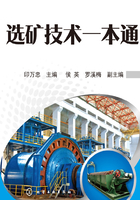
四、破碎筛分工艺
126.破碎段的基本形式有哪些?
破碎段是破碎流程的最基本单元。破碎段数的不同以及破碎机和筛子的组合不同,便有不同的碎矿流程。破碎段是由筛分作业及筛上产物所进入的破碎作业所组成。个别的破碎段可以不包括筛分作业或同时包括两种筛分作业。
破碎段的基本形式如下:如图2-42所示,(a)为单一破碎作业的破碎段;(b)为带有预先筛分作业的破碎段;(c)为带有检查筛分作业的破碎段;(d)和(e)均为带有预先筛分和检查筛分作业的破碎段,其区别仅在于前者是预先筛分和检查筛分在不同的筛子上进行,后者是在同一筛子上进行,所以(e)可看成是(d)的改变。因此破碎段实际上只有4种形式。

图2-42 破碎段的基本形式
两段以上的破碎流程是不同破碎段的形式的各种组合,故有许多可能的方案。合理的破碎流程可以根据需要的破碎段数以及应用预先筛分和检查筛分的必要性等加以确定。
127.怎样确定破碎段数?
需要的破碎段数取决于原矿的最大粒度,要求的最终破碎产物粒度以及各破碎段所能达到的破碎比,即取决于要求的总破碎比及各段破碎比。
例如,当原矿粒度为1300~300mm及给入磨矿机(即最终破碎产品)粒度为25~10mm时,破碎流程的总破碎比为:
式中 i——破碎作业的总破碎比;
D最大,d最大——原矿和破碎产物中的最大粒度,mm。
对照表2-35所列出的每段破碎比数值,便可知,即使最小的破碎比12,用一段破碎也难以完成,而最大破碎比130(总破碎比等于各段破碎比的连乘积,总破碎比5×5×6=150>130)用三段破碎就可完成。故球磨作业前的破碎段通常采用两段或三段破碎。当原矿粒度小于300mm时,可取两段。其他情况下所需的破碎段数可依此类推。
表2-35 各种破碎机在不同工作条件下的破碎比范围

128.如何确定预先筛分和检查筛分?
预先筛分是在矿石进入破碎之前预先筛出合格的粒级,可以减少进入破碎机的矿量,提高破碎机的生产能力;同时可以防止富矿产生过粉碎。在处理含水分较高和粉矿较多的矿石时,潮湿的矿粉会堵塞破碎饥的破碎腔,并显著降低破碎机的生产能力。利用预先筛分除掉湿而细的矿粉,可为破碎机创造良好的工作条件。
因此,预先筛分的应用主要根据矿石中细粒级(小于该段破碎机排矿口宽度的粒级)的含量来决定。细粒级含量愈高,采用预先筛分愈有利。研究证明,技术上和经济上应预先筛分有利的矿石,其中细粒级的极限含量与破碎机的破碎比有关,其关系如表2-36所示。
表2-36 采用预先筛分有利的细粒组含量极限值与破碎比的关系

当原矿粒度特性为直线时,在各种破碎比的条件下.其中细粒级的含量均超过了上述极限值(即有利于采用预先筛分的极限含量)。
当原矿粒度特性为直线时,不管破碎比为多大,采用预先筛分总是有利的。多数情况下,原矿的粒度特性呈凹形,故破碎前采用预先筛分在经济上都是合算的。但由于采用预先筛分需要增加厂房的高度,当粗碎破碎机和中碎破碎机的产品粒度特性曲线大都是凹形,也就是说细粒占多数,故第Ⅱ破碎段和第Ⅲ破碎段采用预先筛分也是必要的。只有当选择的中碎机生产能力有富余时,才可考虑中碎前不用预先筛分。
检查筛分的目的是为了控制破碎产品的粒度,并利于充分发挥破碎机的生产能力。因为各种破碎机的破碎产物中都存在一部分大于排矿口宽度的粗粒级,如短头圆锥破碎机在破碎中等可碎性矿石时,产物中大于排矿口宽度的粒级含量达60%,最大粒度为排矿口的2.2~2.7倍。
在破碎难碎性矿石时则更甚。各种破碎机破碎产物中粗粒级(大于排矿口尺寸)含量β和最大相对粒度Z(即最大颗粒与排矿口尺寸之比)如表2-37所示。
表2-37 各种破碎机产物中的含量和最大相对粒度

采用检查筛分后,使不合格的粒级返回破碎机,就如同磨矿机与分级机构成闭路循环有利于提高磨矿效率一样,检查筛分可以改善破碎机生产能力。但检查筛分的采用,会使投资增加,并使破碎车间的设备配置复杂化,故一般只在最末一个破碎段采用检查筛分,而且与预先筛分合并构成预先检查筛分闭路循环。
由此得出两点结论:(1)预先筛分在各破碎段均是必要的;检查筛分一般只在最末一个破碎段采用。(2)破碎段数通常为2~3段。
129.如何确定洗矿作业是否必要?
在处理含泥量较多的氧化矿或其他含泥含水较多的矿石时,容易堵塞破碎筛分设备、矿仓、溜槽、漏斗,使破碎机生产能力显著下降,甚至影响正常生产,此时破碎流程必须考虑设置洗矿设施。一般认为原矿含水量大于5%、含泥大于5%~8%,就应该考虑洗矿,以开路破碎为宜。
对某些矿石(如黑钨矿等)为了便于手选、光电选矿或重介质选矿,也需要设置洗矿作业。有些矿石(如沉积铁锰矿床)在破碎过程中经过洗矿、脱泥,使有用矿物富集而获得合格产品。
130.常用的破碎流程有哪些?
(1)两段破碎流程 两段破碎流程有两段开路和两段一闭路两种形式,如图2-43所示。

图2-43 两段破碎流程
(a)两段开路流程;(b)两段一闭路流程
采用两段破碎流程的多是小型选矿厂,因为从采矿来的原矿粒度较小之故,也有的由于有工艺的特殊要求而采用两段破碎流程。
(2)三段破碎流程 三段碎矿流程的基本形式有:三段开路和三段一闭路两种,如图2-44所示。

图2-44 三段破碎流程
(a)三段开路流程;(b)三段一闭路流程
三段一闭路碎矿流程,作为磨矿的准备作业,获得了较广泛的应用。一般来说,不论是井下开采还是露天开采的矿石,只要含泥较少,不堵破碎机和筛孔都能有效适应,采用三段闭路碎矿流程。大量工业实践证明,破碎产品粒度可以控制在12~0mm,能给磨矿作业提供较为理想的给料。因此,规模不同的选矿厂都可以采用。随着选矿技术的发展,出现了能量前移的趋势,因为破碎效率高及磨矿效率低,故多碎少磨成了碎磨领域的技术趋势,即应加强破碎,降低破碎最终粒度。
(3)带洗矿作业的破碎流程 当原矿含泥(-3mm)量超过5%~10%和含水量大于5%~8%时,细粒级就会黏结或结团,恶化破碎过程的生产条件,如造成破碎机的破碎腔和筛分机的筛孔堵塞,发生设备事故,储运设备出现堵和漏的现象,严重时使生产无法进行。此时,应在破碎流程中增加洗矿设施。增加洗矿设施,不但能充分发挥设备潜力,使生产正常进行。改善劳动强度,而且能提高有用金属的回收率,扩大资源的利用。
洗矿作业一般设在粗碎前后,视原矿粒度、含水量及洗矿设备的结构等因素而定。常用的洗矿设备有洗矿筛(格筛、振动筛、圆筒筛)、槽式洗矿机、圆筒洗矿机等。洗矿后的净矿,有的需要进行破碎,有的可以作为合格粒级。洗出的泥,若品位接近尾矿品位,则可废弃;若品位接近原矿品位,则需进行选别。
由于原矿性质的不同,洗矿的方式和细泥的处理等不同,因而流程多样,现列举一例。原矿为硅卡片型铜矿床,含泥6%~11%,含水8%左右,其洗矿流程如图2-45所示,破碎流程为三段一闭路。为使破碎机能安全、正常生产,第一次洗矿在格筛上进行,筛上产物进行粗碎,筛下产物进入振动筛再洗。第二次洗矿后的筛上产物进入中碎,筛下产物进螺旋分级机分级、脱泥,分级返砂均与最终破碎产物合并,分级溢流经浓密机缓冲、脱水后,进行单独的细泥磨矿、浮选。

图2-45 带洗矿作业的破碎流程