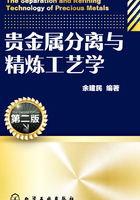
3.2 金的火法精炼
金具有很高的化学稳定性,同时具有很强的抗氧化能力。在高温下,金不能被氧化,而且也不易被氯气氯化,其他贱金属在高温下既可被氧气氧化,又可被氯气氯化,因此,火法精炼金通常采用氧化精炼法和氯化精炼法。应用火法精炼工艺处理冶炼厂的氰化金泥、粗金或回收的粗金时,精金含量通常可达到95%以上,若控制好生产条件,还能够生产出99.6%的精金。目前在国内许多中小矿山普遍采用氧化精炼法来精炼出98%的合质金,而某些大型冶炼厂则采用氯化法来生产99.9%的纯金。
3.2.1 火法氧化精炼法[2,3]
3.2.1.1 火法氧化精炼金的基本原理
火法氧化法精炼金是将含金原料与熔剂(氧化剂和造渣剂)混合,然后置于火法炼金炉中,在1200~1350℃的温度下加入氧化剂进行熔炼,得到纯度较高的金银合金。氧化除去杂质的顺序为锌、铁、锡、砷、锑、铅、铜。其中铜最难氧化,因此氧化杂质铜时,必须使用强氧化剂,如硝酸钠或硝酸钾等,方可使铜氧化。银不被空气或氧化剂所氧化,如果金中含有银,则须用其他精炼法处理,方能除去金中的银。
3.2.1.2 火法氧化精炼金的常用熔剂
火法氧化炼金法常用熔剂有两类:一类是氧化熔剂,另一类是造渣熔剂。常用的氧化熔剂有硝石、二氧化锰,其作用是使炉料中的贱金属(铜、铅、锌、铁等)氧化生成氧化物以便造渣。常用的造渣熔剂有硼砂、石英、碳酸钠等,其作用是与贱金属的氧化物反应生成炉渣。杂质在炼金炉中参与的氧化反应,一般视氧化剂的不同,主要有以下两类:
第1类,主要以空气或氧气为原料,配以其他可燃剂,调节空气或氧气和可燃剂的比例,采用小型的顶吹回转炉或是反射炉进行氧化反应,生产的金纯度可以达到95%以上。
2Me+O22MeO
第2类,主要以硝石为氧化剂,在坩埚炉或转炉内熔化金泥后并加入二氧化硅等造渣剂参与的氧化和造渣反应。通常精炼后金的纯度能达到98%,产生的渣中含有2%~3%的金。由于炉渣密度只有2~3g/cm3,比金银的密度低得多,因此冶炼过程中的炉渣将会浮在熔融金的表面上层被排除。
3Me+2NaNO33MeO+Na2O+2NO↑(氧化反应)
mMeO+nSiO2mMeO·nSiO2(造渣反应)
3.2.1.3 氧化炼金法的设备及其生产工艺
(1)坩埚炉炼金
坩埚炉炼金多用于小型矿山,适用于砂金、汞膏和含金钢棉的熔炼,也可用于熔炼氰化金泥。坩埚炉炼金是在坩埚炉中进行的,过程如下:
①升温烘烤 缓慢升高炉温,烘烤坩埚。
②加入炉料 继续加热,升高炉温至800℃时,从炉中取出坩埚,并小心地往坩埚中加入已搅拌好的炉料,并在炉料上部覆盖少量硼砂;当坩埚内的炉料熔化后,停油停风,加入用纸包好的部分炉料,继续加热。
③熔炼 加足炉料,并加入熔炼金属量4%~6%的硝石,然后进入全面熔炼阶段。通常一个20号坩埚一次可以熔炼10~15kg金泥,熔化需要1.5h,熔化完毕后,停油停风,用专用钳将坩埚从炉中取出,并迅速将熔体倒入蹲罐(一种倒圆锥形铸铁罐)内分层冷却,冷凝后倒出,用小锤打击将渣与金银合金分离。
④铸锭 熔炼完毕后,将所有的金块集中进行铸锭。
(2)转炉(顶吹回转炉)炼金
转炉多见于中型以上矿山,适用于氰化金泥的氧化熔炼。转炉和常规的燃烧煤气炉或坩埚炉相比,其优点是金的回收率高,工艺过程中积压的金量较少,作业时间短,生产成本低。转炉炼金是在转炉内进行的,过程如下:
①升温 先用木柴加热12~18h,使炉温升至800℃左右,接着用油或煤气加热4~8h,使炉温达到1200℃左右。
②投料 停火停风,把炉口侧向一边,小心地一次性加入配好的炉料。加料要快,加完料后在炉料表面上撒一层硼砂。
③熔化 加料后使炉温在最短的时间内升至最高,让炉料迅速熔化。
④倒渣 当熔体不在翻腾后0.5h即可倒渣。倒渣分两次,第1次渣占总渣量的80%,第2次要慢,以免将金的熔体倒出。
⑤铸锭 清渣后,将金液倒入铸模内,铸成金锭。
⑥停炉 停油停风,并用耐火材料或黄泥封住燃烧口和炉口,以降低炉温,保护炉衬。
(3)可控硅中频感应炼金炉炼金
可控硅中频感应炼金炉在国内最早是由吉林省冶金研究所生产的专用电炉,由KGPS型1500Hz可控硅中频电源装置及GWLJ型中频感应炼金炉两部分组成。目前国内中频感应炉技术发展迅速,中频感应炉种类繁多。可控硅中频感应炼金炉炼金多见于有色冶炼厂,主要用于金泥、合质金和成品金的熔铸。
可控硅中频感应炼金炉炼金过程如下:
①预热炉体 熔炼前,开通电源,将炉体预热5~10min,并开启炉体循环冷却水泵。
②预热坩埚 缓慢升高炉温,烘烤坩埚5~10min。
③投料 将配好的炉料加入烘好的坩埚中,并在炉料上部覆盖少量硼砂,当坩埚内的炉料熔化后,停止供电,再加入部分炉料,继续加热。炉料可分多次加入,直至加满坩埚为止。
④熔化 加料后,提高中频感应炉的阳极电流和槽路电压,使炉料尽快熔化。
⑤精炼 炉料熔化后,用导管将空气或工业氧气通入熔融金属液体中或加入适量硝石,保温熔炼10~15min,并加入适量硼砂,贱金属与氧气或硝石充分发生氧化反应,氧化为金属氧化物,金属氧化物与加入的熔剂进行造渣,炉渣浮在熔融金表面。
⑥倒渣 当熔体不在翻腾后0.5h即可倒渣。倒渣时采用人工抱钳将坩埚抬起,抱钳用电动葫芦控制,人工掌握坩埚倾角,将渣倒出。倒渣分两次,第一次渣占总渣量的80%;第二次要慢,以免将金的熔体倒出。
⑦铸锭 清渣后,将金液倒入铸模内,铸成金锭。
⑧停炉 熔炼结束后,停止给炉体供电,但需要给炉体降温,因此,待循环水温降至30℃后,停止循环水的供应。
另外在转炉的基础上由南非公司进行改进后生产的卡尔多炉,较转炉而言,其生产效率高,生产成本低,而且具有更快的精炼速率和较低的金损失。由于工艺流程的其余部分均同于常规的转炉工艺,在此不对其工艺作进一步的说明和分绍。
3.2.2 氯化精炼法[4,5]
3.2.2.1 氯化法精炼金的基本原理
氯化精炼法是澳大利亚淘金者、英国人F.B.Miller于1867年提出的,1872年在澳大利亚悉尼造币厂首次用于生产,后来先后在南非兰德精炼厂和美国南达科他州得到应用。由于氯化精炼法具有流程短、速率快、对原料适应性强等优点,目前在产金大国南非、俄罗斯及加拿大等仍在使用。我国四川长城金银精炼厂(原成都印钞公司)1994年从澳大利亚引进该项技术应用于合质金的精炼。
氯化法的原理是基于各种元素氧化还原电势的差异,贱金属和银比金更容易被氯气所氯化,生成氯化物而与金分离。其实质是用氯气吹炼熔融的粗金,贱金属与银发生氯化反应生成氯化物,而金由于电势最高,其生成氯化物的自由焓变量为正值,难以生成氯化物。主要金属的氯化反应及其热力学自由焓变化,生成氯化物的熔点、沸点列于表3-2。从表3-2可见,生成氯化物的顺序首先是贱金属,其次是银,最后是金。
表3-2 主要金属的氯化反应及氯化物性质

氯化过程在感应电炉石墨坩埚内进行,经过熔炼的粗金锭装入500kg容量的坩埚中,再加入一定量的硼砂、石英砂及氯化钠混合熔剂。熔剂的作用是在熔化后的金属表面形成一薄渣层,减少金属的挥发,防止坩埚壁受侵蚀。金属熔化后,将预热过的陶瓷氯气喷管(或石英管、碳素管)经坩埚盖插入熔体中,通入氯气。为使氯气很好地分散,管端壁分布有小孔。氯化在1150~1200℃进行,氯化精炼时杂质反应的动力学曲线如图3-1所示。

图3-1 氯化精炼时杂质反应的动力学曲线
1—Fe;2—Zn;3—Pb;4—Cu;5—Ag粗金原料含量(%):Ag 9.0、Cu 1.4、Pb 0.35、Fe 0.18、Zn 0.06
可见在氯化过程的实际条件下,杂质转化为氯化物的顺序大体上与热力学计算的顺序相同:铁、锌、铅等最先反应,生成的氯化铁与氯化锌因沸点低转化为气相,氯化铅部分挥发,部分浮在金属表面。只有在大部分铁、锌、铅被氯化后,铜和银才开始与氯气反应,CuCl2与AgCl的沸点高于氯化过程的温度,在金的表面形成熔化的氯化物层。待浮渣与氯化物聚集到一定量时定期清除,并重新加入熔剂继续氯化,如此反复几次。根据氯气管上出现黄色金层和熔体上出现红烟,可判断氯化过程的终点,并取样分析,合格后用骨粉吸净液面上的浮渣,浇铸成金锭或阳极板送电解进一步精炼。氯化过程时间的长短主要取决于杂质含量的多少。如处理20kg含90%的粗金,作业时间为1h,而处理12kg含60%的粗金,则需2.5h。
氯化物夹带有一定量的金粒,回收的方法是在坩埚炉内分批加入苏打进行还原熔炼:
4AgCl+2Na2CO34Ag↓+4NaCl+2CO2↑+O2↑
氯化物中的AgCl约有20%被还原为金属银,并将氯化物中夹带的金粒大部分捕集沉入坩埚底部,经分离得到的金银合金返回氯化精炼,因此,可保证较高的金回收率。
脱金后的氯化物为提银的原料,其中含AgCl约70%,其余为铜、铅、钠的氯化物。将其水淬为细小颗粒,用氯酸钠加氯化钠的盐酸溶液进行浸出,除去铜、铅等杂质。得到的AgCl经锌粉或铁屑置换成银粉,洗净、烘干后铸成阳极板生产电解银粉。
氯化精炼时由于氯化物挥发,金银的损失不可避免,在回收的烟尘中含1%~2%的金、20%左右的银,可在银系统加以回收。
3.2.2.2 氯化法精炼金的生产过程
氯化精炼要在合金熔融状态下进行,需要有较高的温度,实践中采用的温度为1250℃。所用的加热设备一般为中频加热电炉或碳化硅棒电炉。使用内部为矾土、外衬为黏土和石墨制成的圆柱形坩埚,这种坩埚能够承受高温。采用中频电炉进行冶炼。炉子上部装有排风烟罩,烟尘从烟罩排出,经布袋除尘器收集,其装置见图3-2。

图3-2 氯化法精炼金的装置图
1—台秤;2—氯气瓶;3—流量计;4—陶瓷管;5—合质金熔融体;6—中频炉
熔化前,向坩埚内装入合金,并加入硼砂、二氧化硅和食盐组成的熔剂。加入的熔剂量为合金量的6%,其目的是吸收杂质和抑制贵金属的挥发。
当粗金全部熔化时,将陶瓷管插入熔体中,使其下端靠近坩埚底部,将管夹住定位,然后将橡胶软管接于陶瓷管上端,通入的氯气经过软橡胶管、陶瓷管直至熔体下部。为了使气体在熔融金属中均匀分配,在陶瓷管靠近底部钻有分布均匀的小孔。
氯气通入后,首先氯化的是铁,在操作温度下,以氯化物形态挥发,接着是锌和铅氯化,也以氯化物形态挥发。这期间,熔体产生激烈的搅动和沸腾,主要是氯化铁、氯化锌和氯化铅生成的气体冲出熔体,造成沸腾。为了避免熔体外溅,应减慢通入氯气的速率,只有当铁、锌、铅三种元素几乎全被除去后,铜和银才开始生成氯化物。后者生成的氯化物,以液体状态浮于熔体上部,进入浮渣。这时,液体金属不再发生搅动,即可适当增大氯气通入的速率。当熔融的粗金和氯化物充满坩埚时,将上部浮渣舀出,倒进另一坩埚,以提取铜、银和微量金。氯化物浮渣舀出以后,再重新加入熔剂,继续氯化,继续舀出,反复3~4次。当发现熔融金上部有红色的氯化金烟雾时,应立即减少氯气的通入量。精炼末期,除上部有红色的氯化金烟雾外,还发生激烈的湍流搅动,这时应用专门的取样坩埚穿过浮渣从熔融的金属中取出试样,送化验室分析化验。当测试金中含银量<0.35%时,认为金锭已经达到充分精炼,应停止通入氯气,否则,还需继续通入氯气精炼。
取样采用专用小型耐火耐酸坩埚(图3-3),坩埚底部钻有10mm的小孔,并用带操作把的黏土塞塞住。取样时,先将坩埚插入熔体,并用黏土塞堵住底部,当坩埚底部插至熔融金表面以下30mm时,将黏土塞上提,熔融金属即进入取样坩埚中,然后,又将黏土塞下放堵住底部的孔,再将坩埚提到外部,放出液体黄金,供化验分析。若分析合格,即停止通入氯气,撤掉管子,并舀出剩余的氯化物覆盖层。为了清除表面层氯化物,加入骨灰使氯化物集中,用勺撇去表面渣沫,液体金进行铸锭。其品位达到99.6%,可作为货币及首饰金用,若要求更高的纯度,则要求进行电解或用其他精炼方法提纯。

图3-3 取样坩埚断面图
A—耐火黏土坩埚;B—熔渣;C—氯化物;D—金水;E—清除熔渣后取样用金水;F—黏土塞
Denver矿山工程公司所采用的氯化精炼技术是将金锭放在一个固气相高温氯气反应器中在微负压条件下与氯气接触,当在特殊的工艺条件下操作时,氯气与银、锌、汞等合质金反应生成氯化物,而金以元素形式留下。在氯化约6h后,从反应器中除去剩余金物质,用盐酸洗涤,以分离氯化铜,随后用氨水洗涤,以分离氯化银,再用硝酸洗涤,以除去残余金属银。这时的金类似一块硬质海绵,金的纯度为99.9%~99.999%,然后熔铸成金锭。用电积法从洗液中分离出金属铜和银。目前,已有两家精炼厂使用该工艺。
3.2.2.3 氯化法精炼金的优缺点
氯化精炼法可处理经选矿的砂金、汞齐蒸发后的粗金、氰化厂的合质金,含金银总量应在80%以上。铜铅阳极泥经火法熔炼得到的金银合金,含金银总量一般大于97%,均可送氯化精炼。
氯化精炼工艺的优点如下:
a.投资和生产成本低,生产效率高,处理速度快,工作时间短。在等量物料的情况下,采用硝酸分银法精炼需72h,而采用氯化法仅需16h,时间缩短了56h,工作效率提高了77.78%。
b.操作相对简单,生产成本低。硝酸分银法金泥兑银熔炼后水淬,要经过四次硝酸除杂、四次过滤洗涤、两次浓硫酸处理,工序烦琐。而氯化法工艺简单,程序较少,劳动强度小,相比之下,其生产处理成本较低。
c.回收率高,损耗<0.1%。
d.高温氯化精炼工艺对含金的成分适应范围较宽。
e.系统内几乎没有金的积压。
氯化精炼工艺的缺点如下:
a.高温氯化法对于成分复杂的金泥,氯气的用量、时间、温度和通气速率等条件难以准确把握,冶炼产品质量难以稳定指标。氯化过程会有少量金挥发造成金的损失。对含金低的物料。应用该法很不经济。
b.产品纯度不高,虽可用于造币,但不能满足现代高技术的要求,尚需进一步电解精炼。
c.如原料中含有铂族元素,不便回收。
d.采用氯化法精炼,通入的氯气有部分过剩,通过烟罩排入大气,造成环境污染。但可以将排出的烟气经NaOH溶液吸收净化后外排,减小对环境的污染。
因此需根据实际情况权衡利弊,决定是否采用该方法。
3.2.3 温和氯化法
该法与Miller金精炼法有些相似,操作时先将首饰废料和粗金制成金属带,垂直悬挂在密闭的加热反应器内,在300~700℃的氯气流中进行氯化处理,使金属带中的合金元素被氯化除去。金属带的厚度一般为1.25~6mm,反应时间视粗金中金含量的多少而定,经氯化后,金残渣用盐酸、氨水和硝酸洗涤,用该法可得到纯度为99.95%~99.99%的金,但合金中铂不能够被除去。该法可处理金含量在30%~80%的粗金合金。