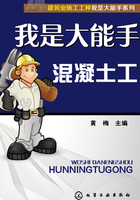
2 普通混凝土施工
2.1 混凝土配制
2.1.1 混凝土配合比设计遵循的原则
混凝土配合比设计应遵循以下几条原则。
①混凝土配合比应综合考虑混凝土强度等级、耐久性能和施工性能等要求,在满足混凝土强度、耐久性能和施工性能要求的条件下则应采用低水泥用量和低用水量的原则进行设计。
②对于有抗冻、抗渗、抗氯离子侵蚀和化学腐蚀等耐久性要求的混凝土配合比设计,还应符合国家现行标准《混凝土结构耐久性设计规范》(GB/T 50476—2008)、《普通混凝土配合比设计规程》(JGJ 55—2011)等标准的有关规定。标准中对冻融环境、氯离子侵蚀环境等条件下的混凝土配合比设计参数均有明确的规定。
③冬期的施工应按照不同的负温进行配合比设计。有关参数可按《建筑工程冬期施工规程》(JGJ/T 104—2011)执行。
④配合比设计和试配所用的原材料应与施工采用的原材料应一致,并应符合国家现行相关标准的要求。试配时可对原材料按照相关标准进行检测。
⑤配合比设计时的混凝土性能试验应当按照现行国家标准《普通混凝土拌合物性能试验方法标准》(GB/T 50080—2002)、《普通混凝土力学性能试验方法标准》(GB/T 50081—2002)和《普通混凝土长期性能和耐久性能试验方法标准》(GB/T 50082—2009)的相关规定进行。
2.1.2 混凝土配合比设计要求
①普通混凝土配合比应按照国家现行标准《普通混凝土配合比设计规程》(JGJ 55—2011)的规定进行计算。
②设计参数和原材料用量应满足下列要求:
a.混凝土配合比设计中的最大水胶比应符合现行国家标准《混凝土结构设计规范》(GB 50010—2010)的相关规定;
b.除配制C15及以下强度等级的混凝土外,混凝土的最小胶凝材料用量应符合表2-1的相关规定;
表2-1 混凝土的最小胶凝材料用量

c.混凝土配合比设计应采用工程实际使用的原材料,配合比设计所采用的细骨料含水率要小于0.5%,粗骨料含水率应小于0.2%;
d.钢筋混凝土耐久性参数应符合《混凝土耐久性检验评定标准》(JGJ/T 193—2009)的规定,其单位体积混凝土的胶凝材料用量宜控制在表2-2所示范围内;
表2-2 单位体积混凝土的胶凝材料用量

注:1.表中数据适用于最大骨科径为20mm的情况,骨料粒径较大时宜适当降低胶凝材料用量,骨料粒径较小时可适当增加。
2.引气混凝土的胶凝材料用量与非引气混凝土要求相同。
3.对于强度等级达到C60的泵送混凝土,胶凝材料最大用量可增大至530kg/m3。
e.矿物掺和料在混凝土中的掺量应通过试验具体确定。钢筋混凝土中矿物掺和料最大掺量宜应符合表2-3的规定。预应力钢筋混凝土中矿物掺和料最大掺量宜应符合表2-4的规定。
表2-3 钢筋混凝土中矿物掺和料最大掺量

注:1.采用硅酸盐水泥和普通硅酸盐水泥之外的通用硅酸盐水泥时,混凝土中水泥混合材和矿物掺和料用量之和应不大于按普通硅酸盐水泥用量20%计算混合材和矿物掺和料用量之和。
2.对基础大体积混凝土、粉煤灰和复合掺和料的最大掺量可增加5%。
3.复合掺和料中各组分的掺量不宜超过任一组分单掺时的最大掺量。
表2-4 预应力钢筋混凝土中矿物掺和料最大掺量

注:1.粉煤灰应为Ⅰ级或Ⅱ级F类粉煤灰。
2.在复合掺和料中,各组分的掺量不宜超过单掺时的最大掺量。
③混凝土拌合料应该具有良好的施工和易性和适宜的坍落度。混凝土的配合比要求有较适宜的技术经济性。
④混凝土拌合物中水溶性氯离子最大含量应该符合表2-5的要求。混凝土拌合物中水溶性氯离子含量应按照现行行业标准《水运工程混凝土试验规程》(JTJ 270—1998)中混凝土拌合物中氯离子含量的快速测定方法进行测定。
表2-5 混凝土拌合物中水溶性氯离子最大含量

长期处于潮湿或水位变动的寒冷和严寒环境以及盐冻环境的混凝土要掺用引气剂。引气剂掺量应根据混凝土含气量要求经由试验确定。掺用引气剂的混凝土最小含气量应符合表2-6的规定,最大不宜超过7.0%。
表2-6 混凝土最小含气量

注:含气量为气体占混凝土体积的百分比。
⑤对于有预防混凝土碱骨料反应设计要求的工程,混凝土中最大碱含量不应该大于3.0kg/m3,并宜掺用适量粉煤灰等矿物掺和料;对于矿物掺和料碱的含量,粉煤灰碱含量可取实测值的1/6。
2.1.3 混凝土配合比设计
2.1.3.1 混凝土配合比计算
(1)水胶比
①混凝土强度等级不大于C60等级时,混凝土水胶比宜计算为
(2-1)
式中 W/B——混凝土水胶比;
fcu,0——混凝土试配强度,MPa;
αa、αb——回归系数,取值应符合下述第②项的规定;
fb——胶凝材料28d胶砂抗压强度,MPa,可实测,且试验方法应按现行国家标准《水泥胶砂强度检验方法(ISO法)》(GB/T 17671—1999)执行;也可按下述第③项确定。
②回归系数(αa、αb)宜按下列规定确定:
a.根据工程所使用的原材料,通过试验建立的水胶比与混凝土强度关系式来确定;
b.当不具备上述试验统计资料时,可按表2-7选用。
表2-7 回归系数αa、αb选用表

③当胶凝材料28d胶砂抗压强度值(fb)无实测值时,可按下式计算:
fb=γf γs fce (2-2)
式中 γf、γs——粉煤灰影响系数和粒化高炉矿渣粉影响系数,可按表2-8选用;
fce——水泥28d胶砂抗压强度,MPa,可实测。
表2-8 粉煤灰影响系数(γf)和粒化高炉矿渣粉影响系数(γs)

注:1.采用Ⅰ级、Ⅱ级粉煤灰宜取上限值。
2.采用S75级粒化高炉矿渣粉宜取下限值,采用S95级粒化高炉矿渣粉宜取上限值,采用S105级粒化高炉矿渣粉可取上限值加0.05。
3.当超出表中的掺量时,粉煤灰和粒化高炉矿渣粉影响系数应经试验确定。
④当水泥28d胶砂抗压强度(fce)无实测值时,可按下式计算:
fce=γcfce,g (2-3)
式中 γc——水泥强度等级值的富余系数,可按实际统计资料确定;当缺乏实际统计资料时,也可按表2-9选用;
fce,g——水泥强度等级值,MPa。
表2-9 水泥强度等级值的富余系数(γc)

(2)用水量和外加剂用量
①每立方米干硬性或塑性混凝土的用水量(mw0)应符合下列规定:
a.混凝土水胶比在0.40~0.80范围时,可按表2-10和表2-11选取。
表2-10 干硬性混凝土的用水量 单位:kg/m3

表2-11 塑性混凝土的用水量 单位:kg/m3

注:1.本表用水量是采用中砂时的取值。采用细砂时,每立方米混凝土用水量可增加5~10kg;采用粗砂时,可减少5~10kg。
2.掺用矿物掺和料和外加剂时,用水量应相应调整。
b.混凝土水胶比小于0.40时,可通过试验确定。
②掺外加剂时,每立方米流动性或大流动性混凝土的用水量(mw0)可按下式计算:
(2-4)
式中 mw0——计算配合比每立方米混凝土的用水量,kg/m3;
m'w0——未掺外加剂时推定的满足实际坍落度要求的每立方米混凝土用水量,kg/m3,以表2-11中90mm坍落度的用水量为基础,按每增大20mm坍落度相应增加5kg/m3用水量来计算,当坍落度增大到180mm以上时,随坍落度相应增加的用水量可减少;
β——外加剂的减水率, %,应经混凝土试验确定。
③每立方米混凝土中外加剂用量(ma0)应按下式计算:
ma0=mb0 βa (2-5)
式中 ma0——计算配合比每立方米混凝土中外加剂用量,kg/m3;
mb0——计算配合比每立方米混凝土中胶凝材料用量,kg/m3;
βa——外加剂掺量, %,应经混凝土试验确定。
(3)胶凝材料、矿物掺和料和水泥用量
①每立方米混凝土的胶凝材料用量(mb0)应按下式计算,并应进行试拌调整,在拌合物性能满足的情况下,取经济合理的胶凝材料用量,即
(2-6)
式中 mb0——计算配合比每立方米混凝土中胶凝材料用量,kg/m3;
mw0——计算配合比每立方米混凝土的用水量,kg/m3;
W/B——混凝土水胶比。
②每立方米混凝土的矿物掺和料用量(mf0)应按下式计算:
mf0=mb0 βf (2-7)
式中 mf0——计算配合比每立方米混凝土中矿物掺和料用量,kg/m3;
βf——矿物掺和料的掺量, %。
③每立方米混凝土的水泥用量(mc0)应按下式计算:
mc0=mb0-mf0 (2-8)
式中 mc0——计算配合比每立方米混凝土中水泥用量,kg/m3。
(4)砂率
①砂率(βs)应根据骨料的技术指标、混凝土拌合物性能和施工要求,参考既有历史资料确定。
②当缺乏砂率的历史资料时,混凝土砂率的确定应符合下列规定。
a.坍落度小于10mm的混凝土,其砂率应经试验确定。
b.坍落度为10~60mm的混凝土,其砂率可根据粗骨料品种、最大公称粒径及水胶比按表2-12确定。
表2-12 混凝土的砂率 单位: %

注:1.本表数值系中砂的选用砂率,对细砂或粗砂,可相应地减少或增大砂率。
2.采用人工砂配制混凝土时,砂率可适当增大。
3.只用一个单粒级粗骨料配制混凝土时,砂率应适当增大。
c.坍落度大于60mm的混凝土,其砂率可经试验确定,也可在表2-12的基础上,按坍落度每增大20mm、砂率增大1%的幅度予以调整。
(5)粗、细骨料用量
①当采用质量法计算混凝土配合比时,粗、细骨料用量应按下式计算:
mf0+mc0+mg0+ms0+mw0=mcp (2-9)
砂率计算公式为
(2-10)
式中 mg0——计算配合比每立方米混凝土的粗骨料用量,kg/m3;
ms0——计算配合比每立方米混凝土的细骨料用量,kg/m3;
βs——砂率, %;
mcp——每立方米混凝土拌合物的假定质量,kg,可取2350~2450kg/m3。
②当采用体积法计算混凝土配合比时,粗、细骨料用量应按下面公式计算:
(2-11)
式中 ——水泥密度,kg/m3,可按现行国家标准《水泥密度测定方法》(GB/T 208—1994)测定,也可取2900~3100kg/m3;
——矿物掺和料密度,kg/m3,可按现行国家标准《水泥密度测定方法》(GB/T 208—1994)测定;
——粗骨料的表观密度,kg/m3,应按现行行业标准《普通混凝土用砂、石质量及检验方法标准》(JGJ 52—2006)测定;
——细骨料的表观密度,kg/m3,应按现行行业标准《普通混凝土用砂、石质量及检验方法标准》(JGJ 52—2006)测定;
——水的密度,kg/m3,可取1000kg/m3;
α——混凝土的含气量分数,在不使用引气剂或引气型外加剂时,α可取1。
2.1.3.2 混凝土配合比的试配、调整与确定
(1)试配
①混凝土试配应采用强制式搅拌机进行搅拌,并应符合现行行业标准《混凝土试验用搅拌机》(JG 244—2009)的规定,搅拌方法宜与施工采用的方法相同。
②试验室成型条件应符合现行国家标准《普通混凝土拌合物性能试验方法标准》(GB/T 50080—2002)的规定。
③每盘混凝土试配的最小搅拌量应符合表2-13的规定,并不应小于搅拌机公称容量的1/4且不应大于搅拌机公称容量。
表2-13 混凝土试配的最小搅拌量

④在计算配合比的基础上应进行试拌。计算水胶比宜保持不变,并应通过调整配合比其他参数使混凝土拌合物性能符合设计和施工要求,然后修正计算配合比,提出试拌配合比。
⑤在试拌配合比的基础上应进行混凝土强度试验,并应符合下列规定:
a.应采用三个不同的配合比,其中一个变为试拌配合比,另外两个配合比的水胶比宜较试拌配合比分别增加和减少0.05,用水量应与试拌配合比相同,砂率可分别增加和减少1%;
b.进行混凝土强度试验时,拌合物性能应符合设计和施工要求;
c.进行混凝土强度试验时,每个配合比应至少制作一组试件,并应标准养护到28d或设计规定龄期时试压。
(2)配合比的调整与确定
①配合比调整应符合下列规定:
a.根据《普通混凝土配合比设计规程》(JGJ 55—2011)混凝土强度试验结果,宜绘制强度和胶水比的线性关系图或插值法确定略大于配制强度对应的水胶比;
b.在试拌配合比的基础上,用水量(mw)和外加剂用量(ma)应根据确定的水胶比做调整;
c.胶凝材料用量(mb)应以用水量乘以确定的胶水比计算得出;
d.粗骨料和细骨料用量(mg和ms)应根据用水量和胶凝材料用量进行调整。
②混凝土拌合物表观密度和配合比校正系数的计算应符合下列规定。
a.配合比调整后的混凝土拌合物的表观密度应计算为
=mc+mf+mg+ms+mw (2-12)
式中 ——混凝土拌合物的表观密度计算值,kg/m3;
mc——每立方米混凝土的水泥用量,kg/m3;
mf——每立方米混凝土的矿物掺和料用量,kg/m3;
mg——每立方米混凝土的粗骨料用量,kg/m3;
ms——每立方米混凝土的细骨料用量,kg/m3;
mw——每立方米混凝土的用水量,kg/m3。
b.混凝土配合比校正系数应按下式计算:
(2-13)
式中 δ——混凝土配合比校正系数;
——混凝土拌合物的表观密度实测值,kg/m3。
③当混凝土拌合物表观密度实测值与计算值之差的绝对值不超过计算值2%时,调整的配合比可维持不变;当两者之差超过2%时,应将配合比中每项材料用量均乘以校正系数(δ)。
④配合比调整后,应测定拌合物水溶性氯离子含量。
⑤对耐久性有设计要求的混凝土应进行相关耐久性试验验证。
⑥生产单位可根据常用材料设计出常用混凝土配合比备用,并应在启用过程中予以验证或调整。遇有下列情况之一时,应重新进行配合比设计。
a.对混凝土性能有特殊要求时。
b.水泥、外加剂或矿物掺和料等原材料品种、质量有显著变化时。
2.1.3.3 有特殊要求的混凝土配合比设计
(1)抗渗混凝土
①抗渗混凝土的原材料应符合下列规定:
a.水泥宜采用普通硅酸盐水泥;
b.粗骨料宜采用连续级配,其最大公称粒径不宜大于40.0mm,含泥量不得大于1.0%,泥块含量不得大于0.5%;
c.细骨料宜采用中砂,含泥量不得大于0.3%,泥块含量不得大于1.0%;
d.抗渗混凝土宜掺用外加剂和矿物掺和料,粉煤灰等级应为Ⅰ级或Ⅱ级。
②抗渗混凝土配合比应符合下列规定。
a.最大水胶比应符合表2-14的规定。
b.每立方米混凝土中的胶凝材料用量不宜小于320kg。
c.砂率宜为35%~45%。
表2-14 抗渗混凝土最大水胶比

③配合比设计中混凝土抗渗技术要求应符合下列规定。
a.配制抗渗混凝土要求的抗渗水压值应比设计值提高0.2MPa。
b.抗渗试验结果应满足要求:
(2-14)
式中 Pt——6个试件中不少于4个未出现渗水时的最大水压值,MPa;
P——设计要求的抗渗等级值。
④掺用引气剂或引气型外加剂的抗渗混凝土,应进行含气量试验,含气量宜控制在3.0%~5.0%。
(2)抗冻混凝土
①抗冻混凝土的原材料应符合下列规定:
a.水泥应采用硅酸盐水泥或普通硅酸盐水泥;
b.粗骨料宜选用连续级配,其含泥量不得大于1.0%,泥块含量不得大于0.5%;
c.细骨料含泥量不得大于0.3%,泥块含量不得大于1.0%;
d.粗、细骨料均应进行坚固性试验,并应符合现行行业标准《普通混凝土用砂、石质量及检验方法与标准》(JGJ 52—2006)的规定;
e.抗冻等级不小于F100的抗冻混凝土宜掺用引气剂;
f.在钢筋混凝土和预应力混凝土中不得掺用含有氯盐的防冻剂;在预应力混凝土中不得掺用含有亚硝酸盐或碳酸盐的防冻剂。
②抗冻混凝土配合比应符合下列规定。
a.最大水胶比和最小胶凝材料用量应符合表2-15的规定。
表2-15 最大水胶比和最小胶凝材料用量

b.复合矿物掺和料最大掺量宜符合表2-16的规定。
③掺用引气剂的混凝土最小含气量应符合《普通混凝土配合比设计规程》(JGJ 55—2011)的规定。
表2-16 复合矿物掺和料最大掺量

(3)高强混凝土
①高强混凝土的原材料应符合下列规定:
a.水泥应选用硅酸盐水泥或普通硅酸盐水泥;
b.粗骨料宜采用连续级配,其最大公称粒径不宜大于25.0mm,针片状颗粒含量不宜大于5.0%,含泥量不应大于0.5%,泥块含量不应大于0.2%;
c.细骨料的细度模数宜为2.6~3.0,含泥量不应大于2.0%,泥块含量不应大于0.5%;
d.宜采用减水率不小于25%的高性能减水剂;
e.宜复合掺用粒化高炉矿渣粉、粉煤灰和硅灰等矿物掺和料;粉煤灰等级不应低于Ⅱ级;对强度等级不低于C80的高强混凝土宜掺用硅灰。
②高强混凝土配合比应经试验确定,在缺乏试验依据的情况下,配合比设计宜符合下列规定。
a.水胶比、胶凝材料用量和砂率可按表2-17选取,并应经试配确定。
表2-17 水胶比、胶凝材料用量和砂率

b.外加剂和矿物掺和料的品种、掺量,应通过试配确定;矿物掺和料掺量宜为25%~40%;硅灰掺量不宜大于10%。
c.水泥用量不宜大于500kg/m3。
③在试配过程中,应采用三个不同的配合比进行混凝土强度试验,其中一个可为依据表2-11计算后调整拌合物的试拌配合比,另外两个配合比的水胶比,宜较试拌配合比分别增加和减少0.02。
④高强混凝土设计配合比确定后,尚应采用该配合比进行不少于三盘混凝土的重复试验,每盘混凝土应至少成型一组试件,每组混凝土的抗压强度不应低于配制强度。
⑤高强混凝土抗压强度测定宜采用标准尺寸试件,使用非标准尺寸试件时,尺寸折算系数应经试验确定。
(4)泵送混凝土
①泵送混凝土所采用的原材料应符合下列规定。
a.水泥宜选用硅酸盐水泥、普通硅酸盐水泥、矿渣硅酸盐水泥和粉煤灰硅酸盐水泥。
b.粗骨料宜采用连续级配,其针片状颗粒含量不宜大于10%;粗骨料的最大公称粒径与输送管径之比宜符合表2-18的规定。
表2-18 粗骨料的最大公称粒径与输送管径之比

c.细骨料宜采用中砂,其通过公称直径为315μm筛孔的颗粒含量不宜少于15%。
d.泵送混凝土应掺用泵送剂或减水剂,并宜掺用矿物掺和料。
②泵送混凝土配合比应符合下列规定:
a.胶凝材料用量不宜小于300kg/m3;
b.砂率宜为35%~45%。
③泵送混凝土试配时应考虑坍落度经时损失。
(5)大体积混凝土
①大体积混凝土所用的原材料应符合下列规定。
a.水泥宜采用中、低热硅酸盐水泥或低热矿渣硅酸盐水泥,水泥的3d和7d水化热应符合现行国家标准《中热硅酸盐水泥低热硅酸盐水泥低热矿渣硅酸盐水泥》(GB 200—2003)规定。当采用硅酸盐水泥或普通硅酸盐水泥时,应掺加矿物掺和料,胶凝材料的3d和7d水化热分别不宜大于240kJ/kg和270kJ/kg。水化热试验方法应按现行国家标准《水泥水化热测定法》(GB/T 12959—2008)执行。
b.粗骨料宜为连续级配,最大公称粒径不宜小于31.5mm,含泥量不应大于1.0%。
c.细骨料宜采用中砂,含泥量不应大于3.0%。
d.宜掺用矿物掺和料和缓凝型减水剂。
②当采用混凝土60d或90d龄期的设计强度时,宜采用标准尺寸试件进行抗压强度试验。
③大体积混凝土配合比应符合下列规定:
a.水胶比不宜大于0.55,用水量不宜大于175kg/m3;
b.在保证混凝土性能要求的前提下,宜提高每立方米混凝土中的粗骨料用量;砂率宜为38%~42%;
c.在保证混凝土性能要求的前提下,应减少胶凝材料中的水泥用量,提高矿物掺和料掺量。
④在配合比试配和调整时,控制混凝土绝热温升不宜大于50℃。
⑤大体积混凝土配合比应满足施工对混凝土凝结前时间的要求。
2.1.4 混凝土配合比设计注意事项
①配合比设计前的准备工作应当充分。
②区分数理统计及非数理统计方法判定混凝土强度的不同。
③生产配合比的调整及施工中的控制。
④在保证质量的前提下,应当注重经济效益。
⑤试配时,试件制作、养护、强度试验应按《普通混凝土力学性能试验方法》(GB/T 50081—2002)的相关要求进行。
⑥特殊要求的混凝土主要包括:抗渗混凝土,其抗渗等级P6;高强度混凝土,其强度等级大于等于C60;泵送混凝土,其坍落度大于等于100mm;大体积混凝土,其实体结构物最小尺寸大于等于1m。
⑦在普通混凝土配合比设计中,要汇集有关资料,并建立常用的混凝土配合比备用;建立3d强度或快测强度推定28d强度的关系式,推定fce值时要注意留足富余。
⑧在规范要求允许的条件下,试验室应配制不同的配合比,并从经济、工作性能、质量等方面综合考虑择优选用,并要针对不同施工部位、不同评定方法给予适当调整,要尽量避免凡是同一强度均使用一个配合比的做法。
⑨试验室还应收集每次配合比及施工情况的详细数据,并注意对这些数据进行综合统计分析,以便得出本试验室的水灰比、用水量、砂率、水泥用量范围及数值,如此重复,就能成为一个很可观、很宝贵的参考资料,并对以后的施工将会起到不可估量的作用。
⑩水泥砂浆参考配比见表2-19。
表2-19 水泥砂浆参考配比

混凝土轴心抗压、轴心抗拉强度标准值fck、ftk应按表2-20采用。
表2-20 混凝土强度标准值 单位:N/mm2

混凝土轴心抗压、轴心抗拉强度设计值fc、ft应按表2-21采用。
表2-21 混凝土强度设计值 单位:N/mm2

注:1.计算现浇钢筋混凝土轴心受压及偏心受压构件时,如截面的边长或直径小于3mm,则表中混凝土的强度设值应乘以系数0.8。
2.当结构质量(如混凝土成型、截面和轴线尺寸等)确有保证时,可不受此限制。
混凝土受压或受拉的弹性模量Ec应按表2-22采用。
表2-22 混凝土弹性模量 单位: ×104N/mm2

混凝土轴心抗压、轴心抗拉疲劳强度设计值
、
应按表2-23中的混凝土强度设计值乘以相应的疲劳强度修正系数γρ来确定。
混凝土疲劳应力比值应按下列公式计算:
(2-15)
式中 、
——构件疲劳验算时,截面同一纤维上的混凝土应为最小应力、最大应力。当采用蒸汽养护时,养护温度不宜超过60℃;当超过时,计算需要的混凝土强度设计值应相应提高20%。
表2-23 混凝土疲劳强度修正系数

当温度在0~100℃范围内的时候,混凝土线膨胀系数αc可采用1×10-5/℃。混凝土泊松比υc可采用0.2。混凝土剪变模量Gc可按表2-24中混凝土疲劳变形模量的0.4倍采用。
表2-24 混凝土疲劳变形模量
