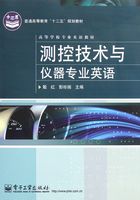
Part 1 Overview
Unit 1 Measurement, Control and Instrumentation

Instrumentation is defined as the art and science of measurement and control.Instrumentation engineers are responsible for controlling a whole system like a power plant.
An instrument is a device that measures and/or regulates process variables such as flow, temperature, level, or pressure. Instruments include many varied contrivances that can be as simple as valves and transmitters, and as complex as analyzers. Instruments often comprise control systems of varied processes such as refineries, factories, and vehicles. The control of processes is one of the main branches of applied instrumentation. Instrumentation can also refer to handheld devices that measure some desired variable. Diverse handheld instrumentation is common in laboratories, but can be found in the household as well. For example, a smoke detector is a common instrument found in most western homes.
Output instrumentation includes devices such as solenoids,valves,regulators,circuit breakers, and relays. These devices control a desired output variable, and provide either remote or automated control capabilities. These are often referred to as final control elements when controlled remotely or by a control system.
Transmitters are devices that produce an output signal, often in the form of a 4~20mA electrical current signal, although many other options using voltage, frequency, pressure, or ethernet are possible. This signal can be used for informational purposes, or it can be sent to a PLC, DCS, SCADA system, LabView or other type of computerized controller, where it can be interpreted into readable values and used to control other devices and processes in the system.
Control Instrumentation plays a significant role in both gathering information from the field and changing the field parameters, and as such are a key part of control loops.
History
In the early years of process control, process indicators and control elements such as valves were monitored by an operator that walked around the unit adjusting the valves to obtain the desired temperatures, pressures, and flows. As technology evolved pneumatic controllers were invented and mounted in the field that monitored the process and controlled the valves. This reduced the amount of time process operators were needed to monitor the process. Later years the actual controllers were moved to a central room and signals were sent into the control room to monitor the process and outputs signals were sent to the final control element such as a valve to adjust the process as needed. These controllers and indicators were mounted on a wall called a control board. The operators stood in front of this board walking back and forth monitoring the process indicators. This again reduced the number and amount of time process operators were needed to walk around the units. The basic air signal used during these years was 3~15 psig.
In the 1970s electronic instrumentation began to be manufactured by the instrument companies. Each instrument company came out with their own standard signal for their instrumentation, 10~50mA, 0.25~1.25V, 0~10V, 1~5V, and 4~20mA, causing only confusion until the 4~20mA was universally used as a standard electronic instrument signal for transmitters and valves. The transformation of instrumentation from mechanical pneumatic transmitters, controllers, and valves to electronic instruments reduced maintenance costs as electronic instruments were more dependable than mechanical instruments. This also increased efficiency and production due to their increase in accuracy.
The next evolution of instrumentation came with the production of Distributed Control Systems (DCS). The pneumatic and electronic control rooms allowed control from a centralized room, DCS systems allowed control from more than one room or control stations. These stations could be next to each other or miles away. Now a process operator could sit in front of a screen and monitor thousands of points throughout a large unit or complex.
Measurement
Instrumentation is usually used for measurement. Measurement is the process or the result of determining the magnitudes of many parameters (physical values). These parameters include:
(1)Chemical composition;
(2)Chemical properties;
(3)Properties of light;
(4)Vibration;
(5)Weight;
(6)Voltage;
(7)Inductance;
(8)Capacitance;
(9)Resistivity;
(10)Viscosity;
(11)Other mechanical properties of materials;
(12)Properties of ionising radiation;
(13)Frequency;
(14)Current;
(15) Pressure, either differential or static ;
(16)Flow;
(17)Temperature;
(18)Levels of liquids etc.;
(19)Density.
With the exception of a few seemingly fundamental quantum constants, units of measurement are essentially arbitrary; in other words, people make them up and then agree to use them. Nothing inherent in nature dictates that an inch has to be a certain length, or that a mile is a better measure of distance than a kilometre. Over the course of human history, however, first for convenience and then for necessity, standards of measurement evolved so that communities would have certain common benchmarks. Laws regulating measurement were originally developed to prevent fraud in commerce.
Measurement methods are often scrutinized for their validity, applicability, and accuracy. It is very important that the scope of the measurement method be clearly defined, and any aspect included in the scope is shown to be accurate and repeatable through validation.
Measurement method validations often encompass the following considerations:
(1)Accuracy and precision: Demonstration of accuracy may require the creation of a reference value if none is yet available.
(2)Repeatability and Reproducibility, sometimes in the form of a Gauge R&R.
(3)Range, or a continuum scale over which the measurement method would be considered accurate. Example: 10N to 100N force test.
(4)Measurement resolution, be it spatial, temporal, or otherwise.
(5)Curve fitting, typically for linearity, which justifies interpolation between calibrated reference points.
(6)Robustness, or the insensitivity to potentially subtle variables in the test environment or setup which may be difficult to control.
(7)Usefulness to predict end-use characteristics and performance.
(8)Measurement uncertainty.
(9)Interlaboratory or round robin tests.
(10)other types of measurement systems analysis.
Control
In addition to measuring field parameters, instrumentation is also responsible for providing the ability to modify some field parameters.
Modern day control engineering (also called control systems engineering)is a relatively new field of study that gained a significant attention during 20th century with the advancement in technology. It can be broadly defined as practical application of control theory. Control engineering has an essential role in a wide range of control systems, from simple household washing machines to high-performance F-16 fighter aircraft. It seeks to understand physical systems, using mathematical modeling, in terms of inputs, outputs and various components with different behaviors; use control systems design tools to develop controllers for those systems; and implement controllers in physical systems employing available technology. A system can be mechanical, electrical, fluid, chemical, financial and even biological, and the mathematical modeling, analysis and controller design uses control theory in one or many of the time, frequency and complex-s domains, depending on the nature of the design problem.
1.Control theory
There are two major divisions in control theory, namely, classical and modern, which have direct implications over the control engineering applications. The scope of classical control theory is limited to single-input and single-output (SISO) system design. The system analysis is carried out in time domain using differential equations, in complex-s domain with Laplace transform or in frequency domain by transforming from the complex-s domain. All systems are assumed to be second order and single variable, and higher-order system responses and multivariable effects are ignored. A controller designed using classical theory usually requires on-site tuning due to design approximations. Yet, due to easier physical implementation of classical controller designs as compared to systems designed using modern control theory, these controllers are preferred in most industrial applications. The most common controllers designed using classical control theory are PID controllers.
In contrast, modern control theory is carried out in the state space, and can deal with multi-input and multi-output (MIMO) systems. This overcomes the limitations of classical control theory in more sophisticated design problems, such as fighter aircraft control. In modern design, a system is represented as a set of first order differential equations defined using state variables. Nonlinear, multivariable, adaptive and robust control theories come under this division. Being fairly new, modern control theory has many areas yet to be explored. Scholars like Rudolf E. Kalman and Aleksandr Lyapunov are well-known among the people who have shaped modern control theory.
2.Control systems
Control engineering is the engineering discipline that focuses on the modeling of a diverse range of dynamic systems (e.g. mechanical systems) and the design of controllers that will cause these systems to behave in the desired manner. Although such controllers need not be electrical many are and hence control engineering is often viewed as a subfield of electrical engineering. However, the falling price of microprocessors is making the actual implementation of a control system essentially trivial. As a result, focus is shifting back to the mechanical engineering discipline, as intimate knowledge of the physical system being controlled is often desired.
Electrical circuits, digital signal processors and microcontrollers can all be used to implement control systems. Control engineering has a wide range of applications from the flight and propulsion systems of commercial airliners to the cruise control present in many modern automobiles.
In most of the cases, control engineers utilize feedback when designing control systems. This is often accomplished using a PID controller system. For example, in an automobile with cruise control the vehicle's speed is continuously monitored and fed back to the system, which adjusts the motor's torque accordingly. Where there is regular feedback, control theory can be used to determine how the system responds to such feedback. In practically all such systems stability is important and control theory can help ensure stability is achieved.
Although feedback is an important aspect of control engineering, control engineers may also work on the control of systems without feedback. This is known as open loop control. A classic example of open loop control is a washing machine that runs through a pre-determined cycle without the use of sensors.
3.Recent advancement
Originally, control engineering was all about continuous systems. Development of computer control tools posed a requirement of discrete control system engineering because the communications between the computer-based digital controller and the physical system are governed by a computer clock. The equivalent to Laplace transform in the discrete domain is the z-transform. Today many of the control systems are computer controlled and they consist of both digital and analog components.
Therefore, at the design stage either digital components are mapped into the continuous domain and the design is carried out in the continuous domain, or analog components are mapped in to discrete domain and design is carried out there. The first of these two methods is more commonly encountered in practice because many industrial systems have many continuous systems components, including mechanical, fluid, biological and analog electrical components, with a few digital controllers.
Similarly, the design technique has progressed from paper-and-ruler based manual design to computer-aided design, and now to computer-automated design (CAutoD), which has been made possible by evolutionary computation. CAutoD can be applied not just to tuning a predefined control scheme, but also to controller structure optimisation, system identification and invention of novel control systems, based purely upon a performance requirement, independent of any specific control scheme.
Instrumentation engineering
Instrumentation engineering is the engineering specialization focused on the principle and operation of measuring instruments that are used in design and configuration of automated systems in electrical, pneumatic domains etc. They typically work for industries with automated processes, such as chemical or manufacturing plants, with the goal of improving system productivity, reliability, safety, optimization, and stability. To control the parameters in a process or in a particular system, devices such as microprocessors, microcontrollers or PLCs are used, but their ultimate aim is to control the parameters of a system.
Instrumentation technologists
Instrumentation technologists, technicians and mechanics specialize in troubleshooting and repairing and maintenance of instruments and instrumentation systems. This trade is so intertwined with electricians, pipefitters, power engineers, and engineering companies, that one can find him/herself in extremely diverse working situations.
Words & Terms
instrumentation [ˌinstrumenˈteiʃən] n. 测量仪器, 仪表
measurement [meʒəmənt] n. 量度,测量, 衡量,(量得的)尺寸
power plant 发电站;发电厂,电动装置,发电机
contrivance [kənˈtraivəns] n. 发明,发明才能,想出的办法,发明物
analyzer [ˈænəlaizə] n. 分析器
variable [ˈvεəriəbl] n. 变量,变数
handheld devices 手持式设备
smoke detector 烟雾探测器
solenoid [ˈsəulinɔid] n. 线圈,螺线管
regulator [ˈreɡjuleitə] n. 调节器
circuit breakers 断路器,电路分流器
relay [ˈriːlei] n. 中继转发(设备)
transmitter [trænzˈmitə] n. 变送器,发射机
control loops 控制回路
process control 过程控制
pneumatic [njuː ˈmætik] adj. 充气的,由压缩空气操作(推动)的,风动的
mount [maunt] vt. 安装,配有……
psig abbr. pounds per square inch(gauge) 磅/平方英寸
manufacture [ˌmænjuˈfæktʃə] vt. 制造
dependable [diˈpendəbəl] adj. 可信赖的,可靠的
Distributed Control Systems (DCS) 分布式控制系统,集散控制系统
complex [ˈkɔmpleks] n. 综合体,集合体
composition [ˌkɔmpəˈziʃən] n. 成分,混合物,合成物
property [ˈprɔpəti] n. 性质,属性
vibration [vaiˈbreiʃən] n. 振动,摆动,摇摆
voltage [ˈvəultidʒ] n. 电压,伏特数
inductance [inˈdʌktəns] n. 感应系数,自感应
capacitance [kəˈpæsitəns] n. 电容,电容量
resistivity [ˌriːzisˈtiviti] n. 电阻系数
viscosity [viˈskɔsitiː] n. 黏性,黏稠
ionising radiation 电离辐射
frequency [ˈfriːkwənsi] n. 频率,(声波或无线电波的)振动频率
current [ˈkʌrənt] n. 电流
flow [fləu] n. 流量
density [ˈdensiti] n. 密度
quantum [ˈkwɔntəm] n. 量子,定量,总量
inherent [inˈhiərənt] adj. 固有的;内在的
convenience [kənˈviːnjəns] n. 方便,便利
benchmark [ˈbentʃˌmaːk] n. 基准
fraud [frɔːd] n. 欺诈,欺骗行为;骗子
scrutinize [ˈskruːtnˌaiz] vt. 仔细检查,详审
validation [væliˈdeiʃən] n. 批准;确认
encompass [enˈkʌmpəs] vt. 围绕;包围
gauge [ɡeidʒ] n. 规范,计,量规 vt. 计量, 度量
range [reindʒ] n. 量程,范围,射程,距离
scale [skeil] n. 刻度,比例(尺),程度,范围,等级,级别
resolution [ˌrezəˈluː ʃən] n. 分辨力,分辨率
spatial [ˈspeiʃəl] adj. 空间的,立体空间的,三维空间的
temporal [ˈtempərəl, ˈtemprəl] adj. 时间的
curve fitting 曲线拟合
interpolate [inˈtəːpəˌleit] v. 插值,内插,插补
end-use 最终用途
measurement uncertainty测量不确定度
insensitivity 不灵敏,不灵敏度
interlaboratory [ˌintəˈlæbərətəri] adj. 多个实验室(进行)的
round robin 轮转,循环,比对
complex [ˈkɔmpleks] n. 复数
differential equations 微分方程
second order 二阶
higher-order system 高阶系统
the state space 状态空间
adaptive [əˈdæptiv] adj. 自适应
robust [rəuˈbʌst] adj. 鲁棒,健壮的 n. 鲁棒性
dynamic [daiˈnæmik] adj.动力的
microprocessor [ˈmaikrəuˌprɔsesə] n. 微处理机
trivial [ˈtriviəl] adj. 琐碎的,没有价值的,没有意义的
propulsion [prəˈpʌlʃən] n. 推进
cruise [kruːz] n. 巡航
feedback [ˈfiːdbæk] n. 反馈,反馈信息
torque [tɔːk] n. 扭转力,转(力)矩
discrete [disˈkriːt] adj. 离散的
map [mæp] vt. 映射
structure optimization 结构优化
specialization [ˌspeʃəlaiˈzeiʃən] n. 特别化;专门化
configuration [kənˌfiɡjuˈreiʃən] n. 构造,形状,外貌,轮廓
troubleshooting n. 发现并修理故障,解决纷争
intertwine [ˌintəˈtwain] vi. & vi. 缠结在一起
Notes
The control of processes意为“过程控制”。
Output instrumentation includes devices such as solenoids, valves, regulators, circuit breakers, and relays. These devices control a desired output variable, and provide either remote or automated control capabilities. These are often referred to as final control elements when controlled remotely or by a control system. 句中desired output variable意为“期望输出变量”,are referred to as意为“被称为”。全句译为:输出仪器包括线圈、阀、调节器、断路器和中继器等元件。这些元件控制期望输出变量,使之实现远程控制或自动控制功能。在远程控制或自动控制系统中,称这些元件为终端控制元件。
Control Instrumentation plays a significant role in both gathering information from the field and changing the field parameters, and as such are a key part of control loops. 句中field意为“现场”,control loops意为“控制回路”。全句译为:控制仪器在现场信息采集和现场参数转换中都起到了重要作用。这本身是控制回路的一个关键部分。
pneumatic controllers意为“气压式调节器”。
These controllers and indicators were mounted on a wall called a control board.译为:这些控制器和指示器安装在一个壁面上,称其为控制面板。
The transformation of instrumentation from mechanical pneumatic transmitters, controllers, and valves to electronic instruments reduced maintenance costs as electronic instruments were more dependable than mechanical instruments. 句中reduced为transformation的谓语,as引导原因状语从句。全句译为:从机械气动变送器、控制器和阀的控制方式向电子仪器控制方式的转变,降低了维修成本,因为电子仪器比机械仪器更可靠。
Pressure, either differential or static. 译为“压力,差压或静压”。
With the exception of a few seemingly fundamental quantum constants, units of measurement are essentially arbitrary; in other words, people make them up and then agree to use them. 句中With the exception of意为“除……以外”,quantum constants意为“量子常数”。全句译为:除了少数看上去代表基本法则的量子常数以外,测量的单位实质上是很主观的,换句话说,人们编制并愿意使用它就可以了。
It seeks to understand physical systems, using mathematical modeling, in terms of inputs, outputs and various components with different behaviors; use control systems design tools to develop controllers for those systems; and implement controllers in physical systems employing available technology. 主语it代指“control engineering”,句子中的3个并列成分understand, use 和 implement 为 seeks to 的宾语。全句译为:控制工程根据输入、输出和不同性质的各种元件,建立数学模型,分析物理系统。使用控制系统设计工具来为这些系统开发控制器。在物理系统中运用有效的技术来执行这些控制器。
The system analysis is carried out in time domain using differential equations, in complex-s domain with Laplace transform or in frequency domain by transforming from the complex-s domain. 译为:系统用微分方程实现时域分析,用拉氏变换实现复数(s)域分析,或将复数域转换到频域分析。
CAutoD can be applied not just to tuning a predefined control scheme, but also to controller structure optimisation, system identification and invention of novel control systems, based purely upon a performance requirement, independent of any specific control scheme. 句中 not just to…but also to…意为“不仅……而且……”,novel control systems意为“新型系统”。全句译为:计算机辅助设计(CAutoD)不仅能用于预定义控制模式的调整,而且可以用于控制器结构优化、系统辨识和新型系统的开发。这一切都仅仅基于设计的性能要求,而不依赖于任何具体的控制模式。