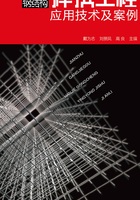
二 焊接线能量定义及其实际控制
焊接线能量知识是焊接应用技术理论和焊接实践有机结合的桥梁,是焊接从业人员必须掌握的立身之本,是非常重要的技术理论参数。因此,必须充分理解其技术实质,并在工程实践中加以灵活运用。
(一)焊接线能量的定义
焊接线能量又称焊接热输入量,是焊缝(熔合线)单位长度所吸收的热量(能量)。用下式来表述:
E=ηAV/U (1.1)
式中 E——线能量(热输入量),kJ/cm;
η——热效率0.8~0.95,在实际计算中可以不考虑热效率;
A——焊接电流,A;
V——电弧电压,V;
U——焊接速度,cm/min。
焊接线能量是焊缝质量“控形”和“控性”最重要的技术参数。实际焊接线能量大小决定焊缝及HAZ的综合性能,因为焊缝中的熔合线(区)是焊接接头最薄弱的部分,是提高焊接质量必须研究的重点部位,线能量概念直接地影响和表征了这一技术要点。
焊接线能量是最有影响的焊接参数,目前生产的钢材,在焊接工程中多数需要限制线能量的上限(少数承受大线能量钢种除外),以免发生过热软化和脆化。而今面对广泛使用的建筑钢结构焊接工程中的结构钢,特别是高强钢,还必须限制线能量的下限,否则易于引起冷裂纹现象。
(二)焊接线能量与焊缝“控形、控性”质量控制
线能量包含三个参数:焊接电流A、电弧电压V、焊接速度U。如果说焊接线能量的确定取决于焊接性;那么,焊接线能量在一定的情况下,焊接参数如何组合,则主要取决于其工艺性,即操作过程的稳定性和良好的成形等。对于GMAW、FCAW-G、SAW而言,焊接电流的变化可以由送丝速度反映出来,因此,要求焊接速度与送丝速度有良好的配合。
焊缝“最精准的控型、最少损害的控性”质量控制观点,是著名学者、焊接专家宋天虎先生提出的新概念。这一观念不仅新颖时尚,而且对工程管理技术实质“一语中的”。这一概念的提出,标志我国焊接质量控制思想认识登上一个新台阶。
所谓焊缝最精准的控形,是指在一定焊接工艺条件下,获得优良致密、无缺陷焊接接头的能力。它不是钢材本身所固有的性能,而是根据某种焊接方法和所采用的具体工艺措施来努力实现的目的。也就是焊缝包括表面、焊缝形状及焊缝的内在成形质量的控制,即焊接电流、电弧电压、焊接速度有机(最佳)组合的结果。应当说,这是焊线能量工艺特性所决定的,所以金属材料的工艺特性与焊接过程密切相关。因此,对焊工的操作水平提出了极高的要求。
所谓焊缝“最少损害的控性”,就是控制焊缝的综合性能。即焊缝的力学性能和冶金性能,其中包括:抗拉强度(σb或Rm)、屈服强度(σs或Re)、伸长率(δ)、断面收缩率(ψ)、冷弯、硬度、冲击韧度(ak)、金相组织。即良好的焊接性和熔池良好的冶金反应是由焊接线能量针对相应母材的焊接性所决定的。而这一关键技术指标,涉及焊接接头的综合性能,特别是脆性断裂的脆性转变温度的高低,因此,是工程技术人员关注的重点。
由此,全面的、无遗漏的、有机的组成焊缝的综合性能。
(三)焊缝最精准的控形指标和焊接线能量的关系
一条质量上乘的焊缝表面应该没有裂纹、咬肉、气孔、夹渣、未熔合、焊瘤,没有明显的焊缝表面宽窄差、高低差,没有超标余高、反面未熔透等焊接缺陷(欠)。
同样,一条质量上乘的焊缝内部应该没有裂纹、超标气孔、超标夹渣、未熔合等焊接缺陷(欠)。
而线能量的大小决定和影响上述缺陷(欠)的产生。
以表面成形为例,当长弧焊接时,电弧电压升高,即使在焊接电流不变的情况下,线能量也会增大,使焊缝变宽;长弧焊接很不稳定,容易使焊缝表面形状不连续,极易造成表面焊缝的宽窄差和高低差,以及气孔和焊瘤的产生。
焊缝的良好成形是焊缝质量的基本保证。焊缝的宽窄差、余高的高低差过大,不仅影响观感质量,而且会使焊缝不连续,进而导致应力与应变不均匀,对焊缝质量有所影响。
即使电压稳定,电流加大也会造成焊接缺陷,一般来说,在这个情况下,焊缝表面成形极易形成焊接应力集中的咬边缺陷(欠),这是在有疲劳强度验算要求的焊缝最不希望看到的。
在电弧电压稳定(即短弧焊接)的情况下,使用小电流焊接时,如果线能量过小,导致焊缝冷却速度过快,焊接的残余氢来不及逸出而残留在焊缝中,这就会增加冷裂纹的敏感性,导致延迟裂纹产生的概率增加。
应当特别指出的是:焊缝的表面绝对不允许有裂纹、夹渣、气孔和未焊透缺陷,这些缺陷都会导致应力集中,从而影响焊接接头的质量,所以用高标准控制焊缝的表面质量至关重要。
焊缝的控形指标即部分缺陷与施工工艺的关系见表1.3。
表1.3 焊接部分缺陷与施焊工艺的关系

注:◎表示有明显影响,○表示在一定条件下有影响,△表示关系很小。
表1.3中带★号参数就是和线能量密切相关的参数,焊接线能量是焊缝控形的关键技术参数,焊接线能量过大参数配比不当所造成的部分缺陷(欠)见图1.2。

图1.2 焊接线能量过大、参数配比不当的部分控形缺陷(欠)
图1.2中各分图解释如下。
(a)下塌。焊根部的熔深过大,超过规定的极限。它可以是连续的,也可以是断续的。
(b)焊瘤。焊接过程中,熔化金属流淌到焊缝以外未熔化的母材表面上所形成的金属瘤。
(c)根部内凹。由于收缩在对接焊缝根部出现的沟槽。
(d)烧穿。由于熔池的塌陷而在焊缝中形成的孔洞。
(e)咬边。在沿着焊缝焊趾的母材部位或前一道焊缝上产生的沟槽或凹陷;通常情况下,它通过深度、长度和尖锐度来表征。
(f)焊缝宽度不均匀。焊缝宽度波动过大。
(g)焊条电弧焊(SMAW)电弧焊焊缝成形质量(从左到右):①正常的电流、弧长和焊接速度;②电流太低;③电流太高;④弧长太短;⑤弧长太长;⑥焊接速度太低;⑦焊接速度太高。
在最佳线能量前提下,如果没有焊接电流、电弧电压、焊接速度三个参数的最佳配合,不可能得到最佳控形的焊缝质量。
(四)焊缝最少损害的控性指标和焊接线能量的关系
在建筑钢结构焊接工程中,多年来,人们普遍认为NDT的结果是可靠的,一旦焊缝UT或RT检验合格后就“万事大吉”,认为工程肯定合格。实际上,这是十分片面的,是不完全靠得住的结论。例如:当人们采用大线能量(大电流、慢焊速)焊接后,尽管UT、RT全部合格,由于焊缝及HAZ晶粒粗大,其综合指标急剧下降,特别是冲击韧度(ak)肯定不合格,而这种不合格不可能用肉眼直接观察到,因此,有很大的隐蔽性,同时也是极大的质量隐患。这种情况如果在实际工程中经常发生,会影响工程质量,应当加以纠正。
焊缝由三个部分组成:焊缝金属、熔合线、HAZ。焊缝金属既不是母材,又不是焊材的熔敷金属,其力学性能与材质的原始规定有较大的差距,这是因为焊缝的综合性质受各方面因素的影响,其主要因素有以下几种。
1.焊接层数的影响
在焊后冷却过程中,焊缝从接近基本金属开始凝固,单道焊的组织为典型的柱状结晶,且共晶粒通常是与等温曲线法向方向(即最大温度梯度方向)长大。由于凝固是从纯度较高的高熔点物质开始,所以在最后凝固部分及柱状晶的间隙处,便会留下低熔点不纯物质。在多层焊时,对前一道焊缝重新加热,加热超过900℃的部分可以消除柱状晶并使晶粒细化。因此多层焊比单层焊的力学性能要好,特别是冲击韧性有显著的提高。
2.焊接线能量的影响
单道焊缝金属,由于冷却进度快,其强度有所上升,增加焊接热输入线能量,提高预热和层间温度,会导致冷却速度降低,晶粒更加粗大,其结果是使焊缝金属强度和韧性下降,所以,高强钢出于强度和韧性的考虑,有必要限制其最低冷却速度,但过快的冷却速度往往会造成淬硬组织,产生冷裂纹,因此,对于高强钢,限制其晶粒度的粗大,确定合理的冷却速度,具有十分重要的意义。
3.基本金属的稀释率对焊缝强度的影响
在焊接接头的设计中,首先要考虑焊材的选择,以保证焊缝金属所要求的强度,但必须强调,不应只要求焊缝的化学成分与母材的化学成分相同。这是因为,根据理论分析,焊缝成分与母材成分相同时,往往不能满足设计指标的要求。因为焊缝与母材经历的冶金过程不同,钢材经冶炼浇铸后,须进行再轧制,轧制后还要经过复杂的热处理,方可满足实际使用的技术要求。焊缝金属主要是在铸态条件下去满足技术要求,有的工艺要求焊后进行热处理,但这不可能同母材的热处理过程一样,没有经过轧制的铸态金属焊缝往往只进行简单的回火处理,其目的是消除残余应力和进行软化。换句话说,焊缝的性能主要靠成分的调整,而不是靠热处理。焊缝金属成分不等于焊接材料的成分,所谓焊接材料的成分,是指熔敷金属的成分,是焊条、焊丝熔化后,在完全没有母材参与的情况下所形成的焊后金属。而实际的焊缝往往有母材参与,受熔合比的影响(熔合比是母材在焊缝中所占的比例)。
由于基本金属(母材)也要参加冶金反应进而对焊接材料进行稀释,其结果是基本金属对焊缝金属性能产生一定的影响,所以,焊缝金属是熔敷金属和熔融的基本金属的混合物。其性能和基本金属、熔敷金属有所区别。在焊缝金属中,基本金属所占的比例取决于焊缝类型和焊接线能量,见图1.3。

图1.3 焊接坡口、焊道同稀释率的关系
由于检测力学指标和金相试验是破坏性试验,因此,焊缝的控性指标不可能在钢结构焊接工程竣工后直接进行检测,只能是靠全过程质量管理与控制来实现和保证,这是焊接控性技术的精髓,也是建筑钢结构安全的根本保证。
焊缝的控性质量是焊接接头最根本的质量指标,涉及焊接母材的焊接性和全面质量管理“人、机、料、法、环”五大管理要素和焊接全过程控制与管理,技术内涵十分丰富、复杂,是人们关注的重点。
焊缝是在不均匀的加热和冷却的冶金反应中形成的,影响焊缝治金性能的因素很多,且十分复杂。在众多影响焊缝质量的因素中,焊接线能量是最重要的因素之一。焊接线能量的大小,决定冶金反应的各项指标,特别是二次结晶过程中的t8/5的长短,直接决定焊缝的冶金性能和力学性能。因此,焊缝的控性指标必须通过PQR、WPS对焊接线能量进行焊接工程全过程控制,每个工序必须按WPS技术要求严格执行才能实现。
(五)焊接线能量在焊接热循环中的作用
事实上,焊接线能量和焊接二次结晶理论密切相关,焊接线能量直接影响其重要参数。
一次结晶结束后,熔池变为固体焊缝,高温的焊缝金属冷却到室温时,要经过一系列的相变过程,这种相变过程就称为焊缝金属的二次结晶。其主要影响参数有t8/5、t8/3、t100等,见图1.4。
如图1.4所示:t8/5是指800℃到500℃的焊接熔池冷却时间;t8/3是指800℃到300℃的焊接熔池冷却时间;t100是指焊缝的最高温度冷却到100℃所需的时间。这三个重要的技术参数虽然不在焊接规范中出现,但它们是保证焊缝质量的关键指标,在焊接工程实践中是非常重要的技术参数。其中t8/5(t8/3)的大小决定HAZ及焊接接头的综合性能,是一个理论和实践都很强的技术指标,因此,成为工艺研究重点,应当引起人们的高度重视,t8/5(t8/3)有多种确定方法,将在有关章节中进行阐述。

图1.4 焊接热循环中重要技术参数
1.t8/5(t8/3)主要影响因素
t8/5(t8/3)主要影响因素有:板厚,焊缝接头形式,焊接线能量,预热、层(道)间温度,母材物理性能。
t8/5(t8/3)过长或过短,都会对焊接接头的综合性能带来一定的影响;冷却时间的延长通常会导致冲击性能的减少和热影响区冲击过渡温度的上升,强度也会降低,而其降低的程度则取决于钢材种类及化学成分。
2.t8/5(t8/3)对焊缝硬度有较大影响
t8/5(t8/3)冷却时间对焊缝硬度有较大影响,其硬度在一定程度上也间接反映强度的变化,t8/5(t8/3)冷却时间延长,硬度值减小。
3.t8/5(t8/3)对冲击性能的影响
t8/5(t8/3)冷却时间的延长通常会导致冲击性能的减少和热影响区冲击脆性温度的上升,强度也会降低,降低的程度取决于钢材种类及其化学成分。
在实际焊接工程中,人们通过控制焊接预热温度和焊接线能量来获得合适的t8/5(t8/3),进而获得理想的焊接控性质量,由此可见,线能量在焊接热循环中的作用举足轻重。
4.t100的作用
在研究高强钢焊接冷裂纹时可以发现,从峰值温度冷却到100℃的时间对冷裂纹有着十分重要的影响,故常用t100作为冷裂纹倾向的重要参数之一。目前尚未建立t100可靠的计算公式,主要通过试验的方法测得。
不言而喻,焊接线能量的大小对t100也会产生很大的影响,t100越长,越有利于焊缝扩散氢的逸出,杜绝和减少延迟裂纹发生。但是,t100的延长必须增加焊接线能量,然而,焊接线能量的增加会导致焊缝及HAZ晶粒粗大,因而降低焊接接头的综合性能。这是一对矛盾,解决这一矛盾的方法是采用合适的焊接线能量和后热(200~350℃)去氢处理工艺,这样既保证了焊接接头的综合性能,又延长了t100,防止了焊接接头氢致裂纹的发生。
(六)最佳焊接线能量和最佳焊接参数上、下限的确定
焊接线能量包含三个参数:焊接电流I(A)、电弧电压U(V)、焊接速度v(cm/min)。焊接线能量的确定取决于钢材的焊接性和焊接的工艺性。最佳焊接线能量和最佳焊接参数的确定,其依据是所焊钢材的t8/5数据,而t8/5数据依据所焊钢材的CCT图或钢材HAZ的冷脆倾向(含过热脆化倾向)的程度来研究决定的。但是,理论推测和实际工程有一定的差距,这往往通过专项试验进行判断。
1.最佳t8/5的确定方法
焊缝金属最佳t8/5与合金化程度有关,随着焊缝合金化程度的提高,最佳t8/5应相应增大。选用不同的焊接材料,应具有相应的焊接工艺参数,以获得最佳t8/5,方可使焊缝金属获得最佳的强韧性配合(可以断定,对于焊缝而言,焊材的最佳t8/5未必会与母材HAZ适用的最佳t8/5一致)。
焊接线能量E的上、下限取决于t8/5的上、下限。而t8/5的上、下限的确定主要有两种方法。
(1)实测法
通过抗裂试验求得不产生冷裂纹的最小临界t8/5。常用斜y试验(小铁研),或CTS抗裂试验法。通过实际焊接试板,变化线能量,测定冲击韧度,按相应判据(常温至-40℃、27J或34J)确定t8/5的上限(也可以由焊接线能量E换算或实测)。
(2)CCT图法
利用焊接母材的CCT图可以估计t8/5的上、下限。但在估计t8/5的下限时,还应考虑HD(扩散氢)及RF(拘束度)的影响,并作必要的修正。
焊接连续冷却组织转变(Continuous Cooling Transformation)曲线图,简称CCT曲线,是表征某焊缝及热影响区金属在各种连续冷却的条件下转变开始温度和终了温度、转变开始时间和终了时间,以及转变的组织、室温硬度与冷却速度之间关系的曲线图。焊接连续冷却转变图分为焊缝金属连续冷却转变图(简称焊缝金属WM-CCT图)和热影响区连续冷却转变图(简称焊接热影响区SH-CCT图)。由于焊接热影响区SH-CCT图应用比较广泛,一般焊接CCT图多指热影响区SH-CCT图。
因此,CCT曲线与实际生产条件相当近似,所以,它是制定工艺时的有用参考资料。根据连续冷却转变曲线,可以选择最适当的工艺规范,从而得到恰好的组织,达到提高强度和塑性,防止焊接裂纹的产生等目的,对合理制定焊接工艺参数有重要的指导意义。
2.热影响区CCT图的表达形式
图1.5给出的是相当于12Mn钢热影响区CCT图的临界冷却曲线和临界冷却时间、
、
、
。图中的
、
、
、
分别表示从A3温度冷却到500℃开始出现中间组织(即各种贝氏类组织)、铁素体、珠光体,以及仅得到铁素体和珠光体组织的临界冷却时间(s)。
、
、
、
分别是由通过z、f、p、e点的临界冷却曲线与500℃等温线的交点Cz、Cf、Cp、Ce向时间坐标轴投影得到的时间值。这些特征值对分析焊接热影响区的组织很有意义,只要知道在实际焊接过程中热影响区所有要研究部位的金属从800℃冷却到500℃的时间t8/5,对照临界冷却时间,就可以判断热影响区的显微组织。

图1.5 成分相当于12Mn的焊接热影响区CCT图(Tm=1350℃)
SH-CCT图的应用:利用热影响区CCT图可以方便地预测热影响组织、性能和硬度变化,预测某种钢焊接热影响区的淬硬倾向和产生冷裂纹的可能性。同时也可以作为调整焊接线能量、改进焊接工艺(焊前预热和焊后热处理等)的依据。
(1)推断焊接热影响区的组织和性能
只要得知被焊钢材热影响区某一部位的实际冷却时间(t8/5),或在某个温度下的冷却速度,将其与该钢焊接热影响区CCT图提供的临界冷却时间、
、
、
或者临界冷却速度相比较,就能判断所研究部位的组织和淬硬倾向。
以成分相当于12Mn的焊接热影响区CCT图为例(见图1.5),对热影响区组织的分析如下。
当时,在热影响区熔合区附近可获得全部马氏体组织,硬度大于395HV。
当时,在热影响区熔合区附近可获得马氏体+中间组织(ZW),硬度为350~395HV。
当时,在热影响区熔合区附近可获得M+ZW+F的混合组织,硬度为274~350HV。
当时,在热影响区熔合区附近可获得M+ZW+(F+P)的混合组织,硬度为195~274HV。
当时,在热影响区熔合区附近仅得到F+P的混合组织,硬度小于195HV。
(2)间接评定钢材的冷裂倾向
①用临界冷却时间评定钢材的抗冷裂性。当实际冷却时间
,焊接热影响区熔合区附近不产生裂纹;而当
时,焊接热影响区熔合区可能产生裂纹。临界冷却时间
已被许多人接受。
②用临界组织含量作为冷裂倾向的判据。使用低氢型焊条焊接低合金钢,必须保证热影响区熔合区附近具有以下组织比例,才能避免产生根部裂纹。
对于抗拉强度σb为600MPa的钢,铁素体+中间组织(ZW)含量应大于40%。
对于抗拉强度σb为700MPa的钢,中间组织(ZW)含量应大于25%。
对于抗拉强度σb为800MPa的钢,中间组织(ZW)含量应大于15%。
③用临界硬度值作为冷裂倾向的判据。根据实际焊接条件,从某低合金高强钢的焊接热影响区CCT图查出其硬度值,与该钢允许的热影响区最高硬度比较,就可以判断其焊接冷裂倾向。实际测定值超过允许的最高硬度时,应考虑焊前预热或焊后热处理措施。
应当指出,热影响区最高硬度试验没有将夹杂物或微观缺陷等因素考虑在内,故不能直接用以判断冷裂倾向,只能做粗略的初步评价。由于焊接连续冷却组织转变(CCT图)是一种间接评定金属焊接性的方法,它不能完全综合实际焊接时各种复杂因素影响。为了可靠起见,在实际工程应用中应配合其他试验。
(七)简析用焊接工艺实际控制焊接线能量技术
建筑钢结构焊接工程中,控制焊接线能量最佳工艺就是“多层多道错位焊接技术”。
多层焊的焊缝质量比单层焊好,多层多道焊的焊缝质量比多层焊好,特别是板厚超过25mm时效果最明显,因此,在厚板焊接时,首选多层多道焊技术。
所谓多层焊技术,不是一次成形,而是多层成形,焊接运条手法允许摆动,焊接厚度一般不控制,适合低碳钢厚板焊接。
多层多道焊就是在多层焊的基础上,焊接手法上不允许摆动,焊接厚度要明确规定,以限制焊接线能量。
1.多层多道错位焊接技术
多层多道错位焊接技术的显著优点就是上一层次对下一层次进行了有效的热处理。受焊接层数的影响,在焊后冷却过程中,焊缝从接近基本金属开始凝固,单道焊的组织为典型的柱状结晶,且共晶粒通常是与等温曲线法向方向(即最大温度梯度方向)长大。由于凝固是从纯度较高的高熔点物质开始,所以在最后凝固部分及柱状晶的间隙处,便会留下低熔点夹杂物。在多层多道焊时,对前一道焊缝重新加热,加热超过900℃的部分可以消除柱状晶并使晶粒细化。因此多层焊比单层焊的力学性能要好,特别是冲击韧性有显著的提高。值得一提的是,多层多道焊对焊接接头的应力、应变控制相当有利,提高了焊接接头的综合性能指标。
多层多道错位焊接技术的主要内容如下。
①规定:GMAW、FCAW-G的每一道焊缝宽不超过5mm(通常是在3~5mm之间)。
②SMAW用AV值来确定每一道焊缝的厚度(AV=一根焊条所焊焊缝的长度/一根焊条除焊条头外的长度),通常AV≥0.5~0.6,见图1.6。

图1.6 焊缝长度与焊条长度(除焊条头)的比值AV
③在立焊位置允许摆动,但限制摆幅。SMAW允许宽度为焊条直径的3倍,GMAW、FCAW-G允许摆动15~20mm。
④多层多道错位焊接技术就是在多层多道焊接技术的基础上,加入焊接接头每一道次错位连接,即接头不在一个平面内,通常错位50mm以上。这种技术特别适合于高强钢厚板的焊接。
2.多层多道错位焊是控制线能量的最佳技术
在工程实践中,人们为了追求工作效率,往往采用大电流的焊接方式。然而这是不靠谱的技术,因为从理论上说,采用大的电流,同时采用高的焊速可以获得理想线能量,能够在提高工效的同时保证焊接“控性”质量。但在实际工作中却不完全是这样,因为如果不采用自动焊工艺,光靠人工操作是达不到理论上的结果的,而在高的焊速情况下,工人操作难度却大大增加,这体现在焊工精神高度紧张,一方面要操纵焊枪使之始终保低电弧状态,另一方面要注意焊缝成形;然而人的控制能力和体力都是有限的,时间一长,焊接速度随之下降,因而逐渐形成了“大电流、慢焊速”的大线能量工艺,使焊接接头综合性能大幅度下降,造成焊接接头综合性能下降,这是应当避免的。
焊接过程中,摆动电弧和采用“多层多道错位焊接技术”的本质,就是线能量控制上的差异,两者技术差别如下。
①摆动运条HAZ高温停留时间长,线能量增加,导致晶粒粗大,影响焊接接头的力学性能,特别是冲击性能显著下降。
②摆动运条由于对焊缝两侧反复加热和冷却,反复对根部焊缝和填充金属加载,影响了焊接接头的综合性能。
③直线运条可使高温在HAZ停留时间短,对焊缝没有反复加载的作用,同时有效地防止偏析。
④屈服强度超过400MPa的高强钢必须采用“多层多道错位焊接技术”,使焊接接头获得良好的综合性能。
上述结论是通过焊接专项试验得出的。
3.工程案例
焊接专项对比试验
①目的:论证运条法控制线能量在高强钢焊接中的适应性。
②试验方法。
a.选取两组平焊试件(材质Q345C),焊缝坡口形式采用MC-BV-1,焊缝间隙为25mm。其中试件F1采用直线形运条法进行焊接;试件F2采用月牙形大摆动运条法进行焊接,焊接位置平焊(F)。
b.选取两组立焊试件(材质Q345C),焊缝坡口形式采用MC-BV-1,焊缝间隙为25mm。其中试件V1采用锯齿形大摆动运条法进行焊接;试件V2采用锯齿形小摆动运条法进行焊接,焊接位置立焊(V)。
③试验内容。
试验焊接参数:对比试验的焊接电流和电压完全一致,由于运条方式不同,焊接线能量(热输入量)计算的结果也不同,见表1.4。
表1.4 焊接工艺参数

④焊接试板外观。
试件F1采用直线形运条法进行焊接,试件F2采用月牙形大摆动运条法进行焊接,焊接位置平焊(F),试板外观见图1.7。

图1.7 平焊对比试验外观照片
其试件V1采用锯齿形大摆动运条法进行焊接,试件V2采用锯齿形小摆动运条法进行焊接,焊接位置平焊(V),试板外观见图1.8。

图1.8 立焊对比试验外观照片
⑤试板力学试验结果。
试板经力学试验,其结果见表1.5、表1.6。
表1.5 拉伸试验结果

表1.6 冲击韧性

力学性能的差异,特别是冲击韧性的差距充分说明了两种运条手法上的差距,由上可知,“多层多道错位焊接技术”显然有很大优越性。
⑥金相试验结果。
平焊试板金相组织见图1.9。

图1.9 平焊试板金相组织
a.F1宏观金相。采用冷酸法对试样焊缝区域进行宏观金相检验,经观察焊缝区、熔合线和热影响区均无微小裂纹、气孔、夹渣等缺陷。
b.F1微观金相。焊缝区:由片状铁素体+珠光体组成,组织均匀分布,晶粒度等级为10.8。热影响区:由针状铁素体+珠光体组成,晶粒度等级为11.5。
c.F2宏观金相。采用冷酸法对试样焊缝区域进行宏观金相检验,经观察焊缝区、熔合线和热影响区均无微小裂纹、气孔、夹渣等缺陷。
d.F2微观金相。焊缝区:由片状铁素体+珠光体组成,组织均匀分布,晶粒度等级为9.8。热影响区:由针状铁素体+珠光体组成,晶粒度等级为10.5。
立焊试板金相组织见图1.10。

图1.10 立焊试板金相组织
e.V1宏观金相。采用冷酸法对试样焊缝区域进行宏观金相检验,经观察焊缝区、熔合线和热影响区均无微小裂纹、气孔、夹渣等缺陷。
f.V1微观金相。焊缝区:由片状铁素体+珠光体组成,组织均匀分布,晶粒度等级为10.3。热影响区:由针状铁素体+珠光体组成,晶粒度等级为10.5。
g.V2宏观金相。采用冷酸法对试样焊缝区域进行宏观金相检验,经观察焊缝区、熔合线和热影响区均无微小裂纹、气孔、夹渣等缺陷。
h.V2微观金相。焊缝区:由片状铁素体+珠光体组成,组织均匀分布,晶粒度等级为10.7。热影响区:由针状铁素体+珠光体组成,晶粒度等级为11.6。
金相组织结果比较,“多层多道错位焊接技术”在立焊位置上的小摆动运条手法仍然占有优势。
⑦结论。
“多层多道错位焊接技术”控制焊接线能量效果良好,在建筑钢结构焊接工程中,应大力推广这一技术。
(八)焊缝“最精准的控形、最少损害的控性”同焊接线能量、焊接电流、焊接电压、焊接速度之间的关系
在建筑钢结构焊接工程中,人们总希望使用最佳的焊接参数,以获得最佳t8/5指标和最好的焊缝“最精准的控形、最少损害的控性”焊接质量。
要把希望变成现实,理论上是简单的,实际上是困难的。有人应用焊接线能量的公式和焊接线能量及焊接电流、焊接电压、焊接速度之间存在正、反比的数学关系,从纯粹计算焊接线能量的角度上理念出发,让焊接电流、焊接电压、焊接速度三个参数在很大范围内变化,认为焊接线能量保持数字上的稳定,焊接线能量保持最佳上、下限,便“万事大吉”,因此,毫无节制的变化三个参数,最后将不得其果。
实际上,这是一个很大的误区,焊缝的“最精准的控形、最少损害的控性”的综合指标的控制不是纯粹的数学计算,因为,焊接线能量确定之后,焊接电流、焊接电压、焊接速度同最佳t8/5一样,有一个最佳配比,这是实现最佳焊接线能量和三个焊接参数最佳配比的双控标准,是人们所追求的目标。
焊接工艺参数从两方面决定了焊缝质量。一方面,焊接电流、电弧电压和焊接速度三个参数合成的焊接线能量影响着焊缝的强度和韧性;另一方面,这些参数分别影响到焊缝的成形,也就影响到焊缝的抗裂性,对气孔和夹渣的敏感性。这些参数的合理匹配才能焊出成形良好无任何缺陷的焊缝。对于操作者来说,最主要的任务是正确调整各工艺参数,控制最佳的焊道成形。因此,操作者应清楚地了解各工艺参数对焊缝成形影响的规律,以及焊接熔池形成,焊缝形成和结晶过程对焊缝质量的影响。
实现三个参数的最佳配比在埋弧焊(SAW)、机器人自动焊工艺(GMAW-CO2、FCAW-G)中,就有比人工操作较严格的要求。同自动焊相比,一个(SMAW)操作技术熟练的工人,控制焊接线能量最佳上、下限比较灵活,工人在焊接过程中,根据焊缝成形影响因素的实际情况,在焊接电流确定的前提下,不断地调整焊接电压(实际上调整电弧的长短)、焊接速度,使最佳焊接线能量上、下限实现动态平衡。否则,达不到焊缝综合指标的技术要求。“多层多道错位焊接技术”指标控制的实质就是根据所焊焊缝综合指标的技术要求,强制焊工在调整好合适的焊接电流前提下,控制焊接电弧电压和焊接速度,在焊接线能量的最佳范围内,实现三个参数的最佳配比,从而获得规定的良好的焊缝成形质量,这样才能使焊缝的综合性能达到优良。
通过焊接工艺评定以及力学金相试验能够确定最佳焊接线能量的上、下限(本书也称宽容度)。确定了最佳焊接线能量后,在最佳焊接线能量上、下限中,要对焊接电流、焊接电压、焊接速度进行合理搭配,只有这样,才能获得理想的焊缝“控形、控性”的综合指标。1.建筑钢结构埋弧焊(SAW)焊接电流、焊接电压、焊接速度等工艺参数的选择
在建筑钢结构制作工厂中,埋弧焊(SAW)是最主要的焊接技术。据不完全统计,一个普通的钢结构制作工厂,80%以上焊接工作量是由埋弧焊(SAW)完成的,因此,抓好埋弧焊工艺,对钢结构制作工厂有着十分重大的现实意义。
埋弧焊的工艺特点如下。
第一,稀释率高。在不开坡口对接缝单道焊或双面焊以及开坡口对接缝的根部焊道焊接时,由于埋弧焊焊缝熔透深度大,母材大量熔化,混入焊缝金属,稀释率可高达70%。
第二,热输入高。埋弧焊是一种高效焊接方法,为获得更高的熔敷率,人们错误地选用大电流焊接,因此,焊接线能量增加,焊接过程中就产生了高的输入热量,结果就降低了焊缝金属和热影响区的冷却速度,延长了t8/5,降低了焊接接头的强度和韧性。
第三,焊接速度快。埋弧焊一般的焊接速度为25m/h,最高的焊接速度可达到100m/h。在这种情况下,焊缝良好的成形不仅取决于焊接参数的合理配比,而且也取决于焊剂的特性,这是埋弧焊(SAW)与其他焊接方式不同之处。
根据上述特点,焊接工艺参数的制定应以相应的焊接工艺试验结果或焊接工艺评定试验结果为依据。
埋弧焊工艺参数分为主要参数和次要参数。主要参数是指那些直接影响焊缝质量和生产效率的参数,它们是焊接电流、电弧电压、焊接速度、电流种类、极性和预热温度等;对焊缝质量产生有限影响或无多大影响的参数为次要参数,它们是焊丝伸出长度、焊丝倾角、焊丝与工件的相对位置、焊剂粒度、焊剂堆散高度和多丝焊的丝间距离等。有关操作技术的参数还包括引弧和收弧技术、焊接衬垫的压紧力、焊丝端的对中以及电弧长度的控制等。
(1)焊缝形成和结晶过程的一般规律
焊缝的形成是焊接熔池建立、熔池连续前移和凝固的过程,焊缝纵向和横向截面的形状是由熔池的瞬态形状决定的。在埋弧焊时,焊丝与母材在电弧热作用下熔化,形成液态金属熔池,其形状和尺寸如图1.11所示。

图1.11 埋弧焊熔池的形状及尺寸
H—熔池最大深度;B—熔池最大宽度;l1+l2—熔池长度
决定于电弧的热能即焊接线能量,熔池尺寸的大小与电流电压的乘积成正比,与焊接速度成反比。
埋弧焊(SAW)焊缝的形状通常是焊缝横截面的形状,如图1.12所示。以熔深H、熔宽B和余高a三个尺寸量表征。为保证焊缝的机械强度,焊缝必须有足够的熔深。但大量的实验结果和生产经验证明,焊缝的熔深H与熔宽B及余高a应成适当的比例。

图1.12 各种焊缝横截面形状及尺寸
Fm—母材熔化的横截面积(mm2);FH—焊丝熔敷的横截面积(mm2);a—余高;B—焊缝宽度;H—熔深
通常焊缝的形状以形状系数φ=B/H和增厚系数B/a来表征。小的形状系数表示焊缝横截面形状深而窄,易出现热裂纹和气孔;大的形状系数表示焊缝横截面浅而宽,易形成未焊透或夹渣。因此,形状系数应有一个合适的范围。对于埋弧自动焊焊缝,通常应将形状系数控制在1.3~1.5(单层),增厚系数应控制在4~8,以使接头具有足够的静载和动载强度;增厚系数过小,即焊缝余高过大,则将降低接头的动载强度。
上述焊缝形状对焊缝质量的影响与焊缝的结晶密切相关。焊缝金属的结晶总是以熔池底部边缘母材半熔化状态的晶粒为晶核,晶体生长反向于散热方向,即垂直于熔池壁方向,故焊缝金属的结晶方向取决于熔池的形状。在形状系数φ小的焊缝中,从两侧生长的晶粒几乎对向相交于焊缝中心,结果使低熔点杂质聚集于该部位而极易诱发裂纹和气孔等缺陷。在形状系数较大的焊缝中,其结晶方向有助于将低熔点杂质推向焊缝顶部,如图1.13(a)所示,因而可抑制裂纹和气孔的产生,从焊缝的纵向截面看,熔池底部越细长,两侧生长的晶粒在焊缝中心的夹角越大,焊缝中心的杂质底部如呈椭圆形,就不易出现纵向热裂纹。因此,控制焊缝形成是防止焊缝缺陷形成的先决条件,富有经验的焊工,可从焊缝的外形判断焊缝内部是否存在缺陷,并通过规范参数的调整,使焊缝达到最佳的成形。

图1.13 焊缝形状对焊缝金属结晶的影响
(2)焊接工艺参数对焊缝成形的影响
影响焊缝成形的主要因素是焊接电流、电弧电压、焊接速度、电源种类及其极性。
①焊接电流。
焊接电流是决定焊丝熔化速度、熔透深度和母材熔化量的最重要的参数。焊接电流对熔透深度影响最大,焊接电流与熔透深度几乎是直线正比关系。图1.14示出I形对接焊和Y形坡口对接焊时,焊接电流和熔透深度的关系曲线。以数学式表示如下:
H=kmI (1.2)

图1.14 焊接电流与熔透深度的关系
式中 H——熔透深度;
km——熔透系数;
I——焊接电流,A。
熔深系数km取决于焊丝直径和电流种类。对于ф2mm直径的焊丝。km=1.0~1.7;对于ф5mm焊丝,km=0.7~3;采用交流电埋弧焊时,km一般在1.1~1.3范围之内。
焊接电流对焊缝横截面形状和熔深的影响示于图1.15,即在其他参数不变的条件下,随着焊接电流的提高,熔深和余高同时增大。焊缝形状系数变小,为防止烧穿和焊缝裂纹,焊接电流不宜选的太大,但电流过小也会使焊接过程不稳定,并造成为焊透或未熔合,因此,焊接电流对于不开坡口对接焊缝,按所要求的最低熔透深度来选定即可,对于开坡口焊缝的填充层,焊接电流主要按焊缝最佳的成形为准则来选定。

图1.15 焊接电流对焊缝横截面形状和熔深的影响
H—熔深;B—焊缝宽度;a—余高
此外,焊丝直径决定了焊接电流密度,因而也对焊缝横截面形状产生一定的影响,采用细焊丝焊接时,形成深而窄的焊道,采用粗焊丝焊接时,则形成宽而浅的焊道。
②电弧电压。
电弧电压与电弧长度成正比关系。在其他参数不变的条件下,随着电弧电压的提高,焊缝的宽度明显增大,而熔深和余高则略有减小。电弧电压过高时,会形成浅而宽的焊道,从而导致未焊透和咬边等缺陷的产生。此外,焊剂的熔化量增多,使焊波表面粗糙,脱渣困难。降低电弧电压,能提高电弧的挺度,增大熔深。但电弧电压过低,会形成高而窄的焊道,使边缘熔合不良。电弧电压对焊缝形状的影响示于图1.16。

图1.16 电弧电压对焊缝形状的影响
B—熔宽;H—熔深;a—余高
为获得成形良好的焊道,电弧电压与焊接电流应相互匹配。当焊接电流加大时,电弧电压应相应提高。
③焊接速度。
焊接速度决定了每单位焊缝长度上的热输入能量,在其他参数不变的条件下,提高焊接速度,单位长度焊缝上的热输入能量和填充金属量减少。因而使熔深、熔宽及余高都相应地减小,如图1.17所示。

图1.17 焊接速度对焊缝形状的影响
B—熔宽;H—熔深;a—余高
焊接速度太快,会产生咬边和气孔等缺陷,焊道外形恶化。如焊接速度太慢,则可能引起烧穿。如电弧电压同时较高,则可能导致横截面呈蘑菇形焊缝。而这种形状的焊缝对人字形裂纹或液化裂纹敏感。图1.18示出这种焊缝中产生的典型凝固裂纹。此外,还会因熔池尺寸过大而形成表面粗糙的焊缝。为此,焊接速度应与所选定的焊接电流、电弧电压适当匹配。

图1.18 横截面为蘑菇形焊缝及裂纹分布部位
(3)SAW焊接参数实例
①焊材选配与准备。焊丝、焊剂等焊接材料与母材的匹配,应符合设计要求及现行国家标准GB 50661—2011《钢结构焊接规范》的规定(见表1.7),焊剂在使用前,应按其产品说明书及焊接工艺文件的规定进行烘焙和存放。
表1.7 常用结构钢埋弧焊焊接材料的选配

①薄板I形坡口对接。
②中、厚板坡口对接。
③供需双方协议。
②焊接工艺评定试验。焊接工艺评定试验应按现行国家标准GB 50661—2011《钢结构焊接规范》的规定实施,由具有国家技术质量监督部门认证资质的检测单位进行检测试验。2.建筑钢结构CO2气体保护电弧焊(GMAW-CO2、FCAW-G)焊接电流、焊接电压、焊接速度等工艺参数的选择
CO2气体保护电弧焊(GMAW-CO2、FCAW-G)是通过电极(焊丝)与母材间产生的电弧熔化焊丝及母材,形成熔池金属。电极、电弧和焊接熔池是靠自焊枪喷嘴喷出的保护气体来保护,以防止大气的侵入,从而获得完好接头。
CO2气体保护电弧焊(GMAW-CO2、FCAW-G)同焊条电弧焊相比,操作技术相对简单,工效提高3倍以上,所以是焊接机器人首选的焊接方式。
(1)焊接工艺及焊接技术
熔滴过渡形式的种类及特点:
CO2气体保护焊有三种熔滴过渡形式:第一种是较小电流、较低电弧电压下的短路过渡;第二种是较大电流、较高电弧电压下的射滴过渡(细颗粒过渡);第三种是介于上述二者之间的半短路过渡(混合过渡)。
①短路过渡。
焊丝端部的熔滴与熔池短路接触,由于强烈过热和电磁颈缩力的作用使其爆断,直接向熔池过渡的形式称为短路过渡。
短路过渡是在较小焊接电流和较低电弧电压条件下发生的熔滴过渡形式。
短路过渡过程如图1.19所示。电弧燃烧后,焊丝熔化并在端头形成熔滴[见图1.19(e)]。由于焊丝迅速熔化而形成电弧空间,其长度决定于电弧电压的大小。随后,熔滴体积逐渐增加而弧长略有缩短[见图1.19(f)]。随着熔滴的不断长大,电弧向未熔化的焊丝方面传入的热量减小,因此焊丝熔化速度降低[见图1.19(g)]。由于熔滴与熔池都在不断地起伏运动着,从而增加了熔滴和熔池的接触机会。接触时即使电弧空间短路[见图1.19(h)、(a)],同时电弧熄灭,电弧电压急剧下降而接近于零,而短路电流开始增大,在焊丝与熔池之间形成液体金属柱[见图1.19(b)]。随着短路电流的不断增大,它所引起的电磁颈缩力强烈地压缩液柱,同时表面张力促使液柱熔池流动,因而形成缩颈,即所谓“小桥”[见图1.19(d)]。随后该“小桥”由于过热汽化而迅速爆断,电弧电压迅速恢复到空载电压以上,电弧重新燃起而重复上述过程。

图1.19 短路过渡过程与电流、电弧电压的关系
t1—燃弧时间;t2—短路时间;t3—电压恢复时间;T—焊接循环周期;Imax—短路峰值电流;Imin—最小电流;Ia—焊接电流(平均值);Ua—电弧电压(平均值)
短路过渡一般适用于ф1.2mm以下的细丝,最稳定的电弧电压范围比较窄,通常为20V±2V的范围。
短路过渡具有如下焊接特点:
a.焊接过程中伴随有少量飞溅;
b.焊道熔深较小而余高较大;
c.焊接变形较小;
d.适合于采用细丝(≤ф1.2mm)进行薄板及空间位置焊接。
②射滴过渡。
熔滴尺寸与焊丝直径相当的情况下,以较高的速度通过电弧空间的过渡形式称为射滴过渡。
射滴过渡是较大焊接电流和较高电弧电压条件下发生的熔滴过渡形式。
在较大焊接电流和较高电弧电压下,随着电流的增加,熔滴尺寸并不增加,反而减小,而且焊丝端头逐步深入到熔池凹坑内,熔滴过渡形式转为接近轴向过渡的所谓射滴过渡[见图1.20(b)]。

图1.20 射滴过渡及半短路过渡示意图
射滴过渡时不再有短路现象发生,焊接过程较为稳定,焊接飞溅比较小,这种射滴过渡国内习惯上称为“细颗粒过渡”。国外常称为“非轴向射流过渡”。
概括起来,射滴过渡具有如下特点:
a.熔滴较细;
b.过渡频率较高,为非轴向过渡;
c.焊道熔深较大;
d.飞溅较小,成形较好;
e.焊丝溶化效率较高,适于采用粗丝(ф1.6mm以上)进行中厚板的焊接。
③半短路过渡。
焊接电流和电弧电压等参数处于短路过渡和射滴过渡之间时,或者说采用中等工艺参数时,即可发生半短路过渡形式。
半短路过渡即是短路过渡的基础上,再增加焊接电流和电弧电压,这时焊丝端头的熔滴随之长大,短路次数减少,短路时间缩短,非短路过渡的比例增加,熔滴呈大滴排斥特点[见图1.20(a)]。这是一种短路过渡与非短路过渡相混合的过渡形式,焊接过程不稳,飞溅也较大。这种过渡形式国内习惯上称为大颗粒过渡,生产中一般不被采用。
(2)主要焊接参数的影响及其合理选择
CO2气体保护焊的主要工艺参数有焊丝直径、焊接电流、电弧电压、焊接速度、气体流量、电流极性和焊丝伸出长度等。
①焊丝直径。
CO2气体保护焊所用焊丝直径范围较宽,ф1.6mm以下的焊丝多用于半自动焊,超过ф1.6mm的焊丝多用于自动化焊接。
通常根据工件的板厚和焊接位置来选择焊丝直径(见表1.8),一定的焊丝直径又与一定的焊接电流相适应(见表1.9)
表1.8 焊丝直径的选择

表1.9 不同直径焊丝的电流范围

ф1.0mm以下焊丝的熔滴过渡以短路过渡为主;ф1.2~1.6mm的熔滴过渡形式可为短路过渡和射滴过渡;ф2.0mm以上的粗丝通常是射滴过渡。
从焊接位置上看,细丝可用于平焊和全位置焊接,粗丝则只适于水平位置焊接。
从板厚看,细丝适用于薄板,可采用短路过渡;粗丝适用于厚板,可采用射滴过渡,采用粗丝焊接既可提高效率,又可加大熔深。另一方面,在焊接电流和焊接速度一定时,焊丝直径越细,焊缝的熔深便越大。
②焊接电流。
焊接电流是影响焊接质量的重要工艺参数,它的大小主要取决于送丝速度,随着送丝速度的增加,焊接电流也增加(见图1.21)。另外,焊接电流的大小还与焊丝伸长、焊丝直径、气体成分等有关,当喷嘴与母材间距增加时,焊丝伸长增加,焊接电流减少(见图1.22)。

图1.21 焊接电流与送丝速度的关系

图1.22 焊丝伸长对焊接电流的影响
焊接电流对焊缝的熔深和焊缝成形均有较大影响。无论是平板堆焊还是开坡口的焊缝,都是随着焊接电流的增加,熔深也增加(见图1.23)。但焊接电流在250A以下时,焊缝熔深较小,一般为1~2mm;当电流超过300A后,熔深明显增大。通常,Ⅰ形对接坡口时,若假设间隙为0时,熔深为100%;间隙为0.5mm时,熔深为110%;间隙为1.0mm时,熔深为125%。如间隙为2mm以上时,就会烧穿。V形坡口对接焊时也有类似的情况。

图1.23 熔深与焊接电流的关系
平板堆焊时,不同焊接电流的焊缝成形如图1.24所示。当焊接电流增加时,焊缝熔深和余高均会增加,而熔宽增加不多。

图1.24 不同焊接电流的焊缝成形
CO2气体保护焊中,针对被焊件的板厚并兼顾焊接位置来选择适宜的焊接电流十分重要。特别是在半自动焊时,通常焊丝较细,因而焊接线能量较低。所以在厚板焊接时,为保证熔深和坡口面的良好熔合,在保证飞溅不过大的前提下,应尽可能采用稍高些的焊接电流。
③电弧电压。
电弧电压时电弧两端之间的电压降,在CO2气体保护焊中可认为导电嘴到工件之间的电压。这一参数对焊接过程稳定性、熔滴过渡、焊缝成形、焊接飞溅等均有重要影响。
短路过渡时弧长较短,随着弧长的增加,电压升高,飞溅也随之增加。再进一步增加电弧电压,可达到无短路的过程。相反,如降低电弧电压,则弧长缩短,甚至引起焊丝与熔池的固体短路。
可以根据所采用的焊接电流的大小,计算出电弧电压的近似值。如焊接电流在200A以下,主要是短路过渡,电流电压可由下式计算:
U=0.04I+16±2 (1.3)
当焊接电流在200A以上时,主要是射滴过渡,电弧电压可由下式计算:
U=0.04I+20±2 (1.4)
粗丝情况下,焊接电流在600A以上时,电弧电压一般为40V左右。
细丝CO2气体保护焊的电弧电压与焊接电流的匹配关系如图1.25和表1.10所示。上述的电弧电压计算公式,在采用加长焊接电缆时,可按表1.11的数值加以修正。

图1.25 合适的电弧电压与焊接电流范围
表1.10 短路过渡CO2气体保护焊电弧电压与焊接电流的最佳匹配

表1.11 加长电缆修正电弧电压参考值

电弧电压对焊缝成形的影响如图1.24所示。电弧电压升高,熔深变浅,熔宽增加,余高减小,焊趾平滑;相反,电弧电压降低,则熔深变大,焊缝变得窄而高。
④焊接速度。
焊接速度与电弧电压和焊接电流之间,也有一个相应的关系,在一定的电弧电压和焊接电流下,焊接速度与焊缝成形的关系如图1.26和图1.27所示。

图1.26 焊接速度与焊缝成形的关系
B—熔宽;H—熔深;a—余高

图1.27 不同焊接速度时的焊缝成形
由图可见,焊接速度增加时,焊缝的熔深、熔宽和余高均较小,即称为凸起焊道。焊接速度若过快,易出现咬边缺陷。为防止这种情况,应适当增加焊接电流、减小弧长,并使焊枪带有前倾角进行施焊。
焊接速度慢时,焊道变宽,甚至出现液态金属导前,造成焊瘤缺陷。
半自动焊时,适当的焊接速度为30~60mm/min。过慢或过快的焊接速度都为操作带来困难。自动焊时,由于能严格控制工艺参数,焊接速度可适当提高。
(3)建筑钢结构GMAW焊丝选配(见表1.12)。
表1.12 常用结构钢CO2气体保护焊实心焊丝选配

(九)工程案例及焊接专项试验研究
1.工程案例
正确应用Av理论控制线能量成功的工程案例
1983~1984年,上海宝钢一期工程——焦化、炼铁、炼钢修建了一批干式煤气柜。当时组成是:焦炉煤气柜一个,高炉煤气柜两个,转炉煤气柜一个。在焦炉煤气柜的底板施工中,由于日方专家(S/V)粗枝大叶,指导失误,中方焊工没有经验,拼抢工期,造成底板发生很大变形,处理十分困难,事实上宣告了焦炉煤气柜底板焊接工艺的失败。
高炉煤气柜容积为15000m3,是当时全国最大的干式煤气柜,也是我国第一次在日方专家(S/V)指导下,自行建造的大型干式煤气柜;施工单位汲取兄弟单位的经验教训,应用曾乐先生的有关焊接应用理论,经过研究和现场大规模试验,创造出“高炉煤气柜底板焊接新工艺”,从而获得成功。赢得了领导和日本专家(S/V)的高度称赞;从此,这套理论和工艺跟随上海宝钢冶金建设公司南征北战,屡战屡胜,屡建奇功。30年后,这套理论和工艺仍然没有落后,完全能够指导相同或者相似工程。
(1)具体内容
控制大面积薄板焊接工程中焊接变形的有效途径
摘要:在大面积薄板焊接工程中,焊接变形量的大小是衡量该工程成功与否的重要标志,也是工程质量好坏的关键,因此控制焊接变形是人们十分重视而致力于研究的课题。本文就宝钢高炉煤气柜底板焊接工程的成功经验和失败教训阐述控制薄板焊接变形的一些行之有效的方法及一些粗浅的见解,旨在类似工程借鉴和参考。
①问题的提出。
控制大面积薄板焊接工程的焊接变形不能单一行事,而应综合治理。实践经验告诉我们,焊接工程中的焊接变形和焊后残余应力并不是两种孤立的现象。两者之间的联系是有机的,它们同时存在于同一焊件,相辅相成又相互制约。能量守恒及转换定理是前述观点最有力的理论依据。
为了清楚地阐明上述观点,我们做一定性分析,并从中提出贯穿整个工程的指导思想。
假设一焊件通过焊接加工获得总能量为W总,焊缝冶金反应所用能量为W有,焊接中能量损失为W损,焊接变形所需能量为ε,焊接残余应力所耗能量为δ残,那么它们之和应用下式表达。
W总=W有+W损+ε+δ残=1 (1.5)
根据式(1.5)得
ε+δ残≈C<1 (1.6)
式(1.6)表达了当焊接工程结束时同一焊件的两种能量存在形式,可以这样认为,ε和δ残之和是小于1的近似常量,在一定条件下两者可以相互转换并相互制约,于是式(1.6)具有工程上的应用价值。
在实际工程中,要想获得成功,只能使ε和δ残都以一种合理的状态同时存在,减少一方必须增加另一方,最好的结果是不至于破坏,而工程又没有过大的ε。这就是高炉煤气柜底板焊接工程的基本指导思想,是被实践证明了的正确的指导思想,为了进一步说明这一思想的正确性,以高炉煤气柜底板工程为例进行分析和阐述。
②高炉煤气柜底板工程概况。
宝钢共有两座15000m3全国最大的干式煤气柜,每个煤气柜底板直径为50m,面积为2059m2,焊缝总长度为1300m。
煤气柜底板焊接工程是十分典型的大面积薄板焊接工程。底板由中心板和内外环缝板组成。中心区钢板厚δ=3.2mm,共用201块搭接而成,外环状板采用δ=9mm钢板,共32块,内环状板采用δ=6mm钢板,其32块对接而成,底板的材质为Q235,其具体组成见图1.28。

图1.28 高炉煤气柜底板组成及分区
由于底板的面积大,技术要求高,焊接工程具有相当的难度。该工程采用S/V推荐的检验标准,要求整体底板水平变形失高允许值为50mm,目标值为40mm,焊缝100%真空检漏。
在工程实践中,由于采用了正确的指导思想,推行全面质量管理,工程取得了十分理想的结果。所有焊缝经过100%的真空检漏,全部合格,两个柜底共测192点,变形失高全部在目标值以下,该工程评为冶金部全优工程。
③焊接工艺及剖析。
正确的指导思想是通过正确的工艺来实现的,对焊接工艺的剖析可以更加清楚地阐述指导思想。
双方在S/V工艺基础上经过友好协商所产生的新工艺,简称中方工艺,见表1.1。表1.1中有两大部分,即底板中心薄板区域和底板环状带。在底板环状带7、8两项中,二号柜施工中,S/V坚持他们的意见而造成工程的失败,外环缝撕裂,立柱变形,造成一定损失,而一号柜获得了成功。表1.13中有关中方的工艺是在工程中得到证实并具有应用价值的工艺。
表1.13 煤气柜底板焊接工艺对照及技术要求

a.中心区焊接工艺。
在底板铺设的同时,全部搭接焊缝进行点焊,使之成为一个整体。
按图1.28,中心区共分A、B、…、H区,按编号1、2、3、…顺序进行焊接。
全部焊缝以中心区向四周推进。
按图1.28各区分界线,待各区焊完后,按1、2、…的顺序焊接。
焊接交叉部留出200mm左右先不焊,其他焊缝焊完后再补焊。
环状带(一号柜)按图1.28中1、2、3顺序焊接。
上述内容同表1.13组成了完整的工艺。
前文所述,减少焊接变形必须增加焊后残余应力,即ε增加δ残减少。增加δ残的外部条件是增加对焊缝的约束,造成约束应力。焊缝全部点固的目的是利用钢板的自身重量来形成对焊缝的约束力。钢板经点焊之后,刚性增加。很显然,通过焊接,δ残增加而ε减少,从而达到减少变形的目的。
工程的实践也证实了这一点。底板连成一体后,在焊接过程中由于δ残增加,各点焊处都要承受一定的拉力,由于焊接不可能完全对称,各部位的约束情况也不完全一致,点焊的强度也不统一。凡是点焊强度差的地方,哪怕是离焊缝很远的地方也有被拉开的危险。当补焊处被拉开后,接近焊缝的变形量往往大于其他地方,可以认为,点焊缝拉开后,约束力降低,焊缝中δ残下降,ε也就相应上升。这一规律的发现检验了我们认识的正确性。
b.焊接参数的确定以及AV值的具体应用。
表1.13中第4条明确指出,控制AV值,限制热输入这是因为:薄板焊接同厚板焊接是同一领域的两个技术分支,最显著的区别是在热输入的控制上,在薄板焊接中热输入越小越好,在焊条电弧焊中热输入的概念十分抽象,难以定量计算,为了使热输入在工程中直接度量,从曾乐先生的《焊接工程学》中引入了AV值这一科学指标,见图1.29。

图1.29 焊条电弧焊线能量与AV(焊接长度/焊条长度)关系
工程实际中,我们按“AV=一根焊条焊接长度/一根焊条的长度(除焊条头)”计算AV值。
由于我们采用了AV值,大大方便了现场的技术管理在工程中,焊工只需按焊脚尺寸焊完一根焊条,用直尺一量即可知热输入的大小,这样把繁杂的计算变得简单易行,使工程质量得到了有效的控制。
为了使AV值同其他参数有一个明确的对照,同时搞清AV值同变形失高的具体关系,我们做了一个模拟试验(试板尺寸为2000mm×3.2mm),其结果见表1.14。
表1.14 现场模拟试验

从表1.14可以得出结论:3号试件的参数是最理想的,于是工程中采用了3号试件的参数,并规定AV≥1的具体指标。同时,也可以发现,如果采用计算的方法,其结果肯定有误差,因此计算热输入的方式在焊条电弧焊中是不科学的,而AV值是有应用价值的。涉及具体焊缝,采用了分段倒退跳焊法,使工程获得比较理想的结果。
c.环状带焊接工艺剖析。
在环状带的焊接中,日方工艺和中方工艺取得完全不同的结果,证明了日方工艺的错误和中方工艺的正确。
表1.13中第8点日方工艺是错误的,他们想用环状板同立柱连为一体后,利用立柱侧板的刚度使纵焊缝的收缩产生对中心底板的拉力,使中心底板的变形失高降低到最低程度。可是他们忽视了两个重要环节:其一,环状板变形的总趋势是直径方向的缩小,对中心底板只有压力而无拉力。其二,实际中坡口间隙过大,最小为8mm,最大为16mm,必将带来很大的收缩量,在高约束条件下,其δ残相当大,足以破坏整体结构,这就是日方工艺错误的关键所在。
为了证实我们的分析,将环缝的收缩量做一定量计算。在对接焊缝中,其收缩量应按下式计算。
式中 ΔY——焊缝的收缩量;
AN——焊缝的截面积;
δ——母材的厚度。
根据式(1.7)可得
ΔYmax=4.28mm
ΔYe=136.98mm
反应在直径方向的收缩应由下式计算:
式中 Δфmax——直径方向的最大收缩量;
D——煤气柜底板直径,取51.2m。
根据式(1.9),可得Δфmax=43.62mm。
计算是依据坡口间隙的最大值计算的,为煤气柜底板直径方向的收缩趋势,完全可以肯定地说,在直径方向有收缩43.62mm的可能性,是足以破坏整体结构的。
很显然日方工艺是错误的,中方工艺的正确还在于理论指导正确。环状板已经超出了我们认为的薄板的范畴,这时焊接变形的大小是次要的,而焊接残余应力的减少是主要的,因此控制δ残减少结构的拘束,从而降低δ残值,在一号柜的施工中获得了成功。
在煤气柜底板焊接中,还有很多辅助工艺,比如:锤击、压轮、卡马等。在众多措施中起决定性作用的有两条:
其一,严格按图1.29的分区及焊接顺序焊接,不得违反;
其二,严格控制AV值,AV≥1。
这两条望同行在工程中进行验证,并严格遵守。
d.结论。
文中提出的指导思想在宝钢高炉煤气柜底板工程中得到充分的应用并获得了成功,工程实践告诉我们,大面积薄板焊接变形的控制必须综合治理。对焊接变形和焊后残余应力的控制必须针对具体板厚进行,其原则是根据板厚来区别。高炉煤气柜的底板属于薄板范畴,超出其厚度则不属于这个范畴,同此变形和残余应力的控制各有侧重,在工程中正是贯穿了这一基本思想而获得成功。本文所述的中方工艺是十分成功的,具有推广价值。
(2)工程案例分析
不可否认:当年(30年前)高炉煤气柜底板焊接工程十分成功,笔者认为成功的关键有两点。
①应用了曾乐先生《焊接工程学》中的AV值理论,把难以准确计算的SMAW焊接线能量指标变成为易于度量的参数,重点是严格控制了焊接线能量,创造了薄板焊接工程的新工艺,从而有效地减少了焊缝收缩量。
目前AV值广泛应用在建筑钢结构厚板焊接技术中,可以说,宝钢高炉煤气柜底板焊接工程中首次使用的AV理论已经开花结果;不过由于人们对焊接技术认识上的误区,AV值的应用尚不普及,特别是没有出现在我国相关专业的教科书中,不能不说是一个遗憾。
②宝钢高炉煤气柜底板焊接工程另一个成功经验是成功地控制了焊接应力应变;施工单位没有钻牛角尖,而是巧妙地运用焊接应力和焊接变形相互转换其值不变的新观点,运用底板自身重量(固定焊在一起),形成约束,成功地限制了焊接变形。
宝钢高炉煤气柜底板焊接工程的这一思想,把宏观力学的控制和微观焊接形变有机地组合在一起,贯穿整个工程,并根据不同的状况,对焊接应力与应变有针对性地选择增加和降低,恰到好处,十分成功,从而形成了新的焊接应用技术理论,这肯定是焊接应用技术理论的一次突破。
目前,这套理论十分成功地在建筑钢结构焊接工程中得到了应用。
笔者认真看完自行完成的文章,确认日S/V意见没有完全错,有必要告诉读者,经认真分析:表1.13底板中心薄板区域第6条,日方S/V指导工艺是正确的,当时宝钢高炉煤气柜没有磨开,所以这项有争议的技术要求没有实施,只有焊缝固定焊被拉开的案例。事实上,只要拉开焊缝,约束变小,焊接变形肯定增加。笔者在以后的工程中采纳了日方(S/V)的观点,取得很好的效果,特此说明。
2.专项试验研究
埋弧焊线能量对Q345qD钢焊接接头性能的影响
(1)研究背景
Q345qD作为桥梁用结构钢,在钢桥建设中广泛应用。目前关于埋弧焊线能量对该钢种焊接接头性能的研究却少见报道,本研究通过焊接接头力学性能试验和显微金相分析,对该课题进行了研究。
(2)研究材料
母材:Q345qD,板厚为16mm。
焊材:焊丝为H08Mn2E,ф4.8mm;
焊剂为SJ101q。
焊接设备:MZ-1000。
母材及焊丝化学成分见表1.15,焊剂的化学成分见表1.16,母材及焊材熔敷金属的力学性能见表1.17。
表1.15 母材及焊丝的化学成分

表1.16 焊剂的化学成分

表1.17 母材及焊材熔敷金属的力学性能

(3)研究方法
图1.30所示为试板组装以及焊接程序示意图。通过改变焊接电流和焊接速度来改变焊接线能量,采用三组试板使线能量由高逐渐下降,然后分析接头力学性能数据和显微金相照片,从而找出线能量对接头性能影响的规律(图1.31)。

图1.30 试板组装及焊接程序

图1.31 试板
三组试板焊接线能量见表1.18。
表1.18 三组试板焊接线能量

试板焊后按照GB/T 11345《钢焊缝手工超声波探伤方法和探伤结果分级》进行超声波探伤,均合格。
(4)试验结果
不同线能量各试板接头的力学性能和冲击性能见表1.19、表1.20。
表1.19 不同线能量各试板接头的力学性能

表1.20 不同线能量各试板接头的冲击性能

图1.32是各试板的焊缝组织,1﹟试板焊缝组织为粗大的板条状先共析铁素体和珠光体及少量针状铁素体,且伴有魏氏组织,柱状晶比较粗大,还有很多合金元素形成的弥散分布的第二相粒子;2﹟试板焊缝组织主要是先共析铁素体和珠光体,针状铁素体组织增加,柱状晶细长晶粒细化,有少许第二相粒子;3﹟试板焊缝组织为细长条状的先共析铁素体和珠光体交错分布,针状铁素体比例进一步增加,晶粒细小均匀,焊缝金属的整体组织细化。

图1.32 试板焊缝组织
(5)试验结果分析
焊接线能量大,高温时间停留长,晶粒扩张、合金元素扩散,时间充分。(其结果)晶粒粗大化,第二相粒子弥散形成;反之,晶粒细化,第二相不能形成。
本实验中1﹟试件焊缝弥散分布着第二相粒子,3﹟试件焊缝晶粒最为细小,而2﹟试件兼具前两者的特征,故2﹟试件的强度最高。韧性只取决于晶粒的大小,三组试件随着线能量的降低,晶粒逐步细化,所以冲击功也是逐步提高的。
(6)结论
①大线能量焊接时,合金元素有充分时间扩散,形成第二相弥散分布,将提高强度,降低线能量焊缝金属晶粒得以细化,强度也将得到保障。
②大线能量焊接时,焊缝中产生沿奥氏体晶界分布的先共析铁素体,线能量降低时,形成以针状铁素体为主的组织。因此,降低线能量,将有利于提高焊缝金属的低温韧性。
③对于16mm的Q345qD钢板,埋弧焊线能量不能超过28kJ/cm。