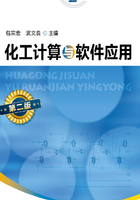
2.4 含化学反应过程
典型的化工生产装置是以反应器为核心,配置分离设备、流体输送设备、换热设备等构成的一个化工过程。在反应器内,伴随着反应物分子重新组合成新物质的过程,会出现能量的消耗、释放和转化。反应物质量变化的数量关系可从物料衡算中求得,能量的变化数量关系则可从能量衡算中求得。
在化学反应过程中,反应物在反应器内通过化学反应转化为产物。由于化学反应种类繁多、机理各异,物料衡算工作量要比单纯物理分离过程大得多。手工计算时,根据化学反应方程式,按照实验得到或其他生产装置得到的反应物转化率、收率、选择性等参数,进行化工单元操作过程(或单个设备)的物料衡算,然后将各个过程汇总得到整个流程的物料衡算,进而完成物料流程图。软件模拟计算时,也需要告诉软件相关的化学反应资料,如化学反应方程式、反应动力学数据、反应器尺寸、反应的转化率、选择性与收率等参数。若工艺过程中多于一个反应器,或一个反应器中多于一个化学反应,则要求对每一设备中的各个反应方程式、化学反应平衡常数、反应动力学参数仔细填写清楚。为保证目的产品组分的产率和选择性,操作者必须了解特定反应过程的特点,选择适宜的反应器类型,熟悉模拟软件中可获得的反应器模块类型以及它们在过程模拟中的应用,保证模拟的正确性。
2.4.1 含反应器的组合流程
对于一个包含反应器、分离设备、流体输送设备、换热设备的组合流程的工艺设计,物料衡算将非常复杂。手工计算时,要通盘考虑,运算要非常小心,步步为营,一有错误就得从头开始。使用软件进行复杂工艺的物料衡算,工作量将大大降低。要求操作者对工艺过程要有充分的了解,能正确选取模块,能准确设置模块参数。在软件运行错误时,能应用化工基础理论知识和软件知识,对各模块的中间数据进行分析,找出错误的原因,用较短时间打通流程,得到正确的物料衡算结果。
例2-9 甲烷水蒸气重整制氢——Calculator+Sensitivity功能的综合使用。
甲烷在高温高压下与水蒸气反应,生成一氧化碳和氢气,反应方程式为:CH4+H2O→3H2+CO。已知原料甲烷温度65.6℃,压力62bar,原料水常压、20℃。两股原料混合后预热到593℃、加压到58.6bar入重整反应器,反应温度788℃,反应器压降1.4bar。设水蒸气摩尔流率是甲烷的4倍,甲烷的转化率为0.995。当甲烷摩尔流率从100kmol/h增加到500kmol/h时,求反应器的热负荷变化。
解 用Aspen Plus软件的计算器功能设置两原料的比例,用灵敏度功能计算反应器的热负荷变化。
① 全局性参数设置 计算类型“Flowsheet”,选择SI-CBAR计量单位集,输入反应前后的所有组分。本例混合物中含极性组分,且涉及高温高压气相反应,选择“PENG-ROB”性质方法。
② 画流程图 按题目介绍内容绘制模拟流程,如图2-63所示。以甲烷进料量100kmol/h为基准,水量400kmol/h,将题目给定的进料物流信息填入对应栏目中。

图2-63 甲烷、水蒸气重整反应流程
③ 设置模块信息 “HEAT”模块按题给信息填写即可。反应器模块有两个页面需要填写,第一个页面是填写反应的温度、压力,第二个页面填写反应方程式与转化率,按题给信息填写即可。至此,两个模块模拟计算需要的信息已经全部设置完毕,计算结果见图2-64,本次计算未考虑甲烷进料量的变化。

图2-64 重整反应初步计算结果
④ 计算器设置 要使进料组分的流率在模拟过程中连续自动变化,可以应用软件的计算器功能。在本题中,把甲烷流率设置为自变量,水蒸气流率是因变量,保持水蒸气流率是甲烷流率的4倍。在“Flowsheeting Options|Calculator”子目录,建立一个模拟对象文件“C-1”,在此文件中定义两个变量“FCH4”和“FH2O”,分别表示甲烷和水的流率。其中甲烷流率“FCH4”是输入变量“Inport variable”,水的流率“FH2O”是输出变量“Export variable”。甲烷变量的定义方式见图2-65,水的变量定义方式类似。在“Calculate”页面,用Fortran语言编写一句话,说明水摩尔流率与甲烷摩尔流率的关系,见图2-66。

图2-65 定义甲烷变量

图2-66 说明水与甲烷的摩尔流率关系
⑤ 求反应器热负荷变化 在“Model Analysis Tools|Sensitivity”子目录,建立一个模拟对象文件“S-1”。在此文件中定义三个变量“DUTY”、“FCH4”、“FH2O”。其中“DUTY”表示反应器的热负荷,定义方式如图2-67,变量“FCH4”、“FH2O”的定义方式与在计算器文件“C-1”中相同。在“Vary”页面,定义甲烷流率的变化范围,如图2-68所示,然后指定灵敏度计算结果的数据输出。模拟结果见图2-69,可见甲烷、水蒸气流率变化时,反应器热负荷跟着变化。

图2-67 定义反应器的热负荷

图2-68 定义甲烷流率的变化

图2-69 甲烷水蒸气重整制氢反应器模拟结果
例2-10 硫黄回收——Claus+SCOT硫黄回收燃烧炉-废热锅炉计算。
在Claus+SCOT硫黄回收工艺中,通常采用高温燃烧、二级转化反应生成硫黄。在燃烧炉内,含硫化氢酸性气部分燃烧,产生的高温气体被引入废热锅炉中产生4MPa的蒸汽供工厂使用,工艺流程如图2-70所示。

图2-70 Claus+SCOT硫黄回收燃烧炉工艺流程
燃烧炉内化学反应复杂,现考虑7个主要反应,见例2-10附表1。其中,S2为元素硫的二聚体,其参数为:PC12.6005MPa,TC1198K,VC112.9768(cc/mol),ZC 0.1429,OMEGA 0.3413。已知进入废热锅炉的软水温度104℃、压力4MPa,求产生的蒸汽流率。原料气和空气的数据见例2-10附表2。
例2-10附表1 硫黄回收过程燃烧炉内的化学反应

例2-10附表2 原料气和空气的组成

解 ① 全局性参数设置 计算类型“Flowsheet”,输入反应前后的所有组分。在“Properties|Parameters|Pure Components|REVIEW-1”页面的S2栏目内,手工输入S2的物性数据,如图2-71所示。本题涉及高温高压气相反应,选择“PENG-ROB”性质方法。

图2-71 手工输入S2的物性数据
② 设置流股信息 把例2-10附表2给定的进料物流信息填入对应栏目中。废热锅炉的软水进料流率填入估计值后使用“Design Specs”功能调整软水进料流率。
③ 设置模块信息 所有模块工艺参数按工艺流程图2-70上的信息填写。反应器模块有两个页面需要填写,第一个页面是填写反应的温度、压力,第二个页面填写反应方程式与转化率,按例2-10附表1上的题给信息填写即可,如图2-72所示。废热锅炉“E61101”模块需要两个物性选项,壳程走高温流体,仍然用PENG-ROB方程;管程走高压软水,选用水蒸气表“STEAM-TA”性质方法。

图2-72 填写反应器模块中的反应方程式
④ 模拟计算 初步计算结果显示水蒸气的汽化分率为0.87,未达饱和,说明软水进料流率需要降低。使用“Design Specs”功能调整后的结果见图2-73,由图2-73可知,可以生产4MPa水蒸气22436kg/h。

图2-73 反馈计算废热锅炉产蒸汽量
2.4.2 反应精馏过程
反应精馏是把反应过程和精馏过程耦合在一个设备内同时进行的过程,也可看成在进行反应的同时用精馏方法分离出产品的过程。设计反应精馏的目的,可以是为提高分离效率而将反应与精馏相结合的一种分离操作,也可以是为了提高反应转化率而借助于精馏分离手段的一种反应过程。反应精馏在工业上应用广泛,利用精馏促进反应的反应精馏过程包括酯化、酯交换、皂化、胺化、水解、异构化、烃化、卤化、脱水、乙酰化和硝化等。利用反应促进精馏的反应精馏过程主要用于相近沸点的混合物、共沸物或同分异构体难分离体系的分离,利用异构体与反应添加剂之间的特殊反应,生成新的化合物后再进行精馏分离。
用Aspen Plus软件模拟反应精馏过程,必须选择“RadFrac”严格计算模块,化学反应过程使用动力学模型,标注反应段的起始塔板与终止塔板,标注反应段的塔板液相体积、或塔板液相持液量、或反应停留时间。分离过程与反应过程在同一设备中同时进行,一些进料组分浓度可能降低或消失,新的组分会生成。对于共沸体系,原有的共沸物可能会消失,新的反应共沸物可能会生成。相对于物理分离过程,描述反应精馏过程的计算方程式的数量与复杂程度增加,因而模拟过程不容易收敛,读者可以通过选择收敛方式、提供辅助信息、增加迭代次数等方法协助软件模拟过程收敛。
例2-11 非均相反应精馏合成乙酸丁酯相图分析。
乙酸丁酯是优良的有机溶剂,广泛用于硝化纤维清漆中,在人造革、织物及塑料加工过程中用作溶剂,也是国标规定允许使用的食用香料。乙酸(A)与丁醇(B)通过酯化反应合成乙酸丁酯(C)和水(D),反应方程式为:
正、逆反应均为2级反应,反应速率方程式为:
式中,浓度计量单位为摩尔分数。
反应速率常数为(活化能单位kJ/kmol):
已知两种反应原料为:液态纯丁醇139℃,2atm,56.5kmol/h;乙酸水溶液94℃,2atm,1752kmol/h,摩尔分数0.03226。反应精馏塔为泡罩塔板,常压精馏,塔径6m,理论板数30,反应段5~25塔板,回流温度50℃。
分离要求:(1)产品乙酸丁酯含量大于0.995(摩尔分数),丁醇摩尔收率大于90%;(2)废水中水的摩尔分数大于0.995。求:两股产物的流率与组成。
解 首先利用软件的绘制相图功能,绘制该反应体系的两个三元相图,并借助于这两个相图分析一下此精馏体系的特点。常压下,丁醇-乙酸-乙酸丁酯的三角相图见图2-74,可见有两个二元共沸点(丁醇-乙酸丁酯正偏差共沸点,发散点;丁醇-乙酸负偏差共沸点,稳定点),一个丁醇-乙酸-乙酸丁酯三元共沸点(发散点)。丁醇-水-乙酸丁酯三角相图见图2-75,可见有三个二元正偏差共沸点(均为发散点),一个三元正偏差共沸点(发散点),有两个液液部分互溶区域(分别是丁醇-水和乙酸丁酯-水)。因三元正偏差共沸点在相图上属于不稳点,且沸点最低,将首先从塔顶蒸出。由图2-75可知,馏出液冷凝后将分成水相和酯相。产物乙酸丁酯沸点最高,将从塔底流出。根据对体系相平衡分析,设计的反应精馏塔应该无塔顶冷凝器,汽相在外置冷凝器中冷凝后分相,酯相回流,水相排出,塔底得到产品乙酸丁酯。

图2-74 丁醇-乙酸-乙酸丁酯相图

图2-75 丁醇-水-乙酸丁酯相图
① 全局性参数设置 计算类型“Flowsheet”,输入反应前后的所有组分。
② 选择性质方法 本题涉及部分互溶区域,应选择NRTL方程计算液相的非理想性;又因涉及乙酸,考虑到乙酸汽相缔合,应选择Hayden-O’Connell方程计算汽相的非理想性,故最终选择“NRTL-HOC”性质方法进行模拟计算,确认NRTL方程的二元交互作用参数。对于部分互溶组分,如丁醇-水和乙酸丁酯-水二元交互作用参数的选择来源于LLE数据源的参数,如图2-76所示。

图2-76 选择二元交互作用参数
③ 画流程图 按题目内容绘制流程如图2-77所示,液液分相器出口的第一液相为水相外排,第二液相为有机相,返回反应精馏塔的塔顶作为回流。把题目给定的进料物流信息填入对应栏目中。

图2-77 反应精馏合成乙酸丁酯流程图
④ 设置模块信息 “B1”模块(“RadFrac”):在精馏塔模块的“Setup”文件夹中,有3个页面需要填写。设理论板数30,无冷凝器,共沸物收率方式,设塔底热负荷29MW。酯相回流从第1板进,乙酸从第5板进,丁醇从第25板进,常压精馏,设全塔压降0.38atm。第一个页面填写见图2-78。

图2-78 反应精馏塔参数设置
在精馏塔模块的“Reaction”文件夹中,有2个页面需要填写。在“Secifications”页面,标注反应段的起始板与终止板,创建一个化学反应方程式的文件夹,见图2-79(a);在“Holdups” 页面,标注反应段的塔板液相体积。由塔径6m,塔板上液位高度0.05m,估算塔板上的液相体积1.4m3,见图2-79(b)。在精馏塔模块的“Estimates|Temperature”页面,给出塔顶和塔底的温度估计值90℃和140℃。

图2-79 反应段标注
“B2”模块:假设无压降,汽相冷凝冷却至50℃。
“B3”模块:绝热、常压,第二液相主要成分为乙酸丁酯。
⑤ 设置化学反应方程式信息 正反应方程式设置方式如图2-80(a)所示,动力学数据设置方式如图2-80(b)所示。同理设置逆反应方程式、输入逆反应动力学数据。

图2-80 正反应动力学数据设置方式
⑥ 收敛方法与方式设置 在“Convergence|Conv Options|Defaults|Default Methods”页面,把撕裂流的收敛方法改为“Broyden”,即用拟牛顿方法计算撕裂流收敛,见图2-81。在“Convergence|Conv Options|Methods|Broyden”页面,把最大迭代次数改为100,见图2-82。在“Convergence|Tear”页面,把循环物流“RE”设置为撕裂流,见图2-83。

图2-81 选择收敛方法

图2-82 修改最大迭代次数

图2-83 设置撕裂流
⑦ 模拟计算 计算结果见图2-84,产品乙酸丁酯的摩尔分数为0.998,丁醇摩尔收率大于92.3%;废水中水的摩尔分数大于0.995,满足题目全部分离要求。

图2-84 乙酸丁酯反应精馏模拟结果
2.4.3 化学吸收与解吸过程
化学吸收是工业上应用广泛的单元操作,既用于气体的分离或净化,如用碳酸钾水溶液吸收二氧化碳、用醇胺溶液吸收硫化氢等,也用于直接生产化工产品,如煤气脱氨过程中用稀硫酸吸收煤气中的氨制造硫酸铵、用水吸收氮的氧化物制造硝酸等。化学吸收是气体混合物中溶质组分与吸收剂中的活性组分之间发生化学反应的吸收操作过程。与物理吸收相比,化学吸收的优点是化学反应将溶质组分转化为另一种物质,提高了吸收剂对溶质的吸收能力,可减少吸收剂用量。化学反应降低了吸收剂中游离态溶质的浓度,增大了传质推动力,可提高气体的吸收程度。化学反应改变了液相中溶质的浓度分布,因而可减小液相传质阻力,提高液相的传质分系数。与物理吸收相比,化学吸收传质速率高,设备尺寸小,选择性提高,能得到高纯度的解吸气体。
用Aspen Plus软件模拟化学吸收与解吸过程与模拟反应精馏过程类似,不同之处是化学吸收与解吸过程属于宽沸程体系,在选择收敛方法时应予以注意。
例2-12 吸收液解吸CO2和H2S——化学吸收模拟。
用带有部分冷凝器的再沸解吸塔对含CO2和H2S酸性气体的吸收液进行解吸。解吸塔的理论塔板数为12,塔径1.8m,塔顶压力165kPa,塔板压降设为0.7kPa/板。入塔吸收液流率3568kmol/h,温度100℃,压力170kPa,溶液中各组分的表观摩尔分数分别是:二乙醇胺0.063,CO2 0.026,H2S 0.001,其余为水。要求解吸液中CO2的表观摩尔分数<0.001,H2S的表观摩尔分数<0.0001。求解吸塔冷凝器和再沸器(重沸器)的热负荷。
解 选择综合过程数据包“Datapkg”中的二乙醇胺溶液脱碳文件“kedea.bkp”为基础进行模拟计算。
① 全局性参数设置 计算类型“Flowsheet”,默认“kedea.bkp”文件内的所有分子组分、离子组分和已经选择的性质方法“NRTLELEC”。在“kedea.bkp”文件的“Reactions”文件夹中,已经输入了若干个化学反应组合的子文件夹。其中的“DEA-ACID”子文件夹中,包含了8个DEA与酸性气体组分在水溶液中的离子反应方程式、动力学方程参数和反应平衡常数,这些方程式和数据可用于本例的模拟计算。
② 画流程图 选用“RadFrac”模块画出解吸流程图,见图2-85。把题给吸收液的物流信息填入进料物流栏目中。

图2-85 解吸流程图
③ 设置模块信息 在“Setup”文件夹中,有3个页面需要填写。在“Configuration”页面,填入理论级数12,冷凝器选择“Partial-Vapor”,收敛方法选择“Strongly non-ideal liquid”。解吸塔操作条件选用两个参数,一是塔顶汽相出料量,填写97.5kmol/h;回流量暂时填写330kmol/h,见图2-86。

图2-86 解吸塔“Configuration”页面设置
在“Streams”页面和“Pressures”页面按题目给定信息填写。为减少塔顶水汽的流失,设计规定控制塔顶温度为40℃,调节手段为塔顶回流量,设置方法如图2-87所示。在解吸塔模块的“Reaction|Specifications”页面,标注解吸塔的反应段起始板与终止板,勾选化学反应方程式的文件“DEA-ACID”参与解吸计算,见图2-88(a),设置估计的塔板总持液量,见图2-88(b)。

图2-87 反馈计算控制塔顶温度及塔顶回流量

图2-88 解吸塔化学反应设置
④ 辅助收敛参数设置 为了加速收敛,在解吸塔模块的“Estimates|Temperature”页面输入估计的塔顶温度40℃,第2板110℃,塔釜118℃。为了增加迭代次数,在解吸塔模块“Convergence|Basic”页面的“Basic convergence”栏目,把最大迭代次数由25次改为50次。为了提高收敛的稳定性,把“Methods”栏目中的阻尼因子“Damping level”由“None”修改为“Severe”,见图2-89。

图2-89 修改迭代参数与添加阻尼因子
⑤ 输出设置 为了使计算结果能够显示溶液中表观分子摩尔组成,在“Properties| Prop-Sets|Properties”页面,建立一个溶液组成输出文件“PS-1”,用来显示解吸溶液中酸性气体成分的表观分子摩尔组成,设置方法如图2-90所示。其中参数“XAPP”是软件自带的物流性质符号,仅在电解质体系中使用,表示组分的摩尔组成。为使溶液中表观分子摩尔组成在输出物流性质中显示,需要把“PS-1”文件添加到物流性质输出格式中。在“Setup|Report Options|Stream”页面,点击“Property Sets”按钮,把“PS-1”文件移动到“Selected prorperty sets”栏目中。

图2-90 设置表观分子摩尔浓度参数
⑥ 模拟计算 结果如图2-91所示,由图2-91(a),解吸塔出口溶液中CO2的表观摩尔分数<0.001,H2S的表观摩尔分数<0.0001,达到分离要求。由图2-91(b),塔顶和塔底热负荷分别是4045kW和6579kW。

图2-91 解吸塔模拟结果