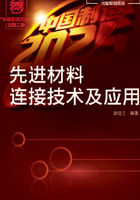
2.1 陶瓷材料的性能特点及连接问题
陶瓷是指以各种金属的氧化物、氮化物、碳化物、硅化物为原料,经适当配料、成形和高温烧结等合成的无机非金属材料。陶瓷具有许多独特的性能,这类材料一般是由共价键、离子键或混合键结合而成,键合力强,具有很高的弹性模量和硬度。
陶瓷材料按其应用特性分为功能陶瓷和工程结构陶瓷两大类。功能陶瓷是指具有电、磁、光、声、热等功能以及耦合功能的陶瓷材料,从性能上分有铁电、压电、光电、声光、磁光、生物等功能陶瓷。工程结构陶瓷强调材料的力学性能,以其具有的耐高温、高强度、超硬度、高绝缘性、高耐磨性、抗腐蚀性等性能,在工程领域得到广泛应用。常见的工程结构陶瓷见表2.1。
表2.1 常见的工程结构陶瓷

2.1.1 结构陶瓷的性能特点
2.1.1.1 物理和化学性能
陶瓷材料的物理性能与金属材料有较大的区别,主要表现在以下几个方面:陶瓷的线胀系数比金属低,一般在10-5~10-6K-1的范围内;陶瓷的熔点(或升华、分解温度)比金属的高得多,有些陶瓷可在2000~3000℃的高温下工作且保持室温时的强度,而大多数金属在1000℃以上就基本上丧失了强度。一些新型的特殊陶瓷具有特定条件下的导电性能,如导电陶瓷、半导体陶瓷、压电陶瓷等。还有一些陶瓷具有特殊的光学性能,如透明陶瓷、光导纤维等,但它们主要是功能陶瓷而不是结构陶瓷。
陶瓷的组织结构十分稳定,具有良好的化学性能。在它的离子晶体中,金属原子被非金属(氧)原子所包围,受到非金属原子的屏蔽,因而形成极为稳定的化学结构。一般情况下不再与介质中的氧发生作用,甚至在1000℃的高温下也不会氧化。由于化学结构稳定,大多数陶瓷具有较强的抵抗酸、碱、盐类的腐蚀以及抵抗熔融金属腐蚀的能力。
2.1.1.2 力学性能
陶瓷材料多为离子键构成的晶体(如Al2O3)或共价键组成的共价晶体(如Si3N4、SiC),这类晶体结构具有明显的方向性。多晶体陶瓷的滑移系很少,受到外力时几乎不能产生塑性变形,常常发生脆性断裂,抗冲击能力较差。由于离子晶体结构的关系,陶瓷的硬度和室温弹性模量也都较高。陶瓷内部存在大量的气孔,致密度比金属差很多,因此抗拉强度不高,但因为气孔在受压时不会导致裂纹扩展,所以陶瓷的抗压强度还是比较高的。脆性材料铸铁的抗拉强度与抗压强度之比一般为1/3,而陶瓷则为1/10左右。
陶瓷是非常坚固的离子/共价结合(比金属键更强)组织,这种结合使陶瓷具有相关的特性:高硬度,高压缩强度,低导热、导电性及化学不活泼性。这种坚固的结合也表现出一些不好的特性,如低延伸性。通过控制显微组织可以克服陶瓷固有的高硬度并制出陶瓷弹簧。已经开发应用的复合陶瓷,其断裂韧性可达钢的一半。
陶瓷更广泛的特性可能并没有被认识到。人们一般认为陶瓷是电/热绝缘体,而陶瓷氧化物(以Y-Ba-Cu-O为基)却具有高温超导性。金刚石、氧化铍和碳化硅比铝或铜有着更高的导热性。
2.1.1.3 几种常用的结构陶瓷
(1)氧化物陶瓷
常用的氧化物陶瓷有氧化铝陶瓷、氧化铍陶瓷和部分稳定氧化锆陶瓷等。表2.2所示是常用的几种氧化物陶瓷的物理性能。
表2.2 几种氧化物陶瓷的物理性能

1)氧化铝陶瓷
氧化铝陶瓷是工程中广泛应用的陶瓷材料,氧化铝陶瓷主要成分是Al2O3和SiO2。Al2O3含量越高性能越好,但工艺更复杂,成本也更高。几种氧化物陶瓷的化学组成见表2.3。
表2.3 几种氧化物陶瓷的化学组成%

氧化铝有十多种同素异构体,常见的主要有三种:α-Al2O3,β-Al2O3和γ-Al2O3。
γ-Al2O3属于尖晶石型立方结构,高温下不稳定。在1600℃转变为α-Al2O3。α-Al2O3在高温下十分稳定,在达到熔点2050℃之前没有晶型转变。
氧化铝陶瓷的主要性能特点是硬度高(760℃时硬度为87HRA,1200℃仍可保持82HRA的硬度),有很好的耐磨性、耐腐蚀性、耐高温性能,可在1600℃高温下长期使用。氧化铝陶瓷还具有良好的电气绝缘性能,在高频下的电绝缘性能尤为突出,每毫米厚度可耐压8000V以上。氧化铝陶瓷的缺点是韧性低,抗热振性能差,不能承受温度的急剧变化。这类陶瓷主要用于制造刀具、模具、轴承、熔化金属的坩埚、高温热电偶套管,以及化工行业中的一些特殊零部件,如化工泵的密封滑环、轴套和叶轮等。
2)部分稳定氧化锆(ZrO2)陶瓷
氧化锆陶瓷有三种晶型:四方结构(t相)、立方结构(c相)和单斜结构(m相)。加入适量的稳定剂后,四方结构(t相)在室温以亚稳定状态存在,称为部分稳定氧化锆(简称PSZ)。部分稳定氧化锆陶瓷可应用于发动机的结构件,其抗弯强度在600℃时可达981MPa。
在应力作用下发生的四方结构(t相)向单斜结构(m相)的马氏体转变称为“应力诱发相变”,在相变过程中吸收能量,使陶瓷内裂纹尖端的应力场松弛,增加了裂纹的扩展阻力,实现氧化锆陶瓷的增韧。部分稳定氧化锆陶瓷的断裂韧性远高于其他的结构陶瓷。目前发展起来的几种氧化锆陶瓷中,常用的稳定剂包括MgO、Y2O3、CaO、CeO2等。
① 高强度氧化锆陶瓷(MG-PSZ) 抗弯强度为800MPa,断裂韧性为10MPa·m1/2。抗振型MG-PSZ的抗弯强度为600MPa,断裂韧性为8~15MPa·m1/2。
② 四方多晶氧化锆陶瓷(Y-TZP) 以Y2O3为稳定剂,抗弯强度可达800MPa,最高可达1200MPa,断裂韧性可达10MPa·m1/2以上。
③ 四方多晶ZrO2-Al2O3复合陶瓷 利用Al2O3的高弹性模量可使多晶氧化锆陶瓷晶粒细化,硬度提高,四方结构的t相含量增加,可以提高陶瓷的强度和韧性。用热压烧结方法制造的ZrO2-Al2O3复合陶瓷的抗弯强度可高达2400MPa,断裂韧性可达17MPa·m1/2。
(2)非氧化物陶瓷
包括氮化硅(Si3N4)、碳化硅(SiC)、氮化硼(BN)与氮化钛(TiN)等。碳化硼(B4C)在工程材料中的硬度仅次于金刚石和立方氮化硼,用于需要高耐磨性能的部件。由于非氧化物陶瓷在高温下仍具有高强度、超硬度、抗磨损、耐腐蚀等性能,已成为机械制造、冶金和宇航等高科技领域中的关键材料。
几种非氧化物陶瓷的物理性能和力学性能见表2.4。
表2.4 几种非氧化物陶瓷的物理性能和力学性能

① 氮化硅陶瓷 六方晶系,以Si3N4为结构单元,具有极强的共价键性,有α-Si3N4和β-Si3N4两种晶体。氮化硅陶瓷的特点是强度高,反应烧结氮化硅陶瓷的室温抗弯强度达200MPa,在1200~1350℃高温下可保证强度不衰减。热压烧结氮化硅陶瓷室温抗弯强度可高达800~1000MPa,加入某些添加剂后抗弯强度可达到1500MPa。氮化硅陶瓷的硬度很高,仅次于金刚石、立方氮化硼和碳化硼等。用氮化硅陶瓷制造的发动机可以在更高的温度下工作,使发动机的燃料充分燃烧,提高热效率,减少能耗与环境污染。
② 碳化硅陶瓷 具有高的热传导性、高耐蚀性和高硬度,是一种键能很高的共价键化合物,具有金刚石的结构类型。常见的碳化硅晶型为2100℃以下稳定存在的立方结构β-SiC和2100℃以上稳定存在的六方结构α-SiC。在压力为101.33MPa时,碳化硅在2830℃左右分解。碳化硅陶瓷的特点是高温强度高,在1400℃时抗弯强度仍保持在500~600MPa的较高水平。碳化硅陶瓷具有很好的耐磨损、耐腐蚀、抗蠕变性能。由于碳化硅陶瓷具有高温强度高的特点,可用于制造火箭尾喷管的喷嘴、浇注金属用的喉嘴、热电偶套管、加热炉管以及燃气轮机的叶片、轴承等,还可用于热交换器、耐火材料等。
③ 赛隆陶瓷(Sialon) 由Si3N4和Al2O3构成的陶瓷称为赛隆陶瓷,其成形和烧结性能优于纯Si3N4陶瓷,物理性能与β-Si3N4相近,化学性能接近Al2O3。这种陶瓷可以采用热挤压、模压、浇注等技术成形,在1600℃常压无活性气氛中烧结即可达到热压氮化硅陶瓷的性能,是目前常压烧结强度最高的陶瓷材料。近年来赛隆陶瓷得到了较快的发展。
(3)陶瓷复合材料
提高陶瓷材料性能的方法之一是制作陶瓷基复合材料。加入其他化合物或金属元素形成的复合Al2O3陶瓷,可改善氧化物陶瓷的韧性和抗热震性。几种氧化铝复相陶瓷与热压氧化铝陶瓷的力学性能见表2.5。由于分散的第二相可阻止Al2O3晶粒长大,又可阻碍微裂纹扩展,因此复相陶瓷的抗弯强度明显提高。含5%(体积含量)SiC的Al2O3复相陶瓷的抗弯强度可达1000MPa以上,断裂韧性提高到4.7MPa·m1/2。
表2.5 热压Al2O3陶瓷及其复相陶瓷的力学性能

陶瓷可作为复合物系统(如玻璃钢GRP)和金属基复合材料(如氧化铝强化的Al/Al2O3)的增强剂,即将陶瓷纤维、晶须或颗粒混入陶瓷基体材料中。使基体和加入的材料保持固有的性能,而陶瓷复合材料的综合性能远远超过单一材料本身的性能。
陶瓷复合材料主要分为纤维增强和晶须或颗粒增强复合材料两大类。
① 纤维增强陶瓷复合材料 纤维是连续的或接近连续的细丝,在保持或提高强度的同时能增强韧性和抗高温性能。可以做成纤维的材料有Al2O3、SiC、Si3N4等。但是,陶瓷基体加入纤维后很难进行加工,许多靠纤维增强的陶瓷复合材料就因为纤维分布不均匀、加工(焊接)后纤维性能下降或基体密实性不足等原因而达不到提高性能的目的。
② 晶须或颗粒增强陶瓷复合材料 晶须是短小的单晶体纤维,无论是棒状或针状,其纵横比约为100,直径小于3μm。以SiC晶须增强的Al2O3陶瓷复合材料已经引起广泛地关注。将SiC晶须加入单一的Al2O3陶瓷或多元基体中,能使材料的强度和断裂韧性提高很多,而且还具有优异的抗热震性、耐磨性和抗氧化性。以ZrO2韧化的Al2O3系列陶瓷复合材料是以弥散分布的部分稳定的ZrO2颗粒来提高Al2O3陶瓷基体的强度和韧性。
陶瓷由于具有良好的介电性、耐热性、真空致密性、耐腐蚀性等,在工程技术中得到广泛应用。它具有持久的热稳定性,耐各种介质的浸蚀性,具有严格的电绝缘性能和绝磁性能,具有很广阔的应用前景。
2.1.1.4 复合陶瓷的制备方法
可采用多种方法制备复合陶瓷。复合陶瓷的制备工艺过程为:配料→混粉→压制成形→烧结。以Al2O3-TiC复合陶瓷为例,在烧结过程中,由于Al2O3和TiC之间会发生反应并有气体发生,因此烧结比较困难。一般需添加烧结助剂、表面处理或热压烧结(hot-pressing sintering,HP)、热等静压烧结(hot-isostatic-pressing sintering,HIP)工艺。烧结是使材料获得预期的显微结构,赋予材料各种性能的关键工序。可将Al2O3-TiC复合陶瓷按烧结方式的不同进行分类。
(1)无压烧结(pressureless sintering,PS)
无压(常压)烧结是指烧结过程中烧结坯体无外加压力、只在常压下烧结。由于Al2O3和TiC在高温下会发生反应产生气体,用常规烧结方法难以致密化(相对密度<94%),为了促进烧结,常在Al2O3-TiC体系中添加各种助烧剂,如TiH2、MgO、CaO、Y2O3、Cr2O3等,并采取快速升温、埋粉等方法,可使烧结体的相对密度达到98%。这种烧结方法可在烧结过程中形成有利于致密化的液相,抑制晶粒异常长大,使材料显微结构均匀。无压烧结可连续作业,生产成本低,产品形状和尺寸不受限制。烧结助剂对Al2O3-TiC复合陶瓷性能的影响见表2.6。
表2.6 烧结助剂对Al2O3-TiC基复合陶瓷性能的影响

(2)热压烧结(hot-pressing sintering,HP)
热压烧结是在加热烧结的同时施加足够大的压力来促进烧结。由于同时加温、加压,有利于粉末颗粒的接触、扩散和流动等传质过程,可降低烧结温度、缩短烧结时间和抑制晶粒长大;不需添加助烧剂,容易获得接近理论密度、气孔率接近零的烧结体。由于热压烧结对粉体的推动力比常压烧结推动力大20~100倍,用常压烧结可以烧结的材料,若用热压烧结,其烧结温度可以降低100~150℃。但热压烧结时材料的形状和尺寸受到限制,不能批量生产,成本也较高。热压工艺对Al2O3-TiC复合陶瓷性能的影响见表2.7。
表2.7 热压Al2O3-TiC基复合陶瓷的性能

(3)自蔓延高温合成法(self-propagating high temperature synthesis,SHS)
利用反应物之间化学反应热的自加热和自传导作用来合成材料的技术。自蔓延高温合成法制备复合陶瓷是以石墨、TiO2粉、Al粉为原料,按反应式3TiO2+4Al+3C3TiC+2Al2O3的配比混合,燃烧的粉末间发生反应时放出大量的热,来维持反应的进行直至蔓延完毕。该方法工艺简单,节能省时,而且可合成传统工艺难以合成的非平衡相、中间产物。该方法反应不易控制,产物疏松多孔,但若同时加压可一步合成致密陶瓷,是未来合成复合材料的一种重要工艺。
(4)放电等离子烧结(spark plasma sintering,SPS)
放电等离子烧结是一种新的烧结技术,具有升温速度快、烧结时间短、晶粒均匀、有利于控制烧结体的结构、获得的材料致密度高等特点。烧结时将Al2O3与TiC粉末按一定配比混合后放在容器内,在高压下,利用直流脉冲电流直接通过模具进行加热,使粉末瞬间处于高温状态,只需几分钟就能完成制备过程。由于制备时间短,可降低生产成本。
(5)其他制备方法
制备复合陶瓷的其他烧结方法还有:热等静压烧结(hot-isostatic-pressing sintering,HIP)、气压烧结(gas pressure sintering,GPS)、多步烧结法(multi-step sintering,MS)等。热等静压烧结是将粉末压坯放入高压容器中,使粉料在加热过程中经受各向均衡的气体压力,使材料致密化。利用该技术制备的Al2O3-TiC复合陶瓷致密度高,性能优异,但其设备比较复杂昂贵。气压烧结法可以抑制反应物的挥发、分解,烧结温度较高。TiC的含量不能太高,当超过30%时,Al2O3-TiC复合陶瓷的致密度和性能都较低。用该法可制备形状较复杂的部件,制得的材料性能较热压法和热等静压法略低。多步烧结即先无压烧结或自蔓延高温合成粉末再经热等静压或热压烧结等,该方法使用的助烧剂较少,所制备的材料性能可接近热压法制备的,但工艺时间较长。以上几种方法成本都较高。
制备方法对复合陶瓷的力学性能有很大的影响。例如,用不同方法制备的Al2O3-TiC复合陶瓷的常温力学性能见表2.8。可见,无压烧结法制得的材料性能较差;热等静压烧结的材料强度好于其他制备方法;自蔓延高温合成法烧结的材料强度不如热压烧结和气压烧结材料;自蔓延高温合成法+热压烧结(或热等静压烧结)制备的Al2O3-TiC陶瓷综合性能较好,材料强度、硬度和韧性比单种制备方法制得的材料要好。
表2.8 不同工艺制备的Al2O3-TiC基复合陶瓷的性能

注:PS为无压烧结;HP为热压烧结;SHS为自蔓延高温合成;GPS为气压烧结;HIP为热等静压烧结。
Al2O3-TiC复合陶瓷常被用作高速切削刀具或高温发热体,所以其热稳定性能至关重要。对Al2O3-TiC陶瓷高温抗氧化性能的研究表明,Al2O3-TiC复合陶瓷在400℃时发生微量氧化。当温度T<900℃时,氧化过程中相界面反应生成了脆性TiO2,氧化增量与时间的关系式为:1-(1-α)2/3=Kt。当温度为900~1100℃时,氧化机制转变为抛物线型,氧化增量与时间的关系式为:α2=Kt。
2.1.2 陶瓷与金属连接的基本要求
工程陶瓷材料由于具有高强度、耐腐蚀、低导热及高耐磨等优良性能,在航空航天、机械、冶金、化工、电子等方面有广阔的应用前景。但陶瓷材料固有的硬脆性使其难以加工、难以制成形状复杂的构件,在工程应用上受到很大限制。推进陶瓷实用化的方法之一是将其与塑韧性高的金属材料连接制成复合构件,发挥两种材料的性能优势,弥补各自的不足。因此焊接是陶瓷推广应用的关键技术之一。
(1)陶瓷连接的形式
陶瓷材料的加工性能差,塑性和冲击韧性低,耐热冲击能力弱,制造尺寸大而形状复杂的零件较为困难,因此陶瓷通常都是与金属材料一起组成复合结构来应用。当陶瓷与金属材料成功连接时,陶瓷将给部件提供附加功能并改善其应用性能。所以陶瓷与金属材料之间的可靠连接是推进陶瓷材料应用的关键。
焊接是陶瓷在生产中应用的一种重要的加工形式。例如,在核工业和电真空器件生产中,陶瓷与金属的焊接占有非常重要的地位。陶瓷材料的连接有如下几种形式:
① 陶瓷与金属材料的连接;
② 陶瓷与非金属材料(如玻璃、石墨等)的连接;
③ 陶瓷与半导体材料的连接。
(2)对接头性能的要求
应用较多的是陶瓷与金属材料的焊接,这种焊接结构在电器、电子器件、核能工业、航空航天等领域的应用逐渐扩大,对陶瓷与金属接头性能的要求也越来越高。对陶瓷与金属接头性能的总体要求如下:
① 陶瓷与金属的焊接接头必须具有较高的强度,这是焊接结构件的基本性能要求;
② 焊接接头必须具有真空的气密性;
③ 接头的残余应力应最小,在使用过程中应具有耐热性、耐腐蚀性和热稳定性;
④ 焊接工艺应尽可能简化,工艺过程稳定,生产成本低。
2.1.3 陶瓷与金属连接存在的问题
由于陶瓷材料与金属原子结构之间存在本质上的差别,加上陶瓷材料本身特殊的物理化学性能,因此,无论是与金属连接还是陶瓷本身的连接都存在不少问题。当陶瓷与金属连接时,为了实现两者的可靠结合,需要在连接材料之间做一个界面。这个界面材料应符合以下几点要求:
① 界面材料与被焊材料有相近的线胀系数;
② 合理的结合类型,也就是离子/共价键结合;
③ 陶瓷与金属间晶格的错配。
陶瓷与金属材料焊接中出现的主要问题如下:
(1)陶瓷与金属焊接中的热膨胀与热应力
陶瓷的线胀系数比较小,与金属的线胀系数相差较大,通过加热连接陶瓷与金属时,热胀冷缩使接头区产生很大的残余应力,削弱接头的力学性能;热应力较大时还会产生裂纹,导致连接陶瓷接头的断裂破坏。
控制应力的方法之一是在焊接时尽可能地减少焊接部位及其附近的温度梯度,控制加热和冷却速度,降低冷却速度有利于应力松弛而使应力减小。另一个减小应力的办法是采用金属中间层,使用塑性材料或线胀系数接近陶瓷线胀系数的金属材料。
(2)陶瓷与金属很难润湿
陶瓷材料润湿性很差,或者根本就不润湿。采用钎焊或扩散焊的方法连接陶瓷与金属材料,由于熔化的金属在陶瓷表面很难润湿,因此难以选择合适的钎料与基体结合。为了使陶瓷与金属达到钎焊连接的目的,最基本条件之一是使钎料对陶瓷表面产生润湿,或提高对陶瓷的润湿性,最后达到钎焊连接。例如,采用活性金属Ti在界面反应形成Ti的化合物,可获得良好的润湿性。
在陶瓷连接过程中,也可在陶瓷表面进行金属化处理(用物理或化学的方法覆上一层金属),然后再进行陶瓷与陶瓷或陶瓷与金属的连接。这种方法实际上就是把陶瓷与陶瓷或陶瓷与金属的连接变成了金属之间的连接,但是这种方法的结合强度不高,主要用于密封的焊缝。
(3)易生成脆性化合物
由于陶瓷和金属的物理化学性能差别很大,连接时界面处除存在键型转换以外,还容易发生各种化学反应,在结合界面生成各种碳化物、氮化物、硅化物、氧化物以及多元化合物等。这些化合物硬度高、脆性大,是产生裂纹和造成接头脆性断裂的主要原因。
确定界面脆性化合物相时,由于一些轻元素(C、N、B等)的定量分析误差很大,需制备多种试样进行标定。多元化合物的相结构确定一般通过X射线衍射方法和标准衍射图谱进行对比,但有些化合物没有标准图谱,使物相确定有一定的难度。
(4)陶瓷与金属的结合界面
陶瓷与金属接头在界面间存在着原子结构能级的差异,陶瓷与金属之间是通过过渡层(扩散层或反应层)而结合的。两种材料间的界面反应对接头的形成和组织性能有很大的影响。接头界面反应和微观结构是陶瓷与金属焊接研究中的重要课题。
陶瓷材料主要含有离子键或共价键,表现出非常稳定的电子配位,很难被金属键的金属钎料润湿,所以用通常的熔焊方法使金属与陶瓷产生熔合是很困难的。用金属钎料钎焊陶瓷材料时,要么对陶瓷表面先进行金属化处理,对被焊陶瓷的表面改性,或是在钎料中加入活性元素,使钎料与陶瓷之间有化学反应发生,通过反应使陶瓷的表面分解形成新相,产生化学吸附机制,这样才能形成牢固的陶瓷与金属结合的界面。
2.1.4 陶瓷与金属的连接方法
陶瓷与金属之间的连接方法,包括机械连接、粘接和焊接。常用的焊接方法主要有钎焊连接、扩散连接、电子束焊、激光焊等,见表2.9。
表2.9 陶瓷与金属的连接方法

陶瓷与金属直接进行焊接的难度很大,采用一般的熔焊方法很难实现,甚至不能进行直接焊接。因此,陶瓷与金属焊接须采取特殊的工艺措施,使金属能润湿陶瓷或与之发生化学反应。金属对陶瓷的润湿与金属和陶瓷之间的化学反应,以及连接过程中两者热胀冷缩的差异和所造成的热应力,甚至引起开裂等,是陶瓷与金属连接时的主要问题。
(1)陶瓷与金属钎焊连接
陶瓷-金属连接中应用最多的是钎焊连接,一般分为间接钎焊和直接钎焊。陶瓷与金属钎焊方法的分类、原理及适用材料见表2.10。
表2.10 陶瓷-金属钎焊方法的分类、原理及适用材料

间接钎焊(也称为两步法)是先在陶瓷表面进行金属化,再用普通钎料进行钎焊。陶瓷表面金属化的方法最常用的是Mo-Mn法,此外还有物理气相沉积(PVD)、化学气相沉积(CVD)、热喷涂法以及离子注入法等。间接钎焊工艺复杂,应用受到一定限制。
直接钎焊法(也称为一步法)又叫活性金属化钎焊法,是在钎料中加入活性元素,如过渡金属Ti、Zr、Hf、Nb、Ta等,通过化学反应使陶瓷表面发生分解,形成反应层。反应层主要由金属与陶瓷的化合物组成,这些产物大多表现出与金属相同的结构,因此可以被熔化的金属润湿。直接钎焊法可使陶瓷结构件的制造工艺变得简单,成为近年来研究的热点之一。直接钎焊陶瓷的关键是使用活性钎料,在钎料能够润湿陶瓷的前提下,还要考虑高温钎焊时陶瓷与金属线胀系数的差异是否会引起裂纹。在陶瓷和金属之间插入中间缓冲层可有效降低应力,提高接头强度。直接钎焊的局限性在于接头的高温强度较低以及大面积钎焊时钎料的铺展问题。
(2)固态扩散连接
固态扩散连接一般分为直接和间接两种形式,主要是采用真空扩散焊,也有采用热等静压法扩散连接的。陶瓷与金属固相连接方法的分类、原理及适用材料见表2.11。
表2.11 陶瓷-金属固相连接方法的分类、原理及适用材料

固态扩散连接是陶瓷-金属连接常用的方法,是指在一定的温度和压力下,被连接表面相互接触,通过使接触面局部发生塑性变形,或通过被连接表面产生的瞬态液相而扩大被连接表面的物理接触,然后结合层原子间相互扩散而形成整体可靠连接的过程。其显著特点是接头质量稳定、连接强度高、接头高温性能和耐腐蚀性能好。
固相扩散焊中,连接温度、压力、时间及焊件表面状态是影响扩散焊接质量的主要因素。固相扩散连接中界面的结合是靠塑性变形、扩散和蠕变机制实现的,其连接温度较高,陶瓷-金属固相扩散连接温度通常为金属熔点的90%。由于陶瓷和金属的线胀系数和弹性模量不匹配,易在界面附近产生很大的应力,很难实现直接固相扩散连接。为缓解陶瓷与金属接头残余应力以及控制界面反应,抑制或改变界面反应产物以提高接头性能,常采用加中间层的扩散焊。
(3)陶瓷与金属的熔化焊
高熔点和陶瓷高温分解使陶瓷和金属的连接采用一般的熔化焊方法较困难。采用熔化焊方法虽然速度快,效率高,可以形成高温下性能稳定的连接接头,但是为了降低焊接应力,防止裂纹的产生,必须采用辅助热源进行预热和缓冷,而且工艺参数难以控制,设备投资昂贵。
陶瓷与金属的熔化焊方法主要包括电子束焊、激光焊、电弧焊等。因为陶瓷材料极脆,塑、韧性很低,使其熔化焊受到很大限制。陶瓷与金属熔化焊的方法、原理及适用材料见表2.12。
表2.12 陶瓷-金属熔化焊方法、原理及适用材料

陶瓷与金属连接的钎焊法、扩散连接方法比较成熟,应用也较为广泛;电子束焊和激光焊也正在扩大其应用。此外,陶瓷与金属的连接还可采用超声波压接焊、摩擦压接焊等方法。