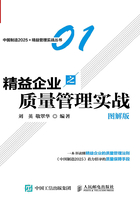
五、智能制造
智能制造以智能加工与装配为核心,同时覆盖面向智能加工与装配的设计、服务及管理等多个环节。智能工厂中的全部活动可以从产品设计、生产制造及供应链三个维度来描述。在这些维度中,如果所有活动均能在网络空间中得到充分的数据支持、过程优化与验证,同时在物理系统中能够实时地得以执行并与网络空间进行深度交互,这样的工厂可称为智能工厂。
1.智能工厂的基本特征
与传统的数字化工厂、自动化工厂相比,智能工厂具备以下几个突出特征。
(1)制造系统的集成化
作为一个高端的智能制造系统,智能工厂表现出了鲜明的系统工程属性。具有自循环特性的各技术环节与单元按照功能需求组成不同规模、不同层级的系统,系统内所有元素均是互相关联的。在智能工厂中,制造系统的集成主要体现在两个方面,具体内容如图6所示。

图6 制造系统集成的主要体现
(2)决策过程的智能化
传统的人机交互中,作为决策主体的人有支配“机器”的行为,而智能制造中的“机器”因拥有扩展人类智能的能力,使人与“机器”共同组成决策主体,在同一信息物理系统中实施交互。信息的种类以及交流的方法更加丰富,从而使人机交互与融合达到前所未有的深度。
制造业自动化的本质是人类在设备加工动作执行之前,将制造指令、逻辑判断准则等预先转换为设备可识别的代码,并将其输入制造设备中。此时,制造设备可根据代码自动执行制造动作,从而节省了此前在制造机械化过程中人类的劳动。在这个过程中,人是决策过程的唯一主体,制造设备仅仅是根据输入的指令自动地执行制造过程,而并不具备如判断、思维等高级智能化的行为能力。在智能工厂中,“机器”具有不同程度的感知、分析与决策能力,它们与人共同构成决策主体。在“机器”的决策过程中,人向制造设备输入决策规则,“机器”基于这些规则与制造数据自动执行决策过程,这样可将由人为因素造成的决策失误降至最低。与此同时,在决策过程中形成的知识可作为后续决策的原始依据,使决策知识库得到不断优化与拓展,进而不断提升智能制造系统的智能化水平。
(3)加工过程的自动化
车间与生产线中的智能加工单元是工厂中产品制造的最终落脚点,智能决策过程中形成的加工指令将全部在加工单元中实现。为了能够准确、高效地执行制造指令,企业必须确保智能制造单元数字化、自动化、柔性化。
首先,智能加工单元中的加工设备、检验设备、装夹设备、储运设备等都是基于单一数字化模型驱动的,这就避免了传统加工中由于数据源不一致而带来的大量问题。
其次,智能制造车间中的各种设备、物料等,大量采用如条码、二维码、RFID等识别技术,使车间中的任何实体均具有唯一的身份标识,在物料装夹、储运等过程中通过对这种身份的识别与匹配,实现了物料、加工设备、刀具、工装等的自动装夹与传输。
最后,智能制造设备中大量引入智能传感技术,通过在制造设备中嵌入各类智能传感器,实时采集加工过程中机床的温度、振动、噪声、应力等制造数据,并采用大数据分析技术来实时控制设备的运行参数,使设备在加工过程中始终处于最佳效能状态,实现设备的自适应加工。例如,传统制造车间中往往存在由于地基沉降而造成的机床加工精度损失,通过在机床底脚上引入位置与应力传感器即可检测到不同时段地基的沉降程度,据此通过对机床底脚的调整即可弥补该精度损失。此外,通过对设备运行数据的采集与分析,还可总结在长期运行过程中设备加工精度的衰减规律、设备运行性能的演变规律等;通过对设备运行过程中各因素间的耦合关系进行分析,可提前判断设备运行的异常,并实现对设备健康状态的监控与故障预警。
(4)服务过程的主动化
制造企业通过应用信息技术、网络技术,根据用户的地理位置、产品运行状态等信息,为用户提供产品在线支持、实时维护、健康监测等智能化服务。这种服务与传统的被动服务不同,它能够通过对用户特征的分析辨识出用户的显性及隐性需求,主动为用户推送高价值的信息与服务。此外,面向服务的制造将成为未来工厂建设中的一种趋势,集成广域服务资源的行业务联网将越来越智能化、专业化,企业对用户的服务将在很大程度上通过若干联盟企业间的并行协同来实现。对用户而言,其所体验到的服务高效性与安全性也随之提升,这也是智能工厂服务过程的基本特点。智能工厂中的主动化服务体系如图7所示。

图7 智能工厂中的主动化服务体系
2.智能工厂的框架体系
智能工厂由物理系统中的实体工厂和网络空间中的虚拟数字工厂构成。其中,实体工厂部署有大量的车间、生产线、加工装备等,为制造过程提供硬件基础设施与制造资源,也是实际制造流程的最终载体;虚拟数字工厂则是在这些制造资源以及制造流程的数字化模型的基础上,在实体工厂的生产之前,对整个制造流程进行全面的建模与验证。为了实现实体工厂与虚拟数字工厂之间的通信与融合,实体工厂的各制造单元还配备有大量的智能元器件,用于制造过程中的工况感知与制造数据采集。在虚拟制造过程中,智能决策与管理系统对制造过程进行不断迭代优化,使制造流程达到最优;在实际制造中,智能决策与管理系统则对制造过程进行实时的监控与调整,进而使制造过程体现出自适应、自优化等智能化特征。
由此可知,智能工厂的基本框架体系包括智能决策与管理系统、企业数字化制造平台、智能制造车间等关键组成部分,如图8所示。

图8 智能工厂基本框架
(1)智能决策与管理系统
智能决策与管理系统如图9所示,是智能工厂的管控核心,负责市场分析、经营计划、物料采购、产品制造以及订单交付等各环节的管理与决策。通过该系统,企业决策者能够掌握企业自身的生产能力、生产资源,调整产品的生产流程与工艺方法,并能够根据市场、客户需求等动态信息作出快速、智能的经营决策。

图9 智能决策与管理系统
一般而言,智能决策与管理系统包含企业资源计划(ERP)、产品全生命周期管理(PLM)、供应链管理(SCM)等一系列生产管理工具。在智能工厂中,这些系统工具的最突出特点在于:一方面向工厂管理者提供更加全面的生产数据以及更加有效的决策工具,相较于传统工厂,在解决企业产能、提升产品质量、降低生产成本等方面能够发挥更加显著的作用;另一方面,这些系统工具已达到了不同程度的智能化水平,在辅助工厂管理者进行决策的过程中能够切实提升企业生产的灵活性,进而满足不同用户的差异化需求。
(2)企业数字化制造平台
企业数字化制造平台需要解决的问题是如何在信息空间中对企业的经营决策、生产计划、制造过程等全部运行流程进行建模与仿真,并对企业的决策与制造活动的执行进行监控与优化。其中的关键因素包括以下两点。
①制造资源和流程的建模与仿真
企业数字化制造平台在建模过程中需要着重考虑智能制造资源的三个要素,即实体、属性和环境。实体可通俗地理解为智能工厂中的具体对象。属性是在仿真过程中实体所具备的各项有效特性。智能工厂中各实体之间的相互作用会改变实体的属性,这种变化通常可用状态的概念来描述。智能制造资源通常会受外界变化的影响,这种对系统活动结果产生影响的外界因素可理解为制造资源所处的环境。企业数字化制造平台在对智能制造资源进行建模与仿真时需要考虑其所处的环境,并明确制造资源与其所处环境之间的边界。
②建立数字化平台与制造资源之间的关联
通过对制造现场实时数据的采集与传输,制造现场可向数字化平台实时反馈生产状况,其中主要包括生产线和设备的运行状态、在制品的生产状态、质量状态以及物料的供应状态等。在智能制造模式下,数据的形式、种类、维度、精细程度等将是多元化的,数据的采集、存储与反馈也需要与其相适应。
在智能制造模式下,产品的设计、加工及装配等环节与传统的制造模式均存在明显的差异。因此,企业数字化制造平台必须适应这些变化,从而满足智能制造的应用需求。
A.智能制造的产品设计
在智能制造的产品设计方面,企业数字化制造平台应提供两方面的功能:第一,能够将用户对产品的需求以及研发人员对产品的构想建成虚拟的产品模型,优化产品的功能,在产品正式生产之前,通过仿真分析保证产品的功能以满足需求,从而减少研制后期的技术风险;第二,能够支持建立满足智能加工与装配标准规范的产品全三维数字化定义,使产品信息不仅能被制造工程师理解,还能够被各种智能化系统接收并无任何歧义地被理解,从而能够完成各类工艺、工装的智能设计和调整。
B.智能加工与装配
在智能加工与装配方面,传统制造中人、设备、加工资源等之间的信息交换并没有统一的标准。而数据交换的种类与方式通常是针对特定情况而专门定制的,这就导致了制造过程中会出现大量的耦合,从而使系统的灵活性受到极大的影响。例如,在数控程序编制过程中,工艺人员通常将加工程序指定到特定的机床中,由于不同机床所使用的数控系统不同,数控程序无法直接移植到其他机床中使用。如当前机床上被指定的零件过多,容易出现被加工零件需要等待而其他机床处于空闲状态的情况。
随着制造系统智能化程度的不断提升,智能加工与装配中的数据将基于统一的模型,而不再针对特定系统或特定设备。这些数据可被制造系统中的所有主体识别,并能够通过自身的数据处理能力从中解析出具体的制造信息。例如,智能数控加工设备可能不再接收数控程序代码,而是直接接收具有加工信息的三维模型,根据模型中定义的加工需求自动生成最优化的加工程序。这样的优势在于:一方面,加工工艺数据具有通用性,因而工艺人员不再需要指定特定机床;另一方面,在机床内部生成的加工程序是最适合当前设备加工代码的,进而实现真正的自适应加工。
(3)智能制造车间
智能制造车间及生产线是产品制造的物理空间,其中的智能制造单元及制造装备提供实际的加工能力。各智能制造单元之间的协作与管控由智能管控及驱动系统实现。智能制造车间的基本构成如图10所示。

图10 智能制造车间的基本构成
①车间中央管控系统
车间中央管控系统是智能加工与装配的核心环节,主要负责制造过程的智能调度、制造指令的智能生成与按需配送等任务。在制造过程的智能调度方面,车间中央管控系统需根据车间生产任务综合分析车间内设备、工装、毛料等制造资源,按照工艺类型及生产计划等将生产任务实时分派到不同的生产线或制造单元,使制造过程中设备的利用率达到最高。在制造指令的智能生成与按需分配方面,面向车间内的生产线及生产设备根据生产任务自动生成并优化相应的加工指令、检测指令、物料传送指令等,然后根据具体需求将其推送至加工设备、检测装备、物流系统等不同设备中。
②智能生产线管控系统
智能生产线管控系统可实时存储、提取、分析与处理各类数据,包括工艺、工装等制造数据,设备运行参数、运行状态等过程数据,同时,该系统能够通过对数据的分析实时调整设备运行参数、监测设备健康状态等,并据此进行故障诊断、维护报警等行为;对于生产线内难以自动处理的情况,智能生产线管控系统还可将其向上传递至车间中央管控系统。此外,生产线内不同的制造单元具有协同关系,系统可根据不同的生产需求对工装、毛料、刀具、加工方案等进行实时优化与重组,优化配置生产线内各生产资源。
③智能制造装备
从逻辑构成的角度看,智能制造装备由智能决策单元、总线接口、制造执行单元、数据存储单元、数据接口、人机交互接口以及其他辅助单元构成。其中,智能决策单元是智能设备的核心,负责设备运行过程中的流程控制、运行参数计算以及设备检测维护等;总线接口负责接收车间总线中传输来的作业指令与数据,同时负责设备运行数据向车间总线的传送;制造执行单元由制造信息感知系统、制造指令执行系统以及制造质量测量系统等构成;数据存储单元用于存储制造过程数据以及制造过程决策数据;数据接口分布于智能设备的各个组成模块之间,用于封装、传送制造指令与数据;人机交互接口是人与智能设备之间传递、交换信息的媒介和对话接口;辅助单元主要是指刀具库、一体化管控终端等。
④仓储物流系统
智能制造车间中的仓储物流系统主要涉及AGV/RGV系统、码垛机以及立体仓库等。
AGV/RGV系统主要包括地面控制系统及车载控制系统。其中,地面控制系统与车间中央管控系统实现集成,主要负责任务分配、车辆管理、交通管理及通信管理等,车载控制系统负责AGV/RGV单机的导航、导引、路径选择、车辆驱动及装卸操作等。
码垛机控制系统是码垛机研制中的关键,主要通过模块化、层次化的控制软件来实现码垛机运动位置、姿态和轨迹、操作顺序及动作时间的控制,以及码垛机的故障诊断与安全维护等。
立体化仓库由仓库建筑体、货架、托盘系统、码垛机、托盘输送机系统、仓储管理与调度系统等组成。其中,仓储管理与调度系统是立体仓库的关键,主要负责仓储优化调度、物料出入库、库存管理等。