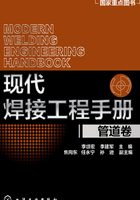
第4章 管道工程焊接工艺评定及焊接工艺规程
4.1 焊接性试验
施工单位首次采用的钢材、焊接材料和焊接方法,应进行焊接性试验。对于较易产生冷裂纹的钢材,应进行冷裂纹敏感性试验。对于较易产生热裂纹的钢材,应进行热裂纹敏感性试验。
4.1.1 焊接性试验的目的
通过焊接性试验初步确定焊接方法、焊接设备、焊接材料、预热温度、后热温度和焊后保温等。
4.1.2 冷裂纹敏感性试验方法
①GB/T 4675.1《焊接性试验 斜Y形坡口焊接裂纹试验方法》
②GB/T 4675.2《焊接性试验 搭接接头(CTS)焊接裂纹试验方法》
③GB/T 4675.5《焊接性试验 焊接热影响区最高硬度试验方法》
④GB/T 9446《焊接用插销冷裂纹试验方法》
⑤GB/T 13817《对接接头刚性拘束焊接裂纹试验方法》
4.1.3 热裂纹敏感性试验方法
①GB/T 4675.1《焊接性试验T形接头焊接裂纹试验方法》
②GB/T 4675.4《焊接性试验 压板对接(FISCO)焊接裂纹试验方法》
4.1.4 焊接性试验方法的选择
根据钢材的化学成分、力学性能和使用性能通常选用一种或两种焊接性试验方法。当材料的焊接性较复杂时,应采用多种试验方法进行综合评定。
4.2 焊接工艺评定
焊接工艺评定是由施工单位进行的焊接工艺验证性试验。焊接工艺评定的目的有两个:一是,证明施工单位按照本单位的管理方法、焊工技术水平、设备性能和检验手段有能力焊接出符合相关法规、标准和设计要求的焊接接头;二是,通过焊接工艺评定确定焊接方法、焊接设备、焊接材料、焊工技术水平和焊接工艺参数。
4.2.1 管道焊接工艺评定常用标准
①SY/T 0452《石油天然气金属管道焊接工艺评定》
②SY/T 4103《钢质管道焊接及验收》
③GB 50236《现场设备、工业管道焊接工程施工及验收规范》
④JB4708《钢制压力熔器焊接工艺评定》
⑤API 1104《管道及有关设施的焊接》
⑥ASME《锅炉及压力容器规范》Ⅸ:《焊接和钎焊评定标准》
4.2.2 焊接工艺评定程序
焊接工艺评定流程框图见图2-4-1。

图2-4-1 焊接工艺评定流程框图
4.2.3 焊接工艺评定的基本要求
①由施工技术部门根据工程设计要求和施工图提出焊接工艺评定委托书。委托书至少包括下列内容:焊接方法、采用标准、合格指标、钢管材质和规格等。
②由焊接试验工程师编写焊接工艺评定指导书。焊接工艺评定指导书至少包括下列内容:焊接方法、接头形式、坡口形式及尺寸、钢管材质和规格、钢管化学成分和力学性能、焊材型号和规格、焊材化学成分和力学性能、焊接位置、预热和后热、电流种类及极性、焊接工艺参数等。
③试件(母材)和焊接材料必须有质量证明书,质量证明书的项目应齐全且符合标准的要求。
④试验用各种设备、仪器、仪表齐全,工作正常、准确。
⑤应由本单位操作技术水平较高的焊工严格按焊接工艺指导书的要求焊接工艺评定试件。试验过程中,应对坡口形式和尺寸、组装质量、环境温度、湿度、风速、预热温度、层间温度、设备、焊接材料、焊接工艺参数、清理状况等全面、认真地记录。
⑥由检验员按标准和设计要求对试件进行外观检查并写出检查报告,合格后进行无损检测;如不合格应修正焊接工艺参数后重新焊接试件(当缺陷不严重时,可以进行修补,不需重焊)。
⑦外观检查合格后,进行无损检测并填写检测报告。无损检测人员应持有技术监督部门颁发的相应资格证书。无损检测合格后,方可进行力学性能及其他试验。如无损检测不合格应修正焊接工艺参数后重新焊接试件。
⑧无损检测合格后,按规定的位置切取试样。试样切取应采用机械方法,也可采用火焰切割或等离子切割,但应留出将切割热影响区加工掉的加工余量。
⑨按标准规定进行各项试验并填写试验报告。任何一项试验不合格,均应重新调整参数,重新焊接工艺评定试件,重新进行各项检验和试验,直至合格。
⑩所有试验完成后,编写焊接工艺评定报告。焊接工艺评定报告至少包括下列内容:焊接方法、接头形式、坡口形式及尺寸、钢管材质和规格、钢管化学成分和力学性能、焊材型号和规格、焊材化学成分和力学性能、焊接位置、预热和后热、电流种类及极性、焊接工艺参数等。焊接工艺评定报告由焊接试验工程师编写,焊接责任工程师审核,技术总负责人批准后方可实施。
4.2.4 焊接工艺评定项目及试件数量
(1)评定项目 根据焊接方法、管材分组、焊材分组进行评定。另外,返修焊接还需模拟实际返修情况进行返修焊接的工艺评定。返修焊接采用与正式焊接相同的焊接方法和焊接材料,也需进行返修焊接的工艺评定。在国际管道工程中,部分监理公司要求进行一次返修焊接工艺评定和二次返修焊接工艺评定,而且全透和非全透的返修也要分别评定。
(2)评定试件数量 对于国内常用的钢材(即有较成熟的应用经验),试件数量能满足取样要求即可;但对国内开发的新钢种或进口的新钢种,应至少焊接两组试件,以确保各参数的准确性。
4.3 焊接工艺规程的制定
焊接工艺规程分为通用性焊接工艺规程和专用性工艺规程,焊接工艺流程框图见图2-4-2。

图2-4-2 管道焊接流程框图
4.3.1 通用性焊接工艺规程
通用性焊接工艺规程,是本单位(或本行业)通用性的焊接工艺文件,所有焊接工作均应遵守。它规范的是原则性的问题,一般不规定具体数据,有数据也是原则性的,一般给一个较大的范围。
4.3.2 专用性焊接工艺规程
专用性焊接工艺规程,是对某一工程编制的专用性文件,一般来说只适用于某一工程。专用性焊接工艺规程要详细规定焊接人员、焊接设备、焊接材料、坡口形式及尺寸、组装质量、清理要求、预热要求、焊接层数和焊接道数、层间清理、层间温度、焊接电流、电弧电压、送丝速度、焊接速度、干伸长度、气体流量、焊枪摆动方式、摆动速度、摆动宽度、两侧停留时间、焊后保温、后热及对环境温度、湿度和风速的要求等。
4.3.3 焊接工艺规程的内容
(1)执行标准 焊接工艺规程应列出规程中所执行的主要标准。
(2)材料 应包括对钢材(母材)和焊接材料的详细要求。
(3)焊接性试验及焊接工艺评定 通用焊接工艺规程中应规定焊接性试验及焊接工艺评定的执行标准、工艺评定项目、工艺评定试件数量、工艺评定流程、工艺评定试样及各种报告的保存要求;专用焊接工艺规程,是在焊接性试验和焊接工艺评定完成后编写的,所以无焊接性试验及焊接工艺评定的内容。
(4)焊工培训及焊工考试 应规定焊工的培训内容、考试项目和合格标准。
(5)坡口的加工与清理 应规定坡口是在管道厂加工还是现场加工、加工方法和加工要求,坡口及两侧的清理方法和清理要求。
(6)施焊环境 施焊环境的天气情况、温度、湿度和风速等。
(7)焊前预热和层间温度 应规定焊前预热方法、预热温度、预热宽度、加热速度等,以及层间间隔时间和层间温度的要求。
(8)焊接设备 应规定焊接设备的种类、特性、额定功率、对设备上各仪器仪表的要求和操作规程等。
(9)焊接 每一层焊道的焊接方法、焊接设备、操作方法、焊材型号规格、焊道厚度、焊道数量、详细的焊接工艺参数和对层间清理的要求等。
(10)焊后保温缓冷及后热 对焊后保温和后热的要求,如钢材强度等级、管壁厚度、保温材料、保温时间、后热加热方法、后热温度、后热时间、后热加热范围、测温方法等。
(11)焊后清理 应规定清理方法和清理标准及清理时应注意的事项。
(12)外观检查 应规定外观检查方法和工具,外观检查合格标准。
(13)修磨和修补 外观检查不合格(裂纹、未熔合等严重缺陷除外),应进行修磨和修补,应规定修磨方法和修补方法及修磨和修补应注意的事项。
(14)焊缝标记 焊缝标记方法(钢印、书写或喷印),标记的编写规则、字体、大小和标记位置等。
(15)无损检测 无损检测方法、无损检测标准、无损检测比例及合格等级。
(16)焊缝的返修 经无损检测不合格或经外观检查缺陷的清除深度超过规定值,均属焊缝的返修。返修焊接工艺应包括缺陷的定性、定位、编写焊缝返修工艺、返修焊工资格、缺陷的清除方法、预热、焊接工艺参数、返修后的检查、检测要求,保温、后热及返修的监督措施等。