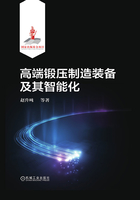
3.1 伺服压力机的工作原理、特点及应用领域
3.1.1 伺服压力机的发展简介
随着我国钢铁、有色冶金、航空航天、铁路高速机车、船舶、核电、风电和军工等行业的快速发展,对高性能锻件的需求量越来越大,同时对模锻设备的节能化、伺服化、精密化要求越来越高。
锻压设备共分为三代:蒸汽锤(蒸汽作为动力),机械压力机(交流异步电动机作为动力),伺服压力机(交流永磁同步伺服电动机作为动力)。图3-1所示为蒸汽锤,它是以蒸汽作为动力,这种锻压设备已经基本上被淘汰。第二代机械压力机也称为曲柄压力机,是一种依靠电动机作为原动机直接拖动的机械传动式设备,如图3-2所示。

图3-1 蒸汽锤

图3-2 传统的机械压力机
第二代机械压力机是现代主流的锻压设备,占整个锻压设备的80%左右,它采用交流异步电动机、离合器、制动器、齿轮减速系统和曲柄滑块机构等组成的机械传动方式。因为交流异步电动机启动电流是额定电流的5~7倍,并且交流异步电动机启停困难、耗时较长,无法满足每分钟启停十几次或几十次冲压工件的要求,因此必须带有离合器和制动器。传统的机械压力机中的离合器和制动器常常被认为是机械压力机的心脏部件,但因为有离合器和制动器,第二代机械压力机要多消耗20%左右的离合与制动能量。此外,离合器和制动器还需要更换磨损过度的摩擦材料,导致使用和维护费用比较高。
何德誉在《曲柄压力机》一书中将机械压力机在工作行程内的能量消耗分为7种,其中滑块停顿飞轮空转时电动机所消耗的功率约为机械压力机额定功率的6%~30%。第二代机械压力机采用了离合器等,存在飞轮空转时消耗的能量,造成严重的能量损耗。
以交流伺服压力机为代表的第三代锻压设备所采用的交流伺服电动机启动电流是不会超过额定电流的,并且交流伺服电动机又允许频繁启停,因此交流伺服压力机的传动系统中不需要离合器和制动器,从而大大简化了结构,节约了离合器与制动器动作时的能量。
目前伺服压力机根据工作方式可分为机械伺服压力机、液压伺服压力机和螺旋伺服压力机等。伺服驱动技术在锻压设备上应用广泛,目前国内外已研发出多种伺服驱动的锻压设备,如伺服式热模锻压力机、机械与液压混合型伺服压力机、交流伺服电动机直驱式回转头压力机、交流伺服式直线电动机驱动压力机、交流伺服电动机驱动的全数控旋压机、交流伺服电动机驱动的全数控式折弯机和伺服式数控卷板机等。
3.1.2 伺服压力机的工作原理
伺服压力机通常指采用伺服电动机进行驱动控制的压力机。伺服压力机通过伺服电动机驱动工作机构运动,来实现滑块的往复运动过程。通过复杂的电气化控制,伺服压力机可以任意编程滑块的行程、速度、压力等,甚至在低速运转时也可以达到压力机的公称吨位。
伺服压力机工作一个循环所消耗的能量A可表示为:
A=A1+A2+A3+A4+A5
式中 A1——工件发生变形所需要的能量(J);
A2——伺服压力机进行拉延工艺时消耗的能量(如果设计的伺服压力机无拉延工艺,则不考虑该能量消耗)(J);
A3——锻压过程中工作机构由于摩擦所引起的能量消耗(J);
A4——锻压过程中由于伺服压力机整体的弹性变形所引起的能量消耗(J);
A5——伺服压力机空程运转所引起的能量消耗(J)。
3.1.3 伺服压力机的特点
交流伺服压力机不同于普通的机械压力机,它具有很多普通机械压力机无法具有的特点。
(1)锻压过程伺服控制,可以实现智能化、数控化、信息化加工 针对不同的加工材料和加工工艺,可以采用不同的工作曲线。锻压能量可以实现伺服控制,可以在需要的范围内数字设定滑块的工作曲线,有效提高压力机的工艺范围和加工性能。锻压参数可以实现实时记录,易于实现压力机的信息化管理。交流伺服压力机操作简单可靠,伺服控制性能好。
(2)节能效果显著 在工作状态下,交流伺服压力机本身的耗能就比普通机械压力机低。交流伺服压力机可以去除离合器等装置,没有了离合器结合耗能。在滑块停止时,伺服电动机停止转动。相比于普通机械压力机,其消除了飞轮空转消耗的能量,有效节省能源。在压力机低速运行时,伺服压力机相对于普通机械压力机的节能效果将更为突出。
(3)滑块运动数控伺服 滑块的运动曲线可以根据需求进行设定。在锻压阶段,可以调节降低滑块的运动速度,实现低速锻压的工作要求。在回程阶段,可以调节提高滑块的运动速度,实现滑块对急回的工作要求。通过伺服控制滑块的运动曲线,有利于提高锻件精度,延长模具寿命。
(4)压力机整体结构得到简化 交流伺服压力机去掉了传统机械压力机中的核心部件——气动摩擦离合器,传动系统简单,同时,交流伺服压力机也不需要大飞轮等,结构得到简化,维修量减少。
(5)提高生产率 由于滑块的运动曲线可以根据需求进行设置,所以可以根据需求调节滑块的运动速度和滑块行程次数。交流伺服压力机的行程可调,行程次数相应可以提高;在保证行程次数不变的情况下,可以提高非工作阶段行程速度,降低冲压阶段的锻冲速度,提高工件的加工质量。相比于普通机械压力机,交流伺服压力机的生产率得到了大幅提高。
(6)超柔性、高精度 图3-3所示为超柔性加工各种工艺滑块速度曲线,交流伺服压力机具有自由运动功能,滑块运动速度和行程大小可以根据成形工艺要求而设定,因此对成形工艺要求具有较好的柔性。交流伺服压力机采用滑块位移传感器实现全闭环控制,提高下死点的精度,补偿机身的变形和其他影响加工精度的间隙。滑块的运动特性可以采取最优策略,例如,拉深、弯曲成形时,采取合理的滑块运动曲线可以减少回弹,提高制件质量和精度。

图3-3 超柔性加工各种工艺滑块速度曲线
a)冲压成形加工 b)拉深成形加工 c)板料锻造加工 d)顺送加工 e)自动化加工
(7)降噪节能 去除传统压力机的离合器/制动器,滑块的运行完全由伺服电动机控制,在启动和制动过程中不会产生排气噪声和摩擦制动噪声,降噪环保;同时减少了摩擦材料的使用,节能省材。此外,减少了压力机工作时的振动,模具寿命可以提高2~3倍。
3.1.4 伺服压力机的应用领域
1.汽车覆盖件生产线
日本网野公司研发生产了大型机械多连杆式伺服压力机,在中国得到较好的应用,目前已引入这种压力机的公司有东风汽车有限公司、天津汽车模具制造公司、成都飞机制造公司、广州日野汽车公司和湖北先锋模具公司等。其中东风汽车公司于2007年引进的是由一台10000kN、四台6000kN的机械多连杆式伺服压力机组成的覆盖件生产线。该生产线承担了东风小霸王系列、东风之星系列、东风梦卡系列等车型白车身中小型冲压件的生产任务。主要工艺有下料、拉延、修边、冲孔、斜切、校正和弯边等。经过实际加工生产验证,该系列的伺服压力机显著提高了生产线的生产效率,实现了重大突破,并且具有节省能源、噪声低、生产率高和生产过程管理可控等优点。
2.镁合金挤压成形
在普通的曲柄压力机上很难成形镁合金材料。日本小松公司在其研发的HCP3000伺服压力机上成功实现了镁合金杯形件的反挤压成形(见图3-4)。首先将坯料放入凹模中,凸模慢速下降,将毛坯压在凸模和顶料器之间,在下降过程中毛坯被加热到300℃;当顶料器到下极限位置时,滑块以恒压力低速度下行,开始挤压过程,直至完成反挤压过程;然后滑块快速回程。滑块在一个循环内经历了四种不同的速度,并且恒压控制挤压过程。这一工艺对速度的控制提出了很高的要求,在普通的曲柄压力机上是很难实现的。

图3-4 镁合金杯形件反挤压成形
3.低噪声冲裁
在普通机械压力机上进行冲裁工艺时,由于材料突然断裂会产生较大的振动和噪声,不仅会影响制件的加工质量,还会形成噪声污染,危害工人健康。如果能够有效地控制滑块运动速度,使制件在变形过程中所储存的变性能在材料完全断裂之前就基本释放完毕,这将有可能大大降低振动,降低噪声,如图3-5所示。

图3-5 低噪声冲裁
4.精密冲裁
日本小松公司在普通机械压力机和HAF伺服压力机上进行了精密冲裁对比试验,工件为空调机凸轮,尺寸为40mm×13mm,负荷为80t,材料为SPC。冲裁的速度越低,冲裁断面剪切带厚度就越大,断面质量就越好,如图3-6所示。普通压力机在2000~3000件后表面会出现裂纹,但伺服压力机在3000件后断面仍然保持完好。

图3-6 精密冲裁
5.轴承垫块压制成形
图3-7所示的轴承垫块,原来在机械压力机上压制成形,压力为110t,工件公差为0.02mm,由于滑块下死点位置漂移,常常周期性地超差;采用伺服压力机后,由于可以严格控制滑块速度和位移,控制滑块在下死点的位置,工件实际偏差可以控制在0.01mm以内,而载荷反而可以减少一半,仅为48t。

图3-7 轴承垫块压制
6.最优速度冲裁
对于SPCC钢板冲裁件,其最佳冲裁速度约为9mm/s。通过设定曲柄、六连杆和八连杆压力机滑块行程为1200mm,连续行程次数为18次/min,分析其运动特性可以看出,不同传动杆系压力机的工作速度也各不相同,以距离下死点3mm处为冲裁开始点,其工作速度分别为133.7mm/s、118.5mm/s、95.6mm/s,远远高于最佳冲裁速度(见图3-8),即采用传统机械压力机,在保证生产节拍的前提下难以实现最佳冲裁速度。而采用伺服压力机,在预达到冲裁点前通过急速降低伺服电动机转速可以达到最佳冲裁速度。

图3-8 曲柄、六连杆、八连杆机械压力机运动特性曲线