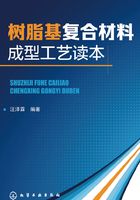
第1章 预浸料制备
1.1 短切纤维预浸料制备
短切纤维预浸料制备主要有预混法、预浸法、层铺法、悬浮浸渍法和造粒等方法。
1.1.1 预混法
预混法是先将增强纤维短切,与一定量的树脂混合均匀,再撕松后烘干或用挤出机挤成条状或丸状(BMC)的工艺方法。
1.1.1.1 主要设备
(1)纤维切割器 常用切割器类型有冲床式、砂轮片式、三辊式和单旋转刀辊式,其工作原理如图1-1所示。冲床式切割器广泛应用于切割非连续纤维(如开刀丝);砂轮片式切割器用于宝塔纱团的整体切割,其工效较高,但所切割的纤维长度不均匀,而且砂轮片容易损坏;三辊式切割器所切割的纤维长短均一,可以连续工作,用于切割连续纤维效果良好,更换切割辊刀片间距可调变切割纤维长度;单旋转刀辊式切割器多用在高硅氧纤维的切割。

图1-1 各种纤维切割器结构
(2)高速分散机 为了使树脂糊分散均匀,需要使用剪切速率很高的搅拌机。高速分散机是对两种或者多种液体和固体粉末状物料进行搅拌、溶解和分散的高效设备。其主要技术参数见表1-1。
表1-1 高速分散机的主要技术参数

(3)捏合机 捏合机的作用是将树脂与纤维混合均匀,其结构主要有可翻转出料的捏合锅、双Z桨式捏合桨和动力传动装置等(如图1-2所示)。

图1-2 捏合机结构示意图
1—电动机;2—减速箱;3—齿轮;4—捏合锅;5—夹套;6—捏合翼
①翻缸形式:手动翻缸、机械翻缸和液压翻缸;
②加热形式:夹套加热、半管加热、远红外加热和电加热;
③捏合方式:相切型和相交型;
④出料方式:底阀式、翻板式、蛟龙式(横式)、旋门式、抽拉式、吸料式和蛟龙式(纵式);
⑤搅拌轴形式:Σ型搅拌桨、Z型搅拌桨、切割型搅拌桨和鱼尾型搅拌桨。
表1-2列出了南通密炼捏合机械有限公司标准型捏合机系列。
表1-2 标准型捏合机系列技术参数

注:1.转速可根据用户要求定做。
2.下出料有球阀出料、快开门出料和螺杆出料。
(4)撕松机 撕松机的作用是将捏合成团的物料进行蓬松。主要由进料辊和一对撕料辊组成。通过两个不同直径的撕料辊按相同方向旋转。物料在两个撕料辊间受撕扯而松散(如图1-3所示)。

图1-3 撕松机结构示意图
1—电动机;2—机体;3—配重;4—进料辊;5,6—撕料辊;7—机罩
(5)挤出机 国外使用的挤出机是黏土型挤出机,具有一根直径很粗的螺杆。螺杆通常都要经过抛光和镀铬处理,以便清洁和延长使用寿命。表1-3列出了几种Bonnot公司黏土型BMC挤出机的基本参数。
表1-3 几种Bonnot公司黏土型BMC挤出机的基本参数

1.1.1.2 预混模塑料制备
(1)原材料
①增强材料 短切纤维预浸料中常用的增强材料主要有玻璃纤维开刀丝、无捻粗纱、高硅氧纤维、碳纤维、芳纶纤维和尼龙纤维等。纤维长度一般为15~50mm,其中以30~50mm为多。
②基体树脂
a.酚醛树脂模塑料的典型配方 酚醛树脂模塑料的典型配方见表1-4。
表1-4 酚醛树脂模塑料的典型配方 单位:质量份

①KH-550加入树脂中充分搅拌后待用。
②先将油溶黑溶于乙醇,再倒入树脂中。
③用乙醇调节树脂的密度为1.0g/cm3。
b.环氧树脂胶液配制 环氧树脂加热到130℃,加入NA酸酐充分搅拌,当温度回升到120℃时滴加二甲基苯胺,并在120~130℃下反应6min后倒入丙酮,充分搅拌,冷却后待用。环氧树脂模塑料的典型配方见表1-5。
表1-5 环氧树脂模塑料的典型配方

c.三聚氰胺树脂胶液及其组成 三聚氰胺树脂模塑料的典型配方见表1-6。
表1-6 三聚氰胺树脂模塑料的典型配方

(2)制备方法 预混模塑料制备是将树脂胶液经胶液配制釜配制并搅拌均匀后,由齿轮输送泵送入自动计量槽内,计量后再送入捏合器。连续玻璃纤维用切割机将纤维切成15~50mm长的短纤维,然后进行蓬松,使纤维分散,再逐渐送入捏合器,与树脂胶液在捏合器内混合均匀,达到规定捏合时间后,倾斜捏合器出料。捏合时间越长,纤维强度损失越大;时间过短,树脂与纤维混合不均匀。再用撕松机将其蓬松后,铺放于钢丝网上,在80℃左右烘干后,包装入袋,即为模塑料。
例如短切玻璃纤维增强镁酚醛树脂,其连续生产工艺流程如图1-4所示。

图1-4 镁酚醛型短切玻璃纤维模压料连续生产工艺流程
1—冲床式切丝机;2—蓬松机;3—胶液釜;4—齿轮输送泵;5—自动计量系统;6—捏合机;7—排风器;8—风丝分离器;9—移动式风罩;10—撕松机;11—履带式烘干炉;12—皮带运输机;13—旋转式出料器;14—装料桶
①将玻璃纤维切成30~50mm长的短切纤维。
②用乙醇调整树脂黏度,控制胶液相对密度在1.0左右。
③按纤维∶树脂=55∶45(质量比),将树脂溶液和短切纤维加入捏合器中充分捏合,注意控制捏合时间。时间过短,树脂与纤维混合不均匀;时间过长,纤维强度损失太大。捏合时,树脂黏度的控制也是很重要的,树脂黏度控制不当,树脂不易浸透纤维,也会增加纤维的损伤,影响纤维的强度。
④捏合后,预混料逐渐加入撕松机中撕松。
⑤将撕松后的预混料均匀铺放在网屏上。
⑥预混料经晾置后在80℃烘房中烘20~30min。
⑦将烘干的预混料在塑料袋中封闭待用。
1.1.1.3 BMC
(1)增强材料 巨石集团有限公司生产的BMC用无碱玻璃纤维短切原丝的品种有562E、552B、558和588等。玻璃纤维长度有3mm、6mm、9mm、12mm、18mm和24mm。
(2)BMC基体树脂及助剂 BMC是在不饱和聚酯树脂中加入增稠剂、低收缩添加剂、填料、脱模剂、着色剂等组分,经混合形成树脂糊,将这种树脂糊与短切玻璃纤维在捏合设备中进行捏合混炼,使其充分混合而成。BMC用不饱和聚酯树脂与SMC用不饱和聚酯树脂是相同的,也就是说,可以用作SMC的不饱和聚酯树脂,同样也可以用作BMC的基体树脂,具体树脂的牌号见1.1.3节。天和有BMC专用树脂,其牌号为DS801N、DS802N、DS822N、DS823N和DS825N等。
BMC与SMC的组成极为相似,是一种改良了的预混块状成型材料,可用于模压、注射和传递等成型工艺。两者的区别仅在于材料形态和制作方法上。BMC中纤维含量较低(15%~20%),纤维长度较短(6~12mm),填料含量较大,因而BMC的强度较SMC低。BMC适用于制造小型制品,SMC则用于生产大型薄壁制品。BMC参考配方见表1-7。
表1-7 BMC参考配方 单位:质量份

①聚苯乙烯溶液指40%的聚苯乙烯、苯乙烯溶液。即聚苯乙烯∶苯乙烯=40∶60。
低密度聚乙烯粉末用于BMC,对BMC的收缩率和光泽度有所改善(见表1-8)。
表1-8 UF-20SS对BMC性能的改善

注射模塑工艺用模塑料的配方范围见表1-9。
表1-9 注射模塑工艺用模塑料的配方范围

(3)BMC(DMC)模塑料的配制
①先将称量好的树脂、引发剂、着色剂、脱模剂、部分填料等逐个加入到高剪切型的搅拌机中搅拌至均匀,然后再缓慢加入剩余的填料混合搅拌均匀,最后加入增稠剂搅拌3~4min,使各组分均匀分布在树脂中制得树脂糊。
②把制得的树脂糊加入到捏合机内,在搅拌下逐渐加入纤维,捏合6~7min,使纤维全部浸透,直至无白色纤维时即可出料,分摊放置,待稠化后包装。
③为了使团状模塑料更加致密,并便于以后的成型操作,可用挤出机挤成条状或丸状,熟化后用聚酯薄膜密封包装,储存备用。
BMC可以采用模压、注射或压注(传递模塑)等成型工艺制成复合材料制品。
1.1.2 预浸法
1.1.2.1 原材料
(1)增强材料 一般都采用连续无捻粗纱。
(2)树脂胶液配方 按配方先将环氧树脂和酚醛树脂进行混合,再将MoS2溶于丙酮,然后倒入树脂中充分搅拌后,使树脂胶液的相对密度在1.00~1.025的范围内。树脂胶液配方见表1-10。
表1-10 树脂胶液配方

1.1.2.2 预浸法模塑料制备
预浸法模塑料是将玻璃纤维束从纱架导出,经集束环进入胶槽,进行常温浸渍,在100~160℃烘箱中烘干,纤维牵引速度为1~1.5m/min,用切割机切割成定长的预浸料。
例如玻璃纤维增强环氧酚醛(6∶4)树脂。
①纤维从纱架导出,经集束环进入胶槽浸胶。
②环氧酚醛(6∶4)胶液相对密度控制在1.00~1.03。
③纤维牵引速度为1.20~1.35m/min。
④纤维经浸胶后通过刮胶辊进入第1、第2级烘箱烘干,第1级温度为110~120℃,第2级则为150~160℃。
⑤经烘干的预浸料由牵引辊引出。
⑥引出的预浸料进入切割机,切成所需长度。
在预浸料制备中主要控制的参数有树脂溶液相对密度、烘箱各级温度及牵引速度等。
1.1.3 层铺法(SMC)
1.1.3.1 原材料
(1)增强材料 部分生产厂家SMC用无碱玻璃纤维合股无捻粗纱(适用于增强不饱和聚酯树脂、乙烯基树脂)的品种:巨石集团有限公司的产品牌号有440、442C、410、456、458A、448和440A等,其线密度规格有2400tex、4392tex、4400tex、4500tex和4800tex等。淄博中材庞贝捷金晶玻纤有限公司的产品牌号有5545、5530、5509、5524、PF7009和PF7024等,其线密度规格为4436tex和4430tex,单丝公称直径为16μm。
(2)基体树脂
①不饱和聚酯树脂 SMC用不饱和聚酯树脂作为一类树脂,产品的用途不同,对树脂的要求也不尽相同。但与通用型树脂相比,SMC树脂还是具有自己的特点。
②乙烯基酯树脂 普通乙烯基酯树脂由于分子中不含羧基,所以用氧化镁作为增稠剂时没有不饱和聚酯树脂具有的那种增稠特性。用酸酐对乙烯基酯树脂进行改性,可使树脂的分子带有羧基,从而使树脂具有增稠特性,以满足模压料的应用需要。常用的酸酐有顺丁烯二酸酐和邻苯二甲酸酐。上纬(上海)精细化工有限公司有SW976和SW978等,华东理工大学华昌聚合物有限公司SMC用商品乙烯基酯树脂有MFE751。
③环氧树脂
④SMC用酚醛树脂(PF-SMC) SMC用酚醛树脂有江门市昆益树脂材料科技有限公司生产的KT-7207和KT-7209以及常熟东南塑料有限公司生产的NR9440等。
(3)填料 填料是用来降低模压制品的生产成本或改善某些物理性能(如表面硬度、固化放热效应等)和化学性能(如耐化学试剂腐蚀性等)的固体物质。在配方中,由于各原材料本身的黏度不同,以不同的比例加以混合,所得到的树脂糊黏度也各不一样。其次是同一种填料,填料的粒度和吸油值的不同,对黏度的影响也较大。粒度和吸油值是一对矛盾,相对来说,粒度越小,吸油值就越大;反之则相反。不同吸油值的填料对树脂糊的黏度也有很大影响。所以在选择填料时,除了要考虑制品本身的功能特性外,还要根据工艺的要求合理选择一定粒度的填料。
用作不饱和聚酯树脂SMC的填料,一般采用重质碳酸钙的粉体,其特点是:颗粒形状不规则,是多分散粉体;粒径分布较宽;粒径大,平均粒径一般为5~10μm。
氢氧化铝的粒径越小,比表面积就越大,阻燃效果也越好。阻燃用的氢氧化铝粉多经过表面处理,且多与其他阻燃剂复配使用,因为单一的氢氧化铝的阻燃性较差,达到一定阻燃级别所需的用量太大,从而会降低被阻燃材料的力学性能及其他有关性能。
氢氧化铝对不饱和聚酯树脂燃烧性能的影响:在不饱和聚酯树脂(PC-H-1097邻苯型)中添加不同量的氢氧化铝,其浇铸体的燃烧性能见表1-11。
表1-11 氢氧化铝含量对不饱和聚酯树脂浇铸体燃烧性能的影响

氢氧化铝加入量对树脂糊黏度的影响见图1-5。

图1-5 氢氧化铝加入量对树脂糊黏度的影响曲线
另外硫酸钡、高岭土、滑石粉等也可用作SMC的填料。
(4)增稠剂 不饱和聚酯树脂固化没有B阶段,要用作SMC的基体必须添加增稠剂。增稠剂是指在一定条件下,能够与树脂产生物理交联作用,使树脂的表观黏度迅速增加的物质。增稠是制备SMC的关键技术之一。
可用作增稠剂的材料很多,有无机增稠剂,也有有机增稠剂。
①无机增稠剂 活性轻质氧化镁用作不饱和聚酯树脂的增稠剂,用量一般为树脂质量的0.3%~3%。氧化镁的制备方法不同,增稠活性往往差异很大,氧化镁的活性对树脂糊的增稠速率的影响(增稠剂用量同为树脂质量的3%)见表1-12。
表1-12 不同活性值的氧化镁增稠树脂的黏度随时间的变化值 单位:Pa·s

表1-12中数据表明:活性高的活性氧化镁(碘吸附值为45.8mg/g)黏度达到7000Pa·s需要8h,而活性低的轻质氧化镁(碘吸附值为31.15mg/g),则需要21h才能使树脂黏度达到1300Pa·s,仅为前者的1/5。
增稠剂的增稠速率不仅可以通过控制增稠剂的加入量来调节,还可通过选用不同品种的增稠剂或混合增稠剂来调节和控制,以达到SMC所需的黏度(见表1-13)。
表1-13 增稠剂对不饱和聚酯树脂黏度的影响(不饱和聚酯由顺酐∶苯酐∶丙二醇=1∶1∶2组成,占70%,苯乙烯占30%)

表1-13中,轻质MgO和CaO的用量分别为不饱和聚酯树脂的1.8%和2.5%,该配方增稠显著,特点是起始黏度低,抑制起始黏度增长的时间长,后期增稠快,是较理想的增稠体系,已获得广泛应用。
另外氢氧化镁、氧化钙、氢氧化钙等也可用作树脂的增稠剂。
②有机增稠剂 主要有结晶不饱和聚酯树脂、甲苯二异氰酸酯(TDI)和聚合MDI等。
结晶不饱和聚酯树脂的增稠是一种物理增稠过程。结晶不饱和聚酯树脂的熔点一般为55℃左右,在这个温度以上时,结晶不饱和聚酯树脂熔化为液体,从而均匀地分散于整个SMC体系内以达到降低树脂黏度和浸渍增强材料的目的。当冷却至室温,结晶不饱和聚酯树脂又恢复至固态相,从而使SMC达到“机械增稠”而不粘手的目的。整个增稠过程需要使预混料保持在55℃以上。采用结晶不饱和聚酯树脂增稠剂的SMC配方见表1-14。
表1-14 采用结晶不饱和聚酯树脂增稠剂的SMC配方

(5)引发剂 SMC的固化还是要依赖于引发剂的作用,主要应用的引发剂有过氧化苯甲酸叔丁酯(TBPB)、过氧化苯甲酰(BPO)、过氧化二异丙基苯、异丙基苯过氧化氢、1,1-双(过氧化叔丁基)-3,3,5-三甲基环己烷、2,5-二甲基-2,5-二(叔丁基过氧)己烷(AD)、2,5-二甲基-2,5-双(过氧化苯甲酰)己烷、2,5-双(2-乙基己酰过氧化)2,5-二甲基己烷等。
(6)稀释剂 树脂黏度较大时给成型加工带来困难,而稀释剂的主要作用是降低基体树脂的黏度,使基体树脂具有良好的润湿和浸透纤维的能力。酚醛树脂常用乙醇为稀释剂,不饱和聚酯树脂的常用稀释剂为苯乙烯,前者为非活性稀释剂,不参与树脂固化反应,后者是活性稀释剂,参与树脂固化反应。
(7)阻聚剂 常用的阻聚剂有对叔丁基邻苯二酚、2-叔丁基对苯二酚及2,6-二叔丁基对甲酚等。
(8)低收缩剂 低收缩添加剂/低轮廓添加剂是SMC/BMC生产过程中一种非常重要的关键原材料。普通不饱和聚酯树脂固化时体积收缩率达7%~10%。对SMC来说,加入热塑性树脂可以改善预浸料的工艺性,减少缩孔,避免预浸料压制过程中产生树脂堆积和制品开裂,从而达到降低收缩率的目的。适当选用低收缩添加剂可使树脂压制过程中收缩量降至接近于0。常用的低收缩剂有低密度聚乙烯粉、聚苯乙烯、聚醋酸乙烯酯和饱和聚酯等。
(9)润湿分散剂 润湿与分散是两种不同的作用,但有时往往是由同一种物质所完成,有润湿作用的物质往往也具有分散作用,故有时也统称润湿分散剂。
加入填料会使树脂糊的黏度升高。BYK的润湿分散剂能使填料的加入方便快捷并降低树脂糊的黏度。其结果是高填料填充量成为可能。低黏度的树脂糊可加快对玻璃纤维的浸润性,如PS或SBS与UP树脂不相容会造成树脂糊中的相分离。使用BYK的助剂,既可提高两相的相容性,又能在储存和加工时稳定树脂糊。润湿分散过程为:①润湿,②分散,③稳定。
1.1.3.2 SMC(片状模塑料)成型
不饱和聚酯树脂SMC是增稠剂、引发剂、交联剂、低收缩添加剂、填料、内脱模剂和着色剂等混合成树脂糊浸渍玻璃纤维短切原丝(原丝长度约25mm,含量约30%),并在两面用聚乙烯或聚丙烯薄膜包覆起来形成的片状模压成型材料。使用时,只需将两面的薄膜撕去,按制品的尺寸裁切、叠层,放入模具中加温加压,即得所需制品。
酚醛SMC是在制造聚酯SMC的设备中制备的,制备工艺与聚酯SMC相似,且与聚酯SMC不相互作用。酚醛SMC制造后要在室温下存放4d,以达到一定的稠度,不需要进行特殊熟化处理。同聚酯SMC一样,酚醛SMC也需要两层聚乙烯薄膜保护,而且在SMC料熟化后保护膜能够容易地剥去。
SMC的工艺参数:幅宽0.45~1.5m;厚度1.3~6.4mm;纤维含量25%~35%;纤维长度12~50mm;纤维取向任意;聚乙烯薄膜厚度0.05mm;单重2~6kg/m2,一般为3~4kg/m2;树脂糊浸渍黏度10~50Pa·s;树脂糊涂覆量3~12kg/min。
(1)胶液配方
①不饱和聚酯树脂 用作SMC的基体树脂主要是不饱和聚酯树脂,不饱和聚酯树脂SMC的配方主要由三部分组成:一是不饱和聚酯树脂胶液,除含有不饱和聚酯树脂之外,还有增稠剂、引发剂、低收缩剂、内脱模剂、色浆,有的配方中还添加阻聚剂;另外就是填料和增强纤维。三者之间大约各占1/3。不饱和聚酯树脂几种典型的SMC配方见表1-15。
表1-15 不饱和聚酯树脂几种典型的SMC配方 单位:质量份

①聚苯乙烯溶液指40%的聚苯乙烯、苯乙烯溶液,即聚苯乙烯∶苯乙烯=40∶60,黏度为10200mPa·s。
在树脂中加入异氰酸酯增稠剂,可以得到互穿聚合物网络(IPN)使树脂增稠,见表1-16。
表1-16 IPN不饱和聚酯树脂型SMC配方

②乙烯基酯树脂 乙烯基酯树脂糊配方见表1-17,图1-6为生产车间实测树脂糊增稠曲线。
表1-17 乙烯基酯树脂糊配方


图1-6 生产车间实测树脂糊增稠曲线
③乙烯基酯树脂与不饱和聚酯树脂同时使用 乙烯基酯树脂SMC压制的产品与不饱和聚酯树脂SMC压制的产品相比较,力学性能提高了,但是表面质量较差,要提高其产品的外观质量必须使用一些助剂,因此而提高了成本。现将乙烯基酯树脂和不饱和聚酯树脂混合使用,当提高不饱和聚酯树脂含量,制品表面质量提高,但是制品力学性能有所下降,调节两种树脂的比例,使其既能满足制品的外观要求,也能满足制品的性能要求。以乙烯基酯树脂∶不饱和聚酯树脂=40∶40为例,其树脂糊配方见表1-18,图1-7为生产车间实测1 ⋕ 配方树脂糊增稠曲线。2 ⋕ 配方添加1质量份的BYK-P9065,SMC模压件的表观质量有所改善,脱模方便,若配方中添加4质量份的BYK-P9065,就不需要再添加脱模剂,不仅可以脱模,而且模压件外观更加光亮。图1-8为生产车间实测2 ⋕ 配方树脂糊增稠曲线。
表1-18 乙烯基酯树脂∶不饱和聚酯树脂=40∶40树脂糊配方 单位:质量份


图1-7 生产车间实测1 ⋕ 配方树脂糊增稠曲线

图1-8 生产车间实测2 ⋕ 配方树脂糊增稠曲线
按BMC组成,无捻粗纱切断的长度为20mm及添加的纤维量符合BMC的要求,在SMC机组上制得短纤维SMC。用此方法制得的短纤维SMC,由于纤维与树脂糊铺放均匀,压制成的制品表观质量比采用捏合器搅拌方法制得的BMC好。若BMC需要量不是太大,在同一台机组上生产,可节省另外设备的投资,而且该方法连续运行,降低了劳动强度,减少了操作人员。短纤维SMC树脂糊的配方见表1-19,图1-9为生产车间实测3 ⋕ 配方树脂糊增稠曲线,图1-10为生产车间实测4 ⋕ 配方树脂糊增稠曲线,图1-11为生产车间实测5 ⋕ 配方树脂糊增稠曲线。
表1-19 短纤维SMC树脂糊的配方 单位:质量份


图1-9 生产车间实测3 ⋕ 配方树脂糊增稠曲线

图1-10 生产车间实测4 ⋕ 配方树脂糊增稠曲线

图1-11 生产车间实测5 ⋕ 配方树脂糊增稠曲线
④环氧树脂胶液组成及配比
a.二异氰酸酯化合物对环氧树脂有增稠的效果,随着增稠剂用量的增加、异氰酸酯预聚体分子量的提高、环境温度的上升、固体环氧树脂加入量的增加,环氧树脂增稠的速度加快。用TDI增稠环氧树脂具有较好的热流动性;随闭模速度和环氧SMC黏度增加,片材流动所需变形功增加,所需模压压力增大。
b. MgO和α-甲基丙烯酸配合可增稠环氧树脂,随着MgO加入量的增加,环氧树脂增稠的速度加快;MgO与α-甲基丙烯酸配比为3∶1时,增稠环氧树脂的效果较好;推测环氧树脂的增稠机理是α-甲基丙烯酸中的端羧基与氧化镁反应,放出热量促使其端羧基与环氧树脂中的仲羟基反应,上述反应生成水产生的氢键和羰基与氧化镁中的金属原子形成络合物,共同导致环氧树脂的黏度增加。
⑤酚醛树脂 对于PF-SMC这种半成品,既要具有足够大的黏度以保持硬度,又要在高温高压下具有可变性和柔软性,还要在储存中保持稳定,也就是说,不能导致流淌树脂,不能由于自聚的变化而产生硬化。氢氧化钙和氧化镁对酚醛SMC的增稠作用:UP-SMC的增稠一般用氧化镁作增稠剂,其增稠分为两个阶段,即氧化镁与不饱和聚酯中的羧基基团成盐和配位反应生成配位络合物。酚醛SMC的增稠是一个更复杂的问题,其增稠机理尚无详细文献报道。
实验中所用酚醛树脂含有3%的羧基基团,远比不饱和聚酯的羧基含量低,虽然氧化镁和氢氧化钙能与酚醛树脂中的羧基基团成盐和配位反应形成配位络化物,但只能达到部分增稠。而其余部分的增稠来自酚醛树脂的羟基与钙的络合以及与填料表面的羟基形成的氢键。这样最终形成一个大的准交联网络结构,从而达到整体增稠。
作者用KT-7209酚醛做了增稠试验,KT-7209酚醛树脂黏度为4000mPa·s(可能是放置时间较长,黏度偏大),在300g树脂中加入39g氧化镁增稠剂,手工搅拌均匀,其混合物黏度变化见表1-20。
表1-20 酚醛树脂增稠数据

酚醛片状模塑料配方见表1-21。
表1-21 酚醛SMC配方 单位:质量份

注:1 ⋕ 配方增稠时间:40℃/72h。
(2)树脂糊的制备及上糊操作 树脂糊的制备一般有如下三种方法。
①批混合法 批混合法是将计量后树脂、低收缩剂、固化剂、颜料、脱模剂、填料等加入反应釜中搅拌均匀,最后加入增稠剂搅拌10min,黏度一般控制在30~50Pa·s。要求增稠剂加入30min后黏度低于最大允许值。用批混合法制成的树脂糊的储存寿命受增稠黏度限制,时间过长树脂开始快速增稠,影响对玻璃纤维的浸渍。但设备造价低,适于小批量生产。
②批混合/连续混合法 该工艺的特点是用两个混料釜系统混合:一个釜里装不饱和聚酯树脂、低收缩添加剂、引发剂、脱模剂和填料;另一个釜里装载体树脂、着色剂、增稠剂。生产时,用计量泵通过混合器进行混合。
③连续混合法 连续混合法是将树脂糊分成两部分单独制备,然后通过计量装置进入静态混合器。混合均匀后连续喂入到SMC成型机的上糊区。在双组分配制中,A组分含有树脂、引发剂和填料。B组分含有惰性聚酯或其他载体、增稠剂和少量作悬浮体用的填料(见图1-12)。

图1-12 树脂糊连续混合供料系统
1—带挤压卸料头的旋转供料器;2—预混合供料器;3—带搅拌器的下料斗;4—脉动料斗;5—带式混合器;6—计量泵;7—树脂泵;8—引发剂储箱;9—泵;10—冷却器;11—反应釜;12—树脂泵
(3)上糊量控制 上糊量指SMC每平方米面积所需树脂糊质量。刮板与聚乙烯薄膜间的距离,是控制上糊量的主要方法。下薄膜上的树脂糊量由刮刀来控制,刮刀放置在薄膜两边的支座上,通过升降刮刀来控制与薄膜的间隙。单位面积树脂糊的质量和单位面积SMC的质量是通过负载传感器的数字显示的。数据精确至1%。产生的信号又可自动反馈调节刮板以得到单位面积预定的树脂糊质量。
(4)玻璃纤维的切割及沉降(见图1-13) 将SMC用短切玻璃纤维引入三辊切割器切割成要求长度而成,产生的短切玻璃纤维依靠其自重,在沉降室内自然沉降。为使短切玻璃纤维沉降均匀,在切割下可设置相应装置或吹入空气,切割器的宽度应大于片材的幅宽,并可根据工艺要求设置切割器,连续玻璃纤维的进料速度(切割速度)一般以80~130m/min为宜,过快易使纤维产生静电,严重影响短切玻璃纤维的均匀分布;过慢则粗玻璃纤维纱分散性不好,并降低生产效率,解决静电相应的方法有严格控制切割区域的温度和相对湿度(要求RH 50%~65%)、在浸润剂中加入抗静电剂、在切割器及纤维导入设备上安装静电消除器等。
另外纱团数z越多,沿刀辊轴向纱的排布越均匀,越有利于纤维的均匀分布,但它受到设备结构限制。纱团的计算公式为:
z=(1000v主kk1k2b)/(k3v切)=(1000v主kk1k2b)/(k3πDn切) (1-1)
式中 v主——片材生产车速,m/min;
b——SMC片宽,m;
D——切割辊直径,m;
k——纤维支数;
n切——切割辊转速,r/min;
k3——纤维股数。
(5)浸渍和压实 为使纤维被树脂浸透、驱赶气泡和使片状模塑料压实成均匀的厚度,有两种浸渍压实结构,即多滚筒的环槽压辊式与双层金属网带式。
①环槽压辊式浸渍装置 环槽压辊式浸渍压实机构由一系列上、下交替排列的成对滚筒组成。每对滚筒的上压辊(小辊)外表带有环槽,下辊(大辊)外表面是平的。于是,当片料通过滚筒时,在环槽的凸凹部分别形成高、低压区。由于相邻两个槽辊的环槽是错开的,这样片料在通过下对辊时,低压区逐渐变成高压区。如此反复数次,使物料沿滚筒轴向来回流动,反复挤压混合,起到均匀混合和充分浸渍的作用。
②双层金属网带式浸渍装置 上下薄膜夹带SMC料进入两个同步运行的金属网之间,上下网带分别有主动辊拖动和张紧辊张紧,位于网带外侧布有上下压辊,张紧辊和压辊均为主动辊,下压辊可以上下移动,当下压辊提起时,使网带和SMC料呈波浪形不断前进,物料在网带的压力和不断搓动下达到充分的浸渍。
(6)收卷、熟化与存放
①熟化条件 当SMC片材收卷完成后,一般要经过一定的增稠时间(熟化)后才能使用,熟化目的是除去大部分挥发物,降低压制时模压料的流动性、模压制品的收缩率,增加尺寸稳定性等。熟化室温度为45℃,乙烯基酯放置24h。目前也有在SMC机组上增设增稠区域或采用一些新型的增稠剂,SMC制备成片材后即可进行压制。
PF-SMC熟化:生产出的PF-SMC需要在30~70℃的恒温内经过24~100h的熟化处理,至物料不粘膜为止。与UP-SMC一样,熟化要适当,防止硬化影响加工制品。熟化应仔细管理,作为PF-SMC质量管理点。PF-SMC在储存中也稍微进行缩合反应及固化,在10℃低温环境下保存,在3个月内能够保持容易使用的硬度。NR9440酚醛树脂熟化时间是40℃下24~36h。
②熟化程度测定 SMC熟化程度有的厂家仍采用针入度法测量;有的厂家是将同批树脂糊用聚乙烯薄膜包裹,到时测黏度。
1.1.3.3 TMC(厚片模塑料)
TMC组成与制作同SMC类似。SMC一般厚0.63cm,而TMC厚度达5.08cm。由于厚度增大,纤维随机分布,从而增强了物料混合效果,提高了流动性,改善了浸透性。由于聚乙烯薄膜用量的减少,从而降低了模塑料成本。TMC自1976年出现以来,已成为比SMC与BMC应用范围更广的模塑料。
TMC成型工艺是玻璃纤维粗纱由切割辊定长切割,通过料斗下部的挡板落到浸渍辊上,树脂糊通过计量泵送到浸渍辊的表面,使树脂与纤维在浸渍辊上混合,并被两个快速反向转动的辊子捏合。两辊的间隙直接影响纤维的浸渍效果。一般在捏合后,纤维已经被浸透。工艺要求纤维的长度为6~50mm。浸渍纤维与树脂的比例由浸渍辊转速控制。预浸纤维离开浸渍辊的捏合区域后,由离浸渍辊很近的均匀转动的两个刮辊刮下。刮辊直径为100mm,高速转动产生离心力,把混合料放到下面的薄膜上。混合料随薄膜移动,并由另外一薄膜覆盖上,然后进入压实区域,压平后成为片材。薄膜的运行速度控制TMC的厚度,TMC较SMC厚得多,不易收卷,因此,在机器的末端将TMC按照一定长度切断,包装成箱。TMC生产设备面积很小,因此,大大减少了苯乙烯的挥发(如图1-13所示)。

图1-13 TMC的生产过程
1—玻璃纤维粗纱;2—切断器;3—短玻璃纤维粗纱;4—浸渍辊;5—树脂糊;6—刮料辊;7,9—聚乙烯薄膜;8—TMC混合料;10—TMC模塑料
1.1.3.4 HMC(高强模压料)
高强模塑料(HMC)的显著特色是采用韧性好的玻璃纤维,且含量高,通常为40%~60%,在树脂糊中使用了乙烯基酯树脂,其制品具有高的力学性能,一般为SMC的2倍,耐化学药品性优良。美国匹兹堡玻璃板(PPG)工业公司HMC与一般SMC比较见表1-22。
表1-22 HMC与SMC性能比较

HMC配方见表1-23,图1-14为生产车间实测HMC配方树脂糊增稠曲线。
表1-23 HMS配方


图1-14 生产车间实测HMC配方树脂糊增稠曲线
上述配方树脂糊对玻璃纤维浸透性较好,片料厚度均匀,玻纤含量比较合适。由于玻纤含量达到50%以上,材料的弯曲和冲击强度比常规SMC提高50%,但由于玻纤含量较高,材料的流动性不佳,不太合适压制型腔复杂的产品,同时由于玻纤含量高,模压时需要用较高的压力,对模具的要求也较高。
1.1.4 悬浮浸渍法
将粉末(或纤维)状树脂和6~25mm的短切玻璃纤维在搅拌器内加水及泡沫悬浮剂(絮凝剂)搅拌成均匀的悬浮料浆,用泵输送到细密的传送网带上,经真空减压脱水,形成湿毡,再经干燥,收卷切断为干毡卷,其厚度为1.5~4mm。这种干毡可以直接装模,在对模中压制成制品,也可以在连续复合机上压制成片状模型料。工艺过程如图1-15所示。

图1-15 悬浮浸渍法生产片状模塑料工艺过程示意图
1—拌浆槽;2—泵;3—浆槽;4—浆料;5—真空脱水器;6—喷黏结剂;7—烘箱;8—坯料;9—加热加压器;10—片状模塑料
该生产工艺的特点是纤维和树脂分布均匀,纤维含量为20%~70%,产品厚度为1.27~6.35mm,此法除用玻璃纤维外,还可以用碳纤维等其他纤维。
1.1.4.1 玻璃纤维增强聚丙烯和PET
悬浮浸渍法生产玻璃纤维增强聚丙烯和PET片材工艺过程如下。
①聚丙烯粉末与异丙醇进行混合以增加其在水中的分散性。当粉末被异丙醇充分浸润后,将等量的水加入混合物中,使其具有可灌注性。使用PET粉末时,则不需要使用异丙醇。
②芳族聚酰胺浆料分散在水中,浓度为4g/L,进行10min的高速混合。典型的纤维长度为2mm,有效直径可达到20μm。
③混合3min后,将浸润的聚合物粉末加入芳族聚酰胺浆料混合物中。
④最后将玻纤和预分散好的浆料聚合物添加至装有750L、30℃水,容积为2000L的混合槽中。浆料中固体的总含量范围在4.6~5.3g/L,或接近0.5%总量。随后浆料被泵送至倾斜线缆机的混合头中,不断搅拌,保持分散状态。连续经过滤网进入混合头,速度为1m/min。过滤出的基材在150℃的炉中干燥,制成0.62mm厚的片材。
1.1.4.2 长碳纤维增强聚苯硫醚
长碳纤维增强聚苯硫醚实验室制备方法:以12L水为介质,称取一定质量的碳纤维(12K-T700)和聚苯硫醚纤维(200D/50f)放入带有搅拌装置的容器内,开启搅拌,设置搅拌转速为200r/min,当搅拌速度稳定后,慢慢加入纤维和分散剂,搅拌15min后快速排尽水,获得混合纤维坯料。将混合坯料置于110℃的烘箱内干燥12h即可。
1.1.5 造粒
1.1.5.1 短纤维粒料制备
短纤维粒料中的纤维是均匀分布在树脂基体中,适用于柱塞式注射成型机和形状较复杂的制品生产,纤维在制品中的长度一般为0.2~1mm。
(1)原材料
①增强材料 用于增强热塑性塑料的短切纤维有玻璃纤维(直径为10~20μm)、碳纤维、芳纶纤维和晶须等。
a.挤出与注塑工艺用无捻粗纱 表1-24列出了巨石集团有限公司生产的热塑性塑料用无碱玻璃纤维无捻粗纱(纤维表面涂覆硅烷基浸润剂)的品种、性能及应用。
表1-24 巨石集团热塑性塑料用无碱玻璃纤维无捻粗纱的品种、性能及应用①

①巨石集团有限公司2015年复合材料展览会产品说明书。
b.短切原丝在热塑性树脂中的应用 巨石集团有限公司生产的热塑性塑料用无碱玻璃纤维短切原丝系采用硅烷基偶联剂、专用浸润剂配方,具有与PA、PBT/PET、PP、AS/ABS、PC、PPS/PPO、POM、LCP等基体树脂良好的相容性,优良的集束性和流动性,良好的成型加工性能,可赋予复合材料优异的力学性能和表面状态,增强热塑性塑料用无碱玻璃纤维短切原丝的品种有巨石集团有限公司的560A、568H、534A、508A、508H、540H、510、510H、500和584等,PPG公司的HP3299、HP3540、HP3610和HP3786等。
②基体树脂 几乎所有的热塑性塑料都可以用纤维增强。对于熔融温度较低的热塑性塑料,如聚丙烯、聚氯乙烯、聚苯乙烯等,可直接将其加温熔融,连续纤维束喂进双螺杆挤出机内与熔融态树脂混合后挤出,由切割机切断,长度一般为3~6mm,纤维太长则使后面的注射成型困难。纤维含量有20%、30%和40%等。
熔融浸渍要想使高黏度的熔融态树脂(黏度高达103Pa·s以上)在较短的时间内完全浸润纤维是困难的。要获得理想的浸润效果,就要求树脂的熔体黏度足够低,且在高温下足够长时间内稳定性好。因而聚苯硫醚(高温易氧化交联)、聚醚砜(熔体黏度高)等树脂实际上难以采用这种方法预浸。
短切玻璃纤维增强聚丙烯,采用通常的成型方法,玻璃纤维长度大约为0.3~0.6mm;挤出造粒玻璃纤维长度为0.5~1.0mm。将聚丙烯(熔体流动速率=3~13g/10min)与玻璃纤维混合均匀,切粒即得增强聚丙烯。
(2)粒料生产工艺
①单螺杆挤出机 此法是将短切玻璃纤维原丝与树脂按设计比例加入到单螺杆挤出机中混合、塑化、挤出条料,冷却后切粒。对于粒料树脂,要重复2~3次才能均匀。对于粉状树脂,则可一次挤出造粒(生产工艺过程如图1-16所示)。此法的优点是:纤维和树脂混合均匀,能适应柱塞式注射机生产。其缺点为:玻璃纤维受损伤较严重;料筒和螺杆磨损严重;生产速度较低;劳动条件差,粉状树脂和玻璃纤维易飞扬。

图1-16 短切玻璃纤维增强粒料生产工艺过程示意图
1—玻璃纤维纱锭;2—切割器;3—加料斗;4—计量器;5—混料斗;6—挤出机;7—切粒机
②单螺杆排气式挤出机 此法是将长纤维粒料加入到排气单螺杆挤出机中,回挤一次造粒。如果粒料中挥发物较少,则可用普通挤出机回挤造粒。
此法的优点是:生产效率高;粒料质地密实,外观质量较好;劳动条件好,无玻璃纤维飞扬。缺点是:用长纤维粒料二次加工,树脂老化概率增加;粒料外观及质量不如双螺杆排气式挤出机造粒好。如果考虑到长纤维造粒过程,其工序多,劳动生产率低。此法对设备要求不高,国内采用的厂家较多。
③双螺杆排气式挤出机(如图1-17所示) 此法是将树脂和纤维分别加入双螺杆排气式挤出机的加料孔和进丝口,玻璃纤维被左旋螺杆及捏合装置所破碎,在料筒内纤维和树脂混合均匀,经过排气段除去混料中的挥发性物质,进一步塑炼后经口模挤出料条,再经冷却、干燥(水冷时用),然后切成粒料。粒料中的纤维含量,可由调整送入挤出机的玻纤股数和螺杆转速来控制。单螺杆挤出机主要是靠机头压力产生均质熔体,双螺杆挤出机完全是靠螺杆作用使树脂充分塑化,并与纤维均匀复合(图1-18)。因此,它除具有排气式单螺杆挤出造粒的优点外,可比单螺杆挤出机更有效地挤出造粒和利用松散物料。

图1-17 双螺杆排气式挤出机结构图
1—料斗;2—料筒;3—螺杆;4—节流阀;5—排气口;6—真空泵;7—机头;8—口模;9—栅板;10—真空泵;11—冷凝器

图1-18 双螺杆排气式挤出机纤维粒料制备工艺流程图
1—计量带式给料器ZSK/V;2—热塑性塑料;3—玻璃纤维粗纱;4—排气;5—条模;6—水浴;7—料条切粒机
④造粒机头 按造粒机头的结构不同可分为如下几类。
a.带自动压紧装置的造粒机头 这种机头的刀架后面设有弹性装置,可自动压紧刀架,压力大小可以通过螺杆来调节。
b.锥形流道造粒机头 这种机头的流道形式为锥形,所以称为锥形流道造粒机头。
c.圆形造粒机头 这种机头的外形为圆形,所以称为圆形造粒机头。
d.芯棒式造粒机头 这种机头的内部设有芯棒结构,所以称为芯棒式造粒机头。
按机头内的压力大小可分为:低压机头(其料流压力小于4MPa)。中压机头(其料流压力在4~10MPa)和高压机头(其料流压力大于10MPa)。
⑤切粒机 根据粒料相同的冷却方式,切料装置与机头配合各异,其造粒工艺流程与产量也不相同,有如下两种切粒方法。
a.拉条切粒 这是挤出造粒中最简单、产量较低的造粒方式,适合于试验。其工艺流程如下:
挤出机→滤板与滤网→拉条机头→风冷或水冷却→旋转刀切粒→圆柱形颗粒料
b.模面切粒
(3)实用举例
①阻燃聚丙烯塑料粒料 其配方见表1-25。
表1-25 阻燃聚丙烯塑料粒料配方 单位:质量份

②阻燃、抗静电玻璃纤维增强尼龙6粒料
a.原材料与配方 所用原材料与配方见表1-26。
表1-26 阻燃、抗静电玻璃纤维增强尼龙6粒料配方

b.主要设备 双螺杆挤出机:TSE-45型;高速混合机:SHR-100A。
c.制备工艺 按表1-26给出的配比称量所需的原材料,然后依次倒入高速搅拌机中,高速搅拌10~30s,用双螺杆挤出机按表1-27所列的挤出工艺参数挤出、造粒。
表1-27 挤出工艺参数

③PET/玻纤注塑专用料
a.配方(见表1-28)
表1-28 PET/玻纤注塑专用料配方

b.制备工艺 先在高速混合机内加入PET切片、改性剂和各种助剂,混合均匀后取出,配以一定比例的玻纤在双螺杆挤出机上挤出,挤出料经水冷造粒。挤出工艺参数:塑化熔融温度240~275℃;喂料速度10~12r/min;螺杆转速100~120r/min;切粒速度300~500r/min。
c.性能 表1-29列出了不同玻纤含量的PET/玻纤注塑专用料的性能。
表1-29 不同玻纤含量的PET/玻纤注塑专用料的性能

④PBT节能灯专用料
a.配方(见表1-30)
表1-30 PBT节能灯专用料配方 单位:质量份

b.制备工艺 将烘好的PBT、增韧剂、遮光剂、阻燃剂等经高速混合机混匀后,置于加料器中,定量从第一进料口加入,PBT专用玻璃纤维从第二加料口引入,在温度为220~230℃、螺杆转速为160~230r/min下,经双螺杆挤出机共混挤出、冷却、切粒得到遮光型阻燃增强PBT,即PBT节能灯专用料。
c.性能 PBT节能灯专用料综合性能较好(见表1-31)。
表1-31 PBT节能灯专用料性能

⑤聚苯硫醚(PPS)/玻璃纤维粒料 制备聚苯硫醚(PPS)/玻璃纤维料粒应选用高温型、耐磨、耐腐蚀材质制造的双螺杆挤出机,其典型制备工艺见表1-32,纤维增强PPS树脂性能见表1-33。
表1-32 典型的双螺杆挤出机制备PPS/GF料粒的工艺条件

表1-33 纤维增强PPS树脂性能

①R-4,G-6为菲利浦石油公司产品。
②GL-50-001为美国Polymer Composites公司产品。
⑥碳纤维粒料制造工艺 集束碳纤维经切断机切短到3~7mm长,加入到挤出机的加料斗,与热塑性树脂粒料定量混合,然后进入挤出机,在出口被切粒机切成所需长度的碳纤维增强塑料粒料。碳纤维的集束剂很重要,使其成束,便于控制切短长度,切短后又容易开纤,使其具有流动性,防止堵塞料斗。切短碳纤维与热塑性树脂粒料混合后,加入螺杆挤出机,使其充分混合均匀,采用双螺杆挤出机效果较好。
1.1.5.2 长纤维增强热塑性塑料粒料制备(LFT-G)
长纤维增强热塑性塑料(long-fiber reinforce thermoplastic,LFT)粒料是指将连续玻璃纤维用熔融的热塑性树脂充分浸渍后,通过定型模头,拉出成棒状或带状,切成不同长度(一般为11~25mm)的纤维增强粒料。与传统的短纤维增强材料的生产方法不同,用这种方法生产的长玻璃纤维增强材料,由于玻璃纤维没有通过挤出机的混炼过程,不会因为螺杆的剪切作用而被切短,因此纤维的长度与所切粒子的长度一样,可达到能够注射成型的最大长度,通过采用合适的注射成型工艺,制品中的玻璃纤维长度仍然可以保持在3~5mm的长度(短玻璃纤维仅有0.2~0.7mm)。
(1)原材料
①增强材料 LFT用无碱玻璃纤维直接无捻粗纱(纤维表面涂覆硅烷基浸润剂)。
②基体树脂 主要是聚丙烯、聚氯乙烯、尼龙和ABS树脂。
(2)主要设备 造粒需要的设备有挤出机、纱架、机头、牵引机和切粒机等。
①机头 生产长纤维粒料的机头由型芯、型腔和集束装置三部分组成(见图1-19)。玻璃纤维通过型腔中的导纱孔进入机头型腔与熔融的树脂混合。为了使树脂能充分浸渍纤维,机头内设有集束板或集束管,使熔融树脂进一步浸透纤维,成为密实的纤维树脂混合料条。

图1-19 长纤维增强粒料包覆机头结构
1—送丝孔;2—型芯;3—熔融树脂;4—型腔;5—集束装置;6—出料口
②牵引和切粒 牵引和切粒一般是在一台机器上完成。牵引机构是由两对牵引辊完成,第一对牵引辊的牵引速度比第二对辊低,从而保证两道牵引辊之间有一定的张力,防止料条堆积,但张力不能过大,否则会将料条拉断。
造粒是用切刀将料条连续不断地切成所需要长度的粒料。切刀分滚切式和剪切式两种。一般塑料造粒,多选用滚切式切刀;生产增强粒料时,则需要选用剪切式切刀。因料条中的玻璃纤维用滚切式切刀不容易切断,常从粒料中拉出。增强粒料中玻璃纤维硬度较大,因此,刀具必须锋利、耐磨。常选用高速工具钢制造。如选用W18Cr4V2工具钢。
上海杰事杰公司杨桂生等研制的新型切粒机,主要是由下列部件组成:位于转轴端上的动刀盘上装有动刀;与动刀盘位置相对的定刀座上设有进料辊、进料口和定刀刀片,定刀座上具有可沿动刀盘的中心轴方向调节定刀座位置的调节螺母;具有两个进料口;定刀刀片设置在每个进料口的一侧,其刀口方向与动刀旋转方向相反;动刀盘上设有3~24把沿其中心轴呈放射状排列的动刀。图1-20为切粒机转盘和进料结构示意图。

图1-20 切粒机转盘和进料结构示意图
1—工作面;2—转动轴;3—动刀盘支座;4—固定螺钉;5—动刀盘;6—动刀;7—定刀支座;8—导向板;9—进料辊;10—进料辊支架;11—定刀支座调节螺钉;12—定刀支座固定螺钉
(3)制造工艺 连续玻璃纤维无捻粗纱通过特殊模头,同时向模头供入由螺杆挤出熔融树脂,在模头内无捻粗纱与熔融树脂接触被强制散开,受到熔融树脂充分浸渍后,使每根纤维被树脂包覆,经冷却后,再切成较长的粒料(11~25mm)。
制造长纤维料粒的设备有立式和卧式两种。立式造粒设备的挤出机置于混凝土高台上,包覆机头出口垂直向下,如图1-21所示。由牵引滚筒卷取料条,然后再送至切粒机切粒,因而它的造粒为间歇式。卧式布置是将包覆机头出口呈水平方向放置,如图1-22所示。由于挤出机放在平地,操作较方便,料条是通过牵引辊直接喂入切粒机切粒,所以它的造粒是连续的。

图1-21 制造粒料设备立体布置图
1—玻璃纤维;2—送丝机构;3—电动机;4—无级变速箱;5—牵引滚筒;6—机头;7—冷却水;8—料条;9—送至切粒机;10—挤出机

图1-22 制造粒料设备平面布置图
1—玻璃纤维;2—送丝机构;3—挤出机;4—机头;5—牵引辊;6—水冷或风冷;7—切粒机
(4)实用举例
①长纤维增强ABS粒料制备 将干燥后的ABS、增韧剂、相容剂和抗氧剂按一定配比在高速混合机中混合均匀,然后在双螺杆挤出机上挤出(螺杆转速为200r/min,1~6区温度分别为190℃、195℃、215℃、215℃、225℃、225℃),长玻纤进入特殊的浸渍口模,浸渍温度为250℃,在口模内完成树脂对玻纤束的浸渍,经冷却、切粒制得长玻纤增强ABS粒料。
用连续纤维无捻粗纱与热塑性塑料通过挤出、造粒或制片方法制成粒料半成品,再经注射成型(LFT-G)或模压成型(LFT-D)为制品。长纤维粒料长度为12mm以上(一般为12~25mm),纤维长度与粒料相当。经过注射或模压之后,最终制品内的纤维平均长度仍然不低于4mm(注塑制品中纤维长度约4~6mm,压塑制品中纤维长度约20mm)。纤维含量可达20%~60%,最常用的为40%和50%。
②长纤维增强PBT粒料制备 PBT树脂120℃烘干2h,将烘干的PBT、AX8900、抗氧剂及其他加工助剂按照一定配比在高速混合机中混合均匀,再在SJSH-30型双螺杆挤出机中熔融挤出,在挤出机机头处引入经热风处理过的LFT玻纤,通过自制的浸渍机头制成连续长玻纤浸渍PBT复合材料,冷却,风干造粒,挤出温度为220~240℃,浸渍机头温度为245℃,切粒长度为15mm。
③玻璃纤维增强聚氯乙烯窗框
a.原材料与配方(见表1-34)。
表1-34 玻璃纤维增强聚氯乙烯窗框配方

b.设备及工艺条件。
ⅰ.设备:捏合机,GH200A型,北京塑料机械厂;塑炼机,SK-550型,大连橡胶塑料机械厂;切粒机,JL-240型,上海轻工机械公司。
ⅱ.工艺条件见表1-35。
表1-35 工艺条件

c.制备工艺
ⅰ.制备工艺流程 配料→高速混合→双辊炼塑→双辊拉片→切料
ⅱ.原料预处理
(ⅰ)玻璃纤维处理 用玻璃纤维切碎机将玻璃纤维切成4~6mm长的短纤维,呈绒毛状,然后用环氧硅烷进行偶联处理,以增大与PVC树脂的密合性。
(ⅱ)云母处理 采用直径为20μm的云母片,用氨基硅烷进行偶联处理,以增大与PVC树脂的密合性。
(ⅲ)碳酸钙处理 采用粒径为0.08mm的轻质碳酸钙,用硬脂酸进行表面处理,以增大与PVC树脂的密合性。
④玻璃纤维/碳纤维增强酚醛粒料制备
a.制备工艺
粗纱→浸胶→预烘→集束→烘干→固定束形→冷却→牵引→切粒。
b.工艺参数(见表1-36)
表1-36 玻璃纤维/碳纤维增强酚醛粒料制备工艺参数

1.1.6 原位成纤复合材料制备
原位成纤是指复合材料中的纤维并不是预先纺制的,而是在挤出、注塑等加工过程中“就地”形成,即分散相在连续相中由于受到剪切、拉伸作用而发生形变、聚结,形成微纤,其直径分布在10μm左右。
1.1.6.1 PP/活性PA66(α-PA66)原位成纤复合材料粒料制备
将PP与α-PA66按75∶25的配比混合均匀,在双螺杆挤出机(螺杆直径为21.7mm,长径比为40,圆形口模直径为3mm)中热机械熔融共混挤出,挤出物通过牵引机进行拉伸,通过调整牵引辊的转速可以实现不同的拉伸比(口模的横截面面积与挤出物的横截面面积之比),本工艺试样拉伸比为8。拉伸后的料条在冷水(约15℃)中冷却,最后切粒。挤出机从加料段到口模的温度:265℃/275℃/280℃/280℃/275℃;主螺杆转速:90r/min。
1.1.6.2 PA11/PP原位成纤复合片材制备
将PA11在鼓风干燥箱中80℃恒温干燥12h。干燥后将PP、PA11粒料按质量比90∶10混合均匀,经聚合物微纳叠层共挤装置中挤出,挤出温度为240℃,螺杆转速230r/min,喂料频率15r/min,牵引辊电动机转速45r/min,制得原位成纤复合片材。