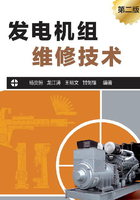
第三节 零件检验的原则与基本方法
维修过程中的检验工作包含的内容很广,在很大程度上,它是制定维修工艺措施的主要依据。它决定零部件的弃取,决定装配质量,影响维修成本,是一项重要的工作。
一、检验的原则
①在保证质量的前提下,尽量缩短维修时间,节约原材料、配件、工时,提高利用率与降低成本。
②严格掌握技术规范、修理规范,正确区分能用、需修、报废的界限,从技术条件和经济效果综合考虑,既不让不合格的零件继续使用,也不让不必维修或不应报废的零件进行修理或报废。
③努力提高检验水平,尽可能消除或减少误差,建立健全合理的规章制度。按照检验对象的要求,特别是精度要求选用检验工具或设备,采用正确的检验方法。
二、检验的内容
(一)检验分类
(1)修前检验 它是在机械设备拆卸后进行。对已确定需要修复的零部件,可根据损坏情况及生产条件选择适当的修复工艺,并提出技术要求;对报废的零部件,要提出需补充的备件型号、规格和数量;不属备件的需要提出零件蓝图或测绘草图。
(2)修后检验 这是指机械设备零件经加工或修理后,检验其质量是否达到了规定的技术标准,确定是成品、废品或返修。
(3)装配检验 它是指检验待装零件质量是否合格、能否满足要求;在装配中,对每道工序都要进行检验,以免产生中间工序不合格,影响装配质量或造成返工;组装后,检验累积误差是否超过技术要求;总装后要进行调整,保证工作精度、几何精度及进行其他性能检验、试运转等,确保维修质量。
(二)检验的主要内容
(1)零件的几何精度 包括零件的尺寸、形状和表面相互位置精度。平时经常检验的是尺寸、圆柱度、圆度、平面度、直线度、同轴度、平行度、垂直度、跳动等项目。根据维修特点,有时不是追求单个零件的几何尺寸,而是要求相对配合精度。
(2)零件表面质量 包括零件表面粗糙度以及零件表面有无擦伤、腐蚀、裂纹、剥落、烧损和拉毛等缺陷。
(3)零件的物理力学性能 除零件硬度、硬化层深度外,对零件制造和修复过程中形成的性能,如应力状态、平衡状况、弹性、刚度、振动等也需根据情况适当进行检测。
(4)零件的隐蔽缺陷 包括制造过程中的内部夹渣、气孔、疏松、空洞、焊缝等缺陷,还有使用过程中产生的微观裂纹。
(5)零部件的质量和静动平衡 如活塞、连杆组之间的质量差;曲轴、风扇、传动轴、飞轮等高速转动的零部件进行静动平衡。
(6)零件的材料性质 如零件合金成分、渗碳层含碳量、各部分材料的均匀性、铸铁中石墨的析出、橡胶材料的老化变质程度等。
(7)零件表层材料与基体的结合强度 如电镀层、喷涂层、堆焊层等与基体金属的结合强度,机械固定连接件的连接强度、轴承合金和轴承座的结合强度等。
(8)组件的配合情况 如组件的同轴度、平行度、啮合情况与配合的严密性等。
(9)零件的磨损程度 正确识别摩擦磨损零件的可行性,由磨损极限确定是否能继续使用。
(10)密封性 如内燃机缸体、缸盖需进行密封试验,检查有无泄漏。
三、检验的方法
(一)感觉检验法
不用量具和仪器,仅凭检验人员的直观感觉和经验来鉴别零件的技术状况,统称感觉检验法。这种方法精度不高,只适用于分辨缺陷明显的或精度要求不高的零件,要求检验人员有丰富的经验和技术。具体方法如下。
(1)目测 用眼睛或借助放大镜对零件进行观察和宏观检验,如对倒角、圆角、裂纹、断裂、疲劳剥落、磨损、刮伤、蚀损、变形、老化等做出可靠的判断。
(2)耳听 根据机械设备运转时发出的声音或敲击零件时的响声判断技术状态。零件无缺陷时声响清脆,内部有缩孔时声音相对低沉,若内部出现裂纹,则声音嘶哑。
(3)触觉 用手与被检验的零件接触,可判断工作时温度的高低和表面状况;将配合件进行相对运动,可判断配合间隙的大小。
(二)测量工具和仪器检验法
这种方法由于能达到检验精度要求,所以应用最广。
①用各种测量工具(如卡钳、钢板尺、游标卡尺、千分尺或百分表、厚薄规、量块、齿轮规等)和仪器检验零件的尺寸、几何形状、相互位置精度。
②用专用仪器、设备对零件的应力、强度、硬度、冲击性、伸长率等力学性能进行检验。
③用静动平衡试验机对高速运转的零件做静动平衡检验。
④用弹簧检验仪或弹簧秤对各种弹簧的弹力和刚度进行检验。
⑤对承受内部介质压力并须防止泄漏的零部件,需在专用设备上进行密封性能检验。
⑥用金相显微镜检验金属组织、晶粒形状及尺寸、显微缺陷、分析化学成分。
(三)物理检验法
它是利用电、磁、光、声、热等物理量,通过零部件引起的变化来测定技术状况,发现内部缺陷。这种方法通常和仪器、工具检测相结合,它不会使零部件受伤、分离或损坏。目前,普遍称这种方法为无损检测。
对维修而言,这种监测主要是对零部件进行定期检查、维修检查、运转中检查,通过检查发现其缺陷,根据缺陷的种类、形状、大小、产生部位、应力水平、应力方向等,预测缺陷发展的程度,确定采取修补或报废。目前,在生产实践中得到广泛应用的有磁力法、渗透法、超声波法和射线法等。
1.磁力法
它是利用磁力线通过铁磁性材料时所表现出来的情况来判断零件内部有无裂纹、空洞、组织不均匀等缺陷,又称磁力探伤。这种方法的原理是用强大的直流电感应出磁场,将零件磁化。当磁场通过导磁物质时,磁力线将按最短的直线通过。如果零件内部组织均匀一致,则磁力线通过零件的方向是一致的。若零件的内部有缺陷时,在缺陷部分就会形成较大的磁阻,磁力线便会改变方向,绕过缺陷,聚结在缺陷周围,并露出零件表面形成与缺陷相似的漏磁场。在零件的表面均匀地撒上铁粉时,铁粉即被吸附在缺陷的边缘,从而显露出缺陷的位置和大小,如图2-1所示。

图2-1 磁力探伤原理
这种方法的特点是灵敏度高、操作简单迅速,但只能适应于易被磁化的零件,且在零件的表面处,若缺陷在较深处则不易查出。磁力探伤在生产单位中应用十分广泛。通用的探伤设备有机床式和手提式两种。
在进行磁力探伤前,应将零件表面清洗干净,将可能流入磁粉的地方堵住。探伤时首先将零件磁化。探伤后应进行退磁处理,其目的是为消除零件中的剩磁,以免影响零部件安装后的正常工作性能。
2.渗透法
这种方法是在清洗过的零件表面上施加具有高度渗透能力的渗透剂。由于湿润作用,使之渗入缺陷中,然后将表面上的多余渗透剂除去,再均匀涂上一薄层显像剂(常用MgO2、SiO2白色粉末)。在显像剂的毛细作用下而将缺陷中的残存渗透剂吸到表面上来,从而显示出缺陷。
渗透法分为着色法和荧光法两种。着色法是在渗透液中加入显示性能强的红色染料,显像剂由白垩粉调制,使渗透液被吸出后,在白色显像剂中能明显地显示出来。荧光法则是在渗透液中加入黄绿色荧光物质,显像剂则要专门配制,当渗透剂被吸出后,再用近紫外线照射,便能发出鲜明的荧光,由此显示缺陷的位置和形状。
着色法所用的渗透剂由苏丹、硝基苯、苯和煤油等组成;荧光渗透剂由荧光质,即拜尔荧光黄和塑料增白剂,还有溶剂,即二甲苯、石油醚、邻苯二甲酸二丁酯组成。显像剂由锌白、火棉胶、苯、丙酮、二甲苯、无水酒精等配制而成。
着色法用以检验零件表面裂纹和磁力探伤及荧光法难以检验的零件。荧光法本身不受材料磁性还是非磁性的限制,主要用于非磁性材料的表面缺陷检验。
渗透法所用设备简单,操作方便,不受材料和零件形状限制,与其他方法相比具有明显的优点,在维修中检测零件表面裂纹由来已久,至今仍不失为一种通用的方法。
3.超声波法
它是利用超声波通过两种不同介质的界面产生折射和反射的现象来探测零件内部的隐蔽缺陷。这种方法又分为以下几种。
(1)脉冲反射法 如图2-2所示。把脉冲振荡器发射的电压加到探头的晶片上使之振动后产生超声波,以一定的速度通过工件传播,当遇到工件缺陷和底面产生反射时,被探头接收,通过高频放大、检波、视频放大后,在示波器荧光屏上显示出来。荧光屏的横坐标表示距离,纵坐标代表反射波声压强度。从图中可以看出缺陷波(F)比底面反射波(B)先返回探头,这样就可以根据反射波的有无、强弱和缺陷,反射波与发射脉冲之间的时间间隙,知道缺陷是否存在以及缺陷的位置和大小等。

图2-2 脉冲反射法
(2)穿透法 如图2-3所示。穿透法又称声影法。从图中看到高频振荡器与发射探头A连接,探头A发射超声波由工作一面传入内部。若工件完整无缺陷,则超声波可以顺利通过工件而被探头B接收,通过放大器放大并在指示器显示出来。如途中遇到缺陷,则部分声波被挡住而在其后形成一“声影”,此时接收到的超声波能量将大大减低,指示器做出相应的指示,从而表示发现了缺陷。

图2-3 穿透法
(3)共振法 以频率可调的超声波射入到具有两面平行的工件时,由底面反射回来的超声波同入射波在一直线上沿相反方向彼此相遇,若工件厚度等于超声波的半个波长或半波长的整数倍便叠加而成驻波,即此时入射波同反射波发生了共振。根据共振频率的测定就能确定工件厚度或检验存在的缺陷。工件完整无缺陷时是对应整个工件厚度产生共振。若具有同工件表面平行的缺陷时,是对应着缺陷深度产生共振,共振频率不同。至于形状不规则的缺陷,因为不可能造成相反方向的两个波,所以不论怎样改变超声波频率都得不到共振,据此断定缺陷的存在。
以上三种方法各应用在不同场合。脉冲反射法灵敏度高,可检查出较小的缺陷,能准确地知道缺陷的位置和大小,但不宜探测太薄的工件或靠近表面的缺陷,此方法使用方便,是目前超声波探伤中最常用的方法。穿透法要求工件两面必须平行,灵敏度较低,对两探头的相对位置要求高,常用于板类夹层和非金属材料的检查,如橡胶、塑料。共振法可准确测定工件厚度,特别适用于检查板件、管件、容器壁、金属胶接结构等薄壁件的内部缺陷,对工件表面粗糙度要求高。
总之,超声波探伤主要与被探测零件材料的组织结构、超声波频率、探头结构、接触条件、工件表面质量和几何形状、灵敏度的调节等因素有关。它能探测工件深处的缺陷、多种不同类型的缺陷,不受材质限制,设备轻便,可在现场就地检验,成本较低,易于实现探测的自动化。但对形状复杂工件探测有困难。
4.射线法
射线的种类很多,其中易于穿透物体的主要有X射线、γ射线和中子射线三种。X射线和γ射线的区别只是发生的方法不同,都是波长很短的电磁波,两者本质相同。中子和质子是构成原子核的粒子,发生核反应时,中子飞出核外形成中子射线。
这三种射线在穿透物体的过程中受到吸收和散射,因此其穿透物体后的强度衰减,而衰减程度由物体的厚度、材料品种及射线种类确定。当厚度相同的板材含有气孔时,这部分不吸收射线,容易透过。相反,若混进容易吸收射线的异物时,这些地方射线就难以透过。因此,根据射线穿透的强弱程度来判断物体有无缺陷。
(1)X射线 射线穿透物体强度的差异通过射线检定器得到反映。按其采用的检定器不同,X射线分为:X射线照相法,检定器为照相软片;X射线荧光屏观察法,检定器为荧光屏;X射线电视观察法,其基本原理与普通工业用闭路电视系统一样。上述方法,目前在生产中应用最广泛的还是X射线照相法。
(2)γ射线 放射性同位素产生的γ射线与X射线的本质及基本特性是一样的,因此探伤原理相同,反射线的来源不同。常用的γ射线照相,它同X射线照相法相比具有许多突出的优点,如穿透能力更大,设备轻便,透射效率更高,一次可检验许多工件,可长时间不间断工作,不用电,适宜野外现场使用。
(3)中子射线 中子射线不同于上述两种,主要用于照相探伤。它常应用在检查由含氢、锂、硼物质和重金属组成的物体,对陶瓷、固体火箭燃料、子弹、反应堆等进行试验研究工作。
此外,还有涡流探伤、激光全息照相检测、声阻法探伤、红外无损检测、声发射检测等方法,限于篇幅,这里不多介绍,可参阅相关书籍。