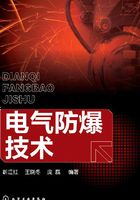
1.6 爆炸事故预防技术
1.6.1 控制工艺参数
1.6.1.1 采用火灾爆炸危险性低的工艺和物料
采用火灾爆炸危险性低的工艺和物料是防火防爆的根本性措施,如以不燃或难燃材料取代可燃材料、采用高闪点的溶剂以减少挥发、用负压低温蒸发取代加热蒸发、降低操作温度等。
1.6.1.2 工艺过程中的投料控制
在工艺过程中进行投料控制,如控制工艺投料量,防止反应失控;控制生产现场易燃易爆物品的存放量,实行按用量领料、限制领用量、分批领料、剩余退库等措施。对于放热反应的工艺,应保持适当和均衡的投料速度,加热速度不能超过设备的传热能力,以避免引起温度急剧升高进而可能导致爆炸事故的发生。应严格控制反应物料的配比,尤其是对反应速度影响很大的催化剂,如果多加就可能发生危险。此外,在投料顺序和控制原料纯度方面都应十分注意,如在聚氯乙烯生产中,采用乙炔和氯化氢作原料,氯化氢中游离氯不允许超过0.005%,因为乙炔遇氯会立即发生燃烧爆炸反应,生成四氯乙烷。
1.6.1.3 温度控制
不同的化学反应都有其最适宜的反应温度,正确控制反应温度不但对保证产品质量、降低消耗有重要意义,而且是防爆所必须进行的控制。温度过高,可能引起剧烈的反应而发生冲料或爆炸。如1991年我国东北某化工厂发生的硝化厂二硝基甲苯车间爆炸事故,就是由于局部温度过高所引起的反应过速导致整个车间爆炸,这次事故造成伤亡124人,直接经济损失达200多万元。温度的控制可以根据不同的生产工艺采取控制反应热量、防止搅拌中断而导致的局部热量积蓄,正确选择传热介质,避免急速的直接加热方式。
1.6.1.4 防止物料漏失
在生产、输送、储存易燃物料过程中,物料的跑、冒、滴、漏往往会导致可燃气体或液体在环境中的扩散,这是造成爆炸事故的重要原因之一,如操作不精心造成的槽满跑料、开错排污阀、设备管线和机泵结合面不紧、设备管线被腐蚀等。各种原因造成的停车事故,如紧急情况下的突然停电、停水、停气等,都可能导致温升发生爆炸。
1.6.2 防止形成爆炸性混合物
1.6.2.1 加强密闭
为了防止可燃气体、蒸气及粉尘与空气形成爆炸性混合物,应设法使生产设备和容器尽可能密闭,对于具有压力的设备,更应注意它的密闭性,以防止气体或粉尘逸出与空气混合形成爆炸性混合物;对真空设备,应防止空气流入设备内部达到爆炸浓度;开口的容器、破损的铁桶、容积较大没有保护的玻璃瓶不允许储存易燃液体,不耐压的容器不能储存压缩气体和加压液体。
为保证设备的密闭性,对危险设备及系统应尽量少用法兰连接;输送可燃气体、液体的管道应采用无缝钢管;盛装腐蚀性介质的容器,底部尽可能不装开关和阀门,腐蚀性液体应从顶部抽吸排出。如设备本身不能密封,可采用液封、负压操作,以防系统中可燃气体逸出厂房。
加压或减压设备,在投产前和运行过程中应定期检查密闭性和耐压程度,对所有压缩机、液泵、导管、阀门、法兰接头等容易漏油、漏气部位应经常检查,填料如有损坏应立即调换,以防渗漏,设备在运转中应经常检查其气密情况,操作压力必须严格控制,不允许超压运转。
接触氧化剂如高锰酸钾、氯酸钾、漂白粉等粉尘生产的传动装置部分的密闭性能必须良好,转动轴密封不严密会使粉尘与润滑油等油类接触氧化,要定期清洗传动装置,及时更换润滑剂,应防止粉尘漏进变速箱中与润滑油相混,避免由于蜗轮、蜗杆的摩擦发热而导致爆炸事故。
1.6.2.2 通风排气
实际生产过程中,要保证设备完全密封有时是很难办到的,总会有一些可燃气体、蒸气或粉尘从设备系统中泄漏出来,生产过程中某些工艺中有时也会挥发出可燃性物质。因此,必须采取其他安全措施,使可燃物的含量降低,也就是说要保证易燃易爆物质在厂房生产环境里不超过最高容许浓度,通风排气是其中的重要措施之一。
对通风排气的要求,主要依据两点考虑:一是当泄漏物质仅是易燃易爆物质,在车间内的容许浓度根据爆炸极限而定,一般应低于爆炸下限的1/4;二是对于既易燃易爆又具有毒性的物质,应考虑到有人操作的场所,其容许浓度只能从毒性的最高容许浓度来决定,因为一般情况下毒物的最高容许浓度比爆炸下限还要低得多。
通风按动力分为机械通风和自然通风,按作用范围可分为局部通风和全面通风。对有火灾爆炸危险的厂房的通风,由于空气中含有易燃易爆气体,所以通风气体不能循环使用,送风系统应送入较纯净的空气。如通风机室设在厂房里,应有防爆隔离措施。输送温度超过80℃的空气或其他气体以及有燃烧爆炸危险的气体、粉尘的通风设备,应用非燃烧材料制成。空气中含有易燃易爆危险物质的厂房,应采用不产生火花的风机和调节设备。
对局部通风应注意气体或蒸气的密度,密度比空气大的要防止可能在低洼处积聚;密度比空气轻的要防止在高处死角上积聚,有时即使是少量也会使厂房局部空间达到爆炸极限。设备的一切排气管(放气管)都应伸出屋外,高出附近屋顶。排气管不应造成负压,也不应堵塞,如排出蒸气遇冷凝结,则放空管还应考虑有蒸汽保护措施。
1.6.2.3 惰化防爆
惰化防爆是一种通过控制可燃混合物中氧气的浓度来防止爆炸的技术。向可燃气体与空气混合物或可燃粉尘与空气混合物中加入一定的惰化介质,使混合物中的氧浓度低于其发生爆炸所允许的最大含量,避免发生爆炸。可燃性混合物不发生爆炸时允许氧的最大安全浓度见表1-12。
表1-12 可燃性混合物不发生爆炸时允许氧的最大安全浓度

根据惰化介质的作用机理,可将其分为降温缓燃型惰化介质和化学抑制型隋化介质。
降温缓燃型惰化介质不参与燃烧反应,其主要作用是吸收燃烧反应热的一部分,从而使燃烧反应温度急剧降低,当温度降至维持燃烧所需的极限温度以下时,燃烧反应停止。降温缓燃型惰化介质主要有氩气、氦气、氮气、二氧化碳、水蒸气和矿岩粉类固体粉末等。
化学抑制型惰化介质是利用其分子或分解产物与燃烧反应活化基团(原子态氢和氧)及中间游离基团发生反应,使之转化为稳定化合物,从而使燃烧过程连锁反应中断,使燃烧反应传播停止。化学抑制型惰化介质主要有卤代烃、卤素衍生物、碱金属盐类以及铵盐类化学干粉等。
对可燃性粉尘爆炸也可以采用类似的惰化方法。表1-13列出了利用氮气作惰化剂时部分常见可燃性粉尘与空气混合物的最高允许含氧量。
表1-13 利用氮气惰化剂时可燃性粉尘与空气混合物的最高允许含氧量

惰化防爆技术主要应用于以下过程或场所。
① 易燃固体物质的粉碎、筛选、混合以及粉状物料的输送等过程中,充入惰性气体以防止形成爆炸性混合物。
② 在可燃气体或蒸气物料中充入惰性气体,使系统保持正压,阻止空气混入,防止形成爆炸性混合物。
③ 将惰性气体用管路与具有爆炸危险的设备相连,当爆炸危险发生时能及时通入惰性气体进行保护。
④ 在易燃液体输送过程中,向容器中充入惰性气体进行保护,避免液体蒸气与空气形成可燃混合气。
⑤ 在爆炸危险生产场所,使用惰性气体对能够产生火花的电气、仪表实施充氮正压保护。
⑥ 在对具有爆炸危险的系统进行动火检修时,先使用惰性气体吹扫,置换系统中可燃气体和蒸气,以避免形成爆炸性环境。
⑦ 在某些生产过程中发生跑料事故时,采用惰性气体对可燃气体进行稀释处理。
表1-14简要说明了不同场合下惰化防爆技术的使用方法。
表1-14 惰化防爆技术的使用场合与使用方法

1.6.3 隔离储存
性质相互抵触的危险化学品如果储存不当,往往会酿成严重的事故。如无机酸本身不可燃,但与可燃性物质相遇能引起着火或爆炸;氯酸盐与可燃的金属相混时能使金属着火或爆炸;松节油、磷及金属粉末在卤素中能自行着火等。由于各种危险化学品的性质不同,其储存条件也不相同。为防止不同性质的物品混合储存接触而引起着火或爆炸事故,应了解各种危险化学品混存的危险性及隔离储存原则,见表1-15~表1-17。
表1-15 混合接触后能引起燃烧的物质

表1-16 形成爆炸性混合物的物质

表1-17 危险物品共同储存的规则

1.6.4 控制点燃源
在工业生产过程中,存在着多种引起火灾爆炸事故的点燃源,如明火、高温表面、摩擦与撞击火花、绝热压缩、自燃发热、电气火花、静电火花、雷击等,对于这些点燃源,在有火灾爆炸危险的场所都应引起充分注意并采取严格的防火措施。
1.6.4.1 对明火及高温表面的控制
明火是指敞开的火焰、火星等。敞开的火焰具有很高的温度和很大的热量,是引起火灾爆炸事故的主要火源。常见的明火包括生产用火、生活用火。生产用火是指生产过程的加热用火和维修用火,如电焊和气焊、喷灯、加热炉、垃圾焚烧炉、非防爆电气设备、开关等。生活用火,如烟头、火柴、打火机、煤气灶、煤油炉等。
(1)在工业生产中为了达到工艺要求经常要采用加热操作,如燃油、燃煤的直接明火加热、电加热、蒸气、过热水或其他中间载热体加热,在这些加热方法中,对于易燃液体的加热避免采用明火,一般采用蒸汽或过热水加热。如果必须采用明火加热,设备应严格密封,燃烧室应与设备分开或隔离,并按防火规定留出防火间距。在使用油浴加热时,要有防止油蒸气起火的措施。
(2)生产过程中熬炼油类、固体沥青、蜡等各种可燃物质,是容易发生事故的明火作业。熬炼设备要经常检查,防止烟道窜火和熬锅破裂。盛装油料不要过满,以防溢出。
(3)在积存有可燃气体、蒸气的管沟、深坑、下水道及其附近,没有消除危险之前,不能明火作业。
(4)在有火灾爆炸危险场所不得用蜡烛、火柴或普通照明灯具,必须采用防爆电气照明。禁止吸烟和携带火柴、打火机等。
(5)喷灯是一种轻便的加热工具,维修时常有使用,在有火灾爆炸危险场所使用应按动火制度进行。
(6)烟囱飞火,汽车、拖拉机、柴油机的排气管火星都有可能引起易燃气体或蒸气的爆炸事故。一般此类运输工具不得进入危险场所,如需进入,其排气管应安装防火罩。烟囱应有足够高度,必要时应装火星熄火器,在一定范围内不得堆放可燃物品。
(7)高温物料的输送管线,不应与可燃物、可燃建筑构件等接触;在高温表面防止可燃物料散落在上面,可燃物的排放口应远离高温表面,如果接近则应有隔热措施。
关于高温表面,一种情况是固体表面温度超过可燃物的燃点时,可燃物接触到该表面有可能一触即燃。另一种情况是可燃物接触高温表面长时间烘烤升温而着火。常见的高温表面有白炽灯泡、电炉及其通电的镍铬丝表面、干燥器的高温部分、由机械摩擦导致发热的传动部分、高温管道表面、烟囱、烟道的高温部分、熔炉的炉渣及熔融金属等。
1.6.4.2 对摩擦与撞击火花的控制
摩擦与撞击往往引起可燃气体、蒸气和粉尘、爆炸物品等的燃烧爆炸事故。如机器上轴承等摩擦发热起火、铁器和机件的撞击、钢铁工具的相互撞击、砂轮的摩擦、导管或容器破裂,内部物料喷出时摩擦起火等,都有可能引起可燃物质的爆炸。因此,在有火灾爆炸危险的场所,应采取防止产生摩擦与撞击火花的措施。
(1)对机器上的轴承等转动部件,应保证有良好的润滑并及时加油,并经常清除附着的可燃污垢,机件摩擦部分如搅拌机和通风机上的轴承,最好采用有色金属或用塑料制造的轴瓦。
(2)锤子、扳手等工具应用有色金属工具制作,如用青铜或镀铜的钢制作。
为防止金属零件等落入设备或粉碎机里,在设备进料前应装磁力离析器。不宜使用磁力离析器的地方如特别危险的硫、碳化钙等的破碎,应采用惰性气体保护。
(3)输送气体或液体的管道,应定期进行耐压试验,防止破裂或接口松脱喷射起火。
(4)凡是撞击或摩擦的两部分都应采用不同的金属制成(如铜与钢),通风机翼应采用铜铝合金等不发生火花的材料制作。
(5)搬运金属容器,严禁在地上抛掷或拖拉,在容器可能碰撞部位覆盖不发生火花的材料。
(6)有爆炸危险的生产厂房,禁止穿带铁钉的鞋,地面应铺不发火材料。
(7)对吊装盛有可燃气体和液体的金属容器用吊车,应经常重点检查,以防吊绳断裂、吊钩松滑,造成坠落冲击发火。
1.6.4.3 对静电火花的控制
生产和生活中的静电现象是一种常见的带电现象。静电的危害性已被人们所认识。在炼油、化工、橡胶、造纸、印刷和粉末加工等行业的生产过程中,由于静电引发火灾爆炸事故的有很多,因此静电预防也就成为安全技术中的一个重要问题。
1.6.4.4 对自燃发热的控制
设备检修和擦洗过程中所使用过的油抹布、油棉纱等,若不及时清理,可能导致棉布热量积聚,达到燃点后即可自燃。因此,浸有油料的棉布等物品必须及时回收,妥善处理。
1.6.4.5 对其他火源的控制
强光和热辐射等,都会导致易燃物的燃烧,如夏天强烈的日光照射会导致硝化纤维自燃,直至酿成火灾爆炸事故。大功率照明灯的长时间烘烤,也是火灾事故常见的原因。
1.6.5 监控报警
爆炸事故预防检测控制系统是预防爆炸事故的重要设施之一,包括信号报警系统、安全联锁装置和保险装置等。生产中安装信号报警装置是用以出现危险状况时发出警告,以便及时采取措施消除隐患。在信号报警系统中,发出的信号常以声、光、数字显示。当检测仪表测定的温度、压力、可燃气浓度、液位等超过控制指标时,警报系统即发出报警信号。安全联锁是将检测仪器和生产设施按照预先设定的参数和程序连接起来;当检测出的参数超过额定范围时,生产设施就自动停止作业程序,达到安全生产的目的。当信号装置指示出已经发生异常情况或故障时,保险装置自动采取措施消除不正常状况和扑救危险状态。