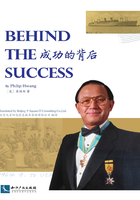
Becoming World No.1 in CRT Terminal Field
“Oh, God, so many!”
I could not help but acclaiming. This was what happened when we dismantled LEAR SIERGER terminal for the first time. After adopting the micro-information processing IC, however, around 60 components were adequate. While in the past, more than 200 parts were needed.
An integrated circuit made the complex circuit board simple, yet the appearance of the entire terminal was still a problem. Terminals sold in the market were not only functionally“dumb”, but also clumsy in their appearance. The weight of monitors made of iron boards as well as its body is considerably high. I therefore intended to make a complete change to the packaging of the terminal. Plastic instead of iron boards was packed with monitors and keyboards, to make them neat and light-weighted.
A cast model was required for the production of plastic shells, while such molding technology was not available in South Korea. Although the molding can be accomplished within a second for large refrigerator snow, it was not the case in those days. It was even impossible for the molding of 12-inch monitors and keyboards to be completed.
We had never expected that the TAIHAN made announcement of stopping its monitor production, which made the situation even worse. According to TAIHAN, production of game monitors would be continued based on orders, while newly-developed monitor terminals would not be produced any more. So, I traveled busily again in other to find other electronics companies that could accept my proposal.
We barely got through the difficulties again, but the mold-casting was still an issue. R&D of 12-inch monitors and micro-information processing IC boards as well as keyboards had been completed, while the part (clothes) for integrating these components was still under development. I built a camp bed in the corner of a molding factory then, to sleep and eat with technicians in order to complete the R&D of molding as soon as possible.
I invested USD 120,000 in the R&D of terminal shells within 6 months. Although I spent a lot in making the first casting mold, our packaging would be stronger and more attractive than those produced in other companies as long as our R&D was successful. Unit price would gradually reduce as a result of the application of plastics.
Mold-casting technology was successfully developed, and I felt relieved. To be frank, I had no funds to continue with the R&D. To put it into production, more investment was needed for the following numerous tests. However, my pocket was empty.
So, I had to mortgage my house and borrowed USD 50,000.
My wife could not understand it and thought that as long as a huge amount of money had been input into the project, why should we mortgage the house for a loan. I felt very guilty but had no choice. I did make profits from our monitors, but the living condition of my family was not obviously improved. Earned profits had been used for R&D, and more ideas should be provided to make money. Our living expenses came from the wage of my wife who worked as a dietitian.
“Dad, we are going to be homeless?”
My daughter looked seriously and asked me this question one day. I did not recover in a moment when the daughter went on and my heart was deeply hurt:
“An uncle told me that daddy had no money, and we will be driven out from home.”
Although staff salaries were postponed, tests were carried out based on strict rules. I stayed in Oriental Precision Company in South Korea.
It was even incredible for ourselves that CRT terminals of“TELE VIDEO” finally passed all the tests. The adoption of micro-information processing technology reduced the unit price of the circuit board, which served as a major innovation. What's more, it played a decisive role in the cost control after initial assembly in South Korea and shipped to the United States.
The company in Silicon Valley produced only circuit boards. The factory in South Korea was responsible for the production and assembly of molds and monitors. They were shipped to the United States. Then, our professional staff completed the second assembly of inserting the boards and they were packed into boxes (made in South Korea), and ready for sale.