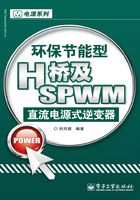
1.3 基本工作原理、分类及特点
1.3.1 传统SPWM多电平逆变器的工作原理与分类
20世纪80年代末多电平逆变器的出现,为人们研制高压大功率逆变器开辟了一条新路,即通过对逆变器电路结构的改造,利用增加逆变器输出电压电平数的方法来减小du/dt、EMI、输出电压中的谐波,并使逆变开关管工作在低频(或工频)状态,以减少开关损耗,增大输出电压和输出功率。经过20多年的研究和开发,现在已经形成了几种典型的多电平逆变器主电路结构形式。这些主电路结构形式从原理上可以分为两大类:一种是半桥结构形式的钳位式多电平逆变器,包括二极管钳位、电容钳位、二极管和电容混合钳位和通用钳位式多电平逆变器;另一种是利用单相全桥逆变器(FBI或H桥)直接串联级叠加结构形式的级联式多电平逆变器。这两种结构形式的多电平逆变器的原理等效电路如图1-2(a)、(b)所示,这是一种输出为正半周电压的原理等效电路,其中图1-2(a)是半桥结构形式的钳位式多电平逆变器的原理等效电路;图1-2(b)是FBI或H桥直接串联级叠加结构形式的级联式多电平逆变器的原理等效电路。下面利用这两个原理等效电路来说明这两类多电平逆变器是如何输出多电平交流电压的。

图1-2 多电平逆变器半周期输出的原理等效电路
多电平逆变器和两电平逆变器一样,也有电压型和电流型逆变器之分,但应用较多的是电压型逆变器,因此下面将以电压型多电平逆变器为主进行介绍。对于电流型多电平逆变器,将在第8章中进行介绍,也可以通过对偶原理去了解。
根据多电平逆变器直流电源电压连接方式的不同,电压型多电平逆变器开关管的通断控制方式也不同。对于如图1-2(a)所示的钳位式多电平逆变器,开关管的通断切换电路(图中点画线框内的切换电路)的工作状态可以等效成一个切换开关S,通过对钳位式多电平逆变器开关管通断状态的控制,或者说通过对开关S的切换控制,就可以得到多电平电压的输出;对于如图1-2(b)所示的级联式多电平逆变器,开关管的通断切换电路(图中点画线框内的切换电路)的工作状态可以等效成几个与独立直流电源E1~EN串(并)联的开关S1~SN,通过对级联式多电平逆变器开关管通断状态的控制,或者说对开关S1~SN的切换控制,就可以得到多电平电压的输出。
而对于两电平逆变器,因其只有一个直流电源,所以开关管的du/dt及输出电压只取决于这一个直流电源。对于多电平逆变器,它是由多个直流电源串联组成的,开关管的du/dt只取决于与之并联的那一个直流电源,但逆变器的输出电压的幅值却取决于多个直流电源电压的串联级叠加之和,因此,多电平逆变器在提高输出电压、增大输出功率的同时,并不增加在开关管上的电压和du/dt,这就是多电平逆变器能够输出高压大功率交流电能的原因。
多电平逆变器的实质是开关管和多个直流电源电压按照特定的电路组合方式形成的主逆变电路。只要按照一定的方式和顺序选择开通开关管,就能够使逆变器主电路内的直流电源电压按照一定的方式和顺序形成多个直流电源电压的串联回路,从而使逆变器得到高压大功率多电平的输出。由于逆变器中开关管上的电压和du/dt,只取决于与开关管并联的直流电源电压,而与多个直流电源电压串联的电压总和的值无关,所以du/dt小,EMI小,逆变效率高,可以实现高压大功率的输出。
下面介绍多电平逆变器的分类。从当前资料上能够得到的传统多电平逆变器电路,根据其结构形式的分类如下表所示。

除了上面所列的多种主要的传统式多电平逆变器之外,还有其他一些多电平逆变器,如我们于2007年后新研发的采用级联叠加变压器的二进制(2N-1)与三进制(3N-1)多电平逆变器、独立SPWM直流电源级联叠加式多电平逆变器,以及直流电容分压SPWM直流电源级联式多电平逆变器等,前两种多电平逆变器将在第3章中进行介绍,后两种多电平逆变器将在第5章与第6章中进行介绍。
1.3.2 传统SPWM多电平逆变器的特点
通过前面的介绍可知,当前的逆变器有两种研究方向:一种研究方向是对两电平SPWM逆变器的研究,它采用单独的一个直流电源,并对逆变开关管进行SPWM控制,从而得到幅值恒定的(+E/2及-E/2,或+E及-E)SPWM波形的输出电压。由于输出电压只有两个电平,故称之为两电平逆变器。这种逆变器的研究发展方向是提高开关频率,采用高频SPWM控制对输出电压的波形进行改善。但由于只有一个直流电源,当此电源电压较高时, du/dt就大,所以开关损耗也大,EMI也大。为了减小du/dt、EMI及开关损耗,必须对逆变器采用软开关技术,必须采用高频开关器件作为逆变开关管,这样做会使电路复杂化,从而会增大成本,减小可靠性,不适宜在高压大功率场合应用;另一种研究方向是对逆变器主电路进行改造,采用多个直流电源及多个开关器件,以特定的电路结构,通过对多个开关管的控制,使不同的直流电源电压串联输出,并用增加输出电压电平数的办法减少输出电压中的谐波。由于是用多个直流电源电压串联的,故开关管的耐压与du/dt只取决于与之并联的那一个直流电源电压,因而du/dt小,EMI也小。但由于逆变器的输出电压取决于多个直流电源串联的电压之和,所以可以提高逆变器的输出电压和输出功率。而且由于是通过增加电平数来减小输出电压谐波的,故可以使开关管工作在低频或工频状态,开关损耗小,逆变效率高,适合于高压大功率场合应用,这是多电平逆变器与两电平逆变器最主要的区别。
此外,多电平逆变器的另一个优点是输出电压的跳变小,即du/dt小。瞬间过大的电压跳变会带来很大的冲击电流,对负载和逆变器本身都有非常大的危害,还会产生很大的EMI。在相同的输出电压等级下,采用多电平逆变器不仅可以降低对开关管的耐压要求,而且还可以减小对交流电动机绝缘的损害,从而可降低电磁干扰(EMI)。
在高压大功率场合应用场合,如在高压大功率交流电动机的变频调速系统中,传统的SPWM两电平逆变器有一个最大的缺点是不容易实现直接高压大功率输出。在需要高压大功率输出时,除了少数低速场合采用AC-AC变频调速方式外,通常多采用AC-DC-AC变频方式。在这种方式中,有的将多个低压小功率的变频器通过变压器多重叠加技术得到高压大功率输出,也有的在交流输入端和输出端分别用变压器进行降压和升压,中间环节仍然采用低压变频器。显然,上述两种方法都需要采用笨重、昂贵和耗电的变压器。对于第二种方法还会出现中间环节电流过大,系统效率下降,可靠性降低、低频时电能传输困难等诸多缺点。为了克服这些缺点有人也采用了直接高压输出的变换方式,这对于开关管提出了很高的技术要求,要求开关管能承受很高的电压应力,一般的做法是用多个低压开关器件的串联来提高承受高电压应力,这样做虽然在一定程度上降低了成本(几个低压开关器件的价格往往比一个相同容量的高压开关器件便宜),但存在着静态和动态均压问题,均压电路将会导致系统复杂化、损耗增加、效率下降。因此,两电平逆变器不如多电平逆变器更适合应用在高压大功率场合。这也是多电平逆变器最大的优点之一。也正是由于这个原因,才使很多学者开始对多电平逆变器进行研究。
除了上述特点外,多电平逆变器的优点还体现在三相系统中输出的共模电压(三相电压之和的平均值)较小。在驱动交流电动机的情况下,共模电压过大会对电动机的轴和轴承造成损害。在高压大功率应用场合这个问题更加明显。而采用多电平逆变器,则输入电流的畸变将会得到一定程度的改善。
此外,人们对高压大功率电压型多电平逆变器进行的广泛深入的研究表明:各种不同电路结构的多电平逆变器,具有各不相同的特点,适用于不同的场合。读者在应用时也应注意这一点。例如,二极管钳位半桥式结构的三相多电平逆变器,其特点是采用多个二极管对相应的开关管进行钳位,以保证每次一个桥臂只有一个开关管动作,以实现多电平输出,而每一个开关管只承受直流电源电压的1/2。这种三相多电平逆变器的缺点是当电平数较多时,钳位二极管承受的反向电压不同,开关管所需的额定电流也不相同,同时还存在电容电压的平衡问题。再如电容钳位半桥式结构的三相多电平逆变器,其工作原理与二极管钳位多电平逆变器相似。但是由于电容的引入使得电压合成的选择增多,故开关状态的选择具有更大的灵活性。这种三相多电平逆变器的缺点是大量的电容使逆变器的体积增大,成本增高及封装困难。虽然通过同一个电平上不同开关状态的组合,可以使电容电压保持均衡,可以较好地应用于有功调节和变频调速系统,但控制较复杂。又如具有独立直流电源的级联式三相多电平逆变器,其特点是要想获得更多的电平,只要增多H桥的串联个数即可。与钳位式多电平逆变器相比,级联式多电平逆变器的优点是不存在电容上电压的均衡问题,不需要钳位二极管或钳位电容,适合于调速控制、容易实现模块化,维护方便,在电平数相同时所需要的元器件数目最少,不受钳位二极管或钳位电容的限制,可以得到更多的电平输出,可以更方便地提高输出电压与更多地减少谐波含量。其控制方法也相对简单,可以对每一个H桥进行SPWM控制,然后进行波形重组。但这种多电平逆变器也有缺点,那就是所用的独立直流电源的个数较多,使直流供电电源电路变得复杂化。
综上所述,由于存在电容均压问题,故钳位式多电平逆变器比较适合应用于无功调节场合,而在有功传递如电动机调速方面应用时控制比较困难,需要实施额外的算法。虽然如此,但钳位式三电平逆变器却仍在交流电动机调速领域应用较多,这主要是因为现有的高耐压器件很适合三电平逆变器应用,电容的均压问题也可以通过控制来解决。对于级联式多电平逆变器,虽然它具有应用独立直流电源个数多的缺点,但在电力有源滤波器中应用时,由于独立直流电源被储能电容所取代,独立直流电源多的缺点也就不存在了,所以它比较适合应用于电力有源滤波器。但在输入变压器成本允许的情况下,或需要减小输入电流的谐波含量时,它也可以应用于交流电动机变频调速系统,因为它可以实现模块化、使用的元器件少、控制简单,如美国罗宾康公司完美无谐波高压变频器就采用了这种方案。