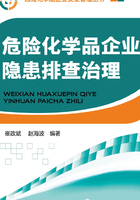
第一章 绪论
第一节 引言
我国有9.6万余家化工企业,其中能够直接生产危险化学品的企业有2.2万多家。因此,安全生产一直是危险化学品企业发展的重要命题。在危险化学品企业中,所有事故的发生都与其生产特点是分不开的,而这些特点存在很多的不安全因素。
(1)物的不安全状态。危险化学品生产中所使用的原料,多属于易燃、易爆、有腐蚀性的物质。目前世界上已有化学物品600万种,经常生产使用的有6.7万种,我国约3万种。这些化学物品中有70%以上具有易燃、易爆、有毒和腐蚀性强的特点,在生产、使用、储运中操作和管理不当,就会发生火灾、爆炸、中毒和烧伤等生产安全事故。
在危险化学品生产进程中,高温、高压设备多。许多危险化学品生产离不开高温、高压设备,这些设备能量集中,如果在设计制造中,不按规范进行,或者质量不合要求,或者在运行操作中失误,就有可能发生灾难性的事故。但在现实中有很多危险化学品生产企业为降低成本、压缩经费,首先削减的是安全生产技术措施经费,导致安全生产投入严重不足,造成设备失修,好多重大、甚至特大隐患得不到治理。一些经济效益较好的危险化学品企业,虽然在安全生产上投入了部分资金,但也是逐步减少;亏损企业则在安全生产上的投入很少甚至根本不投入。在生产现场存在着严重的拼设备和人力的现象。在一些老一点的危险化学品生产企业,存在着设备老化、技术落后、产品单一的问题,生产现场脏、乱、差,以及跑、冒、滴、漏现象十分严重,因而事故隐患也十分突出。
(2)人的不安全行为。目前危险化学品企业发生的生产安全事故中,人为因素造成的事故占事故总数的70%~80%,这其中有员工的安全素质问题,更有企业管理者、特别是安全管理者的综合素质不高的问题。当前由于相当一部分危险化学品企业负担过重,企业主要领导只顾抓市场、抓效益,根本不顾及安全生产和安全管理,当生产与安全发生矛盾时,竟置安全生产于不顾。如因设备运行周期已到、本应停车进行检修,但为了眼前短期的经济效益,不停车检修而使设备带病运行、最终导致重大伤亡事故的例子不胜枚举。企业经济效益不好、职工心理不稳定也是致使事故频发重要原因之一。
还有,大多数危险化学品企业工艺复杂,操作要求极其严格,操作人员稍有不慎,就会发生误操作,人为的隐患也是导致生产事故频频发生的原因之一。众所周知,一种危险化学品的生产往往由诸多个工序、工号组成,而每个工序、工号又由多个化工单元操作和若干台特殊要求的机械设备、电气设备、仪表设备和压力管道联合组成,这样的生产系统工艺流程长、生产技术复杂、工艺参数多、控制要求严,因此,要求任何人、任何情况下不得擅自改动,必须严格遵守操作规程,操作时注意巡回检查,认真记录,纠正偏差,严格交接班,十分注意上下工序之间的联系,及时消除隐患,才能有效地预防各类事故的发生。
(3)管理缺失。很多危险化学品企业虽然也建立了安全生产规章制度,配备了专职安全管理机构和人员。但在实际工作中,制度根本没有落实,机构和人员形同虚设。当前由于相当一部分危险化学品企业存在“经济效益至上”的指导思想,企业领导层或管理层为了追求短期经济效益或个人的“政绩观”作祟,在安全生产、隐患排查治理上表现出麻木不仁、将员工生命当儿戏,当生产和安全产生矛盾、发生冲突时,违章指挥,让职工冒险作业,因此最终导致重大伤亡事故发生的现象层出不穷。
综上所述,在危险化学品企业进行隐患排查治理工作:第一是消除物的不安全状态。第二是消除人的不安全行为。第三是消除管理缺失。这样就抓住了隐患排查治理这个问题的关键,必将产生较为理想的效果。