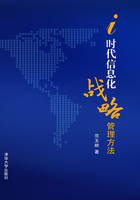
2.7 联合攻击战斗机项目信息技术应用实践
联合攻击战斗机(JSF)研制计划是有史以来规模最大的军用飞机研制计划。联合攻击战斗机研制计划是由美国牵头,英国、荷兰、丹麦、挪威、加拿大、意大利、新加坡、土耳其和以色列等多国参与的国际合作研制项目。JSF的主要目的是取代美空军的F-15E、F-16、A-10和F-117、海军的F-14、海军陆战队的AV-8B、英海军的“海鹞”式和空军的“狂风”、“鹞”式等飞机,定型后的F-35联合攻击战斗机是美国准备在21世纪使用的主力战斗机之一。
联合攻击战斗机的主要设计指标有:
(1)生存力:降低无线电频率以及红外信号,提高机载电子设备的对抗能力,以此提高在未来战场上的生存力和配合F-22战斗机的作战能力。
(2)杀伤力:综合机载和外来探测器得到的信息,提高发射各种精确武器的命中率和杀伤力。
(3)保障性:减少对后勤的依赖,提高出动架次率,以保证强大的作战能力。
(4)实用性:降低研制成本,使联合攻击战斗机能够成为武装力量的一个合理组成部分。
1996年美国国防部JSF项目刚招标时,只有麦道公司、诺斯罗普·格鲁曼公司和洛克希德·马丁公司(Lockheed Martin Aeronautics Company,以下简称马丁公司)三大航空集团提出方案,后来增加了波音公司。美军方经过审查决定由波音公司和马丁公司各自研制2架验证机,编号分别为X-32和X-35。图2-14(a)是马丁公司研制的X-35型联合攻击战斗机,图2-14(b)是波音公司研制的X-32型联合攻击战斗机。经过一番激烈的角逐,马丁公司最终战胜波音公司,赢得了价值约2000亿美元的订货合同。首批飞机已于2008年交货,飞机寿命40至50年。图2-15给出了JSF的主要技术特点。

图2-14 X-35型与X-32型联合攻击战斗机

图2-15 JSF的主要技术特点
(1)全球数字协同网络
(2)整个系统实行PLM
(3)与任何CAX系统兼容
(4)超过50000用户
(5)超级保密,迅即访问
(6)可快速/低风险地扩展
(7)在一条生产线上生产和装配4个军种用的3种机型
(8)使用同一种通用的支援和维护系统
(9)各种机型之间的零部件/系统/设备的通用性达到80%以上
马丁公司为了完成JSF的设计,采用了敏捷制造战略,利用信息技术建立了全球30个国家50家公司参与研发的数字化协同环境,形成了无缝连接、紧密配合的全球虚拟企业,快速地实现了以数字化技术为研制基础的三种变型、四个军种、客户化程度高的飞机设计。图2-16给出了马丁公司建立的JSF企业合作体系结构。
JSF企业合作体系以飞机总成为核心,连接了不同国家、不同军种的客户、飞机结构制造商、发动机制造商和机载电子设备提供商。为使JSF这一全球项目可以在全球范围内进行协同设计、制造、测试、部署以及跟踪,马丁公司没有利用SAP公司的ERP系统由上至下重新改组公司的经营过程,而采用了UGS公司的全生命周期管理(PLM)软件为集成平台,构建了支持全球范围内虚拟企业运作的数字化协同平台,为客户、飞机结构制造商、发动机制造商、机载电子设备提供商等合作成员提供支持,实现其本地应用信息系统与PLM系统的集成。
在项目研制阶段,作为投标方的波音公司和马丁公司在样机的生产过程中,分别以各自的生产特点为基础,大量应用了信息化设计与制造技术。通过采用先进的信息系统和计算机辅助设计、制造技术,在武器装备快速研制、全生命周期管理、降低研制成本、提高武器装备经济可承受性等方面取得了相当显著的效益。联合攻击战斗机研制计划是应用信息化技术的成功案例,代表了信息化技术的发展趋势,值得关注[17a][2a][3b]。

图2-16 JSF企业合作体系结构
1.广泛应用信息化设计及预装配技术
波音公司在真正装配X-32之前首先进行信息化预装配,而没有采用传统装配过程中必需的生产实体模型。波音公司还利用了与合作伙伴之间的时差进行全天24小时连续工作,例如,位于荷兰的福克Elmo公司负责配线,当出现问题时,可以发送一个信息化的修改方案给福克Elmo公司,在24小时之内,福克Elmo公司就能发出修改后的配线方案。这项工作的效果非常显著,前机身的装配过程没有出现任何拖延,也没有出现过装配顺序的错误。
作为马丁公司研究小组成员,诺斯罗普·格鲁门和BAE系统公司也使用Catia系统生成实体模型,彻底实现了无纸化设计制造。同时,自动生成数控加工程序,并利用万能夹具对零件进行高速加工,取消了专用工装。最后使用Metronor计算机辅助测量系统验证零件的几何形状。通过采用这种方法,设计和制造周期共缩短了50%,并消除了因不正确或不完整尺寸、数据误译及NC编程错误等造成的返工,大幅度减少了检验工作。这种工艺方法已经在马丁公司的X-35概念验证机和机体经济可承受性示范项目中的900个全尺寸零件中得到了验证。
2.虚拟开发环境覆盖全生命周期每一阶段
马丁公司选择了洛杉矶的MSC(MacNeal-Schwendler Corporation)公司参与X-35的开发。MSC公司在汽车和飞机虚拟产品设计方面具有几十年的经验,开发了相应的软件工具,包括设计/仿真集成、多学科概念设计、分析知识工程(analysis knowledge engineering)、计算机辅助工程数据管理等应用软件工具。虚拟开发环境可用于模拟飞机设计、保障和制造,以便在硬件制造之前对设计方案进行改进并进行工艺验证。同时,虚拟开发环境可以提供位于不同地点的部门间的实时链接,其中包括得克萨斯州福沃斯工厂的战术飞机系统分部、佐治亚州的玛丽埃塔航空系统分部、马里兰州巴尔的摩航空结构分部以及加利福尼亚帕姆戴尔的“臭鼬”工厂等。马丁公司还与IBM及达索系统公司在虚拟产品开发创新项目中进行合作。新的虚拟产品开发环境允许马丁公司的合作伙伴及供应商在世界各地实时存取和集成所有机体设计的有关数据,从而提高了设计效率,在产品全生命周期最大限度使用建模和仿真工具,进一步降低了研发的成本。
在项目的实施过程中,马丁公司与诺斯罗普·格鲁门公司、英宇航公司、达索系统公司(软件产品为Catia)、SDRC公司(软件产品为Metaphase Product Data Manager)及Engineering Animation公司(软件产品为VAS Digital Mock-Up)联合开发软件工具和新工艺,所有文本数据都利用产品数据管理系统进行管理,实现了各个工作站点实时读取所有产品数据。此外,单一分布式PDM数据库中存放了支持马丁公司X-35研制计划的所有设计、制造和维修的数据,以确保对整个X-35研制计划进行实时集成和评审。这种工作方式不仅降低了设计成本,而且大大减少了设计更改,从而基本消除了制造过程中的返工现象。同时,这种虚拟的产品开发环境也有利于集思广益,开发出创新的项目。
3.采用并行工作方式实现异地联合设计制造
X-35由马丁公司的“臭鼬”项目组开发,与此类似,波音公司的X-32由专门从事尖端产品研发的“鬼怪”项目组负责研制。实际上,波音公司的X-32研制不仅融入了全美许多航空关联企业,同时英国、荷兰、丹麦、挪威、加拿大、意大利、新加坡、土耳其和以色列也参与其中,这种协同工作是在网络化及信息化基础上完成的。该项目组约有4000名高级工程师和研究人员,在设计中用Catia系统先在计算机上进行设计和模拟组装,再与其他承包商合作,共同完成装配作业,这种方法极大地降低了成本。波音公司在装配其X-32概念验证机期间,创造了先进的设计和制造理念——“在任何地方设计和制造”。这种理念使得X-32的生产率大大提高,出错率减少80%。并行的工作方法是实现异地联合设计和制造的前提,并行的工作方法不仅能充分发挥各自的特长,而且极大地提高了工作效率,波音公司X-32概念验证机的开发证实了这种理念的实用性和有效性。
4.产品数据管理极大简化了工作程序,保证了准确性
波音公司在圣·路易斯生产X-32概念验证机前机身的各种部件,在西雅图生产中机身、机翼、后机身和尾翼的各种零部件,都是根据同一个数据库中的数据设计和制造的。过去,波音公司需要把这些数据交给生产部门编写数控加工程序,控制4~5台数控机床加工出一个木质或铝质工件,以检验各系统的运转是否正常。而现在,只需要调用有关零件的数字定义,然后在一台计算机自动编程的数控机床上进行加工,一次加工就能完成,节省了大量时间。过去,从发布零件设计到完成零件加工需要5周时间,而现在只需要5天,质量完全符合要求。
5.广泛应用集成制造系统技术
在联合攻击战斗机研制计划中,制造系统集成技术在降低成本、提高质量、缩短研发周期方面做出了巨大贡献。波音公司总经理及X-32研制计划经理在飞机的开发初期就要求设计和生产要采用创新的方法,并且在X-32前机身部件的制造中使用了大量精益设计和精益制造技术。X-32前机身主要零件包括复合材料蒙皮、数百个加工件和在波音公司肯特空间中心制造的铝隔框等。在肯特空间中心加工的前机身零件充分体现了波音公司“在任何地方设计和制造”的理念,无论地理位置如何,都有能力集成这些技术,降低成本。波音公司建有大量的数据库,可用于X-32零件的自动数控加工,如铝合金隔框,其电子版的三维数字模型发送至西雅图工厂后被自动转换为NC加工程序,然后进行数控铣切,一次加工成所需零件,节省了时间和试验件的费用。
6.通过精益制造实现经济可承受性
精益制造在X-32装配中起着重要作用,X-32已经成为波音公司通过精益设计和制造实现经济可承受性目标的标志。在波音公司制造X-32的过程中,几乎没有发生返工现象,这要归功于先进的设计和制造技术——三维实体建模、虚拟设计及虚拟装配。在波音公司的帕姆戴尔工厂,人员和工时均减少了50%,工装数量比YF-22减少了一半,总的制造和装配成本降低30%~40%。
在总装车间,使用桌面计算机代替纸质图来读取X-32设计说明书。通过视频连接,来自西雅图、圣·路易斯、塔尔萨的工程师们可以和帕姆戴尔的工程师行进行面对面的交流。随着X-32装配工作的进展,工人们开始佩带一种挂在腰间的微型计算机。通过一种单目镜片,能将体现装配顺序的虚拟模型投射到正在装配的部件上方。这项技术是从圣·路易斯移植到帕姆戴尔的,采用这项新的装配技术之后,大大节省了装配时间,能把X-32前机身和中机身对接的装配时间减少到YF-22的一半。事实上,X-32A前机身所用的装配时间只有YF-22的1/3,而装配X-32B前机身的时间又比装配X-32A的时间减少了1/3。对于全部由钛合金制成的X-32A中机身和后机身来说,装配时间仅为YF-22的1/3。
波音公司吸取了其他项目的经验,改进X-32的装配步骤,可以在同一个直线装配线上生产三种不同的机型。据报道,波音AH-64“阿帕奇”直升机的装配线已经于1998年转变成为这种直线装配线。通过这种改造,已经把装配线上的19个工作站减少到10个,装配周期从81天缩短到44天。由于装配线的改进,加之在精益制造方面的革新,每架飞机在AH-64装配线上的流动时间仅仅需要35天,总装周期缩短了60%。根据同样的设想,波音公司计划用一条仅有7个工作站的装配线来满足X-32的生产要求。这种装配线每月能生产17.5架X-32,在每个工作站里停留的工作时间仅为1.5天。飞机在完成前4个工作站的装配之后,就可以从移动式机架上取下。从第5个工作站起,X-32就可以利用其自身的机轮在生产线上转移。同时,移动式机架又回到生产线的起始位置迎接下一架飞机。
7.采用信息化生产技术实现生产的快速转换
联合攻击战斗机有3种不同的机型:美国空军的常规起降型、美国海军的航母舰载型以及美国海军陆战队和英国空、海军的短距起飞/垂直着陆型。3种机型的机翼材料相同,但用户对机翼的要求不同,因此机翼结构设计是不一样的。例如,与空军常规起降型相比,海军舰载型的着陆速度更高,要求机翼有更厚的内表面。而且目前各种机型的生产量尚未确定,即使确定了,其批量也不会像汽车那样大。因此,如何实现3种不同机翼的“混合”式加工制造,控制制造成本,实现联合攻击战斗机的经济可承受性以及针对需求的快速反应制造,便成为联合攻击战斗机生产的技术难题。
马丁公司解决这个问题的最初想法是将各种机翼的设计变化控制在最小的程度,但是这样过分追求共性的做法可能会降低飞机的性能。因此,马丁公司最终采用了信息化技术,使3种机型就像是同一种产品一样容易进行管理和生产,以便发挥规模经济的效益和进行全生命周期更新改造。柔性生产线可以从生产一种机型顺利转向另一种机型而几乎不发生停顿,采用高速数控铣床(主轴转速达到15000~30000转/分钟),直接从Catia软件得到指令,实现上述3种机翼的转换加工,机翼铣削加工成本是常规加工成本的1/3。由于数控铣床主轴转速极高,在铣削过程中飞溅出切屑,带走了部件上的热量,避免了热量积聚,减轻了加工部件的弯曲变形,因此不需要采用铣削夹具。由于不需要夹具,从短距起飞/垂直着陆型机翼转向常规起降型的加工过程只需向数控铣床输入新的加工代码即可。另外,通过使用Cadam软件直接进行编程,同样能够大大缩短生产布置时间。以前机型转换需分别用6周时间进行编程和刀具调试验证,现在1天就能完成上述工作。在这种信息化装配线上,1号X-35概念验证机的整体机翼与中部机身拼装只需4个机械师花14分钟的时间,前部和中部机身拼装只用了16分钟,而采用非信息化制造技术,仅机身拼装就需7~10天时间。
据报道,对比传统制造过程,X-35的工装调整时间和制造时间分别减少90%和66%,制造成本和部件数量分别减少50%以上和50%。这样,建造一架X-35(从订货到交付)将仅需5个月,而过去F-16战斗机则需用15个月。
8.马丁公司在X-35研制和生产中使用的信息化技术系统
图2-17给出了JSF的信息系统框架,其中,产品数据管理系统(PDM)作为集成平台起了核心作用。在JSF的信息系统框架中,选用UGS的Teamcenter作为PDM解决方案,通过虚拟专网、局域网、广域网和Internet向使用者提供各种应用服务。JSF的信息系统实现祥述如下。

图2-17 表示了JSF的信息系统框架
(1)基于万维网的数据交换和共享:马丁公司建立了虚拟私有网传送CATIA软件的大型数据集合,即采用加密解密的方法,通过虚拟隧道进行传输。文档交换工作使用万维网和无线网络应用程序。由马丁公司提供数字图书馆,并采用全生命周期管理软件。
(2)文档需求管理:采用Telelogic公司开发的面向对象的需求管理系统Doors。所谓需求管理是一种获取、组织并记录系统需求的系统化方法,以及一个使客户与项目组对不断变更的系统需求达成并保持一致的过程。
(3)可视化管理:进行数字化装配的关键是完成产品装配过程中的干涉检查和产品结构的可视化管理,在JSF信息系统框架中,该工作由EDS的可视化装配系统软件e-VIS来完成。
(4)零部件管理:由i2公司提供的Aspect软件完成零部件的管理。
(5)设计软件:采用Dassault公司的Catia V4/V5设计软件,Catia是一个集成了CAD、CAE、CAM的应用软件包。
(6)制造资源计划:采用马丁公司自己开发的MRPII系统PIOS,用于控制主生产进度和制定库存品订货计划。
(7)车间计划和工艺规划:采用HUM公司提供的SFM和CAPP软件产品,用于作业计划管理和工艺过程规划。
(8)原材料管理:采用MSC公司开发的Mvision系统进行制造过程中的原材料管理。
(9)仿真:采用Dassault公司的Delmia软件进行工厂/生产线布局和仿真。
(10)后勤管理:采用马丁公司开发的Atlas软件进行后勤管理,Atlas是一个现场状态分析软件,该软件曾被用于分析和验证C-130运输机以及F-22战斗机的平均无故障工作时间。
(11)内容管理:为JSF项目提供文档管理和数字化图书馆,采用Open Text公司提供的基于Web的内容管理系统Livelink软件。
(12)门户:采用PTC公司提供的Windchill/Infoengine,为用户提供访问其他数据处理系统的界面。
(13)成本和进度管理:使用Artimis公司的Project View/Cost View软件,使JSF用户能随时了解项目进度和预算执行情况。
JSF的零部件是由分布在全球各地的企业制造的(远隔8050公里),由于在F-35项目中应用了数字化设计和制造管理技术,使得这些零部件制造的结构准确度得到了保证,提高了装配的效率。JSF项目开创了基于信息技术环境下协同生产的新局面,JSF的高性能也为马丁公司带来了巨大收益,目前已有超过3000架的订单。