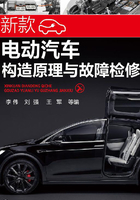
第二章 电动汽车动力电池
第一节 电动汽车动力电池概述
动力电池是纯电动汽车驱动能量的唯一来源,直接关系到电动汽车的动力性能、续航能力和安全性。从纯电动汽车成本构成看,电池系统占据了其成本的30%~50%。动力电池技术一直影响着电动汽车的实用化进程。
锂离子电池是目前电动汽车上最常用的电池种类之一,从1970年诞生至今时间并不算长,但相对于铅酸蓄电池、镍镉电池和镍氢电池,凭借其能量密度高、循环使用寿命长等特点迅速在电动汽车上被广泛应用。目前在电动汽车上配备的锂离子电池主要有锰酸锂电池、钛酸锂电池、磷酸铁锂电池及三元锂电池。
一、电芯模块、电池模组及模组布置
为了提升电池容量,需要把单个电芯进行并联,通常把几个容量、性能参数一致的电芯用激光焊接并联组成基础模块,如3个软包电芯并联(3P parallel),当然也可以更多的电芯并联,如5P,甚至16P等。
为了提升电池电压,则需要把电芯再进行串联,因此再把几个基础模块用激光焊接串联成模块,如2个3P基础模块串联为3P2S(series)电池模块,如图2-1所示,或者3个3P基础模块串联为3P3S电池模块。同时,为了在动力电池内布置方便,模块的组合方式有多种选择:可以单用1个3P2S模块,电池上面可以布置其他电器元件;也可以把2个3P2S叠放串联成3P4S;还可以把1个3P2S和1个3P3S叠放组成3P5S。多种组合方式错落有致地固定在动力电池底板上,方便了总体布局。

图2-1 3P2S模组及电压
选用电芯时要保证一致性,包括容量一致性、内阻一致性、充放电一致性、温升一致性、寿命一致性。电池基础模块或者模组要设置温度传感器,以检测电池温度;温度传感器有的放置在串联模组内部(图2-2)有的放置在模组极柱处(图2-3),还有的放置在串联模块的镍板背面(图2-4)。镍板用激光焊接到极柱上。每个电池基础模块都设置了电压检测线,这些检测信号线汇集到电池电压与温度控制单元(从控盒);从控盒对每一个电芯(基础模块)的电压随时巡检,检测电芯的电压、检测电压最高的电芯、检测电压最低的电芯;计算某个电池电压的偏离情况;根据电压计算出电池的SOC数值,报告给电池主控盒,然后报告给整车控制器。电池各个组合模块必须用螺栓可靠地固定在动力电池的底板上,耐受冲击振动,不得松动。

图2-2 温度传感器(模组内)

图2-3 温度传感器(模组极柱处)

图2-4 温度传感器(镍板背面)
二、电池模组高压串联回路的连接方式
动力电池通常由90~100个电池串联组成,直流电压高达380V(有些车达到600V),因此对外供电安全的措施必须可靠。
电池模组用多层铜皮制成的成型母线带,通过螺栓可靠连接。母线带柔软,避免因车辆振动导致母线与螺栓连接根部产生裂纹。母线带外部用绝缘材料做了耐压绝缘处理。通常在串联的高压回路中,设置了内外部电压检测点、主正负极母线继电器、预充继电器、预充电阻,如图2-5所示。维修开关设置在串联回路的中间,同时维修开关内部还有一个熔断器(图2-6),假如回路电流过大,熔断器会断开,当维修开关拔出时,高压回路呈开路状态。正负极母线对外部负载输出端分别接了继电器,只有正负极母线继电器都接通,才能对外供电或对电池充电。高压母线还设置了电流检测器件,目前有串联在母线上的无感分流器方式和套装在母线外部的霍尔传感器方式(图2-7)。两种传感器都是把检测到的母线电流送到主控盒,用于控制母线输出不能过流,充电和能量回收时电流不能过大。

图2-5 高压控制箱内的继电器

图2-6 维修开关内的熔断器

图2-7 霍尔电流传感器
三、动力电池控制系统
1.预充电控制电路
电动汽车的动力电池负载是电动机,如驱动电动机、空调电动机。这些电动机的控制器内部都有电容,另外车载充电机、DC/DC控制器等内部也有电容器。车辆断电时,电容会放电到零,此时的电容对直流电来讲是短路状态。如果直接把370V左右的直流电加到电容上,瞬时的浪涌电流会烧毁母线、烧蚀继电器主触点、击穿电容器。为了避免此类事故发生,需要设置预充电电阻和预充电继电器。
预充电继电器与预充电阻串联后,并联在正极母线继电器2个主触点之间。动力电池初始上电阶段,不允许同时接通正负极母线继电器,一般是先由整车控制器接通负极母线继电器,动力电池BMS系统对高压母线绝缘检测合格、各个电池电压检测合格后,接通预充电继电器,电流从正极母线经过预充电阻对负载中的电容器件先进行充电。当检测到电容的两端电压接近母线电压后,正极母线继电器再闭合,随后断开预充电继电器,动力电池对外正式供电。
2.高压绝缘检测盒
高压绝缘检测盒的任务一是高压回路绝缘检测,二是母线继电器触点开闭监测。如图2-8所示,高压绝缘检测的检测点设置在动力电池内高压回路上,当动力电池没有对外供电时,检测盒对电池内部高压回路进行绝缘检测,当正负极母线继电器接通负载后,检测盒对全部回路的绝缘进行检测,检测点放在正负极母线继电器主触点上,检测线连接到高压绝缘检测盒内部。

图2-8 绝缘检测与主触点开闭检测原理图
从预充电继电器、正极母线继电器及负极母线继电器的触点处,分别引出检测线送回高压绝缘检测盒。各继电器触点开闭状态可以从各自继电器内外两触点的电位是否相同做出判断,通过主触点两端电位状况与触点控制信号目标的比较,做出触点工作是否正确的判断,并报送上一级控制器。绝缘检测控制单元如图2-9所示,接到高压正负极母线继电器供电指令后,立即开始对高压回路进行绝缘监测。无论电池内部还是外部负载端,只要高压回路绝缘电阻值不合格、超过阈值,立即停止高压供电,并在仪表板上报出高压绝缘故障文字提示。同时,对各个继电器触点开闭状态进行检测,判断总正继电器、总负继电器、预充电继电器的触点是否按照控制策略正常开闭。通过相应监测点的电压检测,分析判断各个继电器触点的开闭状况,报告给动力电池的主控盒。

图2-9 绝缘检测控制单元(高压绝缘检测盒)
3.电芯电压、温度采集线束与从控盒
布置电芯电压,温度采集点与采集线束涉及的电压都不高,一般不会到5V,属于低压直流,但是和车身不能搭铁,是绝缘的。每个电芯的采集线实际是把每个电池基础模块的正负极分别引出导线,连同温度传感器信号线,通过低压线束汇集到从控盒(图2-10)。

图2-10 从控盒
从控盒中的每一个采样电阻对应一组电池电极电压采样线,从采样电阻上可以采集到各个串联电池的电压数据。从控盒对各个并联模块(或单独大电芯)的电压进行巡检采集、计算与处理。从监测数据中需要找出最高电压电芯和最低电压电芯,计算电芯电压最高与最低的差值,差值应小于0.03V。充电时有一节电芯电压达到充电截止电压,即停止充电;放电时有一节电芯电压降到放电截止电压,即停止放电。温度采集单元用于采集监控动力电池的单体或电池组的温度,防止过温导致热失控,造成重大损失。在低温充电时,温度采集单元会给出信号指令,首先对电池加热,达到一定温度时再开通充电。
4.BMS动力电池主控盒的功能
BMS动力电池主控盒(图2-11)是动力电池的管理核心,是一个连接外部通信和内部通信的平台,其主要功能如下。

图2-11 BMS动力电池主控盒
① 接收电池管理系统反馈的实时温度和单体电压(并计算最大值和最小值)。
② 接收高压绝缘盒反馈的绝缘、总电压和电流情况。
③ 与整车控制器的通信。
④ 与充电机或快充桩通信。
⑤ 控制主继电器。
⑥ 控制电池加热。充电时当电芯温度低于设定值,BMS控制加热继电器闭合,通过加热熔丝接通加热膜电路。
⑦ 启动钥匙在ON挡时,对来自整车控制器的唤醒以及充电时来自整车控制器的唤醒做出应答。
⑧ 控制充/放电电流。
⑨ 预充电控制。
⑩ 电池组SOC的测量与估算。
⑪ 整车电池数据的故障分析、判断及在线报警。
⑫ 通过内部CAN总线统计电池箱的电池数据及参数信息。
⑬ 通过CAN1与整车控制器通信,发送电池状态及告警信息。
⑭ 通过CAN2总线将电池数据发送至仪表和充电机。
⑮ 计算电池组最大允许充电电流,通过CAN2总线传送给充电机,实现充电过程闭环控制。
⑯ 当监测到电池出现过热(参数由电池生产厂家决定,可修改)的时候,电池管理系统能启动安装在电池箱的冷却风机,实施强制风冷从而让电池组降温,从而提高电池运行的稳定性和延长电池的使用寿命。
⑰ 充电时当电芯温度低于设定值,BMS控制加热继电器闭合,通过加热熔丝接通加热膜电路(图2-12)。

图2-12 动力电池低温充电加热电路图
如图2-13所示是动力电池控制盒,它把从控盒、高压绝缘盒、主控盒集成在一起,整个动力电池内只有一个控制盒,完成全部管理功能。左侧电路板下部是电池电压主采样电阻群,左上部有绝缘检测和继电器触点开闭检测电路,右上部是计算、处理、执行部分,输出对三个继电器的控制指令以及与整车控制器、充电机的CAN通信。

图2-13 动力电池控制盒
动力电池模块组放置在一个密封并且电磁屏蔽的动力电池箱里面。动力电池系统使用可靠的高低压接插件与整车进行连接。动力电池箱体的防护等级为IP67,用螺栓紧固在车身地板下方,力矩为80~150N·m。整车维护时需要观察电池箱体螺栓是否松动,电池箱是否有破损变形,密封胶是否完整。
5.动力电池为整车供电过程
① 启动钥匙置于ON挡时,蓄电池提供12V电压,对全车高压有控制器的部件(动力电池、电动机控制器、整车控制器、空调控制器、DC/DC控制器)进行低压唤醒、初始化及自检,如无故障,上报整车控制器(VCU)。
② 动力电池内部动力母线绝缘检测合格,各个继电器状态正常,各个电池模组电压及温度状态合格,上报整车控制器(VCU)。
③ VCU控制动力电池负极母线继电器闭合,动力电池内部主控盒控制预充电继电器闭合,为负载端各个电容充电。
④ 电池管理系统根据充电电阻两端电压状态,检测判断到电容充满电后,闭合正极母线继电器,然后断开预充电继电器,此时仪表上出现RADEY灯符号。
6.动力电池充电过程
车辆停止后,启动钥匙在OFF挡位,12V蓄电池ON挡供电断开,车辆高压系统包括整车控制器处于休眠状态。车辆充电时,启动钥匙要求在OFF挡位,充电枪连接正常后,充电机(慢充和快充)送出自有的12V低压电,唤醒整车控制器(VCU),仪表盘出现充电插头信号,表示充电枪连接正常。整车控制器(VCU)以12V低压唤醒动力电池管理系统和DC/DC控制器,并控制闭合动力电池的负极母线继电器。动力电池控制器对电池电芯电压以及总的荷电情况进行检测,对电池内部绝缘进行检测。动力电池内部自检合格后,通过CAN先向充电机发出充电请求信号,闭合正负极母线继电器,开始充电。
充电过程中主控盒与从控盒采集的电池电压和温度信息,随时通过内部CAN线通信。主控盒把信息通过对外CAN总线与整车控制器(VCU)和充电机通信,把动力电池的充电要求信息传给充电机。充电机随时调节充电电流和电压,保证充电安全合理。当充电结束拔出充电枪后,整车控制器停止高压系统供电。
7.动力电池的CAN通信
电池管理系统(主控模块)通过CAN总线将实时的电池状态告知整车控制器以及电动机控制器等设备,使整车采用更加合理的控制策略,将电池组的详细信息告知车载监控系统,完成电池状态数据的显示和故障报警等功能,为电池的维护和更换提供依据。
(1)系统自检 BMS设置了强大的系统自检功能,系统上电后对电压、温度、通信、时钟及存储器等部件进行检测,保证系统自身的工作正常。
(2)系统监测 BMS对整车电池的离散性进行分析并根据不同故障类型进行报警,同时对电池充放电次数以及历史数据进行记录,以便进行系统诊断及性能优化。