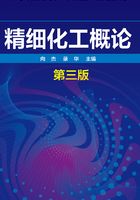
第三节 分离提纯技术发展近况
随着现代生产和科学技术的飞速发展,人们对分离技术提出了越来越高的要求,对产品分离纯度的要求越高,难度就越大。例如,在生命科学的基础研究——蛋白质的分离和纯化以及基因工程产品的纯化过程中,有时就会出现回收率低的现象,其原因是分离过程中发生了部分生物大分子的失活,而难以得到一定量的目标产品。另外,运用现代分离技术分离的对象有些是十分昂贵的,若回收率降低1%,损失就十分惊人,如对某些总量1g的稀贵蛋白质而言,若回收率降低1%,损失可达几十万元。因此,发展现代分离技术也是适应新兴高利润、高技术工业的需要。
在精细化工领域,许多新产品要求高纯度、高性能,为制取这类产品,不仅反应过程需要新工艺,而且分离过程更需要新的技术。目前新的分离技术发展很快,现将其简述如下。
1.错流微量过滤
错流微量过滤是用错流流动方式进行的微量过滤。过滤时料液流动与过滤介质平行,故可称为“平行过滤”。在过滤过程中,被截留的物料一般不会沉积在过滤介质表面形成难以渗透的滤饼,而是被进料流连续带走,仅在过滤介质表面的边界处有轻微沉积,所以基本上是无滤饼过滤,可以周期性地洗涤清除。过滤介质一般是用合成材料或陶瓷材料制成的高孔隙率薄膜,常用薄膜的孔径在0.2μm左右。错流微量过滤可以过滤非常细及非常稀的悬浮物,不需添加絮凝剂及过滤剂。错流微量过滤在酒、醋和果汁的过滤中已有较大规模的应用,另外在油品、染料等方面也有应用。
2.熔融结晶
熔融结晶是根据物质熔点不同进行的结晶分离。熔融结晶具有能耗低、操作温度低、选择性高和设备体积小的优点。熔融结晶常用逐渐凝固法制得产品。逐渐凝固法晶体在冷表面上生长,其生长速度是悬浮结晶法的10~100倍,适于工业应用。其分步结晶步骤如下:①先生成晶层;②将剩余的熔融体排放出来;③加热晶层,使其部分熔融以排出包附在晶层中的杂质;④将所剩晶层熔化下来,并收集作为产品或中间产品。熔融结晶可用于萘、二甲苯、对硝基甲苯、双酚A、对二氯苯等有机化学品及食品的分离和精制。
3.高效液相色谱分离
传统的液相色谱分离方法是使用大颗粒易破碎的载体,分离时间长、效率低。高效液相色谱所用载体颗粒小、孔径大,可以把能与被分离物质相互作用的化学基团,以共同的形式连接到载体颗粒的表面上或结构中,用以改善分离效果。所用载体材料有硅胶及多聚物。
高效液相色谱的种类主要如下。
①离子交换色谱。根据物质所带电荷的强度实现分离,物质用强力结合的方式固定在分离柱的载体上,然后用不同pH值或不同离子强度的缓冲液将物质释出分离。
②凝胶色谱。以物质分子的大小为基础实现分离,大于载体微孔的分子不能进入孔内,会很快穿过分离柱流出,较小分子经扩散进入微孔内,并从孔内出来,分子越小穿过分离柱的时间就越长。
③亲和色谱。靠结合在载体上的配位体分子吸附及脱附物质来实现分离。
④色谱聚焦。这是一项新的离子交换色谱技术,根据等电点的原理实现分离。高效液相色谱可以用于对二甲苯、果糖、异丙基苯、纤维素、胰岛素及蛋白质的分离。
4.超临界萃取
超临界萃取是利用超临界流体作为萃取剂,从固体或液体中有选择地萃取有用组分。超临界流体是高于气体临界温度及临界压力的流体。由于高于临界温度,流体仍保持气相状态;由于高于临界压力,流体密度增大,并随压力上升逐渐接近于液体的密度。超临界流体的密度越大,对溶质的溶解度也越大,并随密度增大逐渐接近于液体的溶解度。另外,超临界流体的性质与溶质的性质越相近,其对溶质的溶解度也越大。基于上述情况,工业上选用超临界流体的性质宜接近被萃取物的性质,操作温度与压力要选择合理,一般压力高于临界压力较多,而温度则与临界温度相近,但优化条件要通过高压相平衡数据测定及工程计算确定。常用的超临界萃取溶剂有CO2、N2O、H2O、CH3OH等。超临界萃取具有效率高、温度低、溶剂易于回收等优点,适用于分离热敏性及易氧化的物质。
超临界萃取可以间歇操作,也可以连续操作。主要有变压和变温萃取分离两种分离工艺:变压萃取分离是将萃取溶质后的超临界流体加以膨胀,由于压力降低,溶解度下降,物质就从萃取剂中析出;变温吸附是将萃取溶质后的超临界流体升温,由于温度上升,溶解度下降,物质就从萃取剂中分离出来。工业上应用超临界萃取的实例有:乙醇、除虫菊酯、咖啡因、啤酒花、香草油及药物等的萃取分离。
5.高效吸收
吸收是分离气体混合物的重要方法,吸收过程通常在吸收塔中进行。工业吸收设备长期以来以板式塔为主,20世纪80年代填料塔发展迅速,特别是新型高效填料的应用,提高了吸收效率。填料有散堆填料及规整填料两类,其中尤以规整填料中的波纹填料不断推陈出新,应用最为广泛。
波纹填料最初出现的是丝网波纹填料,由彼此平行垂直排列的波纹丝网条片组成盘状结构,波纹方向与塔轴倾角为50°或45°,相邻两片波纹相反。其后又出现了形状相似但具体结构及材质互不相同的波纹填料:Mellapak填料,用金属或塑料孔板制作,适用于特大型塔;Kerapak填料,用陶瓷烧制而成,适用于酸性物料的分离。用波纹填料进行吸收的应用面广,广泛用于硝基芳香物、脂肪酸、氯醇、胺类、香料、医药、染料等的分离。
6.选择性干燥
选择性干燥是在对含有溶剂混合物的物料的干燥过程中,有选择地除去或保留其挥发性物质。如药品干燥时,要除去有毒物质,但为压片所需的水分应保留;果汁干燥时,要除去水分,但天然香味应保留;清漆干燥时,为保持漆的光泽,漆内溶剂组成应保持不变。应用各组分干燥时挥发程度的大小来控制选择性干燥过程。选择性为零,各组分的组成在干燥时保持不变;一个组分的选择性大于1时,干燥时该组分的浓度降低;选择性小于1时,该组分在干燥时浓度增大。该法已在工业生产中有应用,如对特种纸张的干燥,使其保留一定量的水分和有用物质,以增强纸张的抗张强度等特性。
采用现代分离技术提高分离效率、降低能耗、降低成本、提高质量并促进传统分离技术不断进步,是今后的重要任务。
7.声呐结晶
用超声波影响结晶行为的技术,称为声呐结晶。超声波能对成核作用和晶体生长两方面产生影响,使成核作用在低过饱和度时诱发,对于一次成核过程,它可作为初始成核作用的额外控制手段,并可提供对晶体尺寸分布的调节作用,声呐结晶是一种有效的、更加可控的、能够代替晶种的方法。对于二次成核过程,利于超声波可产生空穴作用的机理,即气泡空穴倒塌的强烈压力可以引起显著的二次成核。超声波影响晶体生长的机理虽不易理解,但是它可以明显地影响流体流动,为提高晶体表面近旁的质量传递创造条件。由于紧邻晶体表面的空穴作用,使热量高度集中,造成暂时的不饱和,从而提高晶体的纯度。
8.双水相萃取
双水相萃取法是利用物质在互不相溶的两水相间分配系数的差异来进行萃取的方法。当两种高聚物的水溶液相互混合时,若两种被混合分子间存在空间排斥作用,使它们之间无法相互渗透,则在达到平衡时就有可能分成两相,形成双水相。两相的组成和密度均不相同,通常密度较小的一相浮于上方,称为上相(或轻相);密度较大的一相沉于下方,称为下相(或重相)。由于两相的组成不同,则两相对溶质的溶解度也不同,利用这一特点即可完成双水相萃取过程。
双水相萃取的关键是双水相的形成和溶质在双水相中的分配,其影响因素较复杂,主要包括:组成双水相系统的高聚物类型、高聚物的平均分子量及浓度;组成双水相系统的盐的种类、离子强度和浓度;被分离的各种物质的种类、性质、分配特性等;操作条件,如pH值、温度等。影响双水相萃取的因素很多,这些因素之间还有相互作用,而且双水相萃取理论正处于深入研究阶段。因此,目前还不能定量关联分配系数与各因素之间的关系,需通过大量实验,寻找适宜的双水相萃取条件,最终达到提高产品收率和纯度的目的。
双水相萃取体系虽然很多,但在应用研究中,大多集中在PEG-Dextran双水相体系的系列上。该体系的成相聚合物价格昂贵,在工业化大规模生产应用中受到了限制,因而寻找廉价的、新型双水相体系是一个重要的研究发展方向。新型双水相体系,如表面活性剂-表面活性剂-水体系、普通有机物-无机盐-水体系、双水相胶束体系等相继被发现,在双水相萃取中都显示出各自的优势;表面活性剂可增大溶质的溶解度,对有机物分离方便,这些都将推进双水相萃取技术的发展。
在生物化工中,双水相萃取技术的应用越来越多,如蛋白质、氨基酸、抗生素等药物的分离纯化。
9.高效精馏设备——折流式超重力旋转床
传统的精馏过程是利用液相在重力场的作用下与逆流的气相进行接触传质,达到分离提纯的目的。在地球的重力场下,塔设备中的液膜流动较慢,气、液接触比表面积较小,传质效率相对较低,所以设备体积庞大、空间利用率低、占地面积较大。超重力技术是一种强化气液、传质的新型技术,其工作原理是利用高速旋转产生的数百至千倍重力的离心力场(简称超重力场)来代替常规的重力场,在超重力场下,液体分散飞行时所呈现的是非常细小的液滴、液丝状态,因此气、液接触的比表面积非常大,其极佳的微观混合以及极快的相界面更新特征,使其可以极大地强化气、液传质过程,将传质单元高度降低1个数量级。从而使巨大的塔设备变为高度不到2m的超重机,达到提高效率、缩小体积以及在有些场合可大幅降低能耗的目的。
折流式超重力旋转床是一种结构独特的过程强化设备,主要由圆形外壳和折流式转子组成,折流式转子是旋转床的核心部件。其特点是传质效率高,设备体积小,停留时间短,持液量小,抗堵能力强,操作维护方便,安全可靠。适用于贵重物料、热敏物料、高黏度物料或者有毒物料的处理,可以在高度、大小受限制的场合使用。用它代替传统的塔设备,对社会的发展而言可节省钢材资源,延长地球资源的使用年限;对企业的发展而言,可以节约场地与空间资源,减少污染排放,提高产品质量,降低生产劳动强度,提高生产的安全性。折流式超重力旋转床在环保和精细化工等工业中具有十分广阔的应用前景,正在为越来越多的用户所选用。