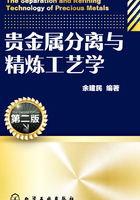
2 贵金属的分离方法
2.1 贵金属物料的溶解
在湿法冶金中,首先要将贵金属精矿或其他物料溶解,即用化学溶剂将其转变为可溶性物质,以便进行随后的分离与精炼。由于贵金属都具有很高的化学稳定性,它们几乎不溶于能腐蚀任何贱金属的介质,而贵金属矿物的抗腐蚀性与其相应金属相当,因此含有贵金属物料的溶解往往成为湿法冶金的难题。在精炼时,要求在溶解的同时,又要避免引入新的杂质的情况下更是如此。
在普通条件下,用单一酸、碱,甚至王水,都难使大多数贵金属溶解。这类难溶物质常用以下几种方法进行溶解。
固态物质溶解于溶液中,可分为两种情况:第一种为简单溶解过程,即物料中的可溶组分溶解于液体的过程,在过程中没有新的物质产生。第二种为化学溶解过程,即固态物质在溶液中发生化学反应生成新的物质后而溶于溶液中。贵金属物料的溶解属于化学溶解过程。
2.1.1 易溶物料的溶解
2.1.1.1 王水溶解法[1]
金不溶于任何单一的酸、碱或盐的水溶液。在有氧化剂存在的情况下,它可溶于HCl、NaCN(或KCN)及SC(NH2)2的溶液中生成配合物,金的最主要溶解溶剂为王水。
Au+4HCl+HNO3HAuCl4+2H2O+NO↑
生成的NO遇空气则变为棕色的NO2。
2Au+8HCl+NaClO32HAuCl4+3H2O+NaCl
2Au+3Cl2+2HCl2HAuCl4
2Au+3NaClO+8HCl2HAuCl4+3NaCl+3H2O
2Au+4NaCN+0.5O2+H2O2NaAu(CN)2+2NaOH
2Au+4SC(NH2)2+Fe2(SO4)3{Au[SC(NH2)2]2}2SO4+2FeSO4
银可溶于硝酸、浓硫酸溶液,在有氧气存在的条件下,亦能溶于氰化物溶液。银的主要溶解溶剂为硝酸。
Ag+2HNO3AgNO3+H2O+NO2↑ (浓硝酸)
3Ag+4HNO33AgNO3+2H2O+NO↑ (稀硝酸)
2Ag+2H2SO4Ag2SO4+2H2O+SO2↑ (浓硫酸)
2Ag+4NaCN+0.5O2+H2O2NaAg(CN)2+2NaOH
铂的溶解反应与金相似,但铂比金难溶解,故主要溶解溶剂为王水。
3Pt+18HCl+4HNO33H2PtCl6+8H2O+4NO↑
钯能溶于硝酸及王水中。
3Pd+8HNO33Pd(NO3)2+4H2O+2NO↑ (烯硝酸)
Pd+4HNO3Pd(NO3)2+2H2O+2NO2↑ (浓硝酸)
3Pd+12HCl+2HNO33H2PdCl4+4H2O+2NO↑
2.1.1.2 水溶液氯化法[2]
传统的王水溶解的方法除分离不完全的缺点外,还产生大量的NO、NO2等有害气体,污染环境,同时需反复蒸干破坏硝基化合物的烦琐操作。后来发展了HCl/Cl2、HCl/H2O2、HCl/NaClO3等溶解方法,而HCl/Cl2是目前从含贵金属的物料中提取贵金属的常用方法,也叫水溶液氯化法,实质上是加大氯气的供给量,提高溶液的氧化电势使贵金属溶解,其溶解能力和王水相当,主要是依靠氯气的氧化作用和新产生的次氯酸使物料溶解。我国早在1965年即开始用此法处理镍阳极泥焙烧浸出贱金属以后的残渣及贵金属精矿,以后又用于从铜阳极泥中提取金、钯、铂。目前国外贵金属精炼厂已普遍采用此法取代王水溶解工艺。浸出介质可用水、氯化钠溶液、稀硫酸、稀盐酸等,一般选用HCl/Cl2体系。贵金属的氯化溶解率主要取决于被氯化物料的预处理过程,一般金、钯、铂的氯化率都比较高,但经焙烧的物料铑、铱、锇、钌的氯化率比较低。此法在国内已得到工业应用,国外已用于废料溶解的工业生产。
(1)易溶物料的氯化溶解
硫化镍电解阳极泥经脱硫焙烧浸出贱金属以后,残渣成分仍很复杂。其中贵金属含量低(Au 1.64%、Pd 0.68%、Pt 1.47%),而贱金属含量仍较高(Ni 8.57%、Fe 20.02%、Cu 19.1%、S 7.37%),另外还含有19.1%SiO2。贱金属除铜主要呈硫化物外,镍、铁主要呈NiO及Fe2O3。
氯化过程中贵金属按下列反应氯化溶解:
Pt+2HCl+2Cl2H2PtCl6
Pd+2HCl+2Cl2H2PdCl6
2Au+2HCl+3Cl22HAuCl4
2Ag+Cl22AgCl
反应生成的AgCl在浓盐酸和碱金属氯化物溶液中由于生成[AgCl3]2-配合离子也部分进入溶液中。
贱金属硫化物及少量元素硫也被氯化:
Cu2S+4H2O+5Cl2CuSO4+CuCl2+8HCl
Cu2S+4FeCl32CuCl2+4FeCl2+S
S+4H2O+3Cl26HCl+H2SO4
上述物料在0.18mol/L H2SO4+25g/L NaCl、6mol/L HCl、1.5mol/L H2SO4+1.5mol/L HCl、6mol/L HCl+25g/L NaCl 4种介质中的氯化效果都很接近,在3mol/L HCl溶液中的氯化速率见图2-1。

图2-1 铂、钯、铜、镍、铁的氯化浸出速率a—50℃;b—80℃;c—96℃
由图2-1可知,在50℃以上氯化过程都能顺利进行。在96℃时氯化8h各金属的氯化效率(%)为:铂97.7、钯97.8、金99.5、铜98.8、铁84、镍86。氯化渣成分含量(%)为:铂0.092、钯0.041、金0.021、铜0.63、铁9.20、镍3.10等。生产实践表明,副铂族金属的氯化效率仅为20%左右,还有相当部分的锇、钌氧化、挥发损失。
(2)贵金属精矿的氯化溶解
在贵金属相互分离和精炼之前都需将精矿溶解,过去都用王水溶解的方法,但反应过程产生有害的氮氧化物及最后需反复加盐酸赶硝基,操作复杂,用HCl/Cl2溶解的效果与王水一样。
经焙烧的贵金属精矿(成分见表2-1)用6mol/L盐酸浆化按固液比1:4配料,加热到90~100℃通Cl2氯化8h(矿浆不再吸收氯气时可认为反应结束)。副铂族金属的氯化效率较低。新的专利方法是将残渣与过氧化钠混合,于600~620℃焙烧,用水浆化后与氯化液重新合并再次氯化可使99.5%以上的铂、钯、金和至少97%的副铂族金属进入氯化液,结果详见表2-1。碱溶处理可使钌转化为可溶性的钌酸盐,也可使铑、铱转变为易溶于酸的高价氧化物或改善它们的表面活性。
表2-1 贵金属精矿两段氯化的结果

目前中国金川集团公司贵金属实际生产中采用HCl/Cl2溶解贵金属的方法。脱胶液经铜粉置换金、钯、铂后的置换渣经洗涤后,氯化溶解在200L搪瓷釜、固液比为1:5、6mol/L HCl溶液体系中进行。过程中连续通入Cl2直到贵金属溶解完。残渣极少且呈灰白色,过滤所得氯化液用来分离金、钯、铂。
2.1.2 难溶物料的溶解
某些铂铑合金、铂铱合金或含铑、铱较高的物料是很难用王水、NaClO3+HCl、HCl+Cl2、HCl+H2O2等强氧化剂溶解的,必须采取一些强化措施。
贵金属合金是由两种或两种以上的元素组成。这些元素在合金中可能以共晶状态、固溶体状态或金属化合物状态存在。所谓固溶体即一种或几种组元像溶质一样,均匀地分布在另一组元(溶剂)之中,冷凝之后形成固态合金。所谓金属化合物即几种金属元素(也包括非金属元素)形成的化合物。所谓共晶即组成合金的组元相互机械地混合在一起,共同结晶出来的,但这些组元可以是元素,也可以是固溶体或化合物。因此合金的化学性质与组成它们的元素相比,有了很大的改变。比如说,金可以溶于王水,银可以溶于硝酸,但由50%金和50%银组成的合金既不溶于王水,也不溶于硝酸。王水或硝酸只能使它发生轻微腐蚀。因此某些贵金属合金的溶解不同于组成它们的组元,需要采取特殊措施才能使其溶解。
2.1.2.1 配银法[1]
金银合金,若金:银 >3:1,可用王水溶解,金转变为HAuCl4进入溶液,银转化为AgCl沉淀;若金含量少于3/4,难溶于王水。若银:金>3:1,此合金可用硝酸溶解,银转变为AgNO3进入溶液,金不溶解,以固体状态存在。如银含量小于3/4,用硝酸也不能完全溶解。
对于硝酸与王水都不能溶解的金银合金,可按银:金>3:1的原则配入适量银,熔融后慢慢地以细流状浇入不断搅拌的大量水中,使之粉碎成细粒,这一作业过程称之为水淬;或者浇铸成锭,冷凝后压成薄片,再用浓硝酸将银溶解,使之与金分离。
2.1.2.2 过氧化钠熔融法[2]
物料在镍(或铁)坩埚中用过氧化钠(或过氧化钡)、氢氧化钠(或碳酸钠)熔融或烧结,经浸出而转入溶液。此法为经典方法之一,是在强氧化剂存在下,将物料中的贵金属氧化的过程,用于处理铱、钌等,如在600~700℃下:
2Ir+6Na2O2+2NaOH2Na2IrO3+5Na2O+H2O+O2↑
2Ru+6Na2O2+2NaOH2Na2RuO4+5Na2O+H2O
此法操作条件恶劣,浸出产物难于过滤,一般需经多次反复操作才能使贵金属较完全地转入溶液,加之所使用的器皿会引入一定量杂质,给随后的处理带来困难,所以通常在不得已的情况下才使用。
2.1.2.3 硫酸氢钾熔融法[2]
物料用硫酸氢钾或焦硫酸钾在瓷坩埚中加热熔融,再经浸取而转入溶液,用于处理铑等。如向粉末钌中加入4mol/L NaOH溶液,加热煮沸,然后小心地逐次加入焦硫酸钾,蒸干熔融后,钌被氧化成暗红色可溶性的钌酸钾,浸出后转入溶液。
Ru+4NaOH+K2S2O8K2RuO4+2Na2SO3+2H2O
此法浸取率不高,需经多次反复操作,过程冗长,不能达到有效分离。
2.1.2.4 中温氯化法[2]
将物料与4~5倍的氯化钠混合后,于中温下置于石英管内的石英舟中,通入的氯气经硫酸和五氧化二磷洗涤、干燥后,送入加热的石英管中,在600~700℃下氯化8~12h,主要用于含钌、铑、铱物料的氯化溶解。如Rh:NaCl=1:3,混匀后置于石英舟中,送入管式炉,于500℃通入氯气1h,得黑红色易溶性的氯铑酸钠。
2Rh+6NaCl+3Cl22Na3RhCl6
此法处理小批量物料较为有效,因氯化装置较复杂、通氯气时间长、腐蚀性强、操作环境差、产物收集麻烦,处理大批量物料尚有一定困难。
2.1.2.5 封闭热压溶解法[3]
这是对难溶物料进行溶解较为有效而简便的一种方法。此法是将物料与溶剂同时置于封闭容器中,加热产生高压而使之溶解。常用的3种溶解装置:铂衬套封闭热压装置、玻璃封管及聚四氟乙烯封管,其中最后一装置在容器材料选择上较为合理。将物料装入热压分解容器中,加入HCl+HNO3(3:1)或HCl+H2O2(4:1)或HCl+NaClO3在140~300℃下反应7~24h,可溶解PtIr18、PtIr32、PtIr25、PtRh20、PtRh30、IrRh10等极难溶解的物料,20世纪60年代以来,国内外已相继用此法处理了一些矿物、岩石、氧化物及难溶铂族金属及其合金。
此法的特点是:
①适用于任何强酸、强碱及其混合溶剂,扩大了溶剂的选择范围,从而使可分解或溶解的物料变得更为广泛。
②可避免污染,不影响下一步操作。
③容器材料具有较高的化学稳定性及一定的机械强度,且耐腐蚀、耐高压,从而降低了试剂消耗,提高了溶解速率,装置还可反复使用。但仅适用于小批量物料。
根据物料和溶解装置的性质选定合适的溶解温度,如用聚四氟乙烯封管时温度必须低于250℃,否则聚四氟乙烯会分解。
2.1.2.6 电化溶解法[4]
此法是在一定的酸性介质中通入交流电使难溶贵金属物料溶解。交流电化溶解的速率与电流密度、物料表面积、电解质溶液浓度和溶液温度有关。即将能导电的金属及合金作为电极置入电解池中用直流电或交流电在90~100℃下电化溶解,能制得纯净的溶液,不引入其他盐类杂质。直流电化溶解法主要用于钌及其合金的溶解,交流电化溶解法主要用于铂、铑、铱、钯和钌等的溶解。使用的电解质随所欲溶解的物质不同而不同。例如,铂铑、铂铱、铑铱合金在HCl介质中,钌在6mol/L HCl介质中,铑铱粉在H2SO4介质中等。
20世纪50年代末以来,前苏联进行了这方面的研究工作,其目的是为了获得分析上便于测定的纯溶液,因处理量较小,在实际工作中其应用有一定的局限性。此法的最大优点是不易引入新的杂质且能直接处理铱、铑等片、粉状物料,虽在设备上还存在一些困难,但还是一个有效而又有发展前途的方法。此法目前在我国已有应用。但此法只能用于金属或合金的溶解,溶解时需一个试样用一个电解池,样品多时电解装置庞大,并且溶解的金属还得通过称量电解前后的电极重量之差来计算。
2.1.2.7 碎化法[5]
对于含铑30%以上的铂铑合金,含铱20%以上的铂铱合金,欲使其溶解必须先将其碎化。所谓碎化,即向合金中另外加入一种易溶于酸的金属,例如,铝、银、铋、锌或铅等,加入金属的质量为原合金的3~7倍(见表2-2),高温熔融成合金,浇成薄片,再用适当的酸将所加入的金属溶解掉,原来的合金转变为高活性的贵金属粉末,称为碎化。碎化后的粉末,可用HCl+Cl2、HCl+H2O2或王水溶解。铂可全部溶解,铑或铱可部分溶解或全部溶解。铑和铱本不溶于王水,但由于以下几种因素起作用,使其部分或全部溶解。
表2-2 碎化剂及其操作条件[9]

①颗粒非常细微。当颗粒尺寸小到一定程度后,金属的化学性质会有某种程度的变化。
②铑和铱与加入的金属形成固溶体或化合物时这些固溶体或化合物的化学性质发生了变化,因而可溶解于王水中。
几种常用碎化剂中银的密度最大,铋其次,铝最小;铋的熔点最低,锌其次,铜最高;锌的沸点最低。锡碎化时,铑铱的溶解率低并且锡易水解,后处理麻烦。铋能与铑生成Bi4Rh、Bi2Rh、BiRh等化合物,而不和铱反应(<1400℃),且酸溶时易水解,难于除尽。铜的熔点较高,活性低,碎化后尚需吹炼将铜氧化为氧化铜或用稀HNO3溶解铜,铜不易除尽,不利于后续工序贵金属的分离。Mn-Cu25合金已用于含铱废料或残渣的碎化,还原熔炼形成的多相固溶体用稀盐酸溶解后可获得颗粒很细的(100目)铱粉。银或银废料(Ag>90%)常用于含金、钯、铂合金的碎化,所熔炼出的合金轧制成薄片或直接用硝酸或硫酸溶解银后,再用王水等氧化剂溶解金、钯、铂等。由于银亦属于贵金属,价值高,加入的银必须回收。银碎化法对含铑、铱的物料效果较差。锌的沸点低,易挥发,且获得的贵金属粉末粗,一般不单独使用,而使用Al-Zn合金复合碎化剂如铝10%~90%、锌10%~90%或铝10%~80%、锌10%~80%、铜10%~30%等,利用该法已处理过PtIr25、PtRh40、IrRh40、锇铱矿。
2.1.2.8 铝热合金化法[6]
这是南非国立冶金研究所(NIM)于20世纪80年代末研究的方法,其过程分为3个步骤:首先,贵金属精矿与金属铝、铁高温熔炼,贵金属转变为金属状态并与铝、铁合金化;其次,用酸溶解铝、铁等贱金属,使贵金属转变为高分散的易溶活性状态;最后,用盐酸-氯气溶解获得高浓度贵金属溶液。针对不同品位及成分的精矿用不同的熔炼方法和操作条件。
①高品位贵金属精矿的活化溶解 传统工艺的“贵铅”是经硝酸溶解铅、银后产出的,以副铂族金属为主的残渣,成分含量(%)为:Pt 5.5、Pd 3.8、Au 0.8、Rh 9.8、Ru 17.1、Ir 2.9、Os 1.9、Ag 1.4,贵金属含量合计大于40%,还含有铜、铁、镍和铅,合计约为35%。该残渣用王水直接溶解或高温氢还原后用王水溶解等不同方法处理时,贵金属的溶解效率都不高。但经铝熔活化后全部贵金属的溶解率都很高。
该方法的操作过程为:精矿与等质量的铝在>1000℃的惰性气氛中直接熔炼为铝合金,用4mol/L HCl溶解贱金属,过滤贱金属溶液后得到的残渣再用王水或盐酸-氯气氧化溶解贵金属。用该方法和其他方法处理贵金属精矿时,贵金属的溶解率比较列入表2-3。
表2-3 高品位贵金属精矿用不同预处理方法的溶解率

该方法因铝的强还原性和铁的有效捕集作用,能保证锇的有效回收,虽然一次不溶渣中铑、铱、钌的含量也可能高于1%,但闭路返回铝熔炼活化过程,不会造成分散损失。
②中等和低品位贵金属精矿的活化溶解 中等品位精矿含贵金属和贱金属各约30%,如高锍加压浸出产出的粗精矿,用2mol/L HCl溶液通入氯气直接加热溶解或高温氢还原后用盐酸-氯气氧化溶解或铝熔活化-酸溶贱金属-盐酸+氯气溶解等3种不同方法处理时,贵金属的溶解率列于表2-4。含贵金属约15%、氧化亚铁14%、二氧化硅16%及其他贱金属含量也较高的低品位精矿,用上述3种不同方法处理时,贵金属的溶解率也列入表2-4。
表2-4 不同方法预处理中、低品位精矿的贵金属溶解率

低品位精矿的铝熔活化过程是:熔炼使氧化亚铁和二氧化硅形成硅酸盐炉渣分离,即将精矿和炭粉、石灰混合制粒,800℃还原焙烧,焙砂和铁屑在电炉中1600℃熔炼为铁合金,分离炉渣后的铁合金按铝:贵金属=0.4:1向熔体中加入铝屑活化产出含贵金属的铝铁合金。由于产出的炉渣量大,其中夹带分散的贵金属含量达2%~3%。合金中贱金属含量可达90%,需消耗大量盐酸或硫酸溶解贱金属。过滤贱金属溶液后的贵金属精矿再用盐酸-氯气溶解。为确认该方法回收贵金属的可靠性,单独处理一批精矿的金属平衡情况列于表2-5。
表2-5 单独处理一批精矿的金属平衡

③富铑铱钌残渣的活化溶解 传统精炼工艺中的富铑铱钌残渣用不同的方法处理时,铑钌铱3种金属的溶解情况列于表2-6。
表2-6 不同方法处理富铑铱钌物料的溶解率

④粗金属铑的活化溶解 粗金属铑直接用王水溶解很困难,90℃王水溶解近半月,溶解率低于60%。若按铑:铝:氧化铁=1:2:0.2比例混合后置于高温炉中升温至1000℃熔炼15min,合金用6mol/L HCl溶液溶解铝、铁,过滤后的铑精矿用王水在90℃溶解20min,铑的溶解率高于99%。
总之,铝热合金化法可使所有惰性难溶状态的贵金属都转化为活性易溶状态,该方法可靠且溶解率很高。但该方法处理低品位精矿用加入氧化铁还原为金属铁作捕集剂,因为铁的熔点高,需要特殊的高温熔炼设备,为防止铁被氧化有时还需惰性气体保护气氛,应用条件较为苛刻。
2.1.2.9 镍锍熔炼-铝热活化溶解技术[6]
该技术兼有富集和活化的效果,可使不同品位和状态的含贵金属的物料富集、活化,产出高品位活性贵金属精矿和溶解获得高质量、高浓度的贵金属溶液。
①低品位贵金属物料的富集活化溶解 低品位贵金属物料的成分含量(%)为:Au 0.113、Pt 0.094、Pd 0.076、Rh+Ir+Os+Ru 0.033、金+铂族金属0.316、Cu 4.7、Ni 4.1、Fe 10.2、SiO211.1、CaO 12.5、S 14.1。
低品位贵金属物料富集活化溶解的方法是在物料中加入硼砂、碳酸钠、石英砂等造渣熔剂,在电弧炉中于1200℃熔炼,物料中的贱金属硫化物熔炼成为捕集了贵金属的锍,在分离炉渣后得到的锍中加入铝反应形成铝的合金,用酸溶解合金中的贱金属,残渣即为活性贵金属精矿,再用盐酸-氯气溶解残渣,所有贵金属溶解率均高于99.8%。
②中等品位贵金属物料的富集活化溶解 对含金+铂族金属为7.748%、贱金属为19.1%的贵金属物料,用同样的方法处理,贵金属的溶解率均高于99.9%。溶液中贵金属的浓度为100g/L。
③合金废料和精炼残渣的活化溶解 对常规方法无法溶解的Pt-Ir25合金废料,用镍锍熔炼→加铝自热活化→盐酸溶解分离贱金属→盐酸-氯气溶解,铂、铱的溶解率均高于99%,产出高浓度铂铱溶液。用此法处理某贵金属二次资源精炼厂长期积累的成分非常复杂的各种贵金属废渣,也取得了令人满意的效果。
④锇铱矿的活化溶解 对砂铂矿提铂后残余的锇铱矿(含锇、铱各约30%),用镍锍熔炼后铝热活化或直接铝热熔炼活化,皆可使惰性锇铱矿分解,熔块用硫酸或盐酸溶解贱金属后,贵金属精矿可在硫酸介质中加氧化剂直接蒸馏后用碱液吸收四氧化锇,蒸馏残液补加盐酸后用氯气溶解铂、铱,溶解率高且可获得高浓度铱溶液。
⑤金川集团公司精炼厂稀贵生产系统将该法用于“铜渣”、“铜渣”处理后的残渣和现生产过程中的一次、二次蒸残渣及地沟回收料(统称贵金属杂料)中贵金属的回收,取得了很好的效果。目前采用该工艺试生产已处理低品位物料20t左右,并产出了纯度为99.99%的贵金属产品。整个工艺过程稳定,取得了很好的效果。炉渣中金、钯、铂含量<40g/t。从投料到产出贵金属产品,金、钯、铂的回收率分别为90.30%、90.50%、91.47%。
该方法的特点如下所述:
a.可处理含贵金属品位<1%、粗金属的各种复杂物料,包括冶炼厂各种品位的贵金属富集物和粗精矿,精炼厂各种难处理废渣,各种贵金属合金和不同的贵金属二次资源。当物料中贵金属品位低,同时含镍或铁的硫化物及硅、钙的氧化物时,可配入适量熔剂直接熔炼,分离炉渣后直接加入铝完成自热还原活化。
b.处理含贵金属废渣、难溶粗金属铑、铱、锇、铱精矿或贵金属合金(如铂铱合金)废料时,首先配入低熔点镍锍(Ni3S2,熔点约为575℃)或铁锍(FeS,熔点约为1000℃)熔炼,熔炼温度低,无须保护气氛,Ni3S2和FeS对粉状贵金属的浸润好、捕集效率高,对块状合金物料的进入碎化能力强。
c.铝热还原反应速率快,在800~1000℃熔铝中加入贵金属锍,瞬时自热达白炽高温完成活化反应,获得含贵金属的多元合金。
d.多元合金用硫酸或盐酸直接溶解贱金属,过滤后即得到高品位活性贵金属精矿。
e.可用贵金属精炼过程中产生的各种含微量贵金属的酸性废液溶解贱金属,既充分利用了残酸又可使微量贵金属置换回收到精矿中,有利于精炼过程中的溶液、残酸和贵金属闭路平衡。例如,酸度为2mol/L HCl的废液成分含量(g/L)为:Ru 0.006、Rh 0.005、Ir 0.0013、Pd 0.00074,在60℃浸出多元合金6h,过滤后的贱金属废液中贵金属的总浓度<0.00001g/L,置换回收率>99.99%。
f.物料中若含锇、钌,在富集熔炼-铝热活化-酸溶贱金属的过程中,可全部有效地捕集回收在活性精矿中,很容易从精矿中用氧化蒸馏方法分离(即在稀盐酸介质中加入双氧水或氯酸钠等氧化剂氧化蒸馏,分别用碱液和盐酸吸收)。蒸馏完后补加浓盐酸并通入氯气加热溶解,获得的贵金属溶液浓度高,是简单的盐酸体系,酸度和金属浓度、贵金属价态和配合物状态易于按要求调整,可方便地衔接溶剂萃取分离工艺。
g.操作过程简单灵活,设备易解决,周期短。
但该法也存在一定的缺点,即当用该法处理铂铱合金、铑铱合金、铂-钯-铑三元催化网王水不溶渣、铂-钯-铑三元催化网炉灰或品位过低的贵金属物料(如低于1000g/t)等废料时,镍锍中的铜在盐酸或硫酸溶解贱金属的过程中不会溶解,在溶解贵金属的过程中这部分铜会随之进入贵金属溶液中,给随后的贵金属分离、提纯带来麻烦。
2.1.3 贵金属物料溶解动力学[1]
溶解过程是由溶液与固体物质组成的多相反应过程,该过程与气固相的多相反应相似,大致可分为如下几个步骤:①溶剂分子向固体表面的扩散;②溶剂分子被吸附在固体表面上;③溶剂与固体中可溶性组分发生化学作用生成可溶性的化合物;④所生成的可溶性化合物在固体表面解吸;⑤可溶性化合物向溶液中扩散。
由于化学反应系在固相表面进行,因而使得固相与液相界面附近的溶剂浓度、反应产物浓度与溶液内部不同。对于溶剂来说固液相界面处,由于反应溶剂不断消耗,该处浓度最低,甚至可能达到零。如果没有新的溶剂扩散进来,反应就不能继续进行;对于反应产物来说,在固液相界面处,浓度不断增加,当达到饱和时,溶解作用将会停止,欲使溶解过程继续进行,就应该使反应产物不断向外扩散。
溶解速率主要决定于溶解过程中速率最慢的步骤。上述五个步骤大致可分为扩散过程与化学反应过程两个过程。一般来说扩散过程进行得很慢,因此它就是决定性因素,换句话说它将成为限制步骤。影响溶解速率最主要的因素是:被溶解物质的性质与状态、溶剂浓度、反应产物从饱和层中向外扩散的速率、过程进行的温度、搅拌条件等。
关于上述因素与溶解速率的关系可用下式表示:
式中 V——在单位时间内发生反应的物质数量,即溶解速率;
D——扩散系数;
F——固体物料的表面积;
δ——固体物料表面饱和溶液层(或称扩散层)的厚度;
cH——固体物料表面饱和溶液层中产物的浓度,即饱和浓度;
cP——整个溶液中产物的浓度。
若溶解过程中有气体产物产生,将会使过程变得更加复杂。气体离开固体并从溶液中冒出,可起到扰乱扩散层和搅拌整个溶液的作用,可加速溶解过程;但是如果产生的气体迟迟不能聚结成大气泡自溶液中冒出,而附在固体表面,它会使固体物质的该部分与溶剂隔离,因而会阻碍溶解过程的进行。然而,在多数情况下,气体的产生会加速溶解过程的进行。
(1)固体物料的性质及其状态
固体物料的性质对溶解过程有重大的影响。对于纯金属而言,化学性质较活泼,即电极电势较负的金属容易溶解。电势较低的金属如果与电势较高的金属组成合金,一般而言可使其溶解速率变慢;反之,电势较高的金属与电势较低的金属组成合金,可使其变得容易溶解。但是也有相反的情况,如金的电势比银高,金中加入较多银后,反而不易溶于王水。所以说,对于纯金属的化学性质可按其标准电势加以判断,而对于合金来说情况就变得比较复杂,不能简单地根据组成合金的元素的标准电势武断地下结论,需要根据前人的经验或通过试验来了解它们的溶解行为。但是,不管纯金属、合金或者化合物,它们在相应溶剂中的溶解行为主要决定于它们与溶剂之间的化学反应。
同一金属物料,它的状态对溶解过程也有非常重大的影响。固体物料的表面积与溶剂接触面积越大越容易溶解,从公式中亦可见,溶解速率V与表面积F成正比。因薄片状、细丝状、粉状及海绵状的固体物料有较大的表面积,因此溶解速率较快。
(2)固体表面饱和溶液的扩散
溶解开始时,固体表面很快便形成饱和溶液层或称扩散层。溶解产物(即溶质)能由扩散层中扩散至整个溶液中,使得溶解过程能继续进行。根据溶解速率公式可知,溶解速率V与(cH-cP)和D成正比,与δ成反比。溶质的饱和浓度和溶质在整个溶液中的浓度之差越大,溶质越易扩散,所以在溶解的开始阶段整个溶液中溶质浓度等于零或者很低时,溶解速率很快,随着整个溶液中溶质浓度的增加,溶解速率变慢,当cP=cH,即cH-cP=0时,扩散即不能进行,因而溶解将停止。
扩散系数D与溶质微粒的大小、溶剂的性质及温度等性质有关。不同的物质在相同条件下可有不同的扩散系数。扩散系数越大,溶解进行得越快。
扩散层的厚度δ是溶解过程的主要阻力,搅拌可以使扩散层厚度变薄,因而可以加速溶解过程的进行。若溶解反应有气体产物产生时,亦能使扩散层遭到破坏,可以加速反应的进行。
(3)温度对溶解速率的影响
在给定溶液中扩散系数D会随着溶液温度的改变而改变。扩散系数D与某些因素的关系表示如下式:
式中 D——扩散系数,cm2/s;
T——热力学温度,K;
μ——溶剂黏度,g/(m·s);
d——扩散物质颗粒大小(分子直径),cm;
R——气体常数[8.31J/(K·mol)];
N——阿伏加德罗常数。
从公式可知,扩散系数D正比于过程进行的热力学温度。当溶液温度提高时,溶质颗粒的运动速率增大,扩散系数也变大,从而溶解速率提高。
提高温度还能改变溶质的溶解度,在多数情况下提高溶液的饱和浓度cH,使cH与cP差值增大,有利于扩散的进行。
升高温度还能促进分子的活化,加速化学反应速率。
温度的变动还影响扩散层厚度δ值,升高温度可使δ值变小。
升高温度还会使溶液黏度降低,从扩散系数D的公式可知,黏度μ减小,扩散系数D增大。
总之,升高温度有利于溶解过程进行,可以加快溶解速率。但温度的提高受到溶剂的沸点及各种经济因素及环保的限制,并非可以无限提高。从另一方面说,如果溶解过程属于放热反应过程,并有气体产生时,尚需控制温度;否则,溶解反应过快会使溶液外溢,造成贵金属损失。
(4)溶剂浓度的影响
溶剂浓度对于溶解过程的影响极大。提高溶剂浓度不仅会增大化学反应速率,而且能提高溶剂向固体表面扩散的速率。这是因为在紧靠固体表面处,由于化学反应使溶剂不断消耗,该处溶剂浓度变得很低,但由于整个溶液中溶剂的浓度很高,两者差值增大,有利于溶剂向固体表面扩散。提高溶剂浓度可加速溶解过程是很明显的。但是必须考虑到以下几点:①溶剂浓度太高会使溶解反应过程进行过于激烈,易使溶液外溢;②溶剂浓度过高会使不该溶解的物质也发生溶解,不仅浪费试剂,而且会使某些杂质进入溶液的量增加。
(5)液固比的影响
在溶解过程中,溶液的质量与固体物质质量之比称为液固比。若液固比太小,即液体量太少,会使溶液很快接近饱和浓度,不利于溶解过程进行。当使用的试剂为一定量时,若液固比太大,即溶液量太多,会相应使溶剂浓度降低,也不利于溶解过程的进行。液固比的值一般是通过试验来确定的。