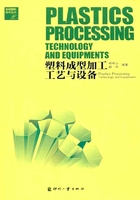
1.12 塑料在加工过程中的物理与化学变化
在成型加工过程中,聚合物会发生一些物理和化学变化。例如在某些条件下,聚合物能够结晶或改变结晶度,能借外力作用产生分子取向,当聚合物分子链中存在薄弱环节或有活性反应基因(活性点)时,还能发生降解或交联反应。
加工过程出现的这些物理和化学变化,不仅能引起聚合物出现如力学、光学、热性质以及其他性质的变化,而且对加工过程本身也有影响。这些物理和化学变化有些对制品性质是有利的,有些则是有害的。
1.12.1 加工过程中的结晶
塑料成型、薄膜拉伸及纤维纺丝过程中常出现聚合物结晶现象,但结晶速度慢、结晶具有不完全性和结晶聚合物没有清晰的熔点是大多数聚合物结晶的基本特点。
当聚合物熔体或浓溶液冷却时,熔体中的某些有序区域开始形成尺寸很小的晶胚,晶胚长大到某一临界尺寸时转变为初始晶核;然后大分子链通过热运动在晶核上进行重排而生成最初的晶片,在此晶片上生长而形成球晶,如图1-34所示。

图1-34 球晶的结构和生长过程示意图
聚合物结晶的不完全性,通常用结晶度表示。一般聚合物的结晶度在10%~60%范围。
结晶受温度的影响较大,如图1-35所示。

图1-35 温度对聚合物结晶的影响
显然,成型过程中的冷却速率会严重地影响聚合物的结晶速度。如果将聚合物熔体从高温骤然降至聚合物的玻璃化转变温度以下,即使是结晶性聚合物也可能得到非晶态固体。
以上讨论的是均相成核的结晶过程。如果在聚合物熔体中有其他物质,则这些外来物质对结晶过程的影响是比较复杂的。有的外来物质会阻碍结晶过程的进行;有的外来物质却能起到成核剂的作用,加速结晶过程,并且减少温度条件对结晶速度的影响。常用的成核剂是微量的高熔点聚合物,它可在熔体冷却时首先结晶。无机或有机结晶物质也可作为成核剂。
1.成型加工条件对结晶过程的影响
成型过程中聚合物的结晶是动态结晶,因为成型过程中熔体会受到外力作用,并产生流动、取向等。成型中聚合物的结晶过程同时还是非等温过程,原因是不仅制品中同一区域的熔体温度随时间延长而降低,而且同一时间不同区域的聚合物所处的温度也不同,这一特点在注射成型过程中体现得尤为明显。这样就使得定量地描述和预测成型工艺条件对塑料制品结晶结构的影响变得非常复杂。
(1)模具温度
温度是影响聚合物结晶过程的主要因素之一。塑料成型时,模具温度应根据制品结构及使用性能要求来确定,不同的使用场合所要求的制品性能不同,结晶结构也应随之发生变化,模具温度亦应随之调整。制品的结构(如厚度)不同,熔体冷却速度不同,要得到同样结晶结构的制品,所选择的模具温度也不同。
影响聚合物熔体在模具中冷却速度的一个很重要的因素就是聚合物熔点Tm与模具温度TM之差,也称过冷度△T(Tm-TM)。根据过冷度的不同,可将聚合物成型时的冷却分为三种情况。
①等温冷却。此时,过冷度△T很小,模具温度 TM接近于聚合物熔点Tm,熔体进入模具后冷却缓慢,结晶过程在近似于等温条件下进行。在这种情况下,由于晶核生成速度低,且生成的晶核数目少,而聚合物分子链的运动活性很大,故制品中易生成粗大的晶粒,但晶粒数量少,结晶速度慢。粗大的晶粒结构会使制品韧性降低,力学性能劣化。同时,冷却速度较慢会使成型周期延长,生产效率降低。另外,由于模具温度太高,成型出的制品刚度往往不够,易扭曲变形,实际生产中较少采用这种操作。
②快速冷却。采用快速冷却时,过冷度△T很大,TM远低于 Tm。熔体进入模具后,接触温度较低的模腔表面,使熔体快速冷却,此时聚合物分子链运动重排的松弛速度滞后于温度的降低速度,这一点对制品表层的影响尤为突出。首先,由于模具温度很低,靠近模具的制品表层部分温度降低较快,但由于聚合物的热导率较小,制品芯部温度下降较缓慢,这样造成制品表层和芯部温差较大,不仅会在结晶速度和结晶度上表现为皮层低于芯部,而且会出现晶粒尺寸上皮层小于芯部,这样易造成制品产生较大的热内应力;其次,由于熔体温度骤冷,造成制品总的结晶度很低,这无疑会使结晶聚合物的物理及力学性能大大降低;最后,迅速冷却造成制品中形成的结晶结构不完善或不稳定,制品在以后的储存和使用过程中会自发地使这种不完善或不稳定的结晶结构转化为相对完善或稳定的结构,即在制品中发生后结晶和二次结晶,从而造成制品形状及尺寸的不稳定性。
与等温冷却相比,快速冷却虽然大大缩短了成型周期,提高了生产效率,但通常制品的性能较难达到要求,因此,实际生产中这种操作运用得也不多。
③中速冷却。中速冷却时,一般控制模具温度 TM在聚合物的玻璃化转变温度Tg与聚合物的最大结晶速度温度之间。此时,靠近表层的聚合物熔体在较短时间内形成凝固壳层,在冷却过程中最早结晶,制品内部温度在较长时间处于 Tg以上,有利于晶体结构的生长、完善和平衡。在理论上,这一冷却速度能获得晶核数量与其生长速率之间最有利的比例关系。晶体生长好,结晶完善且稳定,故制品的尺寸稳定性好。同时,成型周期也较短,因此是实际生产中常常被采用的一种冷却方式。
(2)熔融温度和熔融时间的影响
结晶性聚合物在成型过程中必须要经过熔融塑化阶段,塑化中熔融温度及时间也会影响最终成型出的制品的结晶结构。若塑化时熔融温度低且保持时间较短,熔体中就可能残存较多的晶核,则其再次冷却时就会存在异相成核,结晶速度快,晶粒尺寸小且均匀,制品的力学性能及耐热性能等均较理想;如果熔融温度较高且保持时间较长,分子热运动加剧,分子就难以维持原来的晶核,熔体中没有残存晶核或残存晶核很少,则其再次冷却时主要为均相成核,即结晶速度慢,晶粒尺寸大且不均匀。
(3)应力作用
应力对结晶的影响表现在如下几个方面:首先,应力的大小及作用方式会明显改变聚合物的晶体结构和形态,如剪切应力可以使聚合物的结晶形态发生改变,产生静态下得不到的结晶形态,根据作用力的方向和大小,大致可以得到伸直链晶体、片晶、串晶或柱晶。其次,应力(剪切应力和拉伸应力)的存在会增大聚合物熔体的结晶速度,并降低最大结晶速度温度。这是因为在外界应力作用下,聚合物分子链沿力的方向取向,形成局部有序区域,容易诱导产生晶胚,并进而成长为晶核,使晶核数量增加,从而加速结晶过程。再次,通常随着剪切或拉伸应力(或应变)的增加,聚合物的结晶度也增大。最后,压应力的存在会降低聚合物熔体的结晶温度,如图1-36所示。

图1-36 应力对聚合物结晶的影响
2.结晶对制品性能的影响
(1)结晶对制品密度及光学性能的影响
由于结晶时聚合物分子链作规整、紧密排列,所以晶区密度高于非晶区密度,因而制品的密度也随结晶度的增加而增大。
物质的折射率与密度密切相关,制品中晶区与非晶区折射率也不同。这样,当光线通过结晶性聚合物制品时,就会在晶区与非晶区的界面上发生反射和折射,不能直接通过制品,因此结晶性聚合物制品通常呈乳白色,不透明。但如果晶区与非晶区密度十分接近或者晶区尺寸小于可见光的波长,则结晶性聚合物制品也可具有较好的透明性。在成型过程中,常采用加入成核剂减小晶区尺寸的方法来提高结晶性聚合物制品的透明度。
(2)结晶对制品力学性能的影响
结晶对聚合物制品力学性能的影响,与制品中非晶区所处的力学状态有关。如果制品中非晶区处于橡胶态,则随着结晶度的增加,制品的硬度、弹性模量、拉伸强度增大,而冲击强度、断裂伸长率等韧性指标降低;如果制品中晶区处于玻璃态,随着结晶度的增加,制品变脆,拉伸强度也下降。
除结晶度外,聚合物的结晶形态、晶料尺寸和数量也对制品的力学性能产生影响。一般为使制品获得良好的综合力学性能,总是希望制品内部形成细小而均匀的晶粒结构。
另外需要注意的是,由于聚合物的结晶度通常达不到100%,制品内不同区域的结晶度、结晶结构及形态不同,因此各部分的力学性能会产生差异,这也是结晶性聚合物成型过程中,制品产生翘曲与开裂的原因之一。
(3)结晶对热性能及其他性能的影响
结晶有利于提高制品的耐热性能。例如,结晶度为70%的聚丙烯热变形温度为124.9℃,结晶度变为95%后,热变形温度提高到151.1℃。耐热性能提高后,在相同温度条件下,制品的刚度也会提高,而制品获得足够的刚度是注塑制品脱模的前期条件之一。因此,提高制品的结晶度可以减少制品在模具内的冷却时间,缩短成型周期,提高生产效率。
结晶后由于分子链排列规整、紧密,与无定形聚合物相比,能更好地阻挡各种试剂的渗入,也将影响到气体、蒸汽或液体对聚合物的渗透性。因此,随着结晶度的增加,制品的耐溶剂性得到提高,同时制品的阻隔性提高。
1.12.2 塑料加工过程中的取向
聚合物在加工过程中均要受到剪切应力和拉伸应力的作用,因此在拉伸应力方向上要产生取向。高分子链是几何上高度不对称的,容易沿外力方向上取向。高分子链一般来说具有一定的柔性,也容易在外力作用下沿外力方向排列。高分子链具有分子运动的多样性,链段、晶粒等均可以在外力作用下取向。因此,聚合物在加工过程中取向是不可避免的。
聚合物的链段、分子链、结晶性聚合物的晶片以及具有几何不对称性的纤维状填料,在某些情况下很容易沿着某特定方向作占优势的平行排列,这就是取向。因为在挤出、注塑、压延等加工过程中,由于外场作用,大分子链或链段都表现出不同程度的取向。一些聚合物材料制品呈取向态结构,赋予了制品更优良的力学性能,使制品能满足更高的使用要求,如纤维、打包带、捆扎用的撕裂膜以及塑料薄膜、塑料瓶、塑料桶等。
1.成型加工过程中的取向作用
非晶聚合物大分子的取向(包括流动取向和拉伸取向)有链段取向和分子链取向两种类型。链段取向可以通过单键的内旋转造成的链段运动来完成,在高弹态就可进行;整个大分子链的取向需要大分子各链段的协同运动才能实现,只有在黏流态才能进行。取向过程是链段运动的过程,必须克服聚合物内部的黏滞阻力,链段与大分子链多种运动单元所受的阻力大小不同,因而取向过程的速度也不同。在外力作用下最早发生的是链段的取向,进一步才发展成为大分子链的取向,如图1-37所示。

图1-37 非晶态聚合物的拉伸取向
取向过程是大分子链或链段的有序化过程,而热运动却是使大分子趋向紊乱无序,即解取向过程。取向需靠外力场的作用才能得以实现,而解取向却是一个自发过程。取向态在热力学上是一种非平衡态,一旦除去外力,链段或分子链便自发解取向而恢复原状。因此,欲获得取向材料,必须在取向后迅速降温到玻璃化温度以下,将分子链或链段的运动冻结起来。
2.取向作用对性能的影响
根据外力作用的方式不同,取向可分为拉伸取向和流动取向。拉伸取向是指聚合物的取向单元(包括链段、分子链、晶片、纤维状填料等)在拉伸力的作用下产生的,并且特指热塑性聚合物在其玻璃化转变温度Tg与熔点Tm(或黏流温度Tf)范围内所发生的取向。流动取向是指聚合物处于可流动状态时,由于受到剪切力的作用而发生流动,取向单元沿流动方向所作的平行排列。
根据取向的方式不同,取向又可分为单轴取向和双轴取向。单轴取向是指取向单元沿着一个方向作平行排列而形成的取向状态,双轴取向则指取向单元沿着两个互相垂直的方向取向。
根据取向过程中聚合物的温度分布与变化情况,取向又可分为等温取向和非等温取向。在注射成型时,聚合物在料筒和喷嘴中的取向过程可近似看做等温取向;而在各种流道、浇口和模腔中的取向都是非等温取向。发生在流道、浇口和模腔中的非等温取向对制品的质量和性能将产生很大影响。
根据聚合物取向时的结构状态不同,还可将取向分为结晶取向和非结晶取向。结晶取向是指发生在部分结晶性聚合物材料中的取向,而非结晶取向则指无定形聚合物材料中所发生的取向。
无论是何种取向态,只要它存在于最终制品中就会造成制品性能上表现出明显的各向异性。这种各向异性有些是根据设计及使用要求在成型过程中特意形成的,如薄膜和单丝的拉伸取向,使制品沿拉伸方向的强度及光泽等提高。有的则是在成型过程中须极力避免产生的。这是因为:首先,取向(特别是流动取向)的发生过程和最终结果受很多因素影响,常常是不可预测和控制的,取向结构和状态有很大的随机性;其次,由于在成型中制品各部分所处的应力、温度场等存在差异,因此造成制品各部分的取向也是不一致的,这样制品中就容易产生内应力而使制品出现翘曲、变形甚至开裂现象;再次,取向在造成沿取向方向制品的力学及其他性能提高的同时,也造成了与取向方向垂直方向上的制品相应性能的劣化,最常见的现象就是制品易出现与取向方向平行的撕裂;最后,由于取向状态是热力学非平衡状态,当条件合适时,与之相反的解取向过程会自发进行,造成制品形状及尺寸的不稳定性,常见的现象就是取向后制品的热收缩率很大。制品成型过程中产生的不希望出现的取向应通过改良制品及模具设计、合理选择成型工艺等方法得到减小或消除。
归纳起来,取向对聚合物性能的影响有:取向使聚合物在取向方向上强度增大,使聚合物的 Tg升高,使聚合物的透明性提高,在取向方向上,线膨胀系数增加。
3.成型加工过程中的流动取向
根据取向单元的不同,可将流动取向分为聚合物分子取向和填充物取向。
(1)无定型聚合物的流动取向
以出现取向现象较为复杂和工业上广泛应用的注射成型法为例,来阐明无定型聚合物的流动取向机理。塑料注射过程中的取向如图1-38所示。

图1-38 塑料注射过程中的取向
由图1-38可以看出,塑料熔体流经浇口时产生了较高程度的取向,这种取向状态在熔体到达模具型腔壁时能被及时冷却下来而冻结固定,所以,塑料制品表面的取向程度最高。而由于塑料熔体冷却速率较慢,内部的熔体不能及时冷却下来,仍然处于较高的温度下,这时解取向速率较大,所以塑料制品内部的取向度较低。另外,随着熔体从浇口流向型腔远端,发生较大的解取向,所以,离浇口越远的地方取向度越低。上述取向过程可归纳如图1-39所示。

图1-39 注射成型的塑料制品中的取向分布
(2)填充物取向
有些填充物也是几何上不对称的,如玻璃纤维、晶须、滑石粉等,因此在流动过程中也要沿流动方向上取向。纤维状填料发生流动取向的情形比较复杂,取向机理也不完全等同于聚合物分子的取向。但是一般纤维状填料的取向方向总是与流动方向保持一致,如图1-40所示。

图1-40 纤维状填料在注射成型过程中的取向过程
值得注意的是,纤维状填料的取向在塑料制品使用过程中,一般不会由于聚合物的分子热运动而发生解取向,除非将热塑性塑料制品重新加热到黏流态,否则填料的取向将永远保留在制品中。纤维状填料的取向更大程度上依赖于剪切应力,对温度的依赖性相对较小,这一特点也是纤维状填料取向区别于聚合物分子取向之处。
4.聚合物的拉伸取向
通过拉伸取向可以制备具有特殊性能的塑料产品,如热收缩薄膜等。
在玻璃化温度Tg附近,聚合物可以进行高弹拉伸和塑性拉伸。拉伸应力小于聚合物的屈服应力时,产生高弹拉伸,为链段取向,取向度低,取向不稳定;拉伸应力大于聚合物的屈服应力时,可产生塑性取向,是整个高分子链的取向,不易恢复,取向稳定。
当温度升高到Tf以上处于聚合物的黏流态时,聚合物的拉伸称为黏流拉伸。由于温度很高,大分子活动能力强,即使应力很小也能引起大分子链的解缠结、滑移和取向。但在很高的温度下解取向发展也很快,有效取向程度低。除非迅速冷却聚合物,否则不能获得有实用性的取向结构。同时,因为熔体黏度低,拉伸过程极不稳定,容易造成液流中断。
结晶聚合物的拉伸取向通常在 Tg以上适当温度进行。拉伸时所需应力比非晶聚合物大,且应力随结晶度增加而提高。取向过程包含着晶区与非晶区的转变。结晶区的取向发展较快,非晶区的取向发展慢;当非晶区达到中等取向程度时,晶区的取向就已达到最大程度。
晶区的取向过程很复杂,取向过程包含结晶的破坏、大分子链段的重排和重结晶以及微晶的取向等,过程中并伴随有相变发生。由于聚合物熔体冷却时均倾向于生成球晶,所以拉伸过程实际上是球晶的形变过程,如图1-41所示。

图1-41 结晶聚合物的拉伸取向
影响取向的因素有:
①温度升高,有利于取向,但也有利于解取向。
②在黏流拉伸时,聚合物的取向能否固定下来,决定于聚合物的松弛时间和冷却速率。
③在Tg~Tf(Tm)之间进行拉伸,称为热拉伸,拉伸应力小,拉伸比大,拉伸速度高。
④在室温附近进行的拉伸通常称为冷拉伸,由于温度低,聚合物松弛速度慢,大的拉伸比和快的拉伸速度会引起拉伸应力急剧上升,超过极限时容易引起材料断裂。所以冷拉伸通常适用于拉伸比小、取向度小的情况。
⑤聚合物拉伸过程的热效应还会引起被拉伸材料温度升高,如要进一步提高取向度就需沿拉伸方向形成一定的温度梯度。
⑥一般来说,拉伸比越大,取向度越高,如图1-42所示。

图1-42 拉伸比对取向的影响
1.12.3 塑料在加工过程中的降解与交联
聚合物在加工过程中,要受到高温、强剪切应力等的作用,在这些强的作用下,高分子链要产生断链,因而分子量下降,这就是降解。
1.加工过程中聚合物降解机理
(1)自由基连锁降解反应
由热、应力等物理因素引起的降解属于这一类。在热或剪切力的影响下,聚合物的降解常常是无规则地选择进行的。这是因为聚合物中所有化学键的能量都十分接近的关系。
在这些物理因素作用下,降解机理也极其相似,通常是通过形成自由基的中间步骤按链锁反应机理进行,包括活性中心的产生、链转移和链减短、链终止几个阶段。
①自由基的形成。由聚合物大分子主链上任一化学键(C—C、C—O或C—H等)断裂而产生初始自由基,能量则由热或应力作用所提供。例如:

②活性链转移使链减短。初始自由基使相邻C—C键断裂,在形成新自由基的同时形成分子链末端有双键的降解产物:

或形成新自由基的同时析出单体物质:

向邻近大分子转移,产生有支链的降解产物:

③链终止。自由基重合而链终止,过程中伴随着聚合物结构的改变,
形成线型降解产物:

形成支链型降解产物:

形成交联降解产物:

(2)逐步降解
这种降解往往是在加工的高温下,聚合物含有微量水分、酸或碱等杂质进行有选择的降解,降解一般发生在碳—杂链(如C—N、C—O、C—S、C—Si等处。这是因为碳—杂链的键能较小、稳定性差的缘故。降解具有逐步反应的特征,每一步具有独立性,中间产物稳定,断链的机会随分子量增大而增大,所以随着降解反应的逐步进行,聚合物的分子量逐渐减少的同时,其分子量分散性也逐步减小。
含有酰胺、酯、缩醛的聚合物容易在高温下发生水解、酯解、酸解、胺解等降解反应。如:对PC来说,微量水分就可引起显著降解。
2.加工过程中各种因素对降解的影响
(1)聚合物结构的影响
主链上含有碳—杂原子键时容易发生降解,主链上含有叔碳原子时,容易降解,主链上含有双键时容易降解,主链上C—C键的键能还受到侧链上取代基和原子的影响。
极性大和分布规整的取代基能增加主链C—C键的强度,提高聚合物的稳定性,而不规整的取代基则降低聚合物的稳定性。
主链上不对称的氯原子易与相邻的氢原子作用发生脱氯化氢反应,使聚合物稳定性降低,所以聚氯乙烯甚至在140℃时就能分解而析出HCl。
主链中有芳环、饱和环和杂环的聚合物以及具有等规立构和结晶结构的聚合物稳定性较好,降解倾向较小。
(2)温度、氧及剪切应力的影响
温度越高,降解越快,在高温下停留时间越长,降解越厉害,如图1-43所示。

图1-43 温度对聚苯乙烯降解反应速率的影响
加工过程往往有氧气的存在,氧在高温下能使聚合物氧化生成过氧化物结构,过氧化物容易分解产生自由基,从而引发连锁降解反应,这称为热氧降解,是聚合物降解的主要历程。
在加工过程中,聚合物要反复受到应力的作用(以剪切应力为主),当剪切应力的能量超过键能时,就引起化学键的断裂,产生降解。剪切作用和热作用一起,对聚合物的降解起强烈的降解促进作用。
(3)水分的影响
微量水分是有些聚合物降解的主要因素,如PC、尼龙、ABS、聚酯等。因此,加工之前的干燥是必备的工序。
3.加工过程对降解作用的利用与避免
聚合物在加工过程出现降解后,制品外观变坏,内在质量降低,使用寿命缩短。因此加工过程大多数情况下都应设法尽量减少和避免聚合物降解。为此,通常可采用以下措施。
(1)严格控制原材料技术指标,尽量去除聚合物中的催化剂残留等杂质。
(2)使用前对聚合物进行严格干燥,特别是聚酯、聚醚和聚酰胺等聚合物存放过程容易从空气中吸附水分,用前通常应使水分含量降低到0.01%~0.05%。
(3)确定合理的加工工艺和加工条件,使聚合物能在不易产生降解的条件下加工成型。
(4)加工设备和模具应有良好的结构。主要应消除设备中与聚合物接触部分可能存在的死角或缝隙,减少过长的流道、改善加热装置、提高温度显示装置的灵敏度和冷却系统的冷却效率。
(5)在配方中考虑使用抗氧剂、稳定剂等以加强聚合物对降解的抵抗能力,如图1-44所示。

图1-44 抗氧剂对聚丙烯加工过程中的热氧降解的抑止作用
有些情况下,可以利用聚合物在加工过程中的降解效应,如:橡胶的开炼(塑炼)可降低分子量,提高加工性;聚合物共混物制备时可利用剪切效应产生的自由基,使两种或多种聚合物产生接枝、共聚等反应,从而提高共混物的性能。
4.加工过程中的交联
聚合物在加工过程中要产生交联(凝胶),大多数情况下,使聚合物产生性能变劣,主要是产生凝胶以后,流动性下降,与其他组分相容性变差,混合也不均匀,导致制品质量严重下降。
在降解的同时,也伴随交联反应。
但特别要注意的是,热固性树脂(塑料)和大部分橡胶在成型加工过程中要交联(硫化)以后才有使用价值。
热塑性塑料和热固性塑料加工的区别为:热塑性塑料加温降低熔体黏度使之产生流动变形,冷却获得形状(物理变化为主)。热固性塑料则首先加热提高流动性,使之在压力下产生流动、变形,并获得形状(物理变化为主),然后使具有活性基团的组分在较高温度下发生交联反应并最终完成硬化(化学变化为主)。
交联反应机理可分为自由基交联反应和逐步交联反应。
自由基交联反应机理是交联反应由自由基引发,反应一旦开始即按连锁过程进行:

逐步交联反应机理是反应过程中反应组分间常有氢原子转移(如加成反应)或在交联同时有低分子物生成(缩合反应)的反应,是最常见的逐步交联反应。大分子中环氧基、异氰酸基等活性官能团与交联剂(固化剂)进行的交联反应是加成交联反应的代表。
