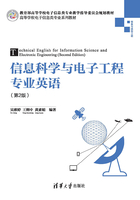
Text
Part I: The Integrated Circuit
Digital logic and electronic circuits derive their functionality from electronic switches called transistor. Roughly speaking, the transistor can be likened to an electronically controlled valve whereby energy applied to one connection of the valve enables energy to flow between two other connections.1 By combining multiple transistors, digital logic building blocks such as AND gates and flip-flops are formed. Transistors, in turn, are made from semiconductors. Consult a periodic table of elements in a college chemistry textbook, and you will locate semiconductors as a group of elements separating the metals and nonmetals.2 They are called semiconductors because of their ability to behave as both metals and nonmetals. A semiconductor can be made to conduct electricity like a metal or to insulate as a nonmetal does. These differing electrical properties can be accurately controlled by mixing the semiconductor with small amounts of other elements. This mixing is called doping. A semiconductor can be doped to contain more electrons (N-type) or fewer electrons (P-type). Examples of commonly used semiconductors are silicon and germanium. Phosphorous and boron are two elements that are used to dope N-type and P-type silicon, respectively.3
A transistor is constructed by creating a sandwich of differently doped semiconductor layers. The two most common types of transistors, the bipolar-junction transistor (BJT) and the field-effect transistor (FET) are schematically illustrated in Figure 2.1. This figure shows both the silicon structures of these elements and their graphical symbolic representation as would be seen in a circuit diagram. The BJT shown is an NPN transistor, because it is composed of a sandwich of N-P-N doped silicon. When a small current is injected into the base terminal, a larger current is enabled to flow from the collector to the emitter. The FET shown is an N-channel FET, which is composed of two N-type regions separated by a P-type substrate. When a voltage is applied to the insulated gate terminal, a current is enabled to flow from the drain to the source. It is called N-channel, because the gate voltage induces an N-channel within the substrate, enabling current to flow between the N-regions.
Another basic semiconductor structure shown in Figure 2.1 is a diode, which is formed simply by a junction of N-type and P-type silicon. Diodes act like one-way valves by conducting current only from P to N. Special diodes can be created that emit light when a voltage is applied. Appropriately enough, these components are called light emitting diodes, or LEDs. These small lights are manufactured by the millions and are found in diverse applications from telephones to traffic lights.

Figure 2.1 BJT, FET, and diode structural and symbolic representation
The resulting small chip of semiconductor material on which a transistor or diode is fabricated can be encased in a small plastic package for protection against damage and contamination from the outside world.4 Small wires are connected within this package between the semiconductor sandwich and pins that protrude from the package to make electrical contact with other parts of the intended circuit. Once you have several discrete transistors, digital logic can be built by directly wiring these components together. The circuit will function, but any substantial amount of digital logic will be very bulky, because several transistors are required to implement each of the various types of logic gates.
At the time of the invention of the transistor in 1947 by John Bardeen, Walter Brattain, and William Shockley, the only way to assemble multiple transistors into a single circuit was to buy separate discrete transistors and wire them together. In 1959, Jack Kilby and Robert Noyce independently invented a means of fabricating multiple transistors on a single slab of semiconductor material. Their invention would come to be known as the integrated circuit, or IC, which is the foundation of our modern computerized world. An IC is so called because it integrates multiple transistors and diodes onto the same small semiconductor chip. Instead of having to solder individual wires between discrete components, an IC contains many small components that are already wired together in the desired topology to form a circuit.
A typical IC, without its plastic or ceramic package, is a square or rectangular silicon die measuring from 2 to 15 mm on an edge. Depending on the level of technology used to manufacture the IC, there may be anywhere from a dozen to tens of millions of individual transistors on this small chip. This amazing density of electronic components indicates that the transistors and the wires that connect them are extremely small in size. Dimensions on an IC are measured in units of micrometers, with one micrometer (1μm) being one millionth of a meter. To serve as a reference point, a human hair is roughly 100μm in diameter. Some modern ICs contain components and wires that are measured in increments as small as 0.1μm! Each year, researchers and engineers have been finding new ways to steadily reduce these feature sizes to pack more transistors into the same silicon area, as indicated in Figure 2.2. The era of “easy” scaling is over. We are now in a period where technology and device innovations are required. Beyond 2020, new currently unknown inventions will be required.

Figure 2.2 Device scaling over time
When an IC is designed and fabricated, it generally follows one of two main transistor technologies: bipolar or metal-oxide semiconductor (MOS). Bipolar processes create BJTs, whereas MOS processes create FETs. Bipolar logic was more common before the 1980s, but MOS technologies have since accounted the great majority of digital logic ICs. N-channel FETs are fabricated in an NMOS process, and P-channel FETs are fabricated in a PMOS process. In the 1980s, complementary-MOS, or CMOS, became the dominant process technology and remains so to this day. CMOS ICs incorporate both NMOS and PMOS transistors.
Part Ⅱ: Application Specific Integrated Circuit
An application-specific integrated circuit (ASIC) is an integrated circuit (IC) customized for a particular use, rather than intended for general-purpose use. For example, a chip designed solely to run a cell phone is an ASIC. In contrast, the 7400 series and 4000 series integrated circuits are logic building blocks that can be wired together for use in many different applications.
As feature sizes have shrunk and design tools improved over the years, the maximum complexity (and hence functionality) possible in an ASIC has grown from 5,000 gates to over 100 million.1 Modern ASICs often include entire 32-bit processors, memory blocks including ROM, RAM, EEPROM, Flash and other large building blocks. Such an ASIC is often termed a SoC (System-on-Chip). Designers of digital ASICs use a hardware description language (HDL), such as Verilog or VHDL, to describe the functionality of ASICs.
Field-programmable gate arrays (FPGA) are the modern day equivalent of 7400 series logic and a breadboard, containing programmable logic blocks and programmable interconnects that allow the same FPGA to be used in many different applications. For smaller designs and/or lower production volumes, FPGAs may be more cost effective than an ASIC design. The non-recurring engineering cost (the cost to setup the factory to produce a particular ASIC) can run into hundreds of thousands of dollars.2
The general term application specific integrated circuit includes FPGAs, but most designers use ASIC only for non-field programmable devices and make a distinction between ASIC and FPGAs.3
Standard cell design
In the mid 1980s a designer would choose an ASIC manufacturer and implement their design using the design tools available from the manufacturer. While third party design tools were available, there was not an effective link from the third party design tools to the layout and actual semiconductor process performance characteristics of the various ASIC manufacturers.4 Most designers ended up using factory specific tools to complete the implementation of their designs. A solution to this problem that also yielded a much higher density device was the implementation of Standard Cells. Every ASIC manufacturer could create functional blocks with known electrical characteristics, such as propagation delay, capacitance and inductance; that could also be represented in third party tools.5 Standard cell design is the utilization of these functional blocks to achieve very high gate density and good electrical performance. Standard cell design fits between Gate Array and Full Custom design in terms of both its NRE (Non-Recurring Engineering) and recurring component cost.6
By the late 1980s, logic synthesis tools, such as Design Compiler, became available. Such tools could compile HDL descriptions into a gate-level netlist. This enabled a style of design called standard-cell design. Standard-cell Integrated Circuits (ICs) are designed in the following conceptual stages, although these stages overlap significantly in practice.
These steps, implemented with a level of skill common in the industry, almost always produce a final device that correctly implements the original design, unless flaws are later introduced by the physical fabrication process.7
A team of design engineers starts with a non-formal understanding of the required functions for a new ASIC, usually derived from requirements analysis.
·The design team constructs a description of an ASIC to achieve these goals using an HDL. This process is analogous to writing a computer program in a high-level language. This is usually called the RTL (register transfer level) design.
·Suitability for purpose is verified by simulation. A virtual system created in software, using a tool such as Virtutech's Simics, can simulate the performance of ASICs at speeds up to billions of simulated instructions per second.
·A logic synthesis tool, such as Design Compiler, transforms the RTL design into a large collection of lower-level constructs called standard cells. These constructs are taken from a standard-cell library consisting of pre-characterized collections of gates such as 2 input nor, 2 input nand, inverters, etc.8 The standard cells are typically specific to the planned manufacturer of the ASIC. The resulting collection of standard cells, plus the needed electrical connections between them, is called a gate-level netlist.
·The gate-level netlist is next processed by a placement tool which places the standard cells onto a region representing the final ASIC. It attempts to find a placement of the standard cells, subject to a variety of specified constraints.
·The routing tool takes the physical placement of the standard cells and uses the netlist to create the electrical connections between them. Since the search space is large, this process will produce a “sufficient” rather than “globally-optimal”solution. The output is a set of photomasks enabling semiconductor fabrication to produce physical ICs.
·Close estimates of final delays, parasitic resistances and capacitances, and power consumptions can then be made. In the case of a digital circuit, this will be further mapped into delay information. These estimates are used in a final round of testing. This testing demonstrates that the device will function correctly over all extremes of the process, voltage and temperature. When this testing is complete the photomask information is released for chip fabrication.
These design steps (or flow) are also common to standard product design. The significant difference is that Standard Cell design uses the manufacturer's cell libraries that have been used in hundreds of other design implementations and therefore are of much lower risk than full custom design.9
Gate array design
Gate array design is a manufacturing method in which the diffused layers, i.e. transistors and other active devices, are predefined and wafers containing such devices are held in stock prior to metallization, in other words, unconnected.10 The physical design process then defines the interconnections of the final device. It is important to the designer that minimal propagation delays can be achieved in ASICs versus the FPGA solutions available in the marketplace. Gate array ASIC is a compromise as mapping a given design onto what a manufacturer held as a stock wafer never gives 100% utilization.11
Pure, logic-only gate array design is rarely implemented by circuit designers today, replaced almost entirely by field programmable devices such as FPGAs, which can be programmed by the user and thus offer minimal tooling charges, marginally increased piece part cost and comparable performance.12 Today gate arrays are evolving into structured ASICs that consist of a large IP core like a processor, DSP unit, peripherals, standard interfaces, integrated memories SRAM, and a block of reconfigurable uncommitted logic.13 This shift is largely because ASIC devices are capable of integrating such large blocks of system functionality and “system on a chip” requires far more than just logic blocks.
Full-custom design
The benefits of full-custom design usually include reduced area, performance improvements and also the ability to integrate analog components and other pre-designed components such as microprocessor cores that form a System-on-Chip. The disadvantages can include increased manufacturing and design time, increased non-recurring engineering costs, more complexity in the CAD system and a much higher skill requirement on the part of the design team.14 However for digital only designs, “standard-cell” libraries together with modern CAD systems can offer considerable performance/cost benefits with low risk. Automated layout tools are quick and easy to use and also offer the possibility to manually optimize any performance limiting aspect of the design.
Structured design
Structured ASIC design is an ambiguous expression, with different meanings in different contexts. This is a relatively new term in the industry, which is why there is some variation in its definition. However, the basic premise of a structured ASIC is that both manufacturing cycle time and design cycle time are reduced compared to cell-based ASIC by virtue of there being pre-defined metal layers and pre-characterization of what is on the silicon.15 One definition states that, in a structured ASIC design, the logic mask-layers of a device are predefined by the ASIC vendor (or in some cases by a third party). Structured ASIC technology is seen as bridging the gap between field-programmable gate arrays and“standard-cell” ASIC designs.
What makes a structured ASIC different from a gate array is that in a gate array the predefined metal layers serve to make manufacturing turnaround faster. In a structured ASIC the predefined metallization is primarily to reduce cost of the mask sets and is also used to make the design cycle time significantly shorter as well. Likewise, the design tools used for structured ASIC can substantially lower cost, and are easier to use than cell-based tools, because the tools do not have to perform all the functions that cell-based tools do.
One other important aspect about structured ASIC is that it allows IP that is common to certain applications to be “built in”, rather than “designed in”. By building the IP directly into the architecture the designer can again save both time and money compared to designing IP into a cell-based ASIC.