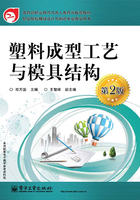
1.2 塑料的性能
塑料的性能包含使用性能和工艺性能,使用性能体现塑料的使用价值;工艺性能体现塑料的成型特性。
1.2.1 塑料的使用性能
塑料的使用性能包括物理性能、化学性能、力学性能、热性能、电性能等,这些性能都可以进行衡量和测定。
1.物理性能
(1)密度:单位体积中塑料的质量(重量)。塑料的密度一般比金属的密度小,在0.83~2.20g/cm3之间。
(2)透湿性:塑料透过蒸气的性质,用透湿系数表示。在一定的湿度下,试样两侧在单位压力差情况下,单位时间内在单位面积上通过的蒸气量与试样厚度的乘积。
(3)透气性:塑料阻止空气穿过的性质,是衡量塑料制品密封能力的一个指标。
(4)吸水性:塑料吸收水分的性质,用吸水率表示。吸水率是指在一定温度下,将塑料放在水中浸泡一定时间后质量(重量)增加的百分率。
(5)透明性:塑料透过可见光的性质,用透光率表示。透光率是指透过塑料的光通量与其入射光通量的百分比的比值。
2.塑料的化学性能
(1)耐化学腐蚀性:指塑料耐酸、碱、盐、溶剂和其他化学物质腐蚀的能力。
(2)耐候性:指塑料暴露在日光、冷热、风雨等气候条件下,保持其性能的能力。
(3)耐老化性:指塑料暴露于自然环境或人工条件下,随着时间的推移,不产生化学结构变化,并保持其性能的能力。
(4)光稳定性:指塑料在日光或紫外线照射下,抵抗褪色、变黑或降解的能力。
(5)抗霉性:指塑料对霉菌的抵抗能力。
3.塑料的力学性能
塑料的力学性能主要包括抗拉强度、抗压强度、抗弯强度、断裂伸长率、冲击韧度、抗疲劳强度、耐蠕变性、硬度、摩擦系数及磨耗等。
磨耗是塑料试样与特定的砂纸摩擦一定时间后损失的体积,其他指标与金属的力学性能指标有相似的意义。
4.塑料的热性能
塑料的热性能主要包括线膨胀系数、导热系数、玻璃化温度、耐热性、热变形温度、熔体指数、热稳定性、热分解温度、耐燃性等。
(1)玻璃化温度:塑料从黏流态或高弹态(橡胶态)向玻璃态(固态)转变(或反向转变)的温度。
(2)耐热性:塑料在外力作用下受热而不变形的性质,用热变形温度或马丁耐热温度衡量。
提示
测定热变形温度和马丁耐热温度的原理:将塑料试样置于等速升温的环境中,并在试样上施加一定的弯矩,测定其达到一定弯曲变形量时的温度。热变形温度适合测量常温下是硬质的塑料和板料的耐热性。马丁耐热温度适合测量耐热性小于60℃的塑料。
(3)熔体指数:热塑性塑料在一定的温度和压力下,其熔体在10min 内通过标准毛细管的质量,以g/10min表示,是反映塑料在熔融状态下流动性的一个量值。
(4)热稳定性:塑料在加工或使用过程中受热而不分解变质的性质。
(5)热分解温度:塑料在受热时发生分解的温度,是衡量塑料热稳定性的一个指标。塑料加热时应控制在此温度以下。
(6)耐燃性:塑料接触火焰时抵制燃烧或离开火焰时阻碍继续燃烧的能力。
5.塑料的电性能
塑料的电性能包括表面电阻率、体积电阻率、介电常数、介电强度、耐电弧性、介电损耗等,是衡量塑料在各种频率的电流作用下表现出来的性能。
1.2.2 塑料的工艺性能
1.热固性塑料的工艺性能
(1)收缩性(缩水):热固性塑料在高温下成型后冷却至室温,其尺寸会发生收缩的特性称为收缩性,用收缩率表示,其表达式为:δ=(Lm−L1)/L1×100%。式中δ为塑料的收缩率,Lm为模具在室温时的尺寸(mm),L1为塑件产品在室温时的尺寸(mm)。
① 造成收缩的原因。
a.化学结构发生变化:热固性塑料在成型过程中,分子结构从线型过渡到体型结构后密度增大,必然导致体积减小,从而造成收缩。
b.热收缩:塑料的膨胀系数要比钢材大,其收缩也比钢材大,故塑料制品尺寸要比模具尺寸小。
c.弹性恢复:塑料在型腔中成型时有很大的压力,一旦开模后压力消失,塑料制品产生弹性恢复而胀大,可抵消一部分收缩。
d.塑性变形:当模具打开时,塑料受的压力降低,但模具仍紧压制品的四周,可使制品局部变形,造成局部收缩。
② 影响收缩,造成收缩率波动的原因。
a.塑料的种类:不同的塑料,由于其分子结构的差异,其收缩是不同的。同一种塑料,由于分子量和填料的品种含量的不同,收缩率也有差别。一般的树脂含量高,分子量大、填料为有机物时收缩较大。
b.塑料制品结构:同一种塑料,由于制品的形状、尺寸、壁厚、有无嵌件、嵌件多少、如何分布等因素也会造成收缩变化,使收缩率波动。一般制品越复杂、壁薄、嵌件多且均匀分布的收缩率较小。
c.成型工艺:预热情况、成型温度、模具温度、成型压力、保压时间、冷却速度等也会使收缩率产生波动。一般地,有预热、成型温度较低,压力较大,保压时间长的产品收缩率较小。
d.后收缩和后处理收缩:塑料件在成型时,由于受到成型压力和剪切应力作用,加上各向异性及成型工艺影响,使产品存在残余应力,脱模后使产品尺寸发生变化,称为后收缩。有时产品在成型后,需要进行热处理,也会使尺寸发生变化,引起收缩,称为后处理收缩。
e.其他原因:塑件的收缩具有方向性。塑料成型时其流动方向上收缩较大,垂直于流动方向上收缩较小。填料分布不均匀,也会造成收缩不均匀。
总之,引起收缩和造成收缩波动的原因很复杂,设计时必须全面考虑,从而获得合格的产品。
(2)流动性。塑料在一定温度与压力下,充满模具型腔的能力称为塑料的流动性。衡量塑料流动性的指标通常用拉西格流动性表示。测定拉西格流动性的标准压模,如图1.1所示。将待测塑料预压成圆锭置于压模上端的圆柱孔中,将其加热至一定温度,给顶部的活动柱塞一定压力,熔融的塑料会从下端的模孔中挤出。我们测量其挤出的长度即为拉西格流动值,单位是mm。数值越大,流动性越好。

图1.1 拉西格流动性测定用压模
① 影响塑料流动性的因素。
a.不同品种的塑料,其流动性不同。
b.同种塑料由于其分子量、填料的性质和含量、颗粒的形状与大小、含水量、增塑剂和润滑剂含量的不同,其流动性也不同。一般来说,树脂分子量小,填料呈球状,增塑剂含量高的塑料流动性大。同种塑料的流动性分成三等,即拉西格流动值为100~130mm、131~150mm、151~180mm三个等级。
c.塑料的流动性还与模具结构,表面粗糙度,预热成型工艺条件(温度,压力)等有关。
② 塑料流动性对塑料制品的质量、模具设计及成型工艺的影响。流动性过大,易造成溢料,制品内部产生疏松、粘模等问题,造成脱模和清理困难;但流动性太小,会造成充模困难,产生缺料等现象;所以应根据制品的结构、尺寸来选择适当流动性的塑料。模具设计时根据塑料的流动性来考虑分型面、浇注系统和进料方向。成型工艺的条件也对流动性产生影响,例如,提高成型温度和压力时,会使流动性增大。
③ 提高塑料流动性。在塑料中加入增塑剂和润滑剂,加大浇注系统的截面,提高表面粗糙度,减少转角,提高成型温度和压力等。
(3)比容和压缩率(压缩比)。比容是单位质量塑料所占的体积,单位是 cm3/g。压缩率是成型前塑料原材料的体积与成型后制品的体积之比,其值恒大于1。造成压缩率恒大于1的原因是因为塑料的原材料较松散,在压力作用下成型后体积减小所造成的。
比容和压缩率大的塑料,要求加料较大,内部充气也较多,成型时排气困难,成型周期长,生产率低;比容和压缩率小,对成型有利,但也会造成加料量不准确。
不同品种的塑料的比容和压缩率不同,同种的塑料也会因为塑料的形状、颗粒度及均匀性的不同,造成比容和压缩率的波动。
(4)水分和挥发物的含量。塑料中的水分和挥发物一方面来自塑料原材料生产过程中遗留下来,以及成型生产之前在运输、保管期间吸收空气中的水分;另一方面来自成型过程中塑料发生化学反应产生的副产品。
如果塑料中水分和挥发物含量过多又处理不及时,会造成塑料流动性增大,易产生溢料、成型周期长、收缩率大,产品易产生气泡、疏松、变形、翘曲、波纹等缺陷。有的挥发物还对模具有腐蚀作用,刺激人的感官。因此,在成型时应尽量消除其有害作用。例如,进行预热干燥、模具上开设排气槽排气、模具型腔表面镀铬防腐等。
(5)固化特性。热固性塑料在成型过程中树脂发生交联反应,分子结构由线型变为体型,塑料由既可熔化又可溶解变成既不可熔化又不可溶解的状态。这个过程称为固化(熟化)。
固化速度是指热固性塑料试样在固化过程中每硬化1mm 厚度所需要的时间,单位为秒(s)。固化速度与塑料的品种、制品的形状、壁厚、是否有预热、成型温度、预压等因素有关。采用预压、预热、提高成型温度、延长加压时间都能加快固化速度。固化速度并不是越快越好,应与成型方法、制品大小及复杂程度相适应。一般地,要求其在塑化和充模时固化速度较慢,有利于充满型腔;而在充满型腔后则应加快固化速度,减少成型时间。形状复杂、尺寸较大的制品应降低固化速度,否则无法成型。
总之,如何通过控制成型工艺条件来控制固化速度是热固性塑料成型中的关键问题之一。
常用热固性塑料的使用性能、成型性能及用途见表1.1。
表1.1 常用热固性塑料的使用性能、成型性能及用途

2.热塑性塑料的工艺性能
(1)收缩性。热塑性塑料的收缩性基本上与热固性塑料的收缩性相同。
(2)塑料状态与加工性。热塑性塑料在一定的压力下,随着温度的变化,呈现三种状态,其塑料状态与成型加工性的关系如图1.2所示。
① 玻璃态:玻璃态(结晶型树脂是结晶态)树脂是坚硬的固体,不易进行大变形量的加工,但可以进行车、铣、钻等切削加工。
② 高弹态:在 Tg~Tf(或 Tm)之间时,树脂是橡胶状态的弹性体,称为高弹态,可进行真空成型、压延成型、中空成型、冲压、锻造等。因为高弹态具有可逆性,为了得到所需形状和尺寸的塑料制品,必须把成型后的制品迅速冷却到Tg以下的温度,防止变形恢复。
③ 黏流态:在Tf(或Tm)~Td之间时,树脂是黏性流体,通常把这种液体状态的聚合物称为熔体。在这种状态下成型后具有不可逆的性质,一经成型和冷却后,其形状永远保持下来,可进行注射、吹塑、挤出等成型加工。值得注意的是,在黏流态的温度范围内,温度过高,会使熔体黏度大大降低,流动性增加,导致溢料、扭曲等问题,如果温度达到 Td附近时,会使聚合物分解。因此Tf(或Tm)、Td是进行成型加工的重要参数。

图1.2 塑料状态与成型加工性的关系
1—非结晶型树脂;2—结晶型树脂;Tg—玻璃化温度;Tf—非结晶型塑料黏流温度;Tm—结晶型塑料熔点;Td—热分解温度
(3)黏度和流动性。
① 黏度:塑料熔体内部抵抗流动的阻力。影响黏度的因素有两个方面。一方面,不同的塑料因其本身的树脂分子结构,塑料组成的不同而具有不同的黏度。另一方面,受到成型工艺中的温度、压力、剪切应力(或剪切速度)的影响。一般地,黏度随剪切应力(或剪切速度)的增加而降低,随温度升高而下降,随压力增高而增大。
② 流动性:热塑性塑料的流动性是指塑料在一定的温度和压力下充满型腔的能力,可以用熔体指数来衡量,其数值用熔体指数测定仪测定。即在一个筒内装入一定量的塑料并加热至规定的温度,在一定的压力下将熔融的塑料从固定直径的毛细管中压出,每10min 所压出的塑料质量即为该塑料的熔体指数,单位为g/10min。
③ 黏度与流动性的关系:黏度大,流动性差;黏度小,流动性好。
提示
我们常按流动性大小将塑料分为三类:
流动性好:聚酰胺、聚乙烯、聚苯乙烯、聚丙稀、醋酸纤维素等。
流动性中等:改性的聚苯乙烯、ABS、AS、聚甲基丙烯酸甲酯、聚甲醛、氯化聚醚等。
流动性差:聚碳酸酯、硬聚氯乙烯、聚苯醚、聚砜等。
(4)吸水性。吸水性表示塑料吸收水分的能力。一般分为两类:一类为具有吸水或黏附水分倾向的塑料,例如,聚甲基丙烯酸甲酯、聚酰胺、聚碳酸酯、聚砜、ABS 等。这类塑料必须在成型前进行干燥处理去除水分,否则水分在成型设备的高温料筒中变成气体并促使塑料发生水解,导致塑料起泡和流动性下降,严重影响制品质量。因此,必须严格控制塑料的含水量。一般不超过0.4%,ABS 应不超过0.2%。
(5)结晶性。结晶性是塑料在冷凝时是否具有结晶的特性。根据其特性,可将塑料分为结晶型和非结晶型两种:结晶型塑料有聚乙烯、聚丙烯、聚四氯乙烯、聚甲醛、聚酰胺等;非结晶型塑料有聚苯乙烯、聚甲基丙烯酸甲酯、ABS、聚砜等。
一般地,结晶型塑料是不透明或半透明的;非结晶型塑料是透明的,但也有例外,例如,ABS 是非结晶型塑料却不透明。结晶型塑料一般使用性能较好,但由于加热熔化需要吸收较多热量,冷却凝固时放出热量也多,因而必须注意成型设备的选用和冷却装置的设计;结晶型塑料收缩大,容易产生缩孔和气孔,并且各向异性明显,内应力大,制品容易产生变形和翘曲。同时结晶型塑料的结晶—熔化温度范围窄,易发生未熔塑料注入模具或堵塞浇口,应引起足够重视。
应当指出,结晶型塑料不可能形成完全的晶体,一般只有一定程度的结晶,其结晶程度随成型条件的变化而改变。如果熔体温度、模具温度高,熔体冷却速度慢,结晶度就越大;相反,则结晶度就越小。结晶度大的塑料密度大,强度、硬度高,刚度、耐磨性好,耐化学性和电性能好。结晶度小的塑料密度小,柔软性、透明性较好,伸长率和冲击韧性较好。因此,可以通过控制成型条件来控制塑料的结晶度从而控制其性能。
(6)热敏性。热敏性是指某些热稳定差的塑料,在温度高和受热时间长的情况下产生降解、分解、变色的特性。具有这种特性的塑料称为热敏性塑料,例如,硬聚氯乙烯、聚甲醛等。
热敏性塑料发生分解、降解,不但影响塑料性能,而且会产生一些有毒和腐蚀性气体(如 HCl 气体),对人体、模具造成损害。为了防止分解和降解,可在塑料中加入热稳定剂,正确控制模具温度和成型时间,对模具和设备采取防腐措施(如镀铬)等。
(7)应力开裂。有些塑料质地较脆,成型时又容易产生内应力,在外力作用下容易产生开裂。为防止开裂,可在塑料中加入增强材料加以改性。采用正确的成型工艺,对塑料制品进行后处理,合理设计制品的结构,在模具上采取措施等,来防止开裂。
(8)熔体破裂。塑料在恒温下通过喷嘴孔或浇口等狭小部位时,流速超过一定值后,挤出的熔体表面会发生明显的横向凹凸不平或外形畸变至使其肢离或断裂,这种现象称为熔体破裂。熔体破裂会影响制品的外观和性能。为防止熔体破裂可以增大喷嘴、浇口、流道的截面尺寸,减小压力和注射速度。
常用热塑性塑料的使用性能、成型性能及用途见表1.2。
表1.2 常用热塑性塑料的使用性能、成型性能及用途

续表

续表

续表
