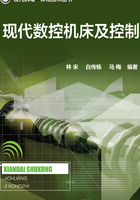
2.2 计算机数字控制装置的硬件结构
计算机数字控制装置(CNC装置)从功能到水平来分有低、中、高三点;从价格、功能、使用等综合指标考虑可分为经济型数控装置和标准型(全功能型)数控装置。CNC装置按微处理器的个数可以分为单微处理器和多微处理器结构;按CNC装置硬件的制造方式,可以分为专用型结构和通用型结构。
2.2.1 单微处理器结构
早期的CNC系统和现在一些经济型CNC系统都采用单微处理器结构。在单微处理器结构中,只有一个微处理器,对存储、插补运算、输入输出控制、CRT显示等功能进行集中控制和分时处理。微处理器通过总线与存储器、输入输出等各种接口相连,构成CNC系统。单微处理器结构具有如下特点。
① 结构简单,容易实现。
② 处理器通过总线与各个控制单元相连,完成信息交换。
③ 由于只用一个微处理器来集中控制,其功能受到微处理器字长、数据宽度、寻址功能和运算速度等因素限制。由于插补等功能由软件来实现,因此数控功能的实现与处理速度成为一对矛盾。
单微处理器结构框图见图2-2。

图2-2 单微处理器结构框图
(1)微处理器
微处理器担负数控系统的运算和管理,它由运算器和控制器两部分组成,是数控系统的核心。运算器是对数据进行算术运算和逻辑运算的部件,在运算过程中运算器不断地得到由存储器提供的数据,并将运算结果送回存储器保存起来。通过对运算结果的判断,设置状态寄存器的相应状态(进位、奇偶和溢出等)。控制器从存储器中依次取出组成程序的指令,经过译码后向数控系统的各部分按顺序发出执行操作的控制信号,使指令得以执行,因此控制器是统一指挥和控制数控系统各部件的中央机构。它一方面向各个部件发出执行任务的命令;另一方面接收执行部件发回的反馈信息,控制器根据程序中的指令信息和反馈信息,决定下一步的命令操作。
目前CNC装置中常用的有8位、16位和32位微处理器,如Intel公司的8088、8086、80186、80286、80386、80486及Pentium系列CPU等;Motorola公司6800、68000、68010、68020、68030;Zilog公司的Z80、Z8000、Z80000等。根据实时控制和处理速度的要求,按字长、数据宽度、寻址能力、运算速度及计算机技术发展的最新成果选用相应的微处理器。
(2)总线
总线是由赋予一定信号意义的物理导线构成,按信号的物理意义,可分为数据总线、地址总线、控制总线三组。数据总线为各部分之间传送数据,数据总线的位数和传送的数据宽度相等,采用双方向线。地址总线传送的是地址信号,与数据总线结合使用,以确定数据总线上传输的数据来源或目的地,采用单方向线。控制总线传输的是管理总线的某些控制信号,如数据传输的读写控制、中断复位及各种确认信号,采用单方向线。
(3)存储器
CNC装置的存储器包括只读存储器(ROM)和随机存储器(RAM)两类。ROM一般采用可以用紫外线擦除的只读存储器(EPROM),这种存储器的内容只能由CNC装置的生产厂家固化(写入),写入信息的EPROM即使断电,信息也不会丢失,它只能被CPU读出,不能写进新的内容,要想写入新的内容必须用紫外线抹除之后,才能重新写入。常用的EPROM有2716、2732、2764、27128、27256等。RAM中的信息可以随时被CPU读或写,但断电后,信息也随之消失。如果需要断电后保留信息,一般可采用后备电池。
(4)输入/输出(I/O)接口
CNC装置和机床之间的信号,一般不直接连接,而通过输入(input)和输出(output)接口(I/O)电路连接。接口电路的主要任务是:进行必要的电气隔离,防止干扰信号引起误动作。要用光电耦合器或继电器将CNC装置和机床之间的信号在电气上加以隔离。I/O信号经接口电路送至系统寄存器的某一位,CPU定时读取寄存器状态,经数据滤波后作相应处理。同时CPU定时向输出接口送出相应的控制信号。
(5)位置控制器
CNC装置中的位置控制单元又称为位置控制器或位置控制模块。位置控制主要是对数控机床的进给运动的坐标轴位置进行控制。例如,工作台前后左右移动、主轴箱的上下移动,围绕某一直线轴旋转运动等。轴控制是数控机床上要求最高的位置控制,不仅对单个轴的运动和位置的精度有严格要求,而且在多轴联动时,还要求各移动轴有很好的动态配合。
对主轴的控制要求在很宽的范围内速度连续可调,并且每一种速度下均能提供足够的切削所需的功率和转矩。在某些高性能的CNC机床上还要求主轴位置可任意控制(即C轴位置控制)。
(6)MDI/CRT接口
MDI接口即手动数据输入接口,数据通过操作面板上的键盘输入。CRT接口是在CNC软件配合下,在显示器上实现字符和图形显示。显示器多为电子阴极射线管(CRT)。近年来已经开始出现平板式液晶显示器(LCD),使用这种显示器可大大缩小CNC装置的体积。
(7)可编程控制器(PLC)
它是用来代替传统机床强电的继电器逻辑控制,利用PLC的逻辑运算功能实现各种开关量的控制。“内装型”PLC从属于CNC装置,PLC与NC之间的信号传送在CNC装置内部实现。PLC与MT(机床)间则通过CNC输入/输出接口电路实现信号传输。数控机床中的PLC多采用内装式,它已成为CNC装置的一个部件。“独立型”PLC又称“通用型”PLC,“独立型”PLC不属于CNC装置,可以自己独立使用,具有完备的硬件和软件结构。
(8)通信接口
该接口用来与外设进行信息传输,如与上级计算机或直接数字控制器DNC等进行数字通信。
2.2.2 多微处理器结构
随着机械制造技术的发展,对数控机床提出了更复杂功能的要求,以及更高速度和精度的要求,以适应更高层次的需要。为此,多微处理器硬件结构得到迅速发展,许多数控装置都采用这种结构,它代表了当今数控系统的新水平。其主要特点有:采用模块化结构,具有比较好的扩展性;提供多种可供选择的功能,配置了多种控制软件,以适应多种机床的控制;具有很强的通信能力,便于进入FMS、CIMS。
多微处理器结构的CNC装置中有两个或两个以上微处理器,所以称为多微处理器结构。多微处理器CNC装置一般采用两种结构形式,即紧耦合结构和松耦合结构。在前一种结构中,由各微处理器构成处理部件,处理部件之间采取紧耦合方式,有集中的操作系统,共享资源。在后一种结构中,由各微处理器构成功能模块,功能模块之间采取松耦合方式,有多重操作系统,可以有效地实行并行处理。
(1)多微处理器CNC装置的功能模块
多微处理器CNC装置的结构都采用模块化技术,设计和制造了紧耦合的许多功能组件电路或功能模块。CNC装置中包括哪些模块,可根据具体情况合理安排。一般由下面几种功能模块组成。
① CNC管理模块 管理模块管理和组织整个CNC系统的工作,主要包括初始化、中断管理、总线裁决、系统出错识别和处理、软件硬件诊断等功能。
② CNC插补模块 该模块完成零件程序的译码、刀具半径补偿、坐标位移量的计算和进给速度处理等插补前的预处理。然后进行插补计算,为各坐标轴提供位置给定值。
③ PLC模块 零件程序中的开关功能和由机床来的信号在这个模块中作逻辑处理,实现各功能和操作方式之间的联锁,机床电气设备的启停、刀具交换、转台分度、工件数量和运转时间的计数等。
④ 位置控制模块 插补后的坐标位置给定值与位置检测装置测得的位置实际值进行比较,进行自动加减速、回基准点、伺服系统滞后量的监视和漂移补偿,最后得到速度控制的模拟电压,去驱动进给电机。这些工作都由位置控制模块完成。
⑤ 存储器模块 该模块为程序和数据的主存储器,或为各功能模块间进行数据传送的共享存储器。
⑥ 操作面板监控和显示模块 零件程序、参数、各种操作命令和数据的输入、输出、显示所需要的各种接口电路。
如果CNC装置需要扩展功能,则可再增加相应的模块。
(2)多微处理器CNC装置的两种典型结构
多微处理器CNC装置一般采用总线互联方式,来实现各模块之间的互联和通信,典型的结构有共享总线和共享存储器两种结构。
① 共享总线结构 以系统总线为中心的多微处理器CNC装置,把组成CNC装置的各个功能部件划分为带有CPU或DMA器件的主模块和不带CPU或DMA器件的从模块(如各种RAM,ROM模块,I/O等)两大类。所有主、从模块都插在配有总线插座的机柜内,共享严格设计定义的标准系统总线。系统总线的作用是把各个模块有效地连接在一起,按照标准协议交换各种数据和控制信息,构成完整的系统,实现各种预定的功能,如图2-3所示。

图2-3 多微处理器共享总线结构框图
这种结构中只有主模块有权控制使用系统总线,由于有多个主模块,系统设有总线仲裁电路来裁决多个主模块同时请求使用总线而造成的竞争,以便解决某一时刻只能由一个主模块占有总线的矛盾。每个主模块按其负担的任务的重要程度,已经预先安排好优先级别的顺序。总线仲裁电路的目的,就是在它们争用总线时,判别出各模块优先级的高低。
这种结构中的各微处理器CPU模块共享总线时,会引起“竞争”,使信息传输效率降低,总线一旦出现故障,会影响全局。但由于其结构简单、系统配置灵活、实现容易、无源总线造价低等优点而被广泛采用。
② 共享存储器结构 在这种结构中,通常采用多端口存储器来实现各微处理器之间的连接与信息交换,由多端口控制逻辑电路解决访问冲突,其结构框图如图2-4所示。

图2-4 多微处理器共享存储器结构框图
图2-5是一个双端口存储器结构,它配有两套数据、地址与控制线,可供两个端口访问,访问优先权预先安排好。当两个端口同时访问时,由内部硬件电路裁决其中一个端口优先访问。

图2-5 双端口存储器结构框图
但这种方式由于同一时刻只能有一个微处理器对多端口存储器读或写,所以功能复杂。当要求微处理器数量增多时,会因争用共享存储器而造成信息传输的阻塞,降低系统效率,因此扩展功能很困难。
2.2.3 专用型结构数控装置和通用型结构数控装置
① 专用型结构 专用型结构数控装置是厂商专门设计和制造的,其特点是专用性强,布局合理,但没有通用性,硬件之间彼此不能交换。这类CNC装置包括FANUC数控装置、SIEMENS数控装置等。
② 通用性结构 这类CNC系统是以工业PC机作为CNC装置的支撑平台,再由各数控厂商根据需要装入自己的控制卡和数控软件构成相应的CNC装置。由于工业PC机大批量生产,成本很低,因而也就降低了CNC系统的成本,同时工业PC机维护和更换均很容易。如美国的ANILAM公司和AI公司生产的CNC装置均属这种类型。
2.2.4 开放式数控系统
(1)开放式数控系统的特点
传统的数控系统是一种专用封闭式系统,各个厂家的产品之间以及与通用计算机之间不兼容;维修、升级困难,维修费用高;专用封闭式数控系统的发展一般滞后5年左右,在计算机技术迅猛发展的今天,这是一个相当长的时间。上述特点严重制约着数控技术的发展。针对这种情况,人们提出了开放式数控系统的概念,国内外正在大力研究开发开放式数控系统,有的已经进行使用。
开放式数控系统目前尚无统一的定义,它应该是一个模块化、可重构、可扩充的软硬件控制系统。它采用分布式控制原则,采用系统、子系统和模块分级式的控制结构,其构造是可移植和透明的;它可以根据用户的需要方便地重现、重构、编辑,以便实现一个系统多种用途;系统中各模块相互独立,各模块接口协议明确。
以个人计算机(PC)为基础的开放式数控系统,利用带有Windows平台的个人计算机,使得开发工作量大大减少,而且很容易实现多轴、多通道控制、实时三维实体图形显示和自动编程等,可以实现数控系统三种不同层次的开放。
① CNC可以直接地或通过网络运行各种应用软件 强有力的软件包(例如数字化)能作为许可证软件来执行。各种车间编程软件、刀具轨迹检验软件、工厂管理软件、通信软件、多媒体软件都可在控制器上运行,这大大改善了CNC的图形显示、动态仿真、编程和诊断功能。
② 用户操作界面的开放 使CNC系统的用户接口有其自己的操作特点,且更加友好,并具备特殊的诊断功能(如远距离诊断)。
③ CNC内核的深层次开放 通过执行用户自己的C或C++语言开发程序,就可以把应用软件加到标准CNC的内核中,称为编译循环。CNC内核系统提供已定义的出口点,机床制造厂商或用户把自己的软件连接到这些出口点,通过编译循环,将其知识、经验、诀窍等专用工艺集成到CNC系统中去,形成独具特色的个性化数控机床。这样三个层次的全部开放,能满足机床制造厂商和最终用户的种种需求,这种控制技术的柔性,使用户能十分方便地把CNC应用到几乎所有应用场合。总之,无论是以个人计算机(PC)为基体,加上CNC系统的主要控制部分而成的数控系统,还是以CNC系统为主,加上个人计算机的有关部分而成的数控系统,都有各自的优势。
(2)国内外开放式数控系统研究简介
开放式数控系统的优越性已为越来越多的厂商和用户所认同,许多国家纷纷进行了研究开发,美国于1987年提出了NGC(Next Generation Workstation/Machine Controller)计划,企图通过实现基于相互操作和分级式软件模块的“开放式系统体系结构标准规范”。NGC计划的目的是产生、制造并批准一个能够成为工业标准的开放式系统控制器的规范(Spefication for an Open system Architecture Standard, SOSAS)。在SOSAS中提出了极为重要的九个功能设计概念。
a.分级式的控制结构,指出了功能性的分解。
b.分布式的控制适应在单个工作站的多机控制。
c.按系统、子系统和模块进行分类。
d.虚拟机械方便了模块间的相互交换和相互操作的能力。
e.控制程序由三级设计表示。
f.信息通过中性制造机械语言(Neutral Manufacturing Language,NML)传递。
g.公共的Look和Feel是人机接口的一部分。
h.信息库管理所要求的信息,并包括实时数据。
i.传感器/操作部件的操作按照标准协议进行。
欧盟提出了OSACA(Open System Architecture for Control within Automation System)计划,日本也提出了OSEC(Open System Environment for Controller)计划。日本OSEC开放系统体系结构见图2-6。

图2-6 OSEC开放系统体系结构
我国从“八五”时期开始进行数控科技联合攻关,设计开发了多种拥有自主版权的开放式数控系统,如华中Ⅰ型、航天Ⅰ型、蓝天Ⅰ型等。
航天数控系统平台是以PC机体系结构为基础构成的开放式数控系统平台,如图2-7所示为单机数控系统平台。它既可以依据此系统平台直接构成单机数控系统,也可以利用此系统平台为基础,与通用PC机互联构成多机或分布式数控系统,如图2-8所示。

图2-7 单机数控系统平台

图2-8 多机数控系统平台
系统平台能支持的数控专用I/O模板数最大为7块:可依据具体系统要求灵活配置。最大的控制轴数为16根轴(共4块位置控制模板,每块模板可控制4根轴);最大的I/O点数为240入/136出,共376个点(包括1块多功能板,80入/16出,5块通用I/O板,每块I/O板32入/24出)。