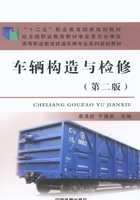
第八节 轮对检修工艺
轮对修理分为厂修和段修(临修按段修标准)。在车辆修理工厂、局属车轮工厂或车辆段轮轴车间(相当于车轮工厂)进行修理称为厂修,按厂修限度标准检查和验收;在车辆段轮轴工组进行的修理称为段修,并按段修限度标准检查和验收。铁路局所属车轮工厂生产的轮对,主要是供车辆段做段修用的,但车轮厂中有一部分需要分解、加工、组装的轮对,为考虑其经济效果,要求按厂修标准施行;对不需分解的轮对,可按段修标准出厂。轮对在车轮厂或车辆段轮轴车间修理的修程分以下几种。
(1)新组装:以新车轴、新车轮按新制技术标准组装成轮对。
(2)重新组装:是以旧车轮和旧车轴(拼修)、旧车轮和新车轴(换轴)及新车轮和旧车轴(换轮)按厂修技术标准组装的轮对。
(3)检修:也称日常维修,它包括完成下列任何一项或全部的维修项目:①退轮检查;②旋修轮缘踏面、轴颈及防尘板座;③加修轴颈及防尘板座;④焊旋轮缘;⑤焊修轴端螺纹孔及中心孔(顶针孔)。
凡拼修、检修的轮对也包括堆焊轮缘、轴端丝扣、顶针孔等修理。
车辆段轮对检修包括:旋修踏面、轴颈及防尘板座;加修轴颈及防尘板座;焊旋轮缘。
一、轮对检修工艺过程
(一)车辆段轮对检修工艺过程
轮对段修时不换任何配件,它由车辆段轮轴工作组负责,其检修工艺过程如图2-40所示。车辆段轮轴工组使用的主要机械设备有车轮车床、车轴车床以及起重机、轮对冲洗机、超声波探伤仪(机)、电磁探伤器(机)、探伤用轮对支架(滚轮器)等。
(二)车轮厂轮对检修工艺过程
车轮厂(或车辆工厂的车轮车间)承担轮对的新组装、重新组装和检修任务。车轮厂轮对检修工艺过程如图2-41所示。
车轮厂实现上述修理工艺过程应具有的主要专用设备是:轮轴顶压机、立式车床、车轮车床、车轴车床、轮对冲洗机、自动堆焊机、直流弧焊机、超声波探伤仪(机)、电磁探伤器(机)、轮对转镐和各式起重机等。
目前,车轮厂和车辆段还配备了轮对动平衡机床,以适应车辆提速后轮对在高速状态下的动平衡的要求。

图2-40 车辆段滚动轴承轮对检修工艺过程
二、轮对检修的主要工序及技术要求
轮对各种修程中的各工序均应按预先规定的工艺规程及技术要求完成,并应符合《车辆轮轴组装检修及管理规则》的规定。
(一)轮对的外观检查、冲洗及轴身除锈
轮对在从转向架上分解下来后,应先进行外观检查,检查时可将车轴沿纵向分为3部分,并采用视线与车轴成45°夹角的三面检查法进行。对于容易发生裂纹或松弛的部位应敲打听音响,对透油、透锈、油层鼓泡、内距改变等迹象详细判断。此外,还应检查车轮踏面有无剥离、擦伤、裂损、碾宽、裂纹,车轴有无弯曲、磨伤、擦伤及电焊打伤。
轮对经外观检查后,应送入轮对冲洗除锈机用高压热水进行冲洗,冲洗水温应为70~80℃,冲洗时间应在5min以上。
轮对应用轴身除锈机进行轴身除锈,与冲洗同时进行,以免产生尘埃。为保证探伤质量,车轴各部位表面的油漆及锈垢必须彻底清除,车轴外露部位必须露出基本金属面(滚动轴承轮对如不退轴承或轴承内圈时,防尘板座及轮座外侧的外露部位除外)。
(二)轮对的尺寸测量
轮对在外观检查后必须测量各部尺寸,并按规定建立轮对卡片,确定施修范围。
应用第四种检查器、轮对内距尺、车轮直径尺、外卡钳、钢直尺及弧度样板测量轮对下述各部尺寸:轴颈直径、轴颈长度、轮座较原型减小量、轮座前肩弧度最小半径、轴颈后肩弧度最小半径、轮辋厚度、踏面圆周磨耗深度、擦伤及局部凹入深度、轮缘厚度、车轮直径及同一轮对轮径之差、轮对内侧距离及内距三处最大差和轮位差。测量时应将以上尺寸记录在轮对卡片上。
检查并记录轴端钢印,凡有下述任一情况者要进行超声波探伤:有轴箱滚动轴承轮对第一次组装时间达到4年,无轴箱滚动轴承轮对第一次组装时间40钢车轴达到5年,50钢车轴达到6年。每次施行段修及以上修程时,均必须对车轴施行全轴超声波穿透探伤检查;对车轴的轮座镶入部施行超声波探伤检查;滚动轴承轮对如不退轴承和轴承内圈时,均必须对车轴的轴颈卸荷槽部位施行超声波探伤检查;车辆颠覆或重车脱轨时,均必须对全车轮对的车轴施行全轴超声波穿透探伤检查和轮座镶入部超声波探伤检查。凡有下述任一情况时,须退轮检查:轮对无组装日期及组装单位责任钢印(进口轮对除外);经超声波探伤检查确认轮座上有裂纹或车轴上的裂纹延伸进轮座镶入部;车轴透声不良或难以判断;轮对内侧距离及内距三处差超过规定限度或轮对的轮位差超过规定限度时须退轴检查。

图2-41 车轮厂滚动轴承轮对检修工艺过程
经检查确认需要修理的轮对均应按表2-20的规定用白铅油或粉笔打上修程标记。
表2-20 轮对修程标记

(三)车轮的旋修
轮缘和踏面经一段时间的运用后,会发生磨耗或其他形式的损伤,因而使外廓标准形状遭到破坏。为了恢复轮缘和踏面的外廓标准形状,在厂、段修时必须对车轮进行经济合理的旋修。旋修时,车轮踏面及轮缘必须按磨耗型(LM型)踏面的外形加工及测量,车轮踏面及轮缘必须按不同的修程要求采用数控或仿形的方式加工(仅碾宽超限时,允许只旋除碾宽部分)。
凡车轮轮缘厚度不足26mm,轮缘垂直磨耗、裂纹、缺损、辗堆者;踏面缺损长度超过150mm或相对车轮轮缘外侧至缺损处的距离不足1508mm者;轮对内侧距离根据轮辋宽度小于最小内距1354mm或1350mm者;车轮外侧碾宽超过5mm以及踏面上粘有熔化金属者均施行旋修。
对于货车车轮踏面圆周磨耗超过5mm;踏面擦伤深度及局部凹下滚动轴承轮对超过0.5mm;踏面剥离长度滚动轴承轮对一处超过20mm,两处每处超过10mm(两处边缘距离须超过75mm);同一车轮直径差超过1mm,或同一车轮踏面与轴颈面的距离在同一直径线上测量的两点差超过2mm;未经旋修的同一轴相对车轮直径差超过3mm者施行旋修。
对于客车车轮踏面圆周磨耗快车超过4mm、其他客车超过5mm,踏面擦伤深度及局部凹下超过0.5mm,踏面剥离长度一处超过20mm、二处每处长超过10mm(25型车及双层客车段修时有剥离),同一车轮相互垂直的直径差超过0.5mm,未经旋修的同一轴相对车轮直径差超过3mm者施行旋修。25型客车及双层客车轮对内侧距离小于最小内距1350mm、三点差大于3mm、轮位差大于2mm时允许旋修车轮内侧面来调整,但旋修量须小于2mm。
轮缘内侧面如因辗制关系而厚度不匀时,应将内侧面加工削正,使其垂直于车轴中心线。
未经电焊的轮缘距顶点14mm以内,允许留有宽不超过5mm、深不超过1.2mm的残沟一圈。
轮缘和踏面经旋修后,其加工部位的表面粗糙度必须达到Ra=25μm,使用第四种检查器检查,轮缘厚度应为30~33mm,轮缘高度应为26~28mm。
旋修后,同一轴相对车轮直径之差不得超过1mm;同一车轮相互垂直的直径差不得大于0.5mm。
(四)车轴的旋修
1.轴身的旋修
车轴轴身的打痕、碰伤、磨伤及电焊打火深度在2.5mm及以上或轴身弯曲时,须将缺陷旋除,旋除后的轴身(包括轴中央部)尺寸允许比原型公称尺寸减少4mm,其表面粗糙度必须达到Ra6.3μm。
2.滚动轴承车轴轴颈及防尘板座的旋修
轴颈(包括卸荷槽)及防尘板必须采用数控或仿形的方式加工。轴颈降等级时必须采用磨削的方法进行终加工;轴颈卸荷槽和防尘板座可采用磨削或车削的方法加工,轴颈卸荷槽经磨削加工后,表面必须进行滚压处理。
轴颈端部不允许存在墩粗的情况,否则应修复;轴颈端部引导斜坡处有碰伤时,允许消除局部高于原表面的堆积金属,并用00号砂布蘸油打磨光滑后使用。
防尘板座端面存在锈蚀或局部碰伤时,允许消除局部高于原表面的金属,并用00号砂布蘸油打磨光滑后使用。
车轴皮带轮安装座表面存在锈蚀或局部碰伤时,允许消除局部高于原表面的金属,并用00号砂布蘸油打磨光滑后使用。检修的车轴其皮带轮安装座直径允许比原型公称尺寸减小0.5mm。
3.轴端中心孔、轴端螺栓孔的检修
轴端中心孔必须逐个检查,中心孔有损伤时,允许消除局部高于原表面的金属,但修复后缺陷面积不得大于原中心孔圆锥面积的1/8。
轴端中心孔允许堵焊,焊后重新加工。加工后各部尺寸必须符合图纸规定,并应测量车轮踏面与轴颈面在同一直径线上的距离差,其差值不得超过0.6mm。
轴端螺栓孔有损伤或滑扣时,累计不得超过3扣(不得连续),毛刺必须消除;螺纹磨损时,必须用止规测试,在距端面5扣以内止住,并且用手试止规不得有明显晃动。
轴端螺栓孔不能使用时,允许将原螺栓孔堵焊,并移位60°加工。堵焊螺栓孔前必须清除螺栓孔内的铁削及杂物,将螺杆前端车制成120°角后旋入螺栓孔中,后端距车轴端面为2~4mm,然后再堵焊,并做修平处理。轴端螺栓孔只允许移位加工一次。轴端螺纹不能使用时,该车轴不再使用。
(五)检验
轮对检修完毕后,须有专人负责,按厂修或段修的规程及轮对组装及检修规则的要求进行检验,经检查验收后方准装车使用。
检查合格的轮对,还须在轴身及车轮表面(踏面和轮辋内、外侧面除外)均匀涂刷醇酸清漆。