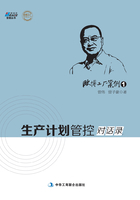
四、第三层觉知:每张订单的状况,一定要清清楚楚
(一)变革前的问题
问题1:订单评审只针对定制
订单评审只针对定制
对常规订单不进行评审,甚至卖场都不要求交期,交期由生产部门说了算。评审也只评审车间的完成时间,不评审其他部门(研发部、品质部、采购部)的工作完成时间。所以,常规订单什么时候需要、什么时候能交,都不确定。
:正常来说,订单评审要求技术部门、品质部门、采购部和车间共同参与,大家共同确定物料到达的时间,工艺图纸、生产报表完成的时间,品质检验标准确定的时间,各车间预计完成的时间,并最终确定出货时间,业务人员再把出货时间反馈给客户。
但在ZG公司,订单评审实际上只是形式。只评审车间的完成时间,不评审其他部门(研发部、品质部、采购部)的工作完成时间。所以,常规订单什么时候需要、什么时候能交,都不确定。
:为什么不在评审过程中,把研发部、品质部和采购部未完成工作的时间确定下来呢?
:因为一旦评审确定,就代表着压力。例如,评审的时候,确定采购的物料具体哪天到,如果物料没有到,管理人员就会有压力。管理人员觉得反正老板也没要求,也没必要让自己承担这种工作压力,所以他们就不评审了。
:本来评审就是要对每个部门进行约束,对每个部门遇到的问题进行预测,然后提前解决它,同时把压力分摊给每个部门。各部门确定的时间点才是我们回复给客户的交期。但现在,很多部门的时间点没有办法控制,交期肯定就被延误了。
问题2:订单状态模糊不清
订单评审后没有确定各车间内部的工序完成时间,没有进行订单汇总,没有表单显示所有订单在各车间的完成时间,各项订单生产到了哪道工序,所在车间是否生产完成、是否有欠数、欠数是多少,都不确定。
:这就导致一个问题,这个问题我们在企业经常遇到,那就是随意回复交期。
例如,客户追货了,本来3月6日要交货的,客户3月4日打电话问业务员这张订单3月6日能不能交。这时会出现两种情况:
第一种,业务员不知道怎么回答,他会说等问过车间再回复。业务员问车间主管这张订单的生产情况,车间主管回答说可能到涂装了吧。再问生产了多少,车间主管说查一下再说。车间主管查来查去,花了很长时间也没有办法得到准确的时间,业务员就只好回复客户一个大概的时间。
第二种,业务员忽悠客户。客户要求3月6日到,业务员就回答肯定能按时到。客户3月4日询问,业务员回答肯定没问题,差不多都入库了,还有十几件在赶工,3月5日能全部入库,他先稳住了客户再说。到了3月6日的时候,他就告诉客户,生产出了一个异常,交期将要延到哪天。
之所以出现这些情况,原因就在于工厂没有一张能够查询订单进度、订单状况的汇总表,业务员只能凭经验、凭感觉去回复客户交期。
:一家工厂整体的生产情况,包括订单的整体状况,没有一个人清楚。例如,车间主管在生产现场看到一个半成品,这个半成品他知道,但这个半成品是哪张订单的,他未必知道;这张订单什么时候要出货,他也未必知道。
我记得我在浙江遇见过一个老板,他和我讲了他和他客户的一些事。他欠一个客户货物,这个客户问他:“你欠我货没问题,但你能告诉我,你还要欠多少天吗?”他答不出来。客户再问:“你还要拖多久?”他说不知道。客户最后问:“那你能告诉我这张订单究竟在你哪个车间做吗?”他还是说不知道。
实际上,很多工厂的老板都不知道接到客户的订单后究竟什么时候才能把货交给客户。订单的进度怎样,物料有没有到齐,各部件完成了多少都是一笔糊涂账,这是我们现在提出要觉知的一个原因。
哪张订单在哪个车间做,一定要清清楚楚。你不知道,是因为你没有注意,这不需要思考,只要觉知就可以了。什么叫觉知?就是去看。现在企业人员缺的不是思考,而是觉知。
问题3:车间根据实际情况生产,订单完成时间未知
PMC下达车间日计划只是根据订单评审后确定的时间下达,车间是否能够按时生产,是否能够按时完成,不确定。
:ZG公司订单评审完成之后,会得出每一个车间大概所需的生产时间,例如3月1日做订单评审,确定3月15日涂装车间要开始上线生产,3月17日生产完成。
到3月14日制订3月15日涂装车间日生产计划的时候,PMC往往怎么做的呢?PMC不管客户要求的出货时间有没有调整,不管前工序做的那些部件到底有没有送到,也不管3月15日涂装能不能做,反正就按照订单评审的时间,在3月14日把3月15日确定的订单安排给涂装车间。
:意思就是到了生产计划要真正安排下去的那一天,PMC不管这个过程中出现多少异常,原来的计划怎么订的现在就怎么下,不做任何排查、不做任何调整,很死板地往下走。
10天以前的计划与现实情况就已经不吻合了,最后生产部门只能说没法按计划执行,只按实际情况来生产。因此,计划和生产就成了两张皮。
问题4:出货情况与订单实际需要匹配情况未知
(1)总装车间当天是否有欠数,欠数什么时间能够完成,什么时间能够全部配套出货,不清楚。
(2)业务部每天下达当天的出货通知单,但是否能够按时出货,不确定!车间生产出来的产品是不是业务部需要的,不确定!
:曾经有一家企业的老板娘告诉我,一到旺季她就很辛苦。为了追货,老板娘经常要守在工厂。明天要出的货,今天要带着业务员各个车间追,并且晚上必须全部入库,这样她才能安心回家。
:其实大家,包括老板,都到最后的那个果上才去追,拼命地追,但不在前面的排查、预防等上面用力。就像佛家说的,在果上用力,不在因上去求。就是该做的排查不做、该调整的工作不调整,到了最后,大家像消防队员一样。不做消防,只做救火,最后的结果肯定就是这样。
(二)变革后的动作
:欧博项目组的老师结合欧博300多家咨询案例的实战经验,通过现场调研,与企业管理人员研讨后确定新的动作(如表1-1所示)。
表1-1 新确定的管理动作

针对问题1:订单评审表
:从表1-2大家可以看到,研发部的图纸什么时候完成,还要研发部门的主管在评审表上签字确认。签字确认的目的是如果没有按时完成,要追究责任。采购部、品质部和PMC都要在订单评审过程中确认各自工作的完成时间。
表1-2 订单评审表

:订单评审由哪个部门主导?
:计划物控部(PMC)主导。
:这是不是就意味着计划物控部可以凌驾于其他几个部门之上呢?
:不是,计划物控部的职责权限企业的相关文件有规定,只能在文件规定的范围内对各部门进行约束。
:实际上,计划物控部更多的是对其他相关部门进行相关事情的管控,而不是对人的管控,因此可以将其定位为管事,而不是管人。它跟其他部门如品质部、研发部、生产部是平行部门,但在事情上可以对这些部门进行管控,就像人力资源部门管控跟人力资源相关的事情一样。
可能很多企业会问为什么要设一个计划物控部呢?厂长安排这一切不可以吗?
:原因很简单,厂长精力有限,无法考虑到每一件事。例如,下达一份生产计划之前要做很多排查动作,而厂长不可能每天去查去问每一款物料都到了没有,他没这精力,没有时间去完成这样的细致工作。
:而且厂长的工作除了管事之外,还要管人。管各个车间的主管,管人各方面的问题,包括人的心态、效率等。所以,PMC等于分担了很大一部分厂长的工作。
:PMC在文件规定的范围内要求各个部门的时候,各个部门的人员不认同,不按照PMC要求的方法做。PMC没有权力直接处理其他部门的人员,它只能把相关情况反馈给厂长,这个时候厂长的作用就体现出来了。
:厂长居中协调。
针对问题2:主生产计划表及跟进表
:针对各项订单生产到哪道工序,订单所在车间各工序是否已生产完成,是否有欠数,欠数是多少,不确定的问题。欧博项目组推出的动作是:第一,对订单状态进行重新评审和梳理,建立主生产计划表。在主生产计划表中形成交期分解,明确每一个车间的上线时间、完成时间以及尾数,数据每天更新(如表1-3所示)。
表1-3 主生产计划表

:从表1-3中,大家可以看到有客户订单号、生产批号、型号,同时确定了交期和每一个车间的完成时间。
以10713031308订单为例,客户要求的交期是4月8日,那么木工车间3月25日就要上线,3月31日完成;涂装车间的上线时间是4月1日,完成时间是4月5日;总装车间是4月6日上线,4月8日完成生产,最后保证出货。这就是我们讲的交期分解。
通过订单评审,把评审出来的时间填入表1-3中。这张表要每天更新,计划物控部门要根据各个车间实际生产的订单来更新。
:可以这样理解,通过订单评审,就有了每一张订单在每一个部门的时间节点,就可以确定生产部门的上线时间、下线时间,然后把这些汇总,就形成了一份主生产计划。主生产计划表把订单的情况列得详详细细、清清楚楚,而且每天更新。
:所以以前客户问企业什么时候能交货时,业务员也没法回答,他只能忽悠。现在有了这张表,事情变得简单了。这张表要与计划物控部门、车间部门和业务部门共享。车间部门和业务部门看着表,马上就能查到每一张订单的进展情况,如产品在哪里加工,加工了多少,整个情况怎么样等。
:这张表使像黑箱子一样的工厂,一下子变得透明。业务员需要与客户及时沟通的就及时沟通,客户需要承诺,他也可以跟客户做出承诺,不能承诺的,他就不会去瞎承诺。甚至老板通过这张表也明白整个工厂的走势怎么样,差在哪里了,需要他做什么。所以,这张表对于整个工厂来说就是一个指挥棒,非常重要。
关于表格的每天更新,我还要补充一下。因为我们发现很多企业也有类似的表格,但被制订出来后没人管,一个月才更新一次。这样管理人员就不可能每天觉知其中的问题,中间发生了什么就只能靠想了,这是欧博最反对的。应该每天更新一次,清清楚楚。
:其实所有的计划都是从这张表中分解出来的。这张主生产计划表是谁使用呢?是PMC经理。这张主生产计划表将每一张订单的每一个产品分解到了每一个车间。表1-4是木工车间对主生产计划表的跟进表,PMC每天根据生产情况进行更新,将订单的状况分解到工序,通过这张表我们可以了解订单的产品部件的生产状态。

表1-4 ZG公司木工车间进度表
:表1-4与主生产计划表有什么区别呢?它们格式是一样的,但这张表更详细。在表1-4中,产品名分解到了每一个部件、每一道工序,从开料到CNC、面板,冷压、封装等,每一道工序的开工时间都在表中列明。
这张表由谁来使用呢?各个车间的计划员,这就相当于主生产计划又在各个车间内部分解了一次。通过这张表,业务员就可以知道,这张订单的这种产品的这个部件到底在哪一个车间的哪一道工序,在这道工序还欠多少。
:主生产计划表是针对车间的,主生产计划跟进表是针对工序的;主生产计划表是部门经理使用,或者PMC使用,但主生产计划跟进表是车间的计划员使用,而且主计划完成的时间点也来源于这张跟进表。因为跟进表是根据现场的每一个部件填写的,它反映了现场部件的信息,再汇合到主计划表中,然后让各个部门分享。主生产计划表以大套小,粗中带细。通过主生产计划表和主生产计划跟进表,企业最基层的管理人员和中层管理人员就可以完成一次次配合。
:通过前面三个动作,我们可以清楚地了解订单的生产状态,如生产到了哪道工序、欠多少、什么时候能出货等。把一张订单从最初的出货时间分解到各道工序的上线时间以及完成时间,我们称之为前推。
:为什么叫前推呢?
:因为它从订单接收开始,通过订单评审,一步一步推导出各道工序和车间的完成时间,从前往后推。
:这个“推”应该有两层意思:一方面指管理动作从接单到评审、交期分解、主计划时间节点的形成,到主计划跟进表的形成,管理动作发挥了推动的作用;另一方面,从物料的情况来说,从开料到后面的每一道工序,物料是推着往后走的。管理动作一层一层往后推进,物料的移动也一步一步往后推进。
针对问题3:滚动计划、层层排查
动作1:周出货计划
:针对问题3,我们的第一个动作是,根据订单评审、交期分解实施周出货计划,业务部每天滚动制订后7天需出货订单的出货计划。
ZG公司以前也有周出货计划,但他们是这周制订下周的。例如,这周五制订下一周的出货计划,完成之后就不动了,而我们要求他们每天制订后7天的滚动出货计划。例如,3月1日要制订3月2日至3月8日的出货计划,3月2日要制订3月3日至3月9日的出货计划,也就是出货计划每天往后滚动7天,为什么要这样做呢?
表1-5 3月25日至3月30日的周出货计划

因为这家公司,特别是很多做内销的企业,客户要求的出货时间是经常变动的。例如,这周五跟客户确定交货日期,客户要求下周四交货,但可能到了下周一,这个客户又将交货日期从周四提前到周二。如果这周制订下一周的计划,就容易导致我们没有办法真正按计划进行生产,我们所制订的日计划就不会很准确。
:7天滚动的目的就是把各种异常综合起来,便于快速反应。如果按照他们以前制订计划的方式,要一个星期才能调整一次,而我们这种滚动方法,可以每天考虑客户的新信息、新异常,然后相应地调整计划。
:这也是制约业务部的一个动作,它逼着业务部去跟客户频繁地确认某张订单具体的出货时间,这样也减轻了生产部的压力。以前生产部没有办法按时出货,业务员不管三七二十一会经常责备生产部。在工厂,由于业务部直接为企业带来收入,所以,老板往往更多地偏向业务部,生产部就会有很多抱怨。
:原则上要求业务部每天都要跟客户确认出货时间,即使不一定每天都要打电话,但至少要给客户一种感觉,一有异常或变动要马上反馈给我们的业务,不然业务没有及时通知生产部门,要挨批。
给业务员压力,让他时刻关注市场的变动,企业就会把握生产的主动权。不然按以前的方式,业务员不频繁跟进客户,异常不能及时被解决,影响准交率。
动作2:车间生产周计划
:第二个动作,PMC每周根据主计划以及7天滚动的出货计划形成车间生产周计划,对各个车间每周的生产任务进行明确。周生产计划从哪里来?根据主生产计划,因为主生产计划已经明确了每一张订单在每一个车间的生产时间,然后再结合7天滚动出货计划。
例如,做面漆车间生产周计划的时候,计划员首先从主生产计划里面找到3月25日至3月30日面漆车间要生产的东西,并形成计划,但这个计划是不是就可以下达给车间了呢?肯定不行,因为还要结合出货需求。主生产计划里的出货时间是订单评审的时候确定的,而制订车间周生产计划已隔了一段时间,这期间客户的出货时间可能会有调整。以前客户可能3月31日要货,但现在制订3月25日至3月30日的计划时,客户可能3月27日就要。这时就必须结合7天滚动出货计划,对周计划进行调整。
:也就是说,假如我的生产主计划是以月为单位,分为四周,我就不能在第三周的时候,将主计划里原来的第三周排程作为我第三周的生产计划。原因是订单评审时制订的第三周计划,在生产计划已进行了两周后,这中间可能已经发生了各种异常,计划员必须考虑这些异常,才能形成第三周的周计划,而不是将原来主计划表中的第三周内容作为第三周的周计划。
所以,这种计划模式最大的特点是一方面考虑了原来的计划,另一方面也考虑了过程中的变化,把计划和变化进行了统一,形成实际的计划,而按企业以前的做法完全行不通。
:也没办法执行。
:因为没有考虑变化。我们经常说计划没有变化快,很多企业就以此为理由,不做计划,或者死板地硬推计划,这些都不可取。我们要把计划和变化结合起来,结合方式就是这种滚动式计划。
:在我们欧博的计划模式里面,把针对问题3所做的两个动作叫作后拉。根据出货需求确定前面的生产需求,确定生产部到底要做什么,出货拉动了生产。
:前推是由订单接收时形成的订单评审推动的,所以它是起点。而后拉由最终的出货拉动,因为订单接收和最终出货有时间差,中间会有很多异常,所以后拉就是根据客户的最终出货时间对前工序进行拉动,前工序要按照出货的要求加工。既考虑前推,又考虑后拉,综合起来叫前推后拉。
:到这里为止,我们制订出了一周的生产计划,但这个计划是不是真正可行的呢?不是,为什么?周出货计划是结合出货做的,只是保证了周生产计划里面的东西是出货所需要的,但不代表车间一定能够生产,因为我们还要考虑物料的问题,那么接下来的这几个动作是针对物料进行的频繁排查。
保证计划执行动作1:滚动出货计划排查表
:那么针对这个问题的第一个动作是,每天排查滚动出货计划排查表,将评审的交期、要紧急出货的订单做为排查的重点。
:表1-6是4月2日至4月11日需要出货的计划表,根据出货计划排查出来的结果,在表中会有体现。
表1-6 4月2至4月11日出货计划排查表(部分)

以第一张订单为例,它的出货时间是4月2日,仓库没有欠数,那就表示这张订单所有需要的产品已经入库了,4月2日可以正常出货。
再看99912112101订单(有阴影一栏),它所要求的出货时间是4月3日,通过排查我们发现仓库还欠100件,那么这100件是哪个车间欠的呢?从表里可以看到,是总装车间。通过这种排查,我们就能很清楚地知道即将出货的产品到哪种程度了。
:滚动出货计划排查表的作用就是弄清楚出货的真实状况,不断地排查就能够查到产品所处的状态,我们就能够明白产品什么时间可以生产出来,把情况搞清楚了,我们才能准确地安排生产任务。
保证计划执行动作2:物料日排查表
:第二个动作是制订物料日排查表,召开物料对单会,每天PMC与车间核对和排查订单的生产进度,以及各车间后3天生产计划所需物料的情况。
通过出货计划和滚动排查,我们确定了今天、明天和后天生产部门要加工的订单和产品。通过物料排查查什么?通过物料排查确定这些订单和产品能不能生产,查前工序有没有把部件和产品按时送至后工序,能不能及时送到车间进行生产。如果都没有问题,那计划就可以准确地传达下去。
:周出货计划排查表检查车间,物料日排查表检查工序,它们通过工序对单知道订单部件在哪道工序生产。物料日排查表和各车间的主生产计划进度跟进表的内容是一样的,也就是说它比周出货计划排查表查得更细。
:出货计划排查表保证出货计划要在3天以内发给车间,保证生产和出货的对应性。但车间能不能生产不知道,因为还不能确定前工序能不能把物料送过来。
假设3月3日要生产A订单,3月1日排查的时候把生产计划发给面漆(涂装)车间,但面漆车间是不是能做还不一定,为什么?因为要考虑前工序能不能把物料送过来。物料对单会其实就是要确定3月1日面漆车间要生产的物料木工车间能不能及时交过来,如果能送过来,那么A订单的任务就能安排给面漆车间了。
保证计划执行动作3:工序滚动日计划
:第三个动作是根据出货计划排查物料日排查结果,PMC每天制订工序滚动日计划(如表1-7所示),并保证计划是能够执行的。“能够执行”指什么?指的是这个计划是对应3天以后出货内容的,这个计划安排给车间不会出现欠料,是完全能够生产的,完全可以考核的。
表1-7 车间生产工序滚动日计划表

:从表1-7大家可以看到,制订计划的时间是3月15日,安排的是3月16至3月18日的生产任务,填制订计划的时间是便于计划员掌握时间界限。表里有“制约”一项,表示谁检查这个动作、谁保证这个动作能够落实。“责任”项的意思是如果检查发现谁没有按要求做,谁就要承担相应的责任。
:这张表有三个要素:第一,做什么事情、怎么做标准要明确;第二,做的过程中,做了没有、做到什么程度要有人检查,有人制约;第三,做了怎么样,不做又怎么样,要有奖罚。标准、制约和责任三个要素缺一不可,这是车间生产工序滚动日计划表与一般的表单不同的地方。
车间生产工序滚动日计划表为什么要有三个要素?因为我们要考虑人的执行问题,否则生产的人不按照表单要求,你也不能强制要求他。另外,还要把规定要做的事情在表单上写得清清楚楚。我想问一下,3天的计划是不是也是滚动的?
:是的。
:就是说3月15日制订3月16日、3月17日和3月18日的计划,3月16日制订3月17日、3月18日和3月19日的计划。那为什么要滚动呢?
:这也是给我们自己一个提前期。例如,假设3月15日制订3月16日、3月17日和3月18日的计划,要求3月16日的计划百分之百冷冻。冷冻的意思就是不允许调整,不管是业务部想插单,还是车间不按计划做,都不行,车间只能完成3月16日规定的任务。
:它为什么可以冷冻呢?
:前面的排查动作保证了这一天(3月16日)的任务是可执行的,它是根据出货进行的。
:也就是经过排查,排除了物料异常,排除了设备异常,排除了品质异常,人员也是正常的,前工序到时间就一定会把东西送到后工序,后工序车间就必须完成任务。
例如,3月15日排查3月16日、3月17日和3月18日的计划,3月16日又要排查3月17日、3月18日和3月19日的计划,3月17号又要排查3月18日、3月19日和3月20日的计划,那么就等于3月18日的计划在真正冷冻之前已被排查了三次。3月18日要生产的产品物料有没有,设备是否正常,人员够不够,通过提前3天的不断排查,排除了各种异常,那么3月18日的计划就必须完成。排查是确保计划执行的关键动作,3月16日是完全被冷冻的,那么3月17日呢?
:3月16日是100%的冷冻,3月17日是60%的冷冻,3月18日是40%的冷冻。或者认为不可能制订日计划,因为在他们看来,每天把任务安排的很准确是很难的。
:要不断地考虑和综合各种异常。为什么很多企业觉得没有必要制订日计划,或者认为不可能制订日计划,因为在他们看来,每天把任务安排的很准确是很难的。
:为什么要做日计划?因为只有做了日计划才能每天对车间管理人员进行评价考核,以日为单位对他们进行规范管理。我们说的日计划与大家平常讲的日计划有什么区别?我觉得区别是我们对日计划会进行考核。很多企业也制订日计划,但真要对日计划进行考核,车间部门不愿意。
:我去过很多企业,这些企业说自己也在制订日计划,我马上就问他们有考核吗?我为什么要这样问?因为这样一问就能问出真相,就能知道他们的日计划是真的还是假的。大多企业因为日计划不真实,所以不敢考核。他们也只是把日计划下给车间由车间看着办。如果真搞考核,大家就集体做假。那为什么他们的日计划不能考核呢?不能考核说明日计划没有办法真正执行,它卡在什么地方呢?
:主要卡的地方就是没有滚动排查动作。
:对,因为如果是前工序导致的异常、采购导致的异常影响了日计划,那么企业对车间员工进行考核就不公平。PMC把计划安排下去之前,特别是把日计划安排下去之前,要通过不断地排查排除可能出现的异常,为日计划的执行和完成做各种准备,也就是服务在先、管控在后。很多企业做生产计划的人没有这样的思想:在制订计划、下达命令之前还要为计划的达成做很多服务工作。排查动作体现了欧博计划模式的管理理念:服务在前,管控在后。
针对问题4:车间清尾日计划
:针对总装车间当天是否有欠数,不确定欠数什么时间完成的问题,我们的动作是PMC每天根据总装完成情况制订车间清尾日计划,对没有按计划完成及紧急出货的订单进行重点跟进。
表1-8是涂装车间面漆组的清尾日计划表。清尾是什么意思呢?
表1-8 涂装车间面漆组清尾日计划表

例如,今天给面漆车间安排10张订单,要求生产100个产品,3月16日只完成了93个产品,还有7个没完成,这7个就是3月16日这天生产的尾数。针对这个尾数,我们要制订清尾计划,将尾数安排到17日的任务里去,而且清尾计划优先于日计划。
第二天(3月17日)面漆组首先要完成的是清尾计划,再按照车间下达的日计划进行生产,这样就保证了各订单每个产品的生产进度能够和出货时间吻合。
:所以关于完成计划,可以用两句话来概括:一是滚动排查、前推后拉;二是两头卡、中间清。其实,尾数是制订生产计划的老大难问题,很多企业都对尾数问题一筹莫展,不知道怎么解决。
很多中小企业想完全杜绝尾数,但基本上做不到,为什么呢?因为品质合格率不高。由于各道工序可能产生品质异常,如返工、返修,甚至报废,使品质极其不稳定。而这些品质异常会导致包装时欠数,就是我们所说的尾数。
解决尾数靠什么?靠我们查清楚每道工序究竟出现了多少异常,产生了多少损耗或返工。查清楚后,该补的补,需要返工的马上返工。
只有一道工序一道工序地清(清尾),每天查每道工序,查完以后马上补,把这些尾数、欠数补到位,才能在包装、总装的时候杜绝欠数。也就是说,解决尾数问题要靠每天清理每道工序。
:根据前面的这么些动作,最后形成计划流程的简图(如图1-5所示):

图1-5 计划流程简图
如图1-5所示,通过各种动作的运作,形成了ZG公司从订单接收到成品出货订单处理新的主要动作。有灰色底纹的部分是增加的动作,增加了交期分解、生产主计划、周出货计划、清尾日计划、异常处理和订单结案,字体加粗部分是在原有基础上进行了调整、优化和完善的部门。