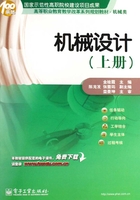
任务四 认识摩擦、磨损现象及润滑方案确定
摩擦是造成能量损失的主要原因,据估计,在全世界工业部门所使用的能源中,大约有1/3~1/2最终以各种形式损耗在克服摩擦上。摩擦会导致磨损,而磨损所造成的损失更是惊人。据统计,磨损造成的损失是摩擦损失的12倍,约有80%的损坏零件是因磨损而报废的。由摩擦所引起的能量损耗和磨损所引起的材料损耗,在经济上造成了巨大的损失。磨损是摩擦的结果,润滑则是减少摩擦和磨损的有力措施,这三者是相互联系不可分割的。
一、摩擦与磨损
1.摩擦及其分类
在外力作用下,一物体相对另一物体具有运动趋势时,两物体接触面间产生的阻碍物体运动的切向阻力称为摩擦力。这种在两物体接触区产生阻碍运动并消耗能量的的现象,称为摩擦。摩擦会造成能量损耗和零件磨损,在一般情况下是有害的,因此应尽量减少摩擦。但有些情况下却要利用摩擦工作,如摩擦型带传动,摩擦制动器等。
根据摩擦副表面间的润滑状态将摩擦状态分为四种:干摩擦、边界摩擦(润滑)、液体摩擦(润滑)和混合摩擦(润滑),如图0-3所示。
(1)干摩擦
两摩擦表面间无任何润滑剂或保护膜的纯净金属接触时的摩擦,称为干摩擦。在工程实际中没有真正的干摩擦,因为暴露在大气中的任何零件的表面,不仅会因氧气而形成氧化膜,且或多或少也会被润滑油所湿润或受到“污染”,这时,其摩擦系数将显著降低。在机械设计中,通常把不出现显著润滑的摩擦,当做干摩擦处理。
(2)边界摩擦
两摩擦表面各附有一层极薄的边界膜(油膜厚度小于1μm),两表面仍是凸峰接触的摩擦状态称为边界摩擦。与干摩擦相比,摩擦状态有很大改善,其摩擦和磨损程度取决于边界膜的性质、材料表面机械性能和表面形貌。
(3)液体摩擦
两摩擦表面完全被油膜(油膜厚度一般在1.5~2μm)隔开、表面凸峰不直接接触的摩擦。此种润滑状态亦称液体润滑,摩擦是在液体内部的分子之间进行,故摩擦系数极小。
(4)混合摩擦
两表面间同时存在干摩擦、边界摩擦和液体摩擦的状态称为混合摩擦。

图0-3 摩擦副的表面润滑状态
2.摩损及其过程
运动副之间的摩擦将导致零件表面材料的逐渐损失,这种现象称为磨损。单位时间内材料的磨损量称为磨损率。磨损量可以用体积、质量或厚度来衡量。
机械零件严重磨损后,将降低机器的工作效率和可靠性,使机器提早报废。因此,预先考虑如何避免或减轻磨损,是设计、使用、维护机器的一项重要内容。但另一方面,磨损也并非全都是有害的,工程上常利用磨损的原理来减小零件表面的粗糙度,如磨削、研磨、刨、抛光、跑合等。
在机械的正常运转中,磨损过程大致可分为以下三个阶段。
(1)跑合(磨合)磨损阶段
由于机械加工的表面具有一定的不平度存在。运转初期,摩擦副的实际接触面积较小,单位面积上的实际载荷较大,因此,磨损速度较快。经跑合后尖峰高度降低,峰顶半径增大,实际接触面积增加,磨损速度降低。
(2)稳定磨损阶段
机件以平稳缓慢的速度磨损,这个阶段的长短就代表机件使用寿命的长短。
(3)剧烈磨损阶段
经稳定磨损阶段后,使精度降低,间隙增大,从而产生冲击、振动和噪声,磨损加剧,温度升高,短时间内使零件迅速报废。

图0-4 零件的磨损过程
3.磨损分类
按破坏的机理,磨损主要有四种基本类型,即黏着磨损、接触疲劳磨损、磨粒磨损和腐蚀磨损。
(1)黏着磨损
当摩擦表面的不平度凸峰在相互作用的各点产生结点后再相对滑移时,材料从运动副的一个表面转移到另一个表面,便形成了黏着磨损。滑动轴承中的“抱轴”和高速重载齿轮的“胶合”现象均是严重的黏着磨损。
(2)接触疲劳磨损
受变应力的摩擦副,在其表面上形成疲劳点蚀,使小块金属剥落,这种现象称为疲劳磨损。接触疲劳磨损常发生在滚动轴承、齿轮、凸轮等零件上。
(3)磨粒磨损
从外部进入摩擦面间的游离硬质颗粒或摩擦表面上的硬质凸峰,在摩擦过程中引起材料脱落的现象称为磨粒磨损。
(4)腐蚀磨损
在摩擦过程中,摩擦表面与周围介质发生化学反应或电化学反应的磨损称为腐蚀磨损,腐蚀可在没有摩擦的条件下形成,而相对运动消除了化学反应的生成物,接着表面又受到腐蚀,如此不断反复。
实际上,大多数的磨损都以复合形式出现,即以上几种磨损相伴存在。微动磨损就是一种典型的复合磨损。微动磨损发生在相对静止的摩擦副上,但须在环境振动影响下,使结合面间沿表面方向有微幅振摆,才能产生。
4.减少磨损的措施
为了减少摩擦表面的磨损,设计时,除了必须满足一定的磨损约束条件之外,还必须采取必要的减少磨损的措施。
(1)正确选用材料
正确选用摩擦副的配对材料,是减少磨损的重要途径。如当以黏着磨损为主时,应当选用互溶性小的材料;当以磨粒磨损为主时,则应当选用硬度高的材料,或设法提高所选材料的硬度,也可以选用抗磨料磨损的材料。
(2)进行有效的润滑
润滑是减少磨损的重要措施。应根据不同的工况条件,正确选用润滑方式,使摩擦表面尽可能在液体摩擦或混合摩擦的状态下工作。
(3)采用适当的表面处理
为了降低磨损,提高摩擦副的耐磨性,可采用各种表面处理。
(4)改进结构设计
提高加工和装配精度的结构设计可以减少摩擦磨损。例如,设计出来的结构,应该有利于表面膜的形成与恢复,压力的分布应当是均匀的,而且,还应有利于散热和磨屑的排出等。
(5)正确的使用、维修与保养
新机器使用之前的正确“磨合”,可以延长机器的使用寿命。经常检查润滑系统的油压、油面密封情况,对轴承等部位定期润滑,定期更换润滑油和滤油器芯,以阻止外来磨料的进入等,对减少磨损都十分重要。
二、润滑
在摩擦副间加入润滑剂,以降低摩擦、减轻磨损,这种措施称为润滑。润滑的主要作用是改善摩擦、减轻磨损,同时润滑剂还能起减振、防锈等作用,液体润滑剂还能带走摩擦热、污物等。
(一)润滑剂的性能与选择
常用的润滑剂除了润滑油和润滑脂外,还有固体润滑剂(如石墨、二硫化钼等)、气体润滑剂(如空气、氢气、水蒸气等)。
1.润滑油
润滑油是目前使用最多的润滑剂,主要有矿物油、动植物油、合成油三大类,其中应用最广泛的为矿物油。
(1)黏度
润滑油最重要的一项物理性能指标为黏度,它是选择润滑油的主要依据。黏度的大小表示了流体流动时其内摩擦阻力的大小,黏度愈大,内摩擦阻力就愈大,流体的流动性就愈差。
黏度可用动力黏度、运动黏度、条件黏度(恩氏黏度)等表示。我国的石油产品常用运动黏度来标定。
① 动力黏度 对于1m3的液体,如果其上下表面发生相对速度为1m/s的相对运动时所需要的切向力为1N,则称该液体的黏度为1 Pa·s(=1N·s/m2)
② 运动黏度 液体的动力黏度与液体在相同温度下密度的比值称为该液体的运动黏度

式中,η为动力黏度,单位为Pa·s; ρ为密度,单位为kg/m3; ν为运动黏度,单位为m2/s。
一般润滑油的牌号就是该润滑油在40℃(100℃)时的运动黏度(mm2/s)的平均值,如L—AN46是全损耗系统用油在40℃时的运动黏度。
③ 条件黏度 在规定的温度下从恩氏黏度计流出200ml样品所需的时间与同体积蒸馏水在20℃时流出所需的时间之比值称为该液体的条件黏度,以°E表示。
运动黏度和恩氏黏度之间可通过下式进行换算:
当1.35≤ oE≤ 3.2时,
当oE>3.2时,
黏度随压强的升高而增大,但当压强小于20MPa时,其影响甚小,可不予考虑。
(2)黏—温特性
润滑油的黏度随温度变化的情况十分明显。温度升高,黏度降低,黏度增大。润滑油受温度影响的程度可用黏度指数V.I(Viscosity Index)表示。黏度指数越大,表明黏度随温度的变化越小,即黏—温特性越好。
表0-4 常用润滑油的主要质量指标和用途

(3)凝点、倾点
凝点是指在规定的冷却条件下,润滑油停止流动的最高温度,润滑油的使用温度应比凝点高5℃~7℃。倾点是润滑油在规定的条件下冷却到能继续流动的最低温度,润滑油的使用温度应高出倾点3℃以上。
(4)闪点
闪点是表示润滑油蒸发性的指标。油蒸发性越大,其闪点越低。同时,闪点也是表示着火危险性的指标。对于高温下工作的机器,闪点是润滑油的一个十分重要的指标,通常应使润滑油的使用温度低于闪点20℃~30℃。
常用润滑油的主要质量指标和用途见表0-4。
2.气体润滑剂
最常用的是空气,此外还有氢气、水蒸气及液态金属蒸气等均可作为气体润滑剂。其特点是黏度低,功耗少,温升小,其黏度随温度变化小,故适于高温和低温环境下的高速场合,但承载能力低。
3.润滑脂
为使润滑剂易于保持在摩擦表面,用稠化剂将润滑油稠化成膏状,即润滑脂。稠化剂是各种金属皂,如钾皂、钠皂、钙皂等,从而可形成不同皂类的润滑脂。有时为提高抗氧化能力和润滑性能,还常常加入添加剂。
润滑脂是除润滑油外应用最多的一类润滑剂。它是润滑油(基础油)与稠化剂(如钙、锂、钠的金属皂)的膏状混合物,习惯上称为黄油或干油。根据调制润滑脂所用皂基之不同,主要有以下几类:一是钙基润滑脂,它具有良好的抗水性,但耐热能力差,工作温度不宜超过55℃~65℃;二是钠基润滑脂,它有较高的耐热性,工作温度可达120℃,但抗水性差,由于它能与少量水乳化,从而保护金属免遭腐蚀,比钙基润滑脂有更好的防锈能力;三是锂基润滑脂,它既能抗水,耐高温(工作温度不宜高于145℃),而且有较好的机械安定性,是一种多用途的润滑脂。无论哪类润滑脂,均常用于不易加油、重载低速的场合。其性能指标主要有两个。
(1)锥入度
锥入度(或稠度)是指在规定条件下,将重量为1.5N的标准锥体在25℃恒温下,由润滑脂表面自由沉下,经5s后可沉入的深度值(以0.1mm为单位)。它标志着润滑脂内阻力的大小和流动性的强弱,主要取决于稠化剂的性质,与基础油无关。锥入度越小,润滑脂越稠,附着性、密封性越好,承载能力越高,但同时摩擦阻力较大,流动性差,而且不易填充较小的摩擦间隙。
(2)滴点
指在规定的加热条件下,润滑脂从标准测量杯的孔口滴下第一滴油时的温度叫润滑脂的滴点,它标志着润滑脂耐高温的能力。选择润滑脂时,工作温度应低于滴点15℃~20℃。
常用润滑脂的主要质量指标及用途见表0-5。
4.固体润滑剂
固体润滑剂有无机化合物(石墨、二硫化钼、硼砂等)与有机化合物(金属皂、动物脂等),使用时常将润滑剂粉末与胶黏剂混合起来应用,也可与金属或塑料等混合后制成自润滑复合材料使用。固体润滑剂适用于高温、大载荷,以及不宜采用液体润滑剂和润滑脂的场合,如宇航设备及卫生要求较高的机械设备中。
表0-5 常用润滑脂的主要质量指标和用途

(二)选用润滑剂的原则
(1)考虑工作载荷
对承受大负荷(或压强大)的边界摩擦副应选黏度高,油性及极压性好的润滑油;对受冲击载荷或往复运动的零件,因不易形成液体膜,可选润滑脂或固体润滑剂;在液体润滑中,润滑油黏度越高,其油膜的承载能力越高。
(2)考虑相对滑动速度
对相对滑动速度较高的运动副,因易形成油膜,宜选黏度较小的润滑油,以减小油膜间由于内摩擦而引起的功率损耗。
(3)考虑工作温度
对在低温下工作的机械应选黏度较小、凝点较低的润滑油;对在高温下工作的机械应选黏度较大和闪点较高的润滑油;对在特低温下工作的机械可选用抗凝添加剂的润滑油或固体润滑剂;对工作温度变化大的机械应选温度变化对黏度影响较小的润滑油。
(4)考虑特殊工作环境
对在多尘环境中工作的机械,可选润滑脂,以利于密封。对有火花产生的场所,应采用高闪点的润滑油。
(三)润滑方法和润滑装置
机械设备的润滑,主要集中在传动件和支撑件上。油润滑的方法多种多样,其分类标准大概有四种:集中润滑或分散润滑,连续润滑或间歇润滑,压力润滑或无压力润滑,循环式润滑或非循环式润滑。
分散润滑比集中润滑简便。集中润滑需要一个多出口的润滑装置供油,而分散润滑中摩擦副的润滑装置则是各自独立的。对轻载、低速的摩擦副可采用间歇无压力润滑或间歇压力润滑,可利用油壶、油枪将油注入油杯进行润滑。连续无压力润滑可采用油绳、油垫、针阀式油杯、油环、油轮等润滑装置。而连续压力润滑需采用油泵、喷嘴装置,高速时还可以采用油雾发生器实现油雾润滑。
脂润滑的装置较为简单,加脂方式有人工加脂、脂杯加脂和集中润滑系统供脂等。对于单机设备上的轴承、链条等部位,由于润滑点不多,大多采用人工加脂或涂抹润滑脂。对于润滑点多的大型设备,如矿山机械、船舶机械等,则采用润滑系统。
三、密封装置
为了使润滑持续、可靠、不漏油,同时为了防止外界脏物进入机体,必须采用相应的密封装置。密封装置从总体上可分为两大类:一类是固定密封,即密封后两密封件之间固定不动;另一类是动密封,即密封后两密封件之间有相对运动。
固定密封可采用各种垫片,包括金属、非金属垫片及密封胶等。动密封又分为接触式、非接触式密封,其中应用较广的是接触式密封,它主要是利用各种密封圈或毡圈密封。各种密封件都已标准化,可查阅手册选取。非接触式密封有迷宫式密封、螺旋式密封等,半接触式密封有活塞环密封、机械密封等,其结构较复杂,主要用于重要部件的密封。
在一般常用的机械中,用得较多的密封装置是密封圈和填料。密封圈有各种形式,有带骨架的和不带骨架的,有普通型和双口型等,应根据使用条件查阅手册进行选择。密封圈也可做防尘密封件使用,但粉尘严重时,应使用专门的防尘密封圈。采用脂润滑时,可使用毡圈密封。