧旋转装置以及钢锭旋转升降台等机械化设备,锻造工具配置与调配系统可按程序组合和调用上下砧具,缩短了辅助作业时间,减轻了繁重的体力劳动,有效地提高了生产效率。
5.单人操作的控制系统
压机采用PLC与计算机两级控制,具有友好的单人操作人机交互操作系统与故障诊断系统,多层面、实时地向操作者提供生产工艺、设备状态技术信息。由1名操作工操作锻造压机、操作机以及辅助装备,实现协调联动操作控制,并按预先编好的锻造程序完成一根台阶轴的锻造。
6.较高的行程速度和锻造频次
采用大流量定量泵、伺服变量泵双组合直接传动和高频响比例阀控制技术,以及三缸分级锻造,可实现液压机在规定条件下进行节能锻造和快速锻造;常锻工作速度可达80~160mm/s,精整快速锻造频次为60~100次/min,缩短作业时间,提高效率和锻件品质,降低功率损耗,节约能源。
7.锻造尺寸精度控制
采用两套绝对值编码器实时检测活动横梁的行程并进行闭环控制,针对快速锻造时连续锻打的工作特点,采用智能调节器自动补偿活动横梁的位移,使锻件的热态精整锻造控制精度达到±(1~2)mm。
8.与操作机联机操作系统
锻造压机可与配套的全液压轨道式锻造操作机实现联机控制操作和实时监测。操作机采用比例伺服控制,可对夹持着锻件的钳头进行高精度的进退、翻转、提升和平移的自动控制,同时具有倾斜、侧摆功能,配合压机完成钢锭开坯、拔长、整圆等联动锻造工艺操作。
7.1.3 快锻液压机的主要应用领域
锻造行业作为国民经济中的一个重要基础工业,各类锻件在众多领域中都起着不可替代的作用。即使在计算机技术、信息技术高度发展和工业现代化的今天,锻造仍然是大到上天、下海、入地材料的加工,小到金银首饰制作,国计民生须臾不离的技术。只要有金属,只要有材料加工,就会有锻造。
20世纪50~90年代制造的三梁四柱式水压机和自由锻锤在我国早期的工业发展中做出了很大的贡献。但由于高耗能、生产效率低、环保差、锻件精度低等方面原因,逐步被中小型快锻压机所取代。快锻压机具有锻造速度快、动作灵敏,锻造频次高、自动化程度高等特点,可自动控制进给量、压下量、打击频率,从而调节温降和变形温升,保证终锻温度、变形率、组织和性能,还能显著降低工人的劳动强度;锻造精度高,锻件厚度公差可达到±(1~2)mm。安全、节能、振动小、噪声低,显著改善生产工作环境。
由于新型合金材料不断出现,这些材料塑性差,变形抗力大,热加工温度范围窄,要求锻压设备能力大、速度快,一般的锻压水压机和气锤都不能兼具这两个条件,而快锻液压机却能够胜任,因此,快锻液压机得到现代锻造企业的广泛青睐,几乎代替了锻压水压机。对于特殊钢及钛合金生产中,为了扩大品种、提高质量,快锻液压机已成为现代化特殊钢厂的必备装备,对耐热合金、不锈钢、高速钢、模具钢等材料都能加工,它可生产较大规格的方、圆、扁坯锻材和盘件、环件、炮筒、炮尾座及各种自由锻件,宜于多品种小批量的生产;它与精密锻造机联合作业,还可生产大型管坯、车轴等产品。
随着国民经济的迅速发展,科技水平不断提高,我国国力的增强,机械基础设备逐渐向大型化、精密化、紧凑化、成套化、自动化方向发展。大型锻件生产,如百万千瓦级火电和超临界、超超临界核电用汽轮机转子、特大支承辊、大型高温高压厚壁筒体、船用大马力低速柴油机组合曲轴等锻件的质量控制需要高精度、高效率的锻造液压机。因此,新型的节能降耗低碳、精简连续、高速高效的产品将会不断地涌现。基于国内自主研发的价格优势、国家政策扶持优势以及产品本身技术性能的不断提高,基于我国大型运输机、航空航天业、船舶、导弹等军工国防工业、高速列车、城市轨道交通等现代化交通运输业的快速发展,自主研发研制的产品,均需大型化、整体化的锻件。因此,快速锻造液压机设备向大型化发展是必然的。