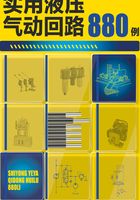
第3章 方向控制回路
在液压系统中,方向控制回路的作用是实现执行元件的启动、停止或改变运动方向。即利用各种方向控制阀来控制系统中各油路油液的接通、断开及变向,方向控制回路主要有换向回路和锁紧回路两类。
3.1 换向回路
3.1.1 采用二位四通电磁换向阀的换向回路(图3-1和表3-1)

图3-1 采用二位四通电磁换向阀的换向回路
表3-1 采用二位四通电磁换向阀的换向回路

3.1.2 采用手动换向阀的换向回路(图3-2和表3-2)

图3-2 采用手动换向阀的换向回路
表3-2 采用手动换向阀的换向回路

3.1.3 采用三位四通换向阀的换向回路(图3-3和表3-3)

图3-3 采用三位四通换向阀的换向回路
表3-3 采用三位四通换向阀的换向回路

3.1.4 采用二位三通换向阀使单作用缸换向的换向回路(图3-4和表3-4)

图3-4 采用二位三通换向阀使单作用缸换向的换向回路
表3-4 采用二位三通换向阀使单作用缸换向的换向回路

3.1.5 采用三通换向阀换向的换向回路(图3-5和表3-5)

图3-5 采用三通换向阀换向的换向回路
表3-5 采用三通换向阀换向的换向回路

3.1.6 采用四通换向阀使柱塞缸换向的换向回路(图3-6和表3-6)

图3-6 采用四通换向阀使柱塞缸换向的换向回路
表3-6 采用四通换向阀使柱塞缸换向的换向回路

3.1.7 先导阀控制液动换向阀的换向回路(图3-7和表3-7)

图3-7 先导阀控制液动换向阀的换向回路
表3-7 先导阀控制液动换向阀的换向回路

3.1.8 电液换向阀换向回路(图3-8和表3-8)

图3-8 电液换向阀换向回路
表3-8 电液换向阀换向回路

3.1.9 装有节流阀的电液换向阀换向回路(图3-9和表3-9)

图3-9 装有节流阀的电液换向阀换向回路
表3-9 装有节流阀的电液换向阀换向回路

3.1.10 液动换向阀自动换向回路
3.1.10.1 液动换向阀自动换向回路Ⅰ(图3-10和表3-10)

图3-10 液动换向阀自动换向回路Ⅰ
表3-10 液动换向阀自动换向回路Ⅰ

3.1.10.2 液动换向阀自动换向回路Ⅱ(图3-11和表3-11)

图3-11 液动换向阀自动换向回路Ⅱ
表3-11 液动换向阀自动换向回路Ⅱ

3.1.11 电液比例换向阀换向回路(图3-12和表3-12)

图3-12 电液比例换向阀换向回路
表3-12 电液比例换向阀换向回路

3.1.12 用多路换向阀换向的换向回路
3.1.12.1 用多路换向阀换向的换向回路Ⅰ(图3-13和表3-13)

图3-13 用多路换向阀换向的换向回路Ⅰ
表3-13 用多路换向阀换向的换向回路Ⅰ

3.1.12.2 用多路换向阀换向的换向回路Ⅱ(图3-14和表3-14)

图3-14 用多路换向阀换向的换向回路Ⅱ
表3-14 用多路换向阀换向的换向回路Ⅱ

3.1.13 用插装阀组成的换向回路
3.1.13.1 用插装阀组成的三通换向回路(图3-15和表3-15)

图3-15 用插装阀组成的三通换向回路
表3-15 用插装阀组成的三通换向回路

3.1.13.2 用插装阀组成的四通换向回路Ⅰ(图3-16和表3-16)

图3-16 用插装阀组成的四通换向回路Ⅰ
表3-16 用插装阀组成的四通换向回路Ⅰ

3.1.13.3 用插装阀组成的四通换向回路Ⅱ(图3-17和表3-17)

图3-17 用插装阀组成的四通换向回路Ⅱ
表3-17 用插装阀组成的四通换向回路Ⅱ

3.1.13.4 用插装阀控制的换向回路(图3-18和表3-18)

图3-18 用插装阀控制的换向回路
表3-18 用插装阀控制的换向回路

3.1.14 时间控制制动式换向回路(图3-19和表3-19)

图3-19 时间控制制动式换向回路
表3-19 时间控制制动式换向回路

3.1.15 行程控制制动式换向回路(图3-20和表3-20)

图3-20 行程控制制动式换向回路
表3-20 行程控制制动式换向回路

3.1.16 采用比例压力阀的换向回路(图3-21和表3-21)

图3-21 采用比例压力阀的换向回路
表3-21 采用比例压力阀的换向回路

3.1.17 比例电液换向阀换向回路
3.1.17.1 开环控制的用比例电液换向阀的换向回路(图3-22和表3-22)

图3-22 开环控制的用比例电液换向阀的换向回路
表3-22 开环控制的用比例电液换向阀的换向回路

3.1.17.2 闭环控制的用比例电液换向阀的换向回路(图3-23和表3-23)

图3-23 闭环控制的用比例电液换向阀的换向回路
表3-23 闭环控制的用比例电液换向阀的换向回路

3.1.18 比例电液方向流量复合阀换向回路
3.1.18.1 用定差溢流阀补偿的比例电液方向流量复合阀换向回路(图3-24和表3-24)

图3-24 用定差溢流阀补偿的比例电液方向流量复合阀换向回路
表3-24 用定差溢流阀补偿的比例电液方向流量复合阀换向回路

3.1.18.2 用定差减压阀补偿的比例电液方向流量复合阀换向回路(图3-25和表3-25)

图3-25 用定差减压阀补偿的比例电液方向流量复合阀换向回路
表3-25 用定差减压阀补偿的比例电液方向流量复合阀换向回路

3.1.19 双向泵换向回路
3.1.19.1 双向定量泵换向回路(图3-26和表3-26)

图3-26 双向定量泵换向回路
表3-26 双向定量泵换向回路

3.1.19.2 双向变量泵换向回路Ⅰ(图3-27和表3-27)

图3-27 双向变量泵换向回路Ⅰ
表3-27 双向变量泵换向回路Ⅰ

3.1.19.3 双向变量泵换向回路Ⅱ(图3-28和表3-28)

图3-28 双向变量泵换向回路Ⅱ
表3-28 双向变量泵换向回路Ⅱ

3.1.19.4 双向变量泵换向回路Ⅲ(图3-29和表3-29)

图3-29 双向变量泵换向回路Ⅲ
表3-29 双向变量泵换向回路Ⅲ

3.2 启停回路
3.2.1 二位二通阀的启停回路(图3-30和表3-30)

图3-30 二位二通阀的启停回路
表3-30 二位二通阀的启停回路

3.2.2 二位三通阀的启停回路(图3-31和表3-31)

图3-31 二位三通阀的启停回路
表3-31 二位三通阀的启停回路

3.3 锁紧回路
为了使液压执行元件能在任意位置上停留,或者在停止工作时,切断其进、出油路,使之不因外力的作用而发生移动或窜动,准确地停留在原定位置上,可以采用锁紧回路。
3.3.1 用换向阀的中位机能锁紧回路(图3-32和表3-32)

图3-32 用换向阀的中位机能锁紧回路
表3-32 用换向阀的中位机能锁紧回路

3.3.2 用单向阀的锁紧回路(图3-33和表3-33)

图3-33 用单向阀的锁紧回路
表3-33 用单向阀的锁紧回路

3.3.3 用液压单向阀的单向锁紧回路(图3-34和表3-34)

图3-34 用液压单向阀的单向锁紧回路
表3-34 用液压单向阀的单向锁紧回路

3.3.4 用液控单向阀的锁紧回路(图3-35和表3-35)

图3-35 用液控单向阀的锁紧回路
表3-35 用液控单向阀的锁紧回路

3.3.5 用液控顺序阀的单向锁紧回路(图3-36和表3-36)

图3-36 用液控顺序阀的单向锁紧回路
表3-36 用液控顺序阀的单向锁紧回路

3.3.6 用液控顺序阀的双向锁紧回路(图3-37和表3-37)

图3-37 用液控顺序阀的双向锁紧回路
表3-37 用液控顺序阀的双向锁紧回路

3.3.7 用锁紧缸锁紧的回路(图3-38和表3-38)

图3-38 用锁紧缸锁紧的回路
表3-38 用锁紧缸锁紧的回路

3.3.8 用液控插装单向阀的液压缸锁紧回路(图3-39和表3-39)

图3-39 用液控插装单向阀的液压缸锁紧回路
表3-39 用液控插装单向阀的液压缸锁紧回路

3.3.9 用制动器的液压马达锁紧回路(图3-40和表3-40)

图3-40 用制动器的液压马达锁紧回路
表3-40 用制动器的液压马达锁紧回路

3.4 连续往复运动回路
3.4.1 用行程开关控制的连续往复运动回路
3.4.1.1 用行程开关控制的连续往复运动回路Ⅰ(图3-41和表3-41)

图3-41 用行程开关控制的连续往复运动回路Ⅰ
表3-41 用行程开关控制的连续往复运动回路Ⅰ

3.4.1.2 用行程开关控制的连续往复运动回路Ⅱ(图3-42和表3-42)

图3-42 用行程开关控制的连续往复运动回路Ⅱ
表3-42 用行程开关控制的连续往复运动回路Ⅱ

3.4.1.3 用行程开关控制的连续往复运动回路Ⅲ(图3-43和表3-43)

图3-43 用行程开关控制的连续往复运动回路Ⅲ
表3-43 用行程开关控制的连续往复运动回路Ⅲ

3.4.2 用行程换向阀控制的连续往复运动回路
3.4.2.1 用行程换向阀控制的连续往复运动回路Ⅰ(图3-44和表3-44)

图3-44 用行程换向阀控制的连续往复运动回路Ⅰ
表3-44 用行程换向阀控制的连续往复运动回路Ⅰ

3.4.2.2 用行程换向阀控制的连续往复运动回路Ⅱ(图3-45和表3-45)

图3-45 用行程换向阀控制的连续往复运动回路Ⅱ
表3-45 用行程换向阀控制的连续往复运动回路Ⅱ

3.4.2.3 用行程换向阀控制的连续往复运动回路Ⅲ(图3-46和表3-46)

图3-46 用行程换向阀控制的连续往复运动回路Ⅲ
表3-46 用行程换向阀控制的连续往复运动回路Ⅲ

3.4.2.4 用行程换向阀控制的连续往复运动回路Ⅳ(图3-47和表3-47)

图3-47 用行程换向阀控制的连续往复运动回路Ⅳ
表3-47 用行程换向阀控制的连续往复运动回路Ⅳ

3.4.3 用压力继电器控制的连续往复运动回路(图3-48和表3-48)

图3-48 用压力继电器控制的连续往复运动回路
表3-48 用压力继电器控制的连续往复运动回路

3.4.4 用顺序阀控制的连续往复运动回路
3.4.4.1 用顺序阀控制的连续往复运动回路Ⅰ(图3-49和表3-49)

图3-49 用顺序阀控制的连续往复运动回路Ⅰ
表3-49 用顺序阀控制的连续往复运动回路Ⅰ

3.4.4.2 用顺序阀控制的连续往复运动回路Ⅱ(图3-50和表3-50)

图3-50 用顺序阀控制的连续往复运动回路Ⅱ
表3-50 用顺序阀控制的连续往复运动回路Ⅱ

3.4.5 行程和压力联合控制的连续往复运动回路(图3-51和表3-51)

图3-51 行程和压力联合控制的连续往复运动回路
表3-51 行程和压力联合控制的连续往复运动回路

3.4.6 气动控制的连续往复运动回路(图3-52和表3-52)

图3-52 气动控制的连续往复运动回路
表3-52 气动控制的连续往复运动回路

3.5 限程回路
3.5.1 用行程换向阀限程的回路(图3-53和表3-53)

图3-53 用行程换向阀限程的回路
表3-53 用行程换向阀限程的回路

3.5.2 用液压缸结构限程的回路(图3-54和表3-54)

图3-54 用液压缸结构限程的回路
表3-54 用液压缸结构限程的回路

3.6 液压缸定位回路
3.6.1 液压缸三位定位回路
3.6.1.1 液压缸三位定位回路Ⅰ(图3-55和表3-55)

图3-55 液压缸三位定位回路Ⅰ
表3-55 液压缸三位定位回路Ⅰ

3.6.1.2 液压缸三位定位回路Ⅱ(图3-56和表3-56)

图3-56 液压缸三位定位回路Ⅱ
表3-56 液压缸三位定位回路Ⅱ

3.6.2 液压缸多位定位回路(图3-57和表3-57)

图3-57 液压缸多位定位回路
表3-57 液压缸多位定位回路

3.7 方向控制回路应用实例
3.7.1 混凝土输送泵开式液压系统
在此以HBT60混凝土输送泵液压系统为例,介绍混凝土输送泵液压系统及换向控制过程。
(1)泵送工作原理
混凝土输送泵采用水平单动双列液压推送活塞式结构,主要包括2只主缸、2只混凝土缸、2只摆动缸、分配阀(又称S摆管)、换向机构、料斗等。其中2只混凝土缸的活塞分别与2只主缸活塞杆连接。
如图3-58(a)所示,泵送混凝土时,在主缸作用下,混凝土缸活塞1前进,混凝土缸活塞6后退。同时,在摆动缸作用下,S摆管4与混凝土缸2连通,另一只混凝土缸5与料斗3连通。这样混凝土缸活塞6后退便将料斗内的混凝土吸入混凝土缸5,混凝土缸活塞1前进,将混凝土缸2内的混凝土送入S摆管泵出。

图3-58 正泵工况与反泵工况
1、6—混凝土缸活塞;2、5—混凝土缸;3—料斗;4—S摆管
当混凝土缸活塞6后退至行程终端时,触发换向装置,主缸换向,同时摆动缸换向,使S摆管4与混凝土缸5连通,混凝土缸2与料斗连通,这时活塞1后退,使混凝土缸2吸入混凝土,活塞6前进,将混凝土缸5内的混凝土送入S摆管泵出,如图3-58(b)所示。
如此循环,从而实现混凝土连续泵送。
反泵工况,如图3-58(c)所示,使处在吸入行程的混凝土缸与S摆管连通,处在推送行程的混凝土缸与料斗连通,从而将管路中的混凝土抽回料斗。当正常泵送过程中遇到输送阻力增大,输送管路有堵塞时,用反泵工况来排堵。
(2)混凝土输送泵液压系统
混凝土输送泵有3大主要功能,一是主泵送功能,吸送混凝土;二是换向功能,使S摆管与主泵送液压缸交替换向;三是搅拌功能,对料斗里的混凝土进行搅拌。其液压原理如图3-59所示,有3个子系统,即主泵送系统、换向系统和搅拌系统。

图3-59 液压原理图
1、2、3—吸油过滤器;4、12—单向阀;5—副泵;6—恒压泵;7—主泵;8、13、22—溢流阀;9—电磁换向阀;10、18、19、24—压力表;11、25—压力继电器;14、23—电液换向阀;15—截止阀;16—减压阀;17—单向节流阀;20—蓄能器;21—冷却器
①主泵送系统 主泵送系统主要由主泵7、电液换向阀23、溢流阀22、泵送主缸等组成。主泵输出的高压油直接进入电液换向阀23,当电液换向阀23处在中位状态时,压力油通过冷却器21和回油过滤器3流回油箱;当电液换向阀23左(右)位工作时,压力油向主缸供油。二主缸采用串联连接,在主泵压力油作用下,一缸前进另一缸后退。当活塞运行到行程终点时,触发换向装置,电液换向阀23右(左)位工作。由于压力油方向改变,从而使主缸活塞运动方向改变,实现主缸活塞的交替前进、后退。
主泵选用恒功率控制的轴向柱塞斜盘式变量泵,在恒功率区域内,当混凝土管路中压力升高时,主泵斜盘倾角会自动减小,排量减小,而功率保证为恒定值,使电动机不至于过载,功率利用高。该泵还带有附加的液压行程限制器和压力切断装置。主泵的控制压力由恒压泵6输出,通过减压阀16使压力在0.5~3.5MPa范围内变动,则主泵输出排量在最小和最大范围内无级变化;当泵送油压超过系统额定压力32MPa时,压力切断装置使主泵斜盘回到零位,主泵排量为零,泵送作业停止。溢流阀22为安全阀,其压力设定值可比压力切断值高1~2MPa,主泵在任何条件下都不会出现高压溢流,从而消除系统中的最大发热源。单向阀4起保护冷却器的作用。
②换向系统 换向系统主要由恒压泵6、单向阀12、蓄能器20、溢流阀13、电液换向阀14、截止阀15、摆动缸等组成。当电液换向阀14阀芯处在中位时,恒压泵6泵出的油经单向阀12、单向节流阀17进入蓄能器,当蓄能器内压力达到18MPa时,恒压泵内的压力控制阀作用,使伺服缸通过连杆推动液压泵斜盘,减小油排量,达到节能目的。当电液换向阀14一端电磁铁通电时,阀芯移动,一摆动缸接通,蓄能器20内储存的压力油经单向节流阀17和恒压泵泵出的油一起进入摆动缸,推动S摆管摆动。当电液换向阀另一端电磁铁通电时,另一摆动缸接通,推动S摆管向相反方向摆动。溢流阀13起安全阀作用,其压力设定值为23MPa。蓄能器的作用是使S摆管迅速换位(交替与两个混凝土缸接通与断开),并减小系统压力波动。
正泵工作时,电磁铁YA1、YA3与YA2、YA4交替通电,自动完成混凝土泵送。当泵送过程中遇到输送管道堵塞时,输送阻力增大,液压系统负荷剧增,当压力达到一定值时,压力继电器25发出信号,自动切换到反泵状态,电磁铁YA1、YA4与YA2、YA3交替通电,反泵状态持续设定时间(一般为4~6个工作循环),自动恢复到正泵状态。
③搅拌系统 搅拌系统由副泵5、溢流阀8、电磁换向阀9、压力继电器11、搅拌马达等组成。当电磁铁YA5通电,电磁换向阀左位工作时,马达正转带动搅拌轴正转,可将料斗中的骨料搅拌均匀,使其具有良好的可泵性,并将其推向料斗的进料口,从而增加混凝土的吸入能力。
当搅拌轴被石子卡死时,压力继电器11发信号,使电磁铁YA5断电、YA6通电,电磁换向阀右位工作,液压马达带动搅拌轴反转,可将卡死在搅拌轴中的石子等排除。当反转达到电控系统设定时间,YA6断电、YA5通电,电磁换向阀左位工作,搅拌轴恢复正转。
④油箱及其他 采用了封闭式液压油箱,能防止杂质混入油中,为了滤清空气、便于观察箱内油位高度、控制油温及过滤油液,在油箱上安装了空气滤清器、液位计、油温表、冷却器、吸油过滤器和回油过滤器。过滤器上装有真空表,当真空表指针超过规定值时,表示滤芯堵塞,要求用户清洗和更换滤芯。
(3)液压系统技术要点
①同一电动机驱动3个液压泵 液压系统中,主泵送系统、换向系统、搅拌系统分别由主泵、恒压泵和副泵驱动,3个液压泵均选德国力士乐公司原装件,分别是A11VO250LRDH2/11R-NZD12K02、A10VO28DR/31R.PSC62K01和1PF2G2-4X/020RR20MR,三者采用通轴传动由同一电机驱动,结构紧凑,便于控制。
②恒压泵与蓄能器配合的换向系统 由恒压泵驱动,流量能根据负载需要自动调整。其压力设定为18MPa。当系统压力达到压力设定时,因此时摆缸还没有动作,变量泵斜盘倾角回到零位,几乎没有流量排出,避免液压泵功率损失。当摆缸动作时,系统压力迅速降低,变量机构控制泵斜盘倾角很快变到最大位置,给摆缸提供足够的压力油;同时,当摆缸开始动作时,由蓄能器储存的能量能在瞬间向系统提供大流量的高压油,使摆缸获得快速运动。
③主缸装有TR机构 当活塞运动到节流阀和单向阀之间时,高压油通过节流阀、单向阀,进入活塞的另一侧,使高低压油腔沟通。此TR装置有3个目的,一是使活塞换向更加及时,可充分利用液压缸有效行程,防止活塞和缸底碰撞;二是为活塞换向运行作准备,缓解了换向冲击;三是为封闭腔自动补油,保证活塞行程不变短。
④低压大排量与高压小排量两种泵送方式 由于主缸采用单杆活塞式液压缸,两腔受压面积不同,当有杆腔进油时,为低压、高速;当无杆腔进油时,为高压、低速。通过调换主缸的软管连接线路可实现高、低压两种泵送方式,一般当泵送油压达25~26MPa时可采用高压泵送。
3.7.2 基于电液比例技术的船舶液压舵机
(1)人工舵机操作概述
我国内河船舶液压舵机多为人工舵,主要依靠操舵人员的经验,根据舵角指示仪反馈舵角与航向的偏差决定换向阀的动作,进而控制舵角并不断地修正。操舵人员劳动强度大,航行安全存在隐患,操舵频率过高,航向保持精度差,为开式系统。人工舵控制如图3-60所示。

图3-60 人工舵控制示意图
(2)系统的改进
电液比例技术发展迅速,在液压系统控制中具有操作方便,容易实现遥控,容易实现编程控制,工作平稳,控制精度较高,对污染不敏感等特点,针对内河船舶液压舵机的不足加以改造,大有可为。
①基于电液比例技术的内河船舶液压舵机
a.电液比例阀。电液比例阀是电液比例控制技术的核心和功率放大元件,代表了流体控制技术的发展方向。它以传统的工业用液压控制阀为基础,采用电-机转换装置,将电信号转换为位移信号,按输入电信号指令连续、成比例地控制液压系统的压力、流量或方向。电液比例阀可以同时实现流量、压力、方向等多参数的复合控制,主要分成比例放大器、比例电磁铁、液控主阀,通过比例电磁铁推动阀芯,经闭环控制,准确定位阀芯位置,改变动态液阻,既能实现换向功能来改变液流方向,又可以使得液流的流量得到精确控制。电液比例阀控制示意如图3-61所示。

图3-61 电液比例阀控制示意图
b.液压系统。液压系统如图3-62所示。舵机设置1个主操舵装置和1个辅助操舵装置。主操舵装置和辅助操舵装置的布置,满足当它们中的1个失效时应不致使另1个也失灵。主操舵装置采用电液比例换向阀作为线性受控单元,比例放大器首先接受来自PLC的模拟量信号,通过前置放大、功率放大、反馈校正、PID调节等处理,产生与指令要求相适应的精确电信号传给比例电磁铁;比例电磁铁会生成相应的电磁力,推动阀芯产生一定的位移,阀芯形成一定的开度,起到阻尼作用,其流出、到达油量就成为可控、可调的了。随着比例放大器对信号处理的不断修正,液阻随之动态变化,输出的流量、压力和方向也就随之变化,实现动态控制。

图3-62 液压系统图
辅助操舵装置作为主操舵装置不能正常工作下的应急操舵,采用手动操舵,通过按钮操控电液换向阀电磁铁的通电与断电,使油路的方向转换,实现手扳舵转,复位舵停,左舵左扳,右舵右扳的直接控制。
②PLC控制系统
a.可编程控制器。可编程序逻辑控制器(PLC)是专为工业环境下应用而设计的工业计算机,可在恶劣的工业现场工作,能够完成顺序控制、位置控制、数据处理、在线监控等功能。特别具有过程控制功能,控制算法(PID)控制模块的提供使PLC具有了闭环控制的功能,控制过程中变量出现偏差时,PID会计算出正确的输出,把变量保持在设定值上。
b.系统的控制算法。在工程实际中,应用最广泛的是PID控制器。PID舵调节规律是以船舶偏航角Δψ、偏航角速度和偏航角角积分给出舵角β,其表达式为:
式中,Kp,Ki,Kd为PID型自动舵的设计参数。比例系数Kp决定控制作用的强弱;积分系数Ki消除系统静差;微分系数Kd有助于减小系统的超调,克服振荡,使系统趋于稳定,加快响应。
在可编程控制器PID控制中,使用的是数字PID控制器,采用的是增量式PID控制算法,根据采样时刻的偏差计算控制量,通过软件实现增量控制。西门子S7-200系列PLC提供了用于闭环控制PID运算指令,用户只需在PLC的内存中填写一张PID控制参数表,再执行相应的指令,即可完成PID运算,改变国内模拟PID舵线路繁杂、稳定性和操控性较差等方面的不足。
c.控制方框图。PID自动舵控制方框图如图3-63所示。

图3-63 PID自动舵控制方框图
图3-63中,当系统设定航向,首先传送至PLC,经D/A转换变成模拟量指令,作为比例放大器输入信号,比例放大器相应输出模拟量提供给比例电磁铁,产生对应的力或位移,作用在电液比例方向阀,从而得到相应的流量、压力以驱动液压缸,进而形成一定的速度或力来驱动舵叶,改变船舶的航向。运用相应的检测元件将船舶航向反馈信号再传回进行比较,以便动态地调整舵角,使最终的船舶实际航向与设定航向相一致。
d.系统软件。PID自动舵控制系统的软件部分主要由手动、随动和自动三部分组成,由控制面板相应的开关进行选择,其系统控制流程如图3-64所示。

图3-64 系统控制流程图
3.7.3 汽车起重机液压系统
(1)概况
汽车起重机是将起重机安装在汽车底盘上的一种起重运输设备,由于具有机动灵活、能以较快速度行走的作业特点。汽车起重机主要由行驶部分及作业部分两部分组成,其中作业部分又包括变幅机构、伸缩机构、起升机构、回转机构和支腿机构。汽车起重机的外形结构示意如图3-65所示。

图3-65 汽车起重机结构示意图
1—变幅机构;2—伸缩机构;3—起升机构;4—回转机构;5—支腿机构
汽车起重机作业机构的所有动作都是在液压驱动下完成,如汽车起重机的吊臂变幅动作、吊臂伸缩动作、起升动作、回转动作以及支腿动作,都是在液压系统的驱动下完成的。在所有机构运行过程中,液压系统起着至关重要的作用。
汽车起重机液压系统的关键件包括主液压泵、主控制阀、支腿操纵阀、主副卷扬和回转减速机等。主液压泵由底盘发动机驱动,主控制阀分别控制回转、伸缩、变幅及卷扬作业动作,支腿操纵阀通过底盘单侧或两侧操纵杆控制支腿同时或单独工作。汽车起重机的作业机构操纵方式通常可以采用手柄操作和电液先导控制两种。在汽车起重机液压系统中包含了多种形式的液压基本回路,如平衡回路、锁紧回路、制动回路、减压回路以及换向回路等。
(2)技术要求
汽车起重机主要的工作任务就是起吊和转运货物,由于汽车起重机执行元件需要完成的动作较为简单,位置精度要求低,因此汽车起重机的大部分作业机构采用手动操纵方式即可。
作为起重机械,除了完成必要的起吊和转运货物的工作任务外,保证起重作业中的安全也是至关重要的问题,因此采取必要的保护措施、保证汽车起重机作业的安全是液压系统设计的重要目标之一。
汽车起重机对作业的安全性要求高。汽车起重机液压系统要能够保证各动作机构的动作安全。保证安全动作的要求如下。
①起吊重物时不准落臂,必须落臂时应将重物放下重新升起作业,此时,伸缩和变幅机构的液压回路必须采用平衡回路。
②回转动作要平稳,不准突然停转,当吊重接近额定起重量时,不得在吊离地面0.5m以上的空中回转。
③起重机在起吊重载时应尽量避免吊重变幅,起重臂仰角很大时不准将起吊的重物骤然放下,防止后倾,这些都要求汽车起重机液压系统的子系统之间采用适当的连接关系。
④汽车起重机不准吊重行驶。
⑤防止出现“拖腿”和“软腿”事故。
⑥防止出现“溜车”现象。
对于汽车起重机液压设备,要完成的动作主要包括起升、伸缩、变幅、回转动作及支腿伸出和缩回动作,每个工作机构要完成的动作循环简单,但整个液压设备的工作机构较多,工作机构之间的互锁、防干涉等关系复杂。
(3)液压系统
某型号汽车起重机液压系统原理如图3-66所示。

图3-66 汽车起重机液压系统原理图
按照能源元件、执行元件、控制调节元件以及辅助元件的浏览顺序确定图3-66汽车起重机液压系统的组成元件,并初步确定各元件的功能。
能源元件:3个同轴连接的定量液压泵,为整个液压系统提供油源。
执行元件:4个水平支腿液压缸,实现水平支撑的作用;4个垂直支腿液压缸,实现垂直支撑的作用;1个伸缩液压缸,使吊臂(手臂)伸缩;1个变幅液压缸,使吊臂变幅;1个回转定量液压马达,使起重设备回转;1个起升定量液压马达,使吊重起升或下落;2个制动液压缸,使起升液压马达制动;2个离合器液压缸,使卷筒与起升液压马达接合。
控制调节元件:2个三位四通弹簧复位式手动换向阀,分别操纵水平和垂直支腿的动作;1个二位三通钢球定位式手动换向阀,使油路在支腿和工作机构之间切换;4个转阀式手动开关阀,控制垂直支腿液压缸的动作;2个三位五通钢球定位式手动换向阀,控制离合器和制动器动作;3个三位六通弹簧复位式手动换向阀,分别操纵回转、伸缩和变幅机构;1个五位六通钢球定位式手动换向阀,操纵起升动作;6个溢流阀(安全阀),调定系统工作压力;1个减压阀,使离合器和制动器回路得到低于主回路的压力;1个顺序阀,实现蓄能器充液和工作机构的顺序动作;3个平衡阀,构成平衡回路;2个梭阀,使控制油始终为压力油;8个液控单向阀,形成双向液压锁;2个固定节流孔,防止冲击;若干个单向阀,防止油液倒流。
辅助元件:1个蓄能器,作辅助油源和应急油源;1个油箱,贮存油液;2个过滤器(精滤和粗滤),过滤油液。
3.7.4 液压钻机起升系统
MC90Y钻机是用于煤层气钻井的全液压专用钻机,整机采用液压驱动,PLC电控操作。其起升系统通过比例变量泵控制主液压缸的伸缩来实现顶部驱动装置的上提和下放操作,液压缸的伸缩变换通过插装阀组实现。在测试过程中,液压缸可以实现伸缩动作,但在伸缩转换过程中,存在8s左右的时间延迟,从而影响钻井过程中对钻具的上提和下放的转换操作。
(1)起升系统工作原理
如图3-67所示,起升系统通过垂直状态的液压缸伸缩,经倍程机构带动顶驱上提和下放。从而实现钻具的上提和下放。为了满足钻井要求,MC90Y钻机的主液压缸最大推力为180t,最大起升速度为1.4m/s,最大流量为2500L/min,通过比例变量泵提供流量。为减少控制阀件,换向功能采用了大流量插装阀组。工作时,比例变量泵接收比例手柄的控制信号,输出控制流量,控制主液压缸的运动速度。主液缸换向通过控制插装阀组上4个开关插装阀的不同开关组合实现。液压缸伸出时,插装阀DT2和DT4打开、DT1和DT3关闭;液压缸缩回时,插装阀DT1和DT3打开、DT2和DT4关闭。此外,插装阀控制采用了内控内排的形式,为了保证工作过程中插装阀DT2和DT3能够有效锁定关闭,插装阀DT2和DT3选用了梭阀机能,当液压缸A腔或B腔回油压力较大时,通过梭阀的选择机能,使插装阀DT2或DT3的关闭功能能始终有效。由于液压缸垂直作业,为使重力负载得到有效的控制,液压缸无杆腔安装了平衡阀,从而使液压缸缩回时比例可控。

图3-67 起升系统液压原理简图
(2)延迟问题及分析
钻机起升系统在调试时,当液压缸连续单方向运行时,控制手柄动作,液压缸很快就可以动作,当控制形式为液压缸伸缩之间切换时,液压缸要经过8s左右才会开始反向运动,多次测试后发现问题始终存在,且时间基本在8s左右。针对整个系统的结构形式,问题分析从电气、液压、控制等方面依次展开。
①测试时为保证安全,发动机转速为800r/min,低于设计速度1800r/min,因此怀疑为供油不足导致延迟,但依次增大发动机转速直至1800r/min,问题依旧,且延迟时间没有变化。
②通过控制手柄正反向运动,观察其关联的继电器是否有执行动作,关联的变量泵控制板是否有信号动作反应,发现继电器和比例放大板在手柄换向操作时,立即出现信号指示,说明电气硬件安装正常和控制程序编写正确。
③在手柄操作过程中,测量比例放大板输出信号和比例变量泵位移传感器反馈信号。测量表明,信号跟随和反馈正常,说明比例变量泵工作正常,不是导致延迟的原因。
④在不启动泵组的情况下操作手柄,插装阀组和安全阀可以听到开关声音,用手可以感觉到安全阀和插装阀控制电磁阀动作时的振动,反应正常,不存在明显延迟。
⑤通过上述测试基本可以判明,起升系统从控制到电气再到液压系统总体设计不存在问题,导致延迟的原因很可能是插装阀组中插装阀的开启和关闭特性造成的。基于此,通过控制系统手动功能测试。手动控制4个插装阀的开关顺序,同时比例变量泵小流量供油,观察液压缸动作和系统压力表的变化。
在插装阀DT1和DT3关闭、DT2和DT4开启条件下,关闭插装阀DT2,液压缸继续缓慢伸出,在8s左右停止伸出,同时系统压力开始上升,此时开启插装阀DT2,液压缸立刻开始伸出;在插装阀DT1和DT3开启、DT2和DT4关闭条件下,关闭插装阀DT3,液压缸继续缓慢收缩,在8s左右停止收缩,系统压力开始上升,此时开启插装阀DT3,液压缸立刻开始收缩。多次重复上两种操作,状态相同,从而可以判定由于插装阀DT2和DT3的关闭机能滞后,导致换向时8s左右的时间延迟,泵组供油通过插装阀DT2或DT3经DT1或DT4直接返回油箱,直至插装阀DT2或DT3完全关闭后,液压缸才开始动作。
(3)延迟问题解决方案
①插装阀工作机理分析 插装阀DT2和DT3的职能符号如图3-68所示,插装阀主体包含3个部分:上部的控制阀,中部的盖板和下部的插装阀插件。插装阀插件包括阀套、弹簧和阀芯(图3-69),梭阀包含在盖板中。通过控制上部控制阀,可以使阀芯的弹簧容腔内获得高压油或释放到油箱,从而与弹簧共同完成阀芯的开关动作。梭阀的控制口Z1和X分别与阀芯的A或B口连通,在关闭状态下,A或B任意一端存在高压时,都可通过梭阀和控制阀连通到阀芯弹簧容腔。由于关闭时,阀芯上端总面积与下端A或B口连通的阀芯面积比为2:1,因此在压差作用下,可以确保阀芯关闭。

图3-68 插装阀职能符号图

图3-69 插件结构图
在本系统中,问题出现在阀芯关闭过程中,在主液缸从伸出转换到缩回时,DT2和DT4关闭、DT1和DT3开启。此时DT1虽然与油箱连通,但需要一定的压力克服阀芯弹簧力,因此A1腔中还有一定的开启压力。DT2阀芯在没有完全关闭时,阀芯上下端面的面积相等,且所受压力相等,因此,阀芯的关闭完全由复位弹簧来实现。由于阀芯关闭过程中要克服具有开启压力的液压油阻力,而复位弹簧力较小,且Z1口和X口压力相等,梭阀中的控制球在阀芯关闭过程中很可能在油压和阀芯容腔吸力的作用下停止在控制输出口附近,使阀芯容腔油液补充速度降低,在一定程度上也会影响阀芯的关闭速度。
②解决措施 由于密闭的A1或B1腔液压阻力的影响,复位弹簧不能快速关闭阀芯,使系统出现延迟,因此增加复位力就可以解决延迟问题。从插装阀工作机能可以得出,增大弹簧的刚度,增大克服液压阻力的能力可以提高关闭速度。在更换DT2和DT3弹簧为2倍刚度的弹簧后,换向延迟现象消失,钻机在连续钻井作业过程中工作正常,起升系统换向操作满足钻井作业要求。