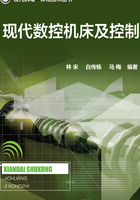
1.5 现代数控机床的发展趋势
在轿车工业领域,年产30万辆的生产节拍是40s/辆,而且多品种加工是轿车装备必须解决的重点问题之一;在航空和宇航工业领域,其加工的零部件多为薄壁和薄筋,刚度很差,材料为铝或铝合金,只有在高切削速度和切削力很小的情况下,才能对这些筋、壁进行加工。近来采用大型整体铝合金坯料“掏空”的方法来制造机翼、机身等大型零件来替代多个零件通过众多的铆钉、螺钉和其他连接方式拼装,使构件的强度、刚度和可靠性得到提高。这些都对数控机床提出了高速、高精和高柔性的要求。
现代数控机床发展趋势主要体现在如下几个方面。
(1)加工高精化
现代科学技术的发展、新材料及新零件的出现,对精密加工技术不断提出新的要求,提高加工精度,发展新型超精密加工机床,完善精密加工技术,以适应现代科技的发展,是现代数控机床的发展方向之一。其精度已从微米级到亚微米级,乃至纳米级。
提高数控机床的加工精度,一般可通过提高数控系统的控制精度和采用机床误差补偿技术来实现。
在提高数控系统的控制精度方面,通常采取采用高速插补技术,以微小程序段实现连续进给,使CNC控制单位精细化;采用高分辨率位置检测装置,提高位置检测精度(日本交流伺服电动机已有装上106脉冲/r(转)的内藏位置检测器,其位置检测精度能达到0.01mm/脉冲);位置伺服系统采用前馈控制与非线性控制等方法。
在机床误差补偿技术方面,除采用反向齿隙补偿、丝杠螺距误差补偿和刀具补偿等技术外,可采用反向间隙补偿、丝杠螺距误差补偿和刀具误差补偿等技术; 还可采用设备的热变形误差补偿和空间误差的综合补偿技术。研究结果表明,综合误差补偿技术的应用可将加工误差减少60%~80%。
采用网格解码器检查和提高加工中心的运动轨迹精度,并通过仿真预测机床的加工精度以保证机床的定位精度和重复定位精度,使其性能长期稳定,能够在不同运行条件下完成多种加工任务,并保证零件的加工质量。
近10多年来,普通级数控机床的加工精度已由±10μm提高到±5μm,精密级加工中心的加工精度则从±(3~5)μm,提高到±(1~1.5)μm。主轴回转精度要求达到0.01~0.05μm,加工圆度为0.1μm,加工表面粗糙度Ra=0.003μm等。
(2)运行高速化
提高生产率是机床技术追求的基本目标之一。数控机床高速化可充分发挥现代刀具材料的性能,不但可大幅度提高加工效率、降低加工成本,而且还可提高零件的表面加工质量和精度,对制造业实现高效、优质、低成本生产具有广泛的适用性。
要实现数控设备高速化,首先要求数控系统能对由微小程序段构成的加工程序进行高速处理,以计算出伺服电动机的移动量。同时要求伺服电动机能高速度地作出反应,开发出CPU已发展到32位以及64位的数控系统,频率提高到几百兆赫,上千兆赫,是提高数控系统高速处理能力的有效手段。
实现数控设备高速化的关键是提高切削速度、进给速度和减少辅助时间。高速数控加工源于20世纪90年代初,以电主轴(实现高主轴转速)和直线电动机(实现高直线移动速度)的应用为特征,使得主轴转速大大提高,主轴转速达到了50000~100000 r/min,主轴最高转速达200000r/min,主轴转速的最高加(减)速度为(2~5)g;进给速度可达60~120m/min,进给的加速度和减速度达到(1~2)g。刀到刀的换刀时间可以达到0.6s,切削到切削的换刀时间可以达到2.8s。工作台(托盘)交换时间4.3s。目前车削和铣削的切削速度已达到5000~8000 m/min,工作台的移动速度,当分辨率为1μm时,在100 m/min(有的到200 m/min)以上,当分辨率为0.1μm时,在24 m/min以上。自动换刀速度在1s以内,小线段插补进给速度达到12 m/min。如日本新泻铁工所生产的UHSIO型超高速数控立式铣床主轴最高转速高达100000 r/min,中等规格加工中心的快速进给速度从过去的8~12m/min提高到60m/min。加工中心换刀时间从5~10s减少到小于1s,而工作台交换时间也由过去的12~20s减少到2.5s以内。目前国外先进加工中心的刀具交换时间普遍已在1s左右,高的已达0.5s。德国Chiron公司将刀库设计成篮子样式,以主轴为轴心,刀具在圆周布置,其刀到刀的换刀时间仅0.9s。
(3)功能复合化
复合化是指在一台设备能实现多种工艺手段加工的方法。增加数控机床的复合加工功能将进一步提高其工序集中度,不仅可减少多工序加工零件的上下料时间,而且更主要地可避免零件在不同机床上进行工序转换而增加的工序间输送和等待的时间,尤其在未组成有效的生产线的条件下,这种工序间的等待时间将远远地超过零件在机床上的工作时间,从而延长了零件的生产周期。
数控机床的发展已模糊了粗精加工工序的概念。加工中心的出现,又把车、铣、镗等工序集中到一台机床来完成,打破了传统的工序界限和分开加工的工艺规程,可最大限度地提高设备利用率。如镗铣钻复合——加工中心(ATC),五面加工中心(ATC,主轴立卧转换);车铣复合——车削中心(ATC,动力刀头);铣镗钻车复合——复合加工中心(ATC,可自动装卸车刀架);铣镗钻磨复合——复合加工中心(ATC,动力磨头);可更换主轴箱的数控机床——组合加工中心。
复合数控机床的高效化可用数控五面加工龙门铣床说明,它使零件的生产周期缩短至工序分散的非数控机床的16%,同时又使加工过程中的切削时间比率由17%增至70%,大大提高了机床的利用率,同时由于减少多次安装零件引起的误差,易于保证加工精度。
为了进一步提高工效,现代数控机床又采用了多主轴、多面体切削,即同时对一个零件的不同部位进行不同方式的切削加工,如各类五面体加工中心。另外,现代数控系统的控制轴数也在不断增加,有的多达十五轴,其同时联动的轴数已达六轴。沈阳机床股份有限公司开发的五轴车铣中心,刀库容量16,可控X、Y、Z、B、C五个轴,具有车削中心加铣削中心的特点。上海重型机床厂开发的双主轴倒顺式立式车削中心,第一主轴正置,第二主轴倒置。主轴具有C轴功能,采用12工位动力刀架,具有自动上下料装置和全封闭等多道防护装置,可一次上料完成零件的正反面加工,包括车削、镗孔、钻孔、攻螺纹等多道工序。适用于大批量轮毂、盘类零件加工。
由于复合数控机床具有良好的工艺适用性,避免了在制品的储存和传输等环节,有力地支持了准时制(JIT),因此对它的研发已被给予了极大的关注。尽管就功能来讲各种复合数控机床的界限会渐现淡化,但各机床制造厂仍保留了各自的特点和侧重点,使复合数控机床呈现出多样性的创新结构。
日本MAZAK公司的INTEGREX车铣中心是近年出现的一种新颖的复合数控机床。它拥有一套类似加工中心配置的自动换刀装置,能实现X、Y、Z轴运动,并具有B轴摆动的主轴头和C轴控制的主轴,既能作铣、钻、镗的动力头,也能作车刀夹持刀架。左右两侧分别装有主副两个车削用电主轴,可以不需对工件调头安装来完成两端的加工。因此它不仅能加工有斜面、斜孔的回转体零件,也能进行以前要用数控铣床或加工中心完成的模具和气缸盖等零件加工。
此外,德国EMAG公司的VSC系列立式多功能制造中心,它的主轴采用倒置式结构,应用模块化的结构设计可配置各种适用的动刀刀塔,通过改变刀具系统的组成,实现车、钻、铣、磨和滚齿等加工,完成各类盘套类零件的制造。
(4)控制智能化
随着人工智能在计算机领域的不断渗透与发展,为适应制造业生产柔性化、自动化发展需要,智能化正成为数控设备研究及发展的热点,它不仅贯穿在生产加工的全过程(如智能编程、智能数据库、智能监控),还贯穿在产品的售后服务和维修中,目前采取的主要技术措施包括如下几点。
① 自适应控制技术 自适应控制可根据切削条件的变化,自动调节工作参数,使加工过程中能保持最佳工作状态,从而得到较高的加工精度和较小的表面粗糙度,同时也能提高刀具的使用寿命和设备的生产效率,达到改进系统运行状态的目的。如通过监控刀削过程中的刀具磨损、破损、切屑形态、切削力及零件的加工质量等,向制造系统反馈信息,通过将过程控制、过程监控、过程优化结合在一起,实现自适应调节。
② 专家系统技术 将专家经验和切削加工一般规律与特殊规律存入计算机中,以加工工艺参数数据库为支撑,建立具有人工智能的专家系统,提供经过优化的切削参数,使加工系统始终处于最优和最经济的工作状态,从而提高编程效率和降低对操作人员的技术要求,缩短生产准备时间。如日本牧野公司在电火花数控系统MAKINO-MCE20中,用带自学习功能的神经网络专家系统代替操作人员进行加工监视。
③ 智能故障诊断与自修复技术 智能故障诊断技术可根据已有的故障信息,应用现代智能方法(AI、ES、ANN等),实现故障快速准确定位的技术。智能故障自修复技术能根据诊断确定故障原因和部位,以自动排除故障或指导故障的排除技术。智能自修复技术集故障自诊断、故障自排除、自恢复、自调节于一体,并贯穿于加工过程的整个生命周期。在整个工作状态中,系统随时对CNC系统本身以及与其相连的各种设备进行自诊断、检查。一旦出现故障,立即采用停机等措施,并进行故障报警,提示发生故障的部位、原因等,并利用“冗余”技术,自动使故障模块脱机,而接通备用模块,以确保无人化工作环境的要求。
④ 智能化交流伺服驱动技术 目前已开始研究能自动识别负载,并自动调整参数的智能化伺服系统,包括智能主轴交流驱动装置和智能化进给伺服装置,使驱动系统获得最佳运行。
⑤ 模式识别技术 应用图像识别和声控技术,使机器自己辨认图样,按照自然语音命令进行加工。
(5)体系开放化
自从世界上第一台数控机床于1958年在美国麻省工学院(MIT)出现以来的几十年的时间内,数控系统一直沿着传统的闭式结构向前发展。对用户来说,这种闭式数控系统只是一个被定义了输入和输出的黑匣子,其内部细节是不可知的。这种数控系统最大缺点在于,无论是制造商还是终端用户,在原来基础上很难或几乎不可能再加入新的控制策略方案和扩展新功能。随着计算机在制造过程中的广泛应用,改善制造过程性能的需求越来越强烈,这种封闭式结构的局限性也越来越明显。
为解决传统的数控系统封闭性和数控应用软件的产业化生产存在的问题。目前许多国家对开放式数控系统进行研究。IEEE将开放式数控系统定义为是具有在不同的工作平台上均能实现系统功能,且可以与其他的系统应用进行互操作的系统。一个开放式的数控系统,系统构件(软件和硬件)具有标准化(Standardization)与多样化( Diversification)和互换性(Interchangeability)的特征;另外,允许通过对构件的增减来构造系统,实现系统“积木式”的集成。构造应该是可移植的和透明的。开放式数控系统体系结构见图1-18。

图1-18 开放式数控系统体系结构
开放体系结构CNC具有以下特点。
① 向未来技术开放:由于软硬件接口都遵循公认的标准协议,只需少量的重新设计和调整,新一代的通用软硬件资源就可能被现有系统所采纳、吸收和兼容,这就意味着系统的开发费用将大大降低而系统性能与可靠性将不断改善并处于长生命周期。
② 标准化的人机界面:标准化的编程语言,方便用户使用,降低了和操作效率直接有关的劳动消耗。
③ 向用户特殊要求开放:更新产品、扩充能力、提供可供选择的硬软件产品的各种组合以满足特殊应用要求,给用户提供一个方法,从低级控制器开始,逐步提高,直到达到所要求的性能为止。另外用户自身的技术诀窍能方便地融入,创造出自己的名牌产品。
④ 可减少产品品种,便于批量生产、提高可靠性和降低成本,增强市场供应能力和竞争能力。
(6)驱动并联化
并联机床是指用并联机构作为进给传动机构的数字控制机床。这种新型机床是现代机器人与传统加工技术相结合的产物,它打破了传统机床结构的概念,抛弃了固定导轨的刀具导向方式,没有传统机床所必需的床身、立柱、导轨等制约机床性能提高的结构,采用了多杆并联机构驱动,大大提高了机床的刚度,使加工精度和加工质量都有较大的改进,如图1-19所示为并联机床结构示意图。另外,由于其进给速度的提高,从而使高速、超高速加工更容易实现。由于这种机床具有高刚度、高承载能力、高速度、高精度以及重量轻、机械结构简单、制造成本低、标准化程度高等优点,在许多领域都得到了成功的应用。

图1-19 并联机床结构示意图
并联机床作为一种新型的加工设备,已成为当前机床技术的一个重要研究方向,受到了国际机床行业的高度重视,被认为是“自发明数控技术以来在机床行业中最有意义的进步”和“21世纪新一代数控加工设备”。
(7)交互网络化
为了适应FMC、FMS以及进一步联网组成CIMS的要求,先进的CNC系统为用户提供了强大的联网能力,除有RS232串行接口、RS422等接口外,还带有远程缓冲功能的DNC接口,可以实现几台数控机床之间的数据通信和直接对几台数控机床进行控制。现代数控机床为了适应自动化技术的进一步发展和工厂自动化规模越来越大的要求,满足不同厂家不同类型数控机床联网的需要,已配备与工业局域网(LAN)通信的功能以及MAP(Manufacturing Automation Protocol——制造自动化协议)接口,为现代数控机床进入FMS及CIMS创造了条件,促进了系统集成化和信息综合化,使远程操作和监控、遥控及远程故障诊断成为可能。不仅利于数控系统生产厂对其产品的监控和维修,也适于大规模现代化生产的无人化车间,实行网络管理,还适于在操作人员不宜到现场的环境(如对环境要求很高的超精密加工和对人体有害的环境)中工作。
交互网络化支持网络通信协议,既满足单机需要,又能满足FMC、FMS、CIMS对基层设备集成要求的数控系统,该系统是形成“全球制造”的基础单元。可以实现网络资源共享;数控机床的远程(网络)控制;基于网络的数字化服务(数控机床的远程监视、故障诊断、远程网络培训与教学、电子商务)等功能。