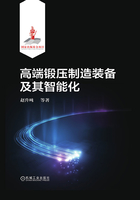
6.3 泵控电液伺服系统的研究
液压机发展趋势之一就是高精度液压机的发展,液压机的高精度要有可控性好、控制精度高的液压系统来保证。电液伺服系统可以充分发挥电子与液压两方面的优点,其具有力或力矩大、精度高、响应速度快及灵活性好等优点,因而得到广泛的应用。
6.3.1 电液伺服系统分类
电液伺服系统主要由电子电气元件、电液伺服阀、液压元件、反馈检测元件和控制对象等组成。根据液压控制元件的不同,电液伺服系统可以分为阀控式和泵控式两大类。
阀控式液压伺服系统是由伺服阀、执行元件、反馈元件、被控对象等组成,执行元件的流量或压力的变化是通过改变伺服阀的流量来实现的。阀控式液压伺服系统具有系统精度高、输出功率大、响应快等优点,因此阀控式液压伺服系统广泛应用于工业生产中。但是其也有固有的缺陷:
1)尽管阀控液压伺服系统具有控制精度高、直线性好及灵敏度高等优点,但污染的液压油容易造成伺服阀的磨损,进而影响伺服阀的控制精度,因此阀控液压伺服系统对油液的纯度要求非常高。该系统需要增加过滤技术以提高工作油的纯度,这样就提高了阀控电液伺服系统的成本。
2)在阀控式液压伺服系统中一般都是定量泵提供液体的压力及流量,因此在系统中存在溢流阀或节流阀,这必将使由节流损失而导致的油温升高。
3)由于伺服阀结构复杂、成本比较高,其价格是普通阀的几十倍甚至上百倍,因此增加了系统的成本。
4)在功率匹配的情况下,伺服阀提供的负载压力最大只有油源压力的2/3,系统能量浪费严重。
泵控式液压伺服系统一般是由定量泵或变量泵、可调速电动机、执行液压元件等组成,控制执行元件的流量或压力的变化是通过改变泵的流量来实现的。泵控式液压伺服系统因没有节流损失,所以效率高、发热量小。但其也存在以下缺点:
1)该系统具有结构复杂、惯性大、稳定性不好等缺点,因此其控制系统的快速性不如阀控系统。
2)由于该系统速度或压力的变化是通过液压泵流量的改变来实现的,这就需要一套比较复杂的变排量控制机构,因此相应地增加了系统成本。
3)电动机效率随负载而变化,在小载荷时电动机效率低,能量浪费严重。
4)由于变量泵的斜盘倾角变化范围有限,因此液压泵流量变化范围有限,系统的调试范围有限。
6.3.2 泵控式液压伺服系统的研究
西安交通大学的赵升吨团队对伺服直驱泵控式液压传动方式进行了研究,对开关磁阻电动机直驱定量泵控式液压伺服系统和交流伺服电动机直驱变量泵的变量斜盘的闭式液压系统进行了仿真及试验研究。
1.两类泵控式电液伺服系统的原理
直驱泵控式电液伺服系统就是利用调速电动机调速范围宽、可以频繁换向的优点来取代液压伺服阀的功能。这种电液伺服系统可以分为两种:一种是利用调速电动机通过改变定量泵的转速来改变泵的输出流量,达到调节执行元件速度的目的,这种泵称为直驱定量泵控式液压伺服系统,其原理如图6-9所示;另外一种是通过变量机构来改变变量泵的输出流量,来实现执行元件速度改变的目的,这种系统称为伺服电动机直驱变量泵的变量斜盘的电液伺服系统,其原理如图6-10a所示。变量泵的变量机构有很多种,但常见的是通过液压系统来改变液压泵的斜盘倾角,该方案具有控制精度低,液压泵的响应速度慢的缺点,为了提高变量泵的响应速度、控制精度以及便于实现伺服控制,西安交通大学的赵升吨教授课题组设计了通过交流伺服电动机驱动滚珠丝杠机构来调节液压泵的斜盘倾角,其原理如图6-10b所示。

图6-9 直驱定量泵控式液压伺服系统

图6-10 交流伺服电动机直驱变量泵的变量斜盘的闭式液压系统
a)伺服直驱变量泵的变量斜盘液压系统原理 b)伺服变量泵变量原理
2.试验研究
赵升吨教授课题组分别搭建了前述的两类泵控液压系统的试验台,通过试验对比它们的动态响应特性的差异,并得出结论。
直驱定量泵控式液压系统性能试验:
1)实验台组成。图6-11所示为直驱定量泵控式液压伺服控制系统试验台。试验装置主要包括:SR电动机、双向定量泵、流量传感器、压力传感器、位移传感器、采集卡等,具体元件的安装及位置如图6-12所示。

图6-11 直驱定量泵控式液压伺服控制系统试验装置

图6-12 试验用部分元件
2)硬件配置信息。数字采集卡、数字示波器、滑阻式位移传感器、液压缸和流量传感器等。
数字采集卡插在计算机主板PCI槽上,通过PCI通信实现对滑块位移及压力流量信号的采集。表6-2为所选SR电动机参数,SR电动机控制器(见图6-12),其主要作用是通过单片机、外存储扩展芯片和可编程器件PLD来实现控制和数据存储功能,内部组成结构如图6-13所示。通过RS232通信协议与上位计算机进行通信,实现人机交互远程控制,并且也可以通过控制器操作面板和模拟量进行控制。
表6-2 试验用SR电动机参数


图6-13 SR驱动器及其控制器内部结构
数字示波器主要采集试验过程中实时性较高和变化较快的数据或者不方便从控制器存储单元中读出的数据,同时可以检验数据采集卡采集的数据是否正确,从而一定程度上可以减少硬件电路开发的时间。
位移传感器安装在液压机的机身上,与液压机的滑块相连,主要功能为读取液压机滑块的输出位置。使用之前需进行位置标定。
为了加载方便和进行后续试验,本液压系统试验用的液压缸利用Y41-63液压机的液压缸进行试验。液压缸的最大行程为500mm、直径为180mm,活塞杆的直径为140mm。
流量传感器采用的是陕西大丰科技有限公司生产的流量计,流量计的量程为180L/min,输出电压为0~5V,在使用时需进行标定。
3)试验结果及分析。试验时,首先通过改变单向阀的弹簧刚度实现单向阀背压改变,进行了补油单向阀的背压对系统动态响应的试验,确定出合适的单向阀弹簧的刚度,接着对系统进行正弦信号输入的跟踪试验。图6-14a所示为系统的单向阀背压为2N时,系统对正弦信号的跟踪响应曲线。图6-14b所示为在无载荷状况下,为补油单向阀的不同背压对系统动态响应的影响。
从图6-14中可以看出,系统存在较大的延迟时间,通过试验得知产生这种现象的原因有三点:一是液压油的可压缩性导致系统响应时间的延迟;二是补油单向阀的背压阻力对液压泵的吸油产生一定阻力,导致液压泵的供油滞后,从而使整个系统产生时间的延迟;三是由SR电动机性能测试试验可知SR电动机存在一个速度死区,进而影响系统的动态响应性。

图6-14 开关磁阻电动机直驱定量泵式液压系统试验结果
a)系统对正弦信号的跟踪响应曲线 b)单向阀的背压对系统动态响应曲线
由图6-14b可知,补油单向阀对系统的动态响应影响较大,当单向阀的背压小于5N,对系统影响较小,在5~25N之间时,系统的响应时间会随单向阀的背压值增大而增大;而当单向阀的背压值大于35N时,系统将不能运动。产生这种现象的主要原因就是补油单向阀的背压影响了液压泵的供油,进而影响了系统的动态响应性。但补油单向阀的背压增大时,液压泵的吸油阻力增大,这样影响了系统的供油,进而影响液压缸的动作。当单向阀的背压值大于35N时,液压泵的吸力不足以打开单向阀,液压泵不能吸油,所以液压缸没有运动。
伺服电动机直驱变量泵的变量斜盘的液压系统试验:
1)试验台组成。试验原理如图6-10所示,试验装置如图6-15、图6-16所示,该试验是在Y32-20型液压机上进行的。试验装置主要包括:异步交流电动机、双向变量泵、单向阀、液控单向阀、溢流阀、计算机、数据采集卡、交流伺服电动机等。其硬件设备见表6-3,试验用液压机的技术参数见表6-4。

图6-15 伺服电动机直驱变量泵的变量斜盘的液压系统试验装置

图6-16 试验用部分元件
表6-3 伺服电动机直驱变量泵变量斜盘的液压系统试验硬件配置清单

表6-4 Y32-20型液压机技术参数

2)控制算法。采用传统的PID控制方法。
3)试验结果。本试验的目的是针对开关磁阻电动机直驱定量泵控式液压系统进行对比试验,因此系统输入信号同开关磁阻电动机直驱式泵控式液压系统同样是阶跃信号,同时对伺服泵不同转角下系统的输出流量试验。图6-17所示为伺服变量泵在不同转角下系统的输出流量曲线,图6-18所示为系统对阶跃输入的响应曲线。
试验结果分析:由图6-17和图6-18比较可知,交流伺服电动机直驱变量泵的变量斜盘的液压系统相对于开关磁阻电动机直驱定量泵控式液压系统具有较好的动态响应性,但可控性较差。伺服电动机直驱变量泵的变量斜盘的液压系统进行跟踪控制很难实现,因为要实现位置跟踪控制必须实现两个闭环控制:一是位置的闭环控制;二是电动机正、反转时转角总和为零的控制。

图6-17 在伺服电动机不同转角下液压系统的流量曲线

图6-18 交流伺服电动机直驱变量泵的变量斜盘的液压系统阶跃响应曲线
3.总结
1)通过伺服电动机直驱变量泵的变量斜盘的液压系统试验可知,影响伺服变量泵的控制精度因素很多,不仅是伺服电动机的控制精度影响该液压系统的控制精度,而且变量泵斜盘的制造精度也同样影响该液压系统的控制精度。
2)分别进行了开关磁阻电动机直驱定量泵控式液压系统及交流伺服电动机直驱变量泵的变量斜盘的液压系统试验,试验结果表明,开关磁阻电动机直驱定量泵控式液压系统具有较好的可控性,但补油单向阀对系统的响应性影响很大;交流伺服电动机直驱变量泵的变量斜盘的液压系统具有较好的动态响应性,但其可控性相对于开关磁阻电动机直驱定量泵控式液压系统较差。