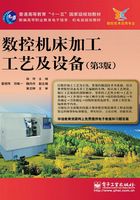
1.3 数控机床的组成及分类
1.3.1 数控机床的组成
数控机床是典型的机电一体化产品,主要由程序载体、输入/输出装置、计算机数控装置(CNC装置)、伺服系统(位置反馈系统)和机床本体等五部分组成。数控机床组成框图如图1.2所示。
数控机床各组成部分的功能简介如下。
1.程序载体
数控机床是按照输入的零件加工程序运行的。零件加工程序中,包括机床上刀具和工件的相对运动轨迹、工艺参数(进给量、主轴转数等)和辅助运动等,用一定的格式和代码,存储在一种载体上,被称为程序载体。如穿孔纸带、盒式磁带或软磁盘等,通过数控机床的输入装置,将程序信息输入到CNC单元内。

图1.2 数控机床的组成及框图
2.输入/输出装置
输入装置的作用是将信息载体中的数控加工信息读入数控系统的内存。根据程序载体的不同,相应有三种输入方式。
(1)控制介质输入。主要有两种输入方法:一种方法是通过纸带输入,即在特制的纸带上穿孔,用孔的不同位置的组合构成不同的数控代码,通过纸带阅读机将指令输入。另一种方法是对于配置有计算机软驱动器的数控机床,可以将存储在磁盘上的程序通过软驱输入系统。
(2)手动输入。操作者可以利用机床上的显示屏及键盘输入加工程序指令,控制机床的运动,具体说来有三种情况。
① 手动数据输入(Manual Data Input, MDI):即通过机床面板上的键,把数控程序指令逐条输入到存储器中。这种方法只适用于一些比较短的程序,只能使用一次,机床动作后程序就消失。
② 在控制装置的程序编辑界面(EDIT)状态下,用按键输入加工程序,存入控制装置的内存中。用这种方式可以对程序进行编辑,程序可重复使用。
③ 在具有会话编程功能的数控装置上,可以按照显示屏上提示的问题,选择不同的菜单,将图样上指定的有关尺寸数字等输入,就可自动生成加工程序存入内存。这种方法虽然是手工输入,但却是自动编程。
图形交互自动编程是现在广泛采用的另一种自动编程方式。利用CAD软件的图形编辑功能将零件的几何图形绘制到计算机上,形成零件的图形文件,然后调用数控编程模块,采用人机交互的方式在计算机屏幕上指定被加工的部位,通过键盘手工输入相应的加工参数后,计算机自动编制出数控加工程序。
(3)直接输入存储器。这种方式是数控系统利用通信方式进行信息交互,即通过对有关参数的设定和相关软件,直接读入在自动编程机上及其他计算机上或网络上编制好的加工程序。目前,在数控机床上常用的通信方式有:
① 串行接口。
② 自动控制专用接口。
③ 网络技术。
输出装置的作用是为操作人员提供必要的信息,如程序代码、切削用量、刀具位置、各种故障信息和操作指示等。常用的输出装置有显示器和打印机等,高档数控系统还可以用图形方式直观地显示输出信息。
3.数控装置
数控装置是数控机床最重要的组成部分,数控机床功能的强弱取决于数控装置。主要由信息的输入、处理和输出三个部分组成。程序载体通过输入装置将加工信息给CNC单元,编译成计算机能识别的信息,由信息处理部分按照控制程序的规定,逐步存储并进行处理后,通过输出单元发出位置和速度指令给伺服系统,以控制机床主运动机构和进给传动机构。
数控机床的辅助动作,如刀具的选择与更换、切削液的启停等能够用可编程序控制器(PLC)进行控制。PLC是用于进行与逻辑运算、顺序动作有关的I/O控制,它由硬件和软件组成。应用于数控机床的PLC分两类:一类是CNC生产厂家为实现数控机床顺序控制,而将CNC和PLC综合设计的内装型(或集成型),这种PLC是CNC装置的一部分;另一类是由专门生产厂家开发的PLC系列产品,即独立型(或外装型)的PLC。
4.伺服系统
伺服系统由伺服驱动电路和伺服驱动电动机组成,包括主轴伺服系统和进给伺服系统。主轴伺服系统的主要作用是实现零件加工的切削运动,其控制量为速度。进给伺服系统的主要作用是实现零件加工的成形运动,其控制量为速度和位置,特点是能灵敏、准确地实现CNC装置的位置和速度指令。每个做进给运动的执行部件都配有一套伺服驱动系统。
伺服系统直接影响数控机床加工的速度、位置、精度、表面粗糙度等。数控机床性能的好坏就取决于伺服驱动系统。
5.位置反馈系统
位置反馈分为伺服电动机的转角位移反馈和数控机床执行机构(工作台)的位移反馈两种,运动部分通过传感器将上述角位移或直线位移转换成电信号,输送给CNC单元,与指令位置进行比较,并由CNC单元发出指令,纠正所产生的误差,适时控制机床的运动位置。
6.机床的机械部件
数控机床的机械结构,除了主运动部件、进给运动部件(如工作台、刀架)、辅助部分(如液压、气动、冷却和润滑部分等)和支撑部件(如床身、立柱)等一般部件外,尚有些特殊部件,如储备刀具的刀库、自动换刀装置(ATC)、自动托盘交换装置等。与普通机床相比,数控机床结构发生了很大的变化,普遍采用了滚珠丝杠、滚动导轨(如图1.3所示),传动轻巧精密,效率更高;用滚动导轨或贴塑导轨消除爬行;采用主轴电机和变速齿轮的变速机构,实现无级变速的同时还减少了变速齿轮的级数,使数控机床的传动系统更为简单;机床的工作台可装有位置反馈装置,传动装置的间隙要尽可能小;由于数控机床的运行速度和加工速度一般都比普通机床高,所以对机床的静态和动态刚度、振动频率等方面要求更高,以适应对数控机床高定位精度和良好控制性能的要求。

1-丝杠;2-滚珠;3-回珠管;4-螺母
图1.3 滚珠丝杠结构示意图
1.3.2 数控机床的分类及应用范围
目前,为了研究数控机床,可从不同的角度对数控机床进行分类。
1.按机床运动轨迹分类
(1)点位控制数控机床。点位控制又称为点到点控制。该系统的特点是只控制机床运动部件(刀具对工件)运动起点和终点坐标点的精确定位。移动过程中不进行切削,对它们定位过程中的运动轨迹及移动速度没有严格要求,各坐标轴之间的运动是不相关的(如图1.4所示)。为了确保准确的定位,点位控制系统在高速运行后,一般采用3级减速,以实现慢速接近定位点并最后准确定位。

图1.4 点位控制
点位控制的数控机床主要用于平面内的孔系,主要有数控钻床、数控坐标镗床、数控弯管机、数控冲剪床、三坐标测量机等,其采用的数控系统称为点位数控系统。随着数控技术的发展和数控系统价格的降低,单纯用于点位控制的数控系统已不多见。
(2)直线控制数控机床。直线切削控制又称为平行切削控制。这类数控机床不仅要求机床运动部件运动起点和终点之间具有准确定位的功能,而且要求实现平行坐标轴的直线切削加工,并且可以设定直线切削加工的进给速度。该系统也可以控制刀具或工作台同时在两个轴向以相同的速度运动,从而沿着与坐标轴成45°的斜线进行加工,如图1.5所示。因此,一般只能加工矩形、台阶形零件。这类数控机床主要有比较简单的数控镗铣床、数控车床、加工中心和数控磨床等。这种机床的数控系统也称为直线控制数控系统。同样,单纯用于直线控制的数控机床也不多见。

图1.5 点位直线控制
(3)轮廓控制数控机床。轮廓控制又称为连续轨迹控制。这类数控机床能够对两个或两个以上坐标轴同时进行控制,不仅能够控制机床移动部件的起点与终点坐标,而且能够精确控制整个加工过程中每一点的速度与位移量,也即控制移动轨迹,将零件加工成一定的轮廓形状,见图1.6所示。

图1.6 轮廓控制
两坐标及两坐标以上的数控铣床(加工中心)、可加工曲面的数控车床、数控磨床、数控齿轮加工机床和各类数控切割机床等均采用轮廓控制方式,它们可以取代各种类型的仿形加工,同时提高了加工精度和加工效率,其相应的数控装置称为轮廓控制数控系统。按同时控制且相互独立的轴数,可以有2轴控制、2.5轴控制和3、4、5轴控制等形式。
① 2轴控制:指的是可以同时控制2轴,但机床轴数也可能多于2轴。主要用于数控车床加工回转曲面或数控铣床加工曲线柱面。如在数控铣床上的X、Y、Z 三个坐标同时控制 X、Y 两个坐标时,可以进行图1.7(a)所示的曲线形状加工。同时控制 X、Z 坐标和Y、Z坐标时,可以加工图1.7(b)所示形状的零件。

图1.7 2轴联动的轮廓加工
② 2.5轴控制:主要用于三轴以上机床的控制,即指两个轴连续控制、第3个轴作周期性的点位或直线控制,从而实现三个坐标轴 X、Y、Z 内的二维控制。如图1.8所示就是采用这种方式用行切法加工的三维空间曲面。

图1.8 2.5轴半联动的曲面加工
③ 3轴控制:一般分为两类,一类是指同时控制 X、Y、Z 三个直线坐标轴联动,这样,刀具在空间的任意方向都可移动,因而能够进行三维的立体加工,比较多的用于数控铣床、加工中心等。如图1.9所示为用球头铣刀铣切三维空间曲面。另一类是除了同时控制X、Y、Z 其中两个直线坐标轴外,还同时控制围绕其中某一直线坐标轴旋转的旋转坐标轴。如车削加工中心,它除了纵向(Z轴)、横向(X轴)两个直线坐标轴联动外,还需同时控制围绕Z轴旋转的主轴(C轴)联动,见图5.6所示。

图1.9 3轴联动的曲面加工控制
④ 4轴控制:是指同时控制四个坐标运动,即在X、Y、Z三个直角坐标轴之外,再加一个旋转坐标轴。同时控制四个坐标的数控机床如图1.10所示,它可以用来加工叶轮或圆柱凸轮。

图1.10 4轴联动的数控机床
⑤ 5轴控制:五轴是指在直线坐标X、Y、Z以外,再加上围绕这些直线坐标旋转的旋转坐标 A、B、C中的两个坐标,形成同时控制五个轴联动。这时,刀具可以给定在空间的任意方向,如图1.11所示,它特别适合加工透平叶片、机翼等更为复杂的空间曲面(如图1.12所示)。

图1.11 5轴联动的加工中心

图1.12 5轴联动的数控加工
2.伺服系统类型的分类
这种分类方法是根据伺服系统测量反馈形式来划分的。
(1)开环伺服系统数控机床。开环伺服系统是不带测量反馈装置的控制系统,如图1.13所示。开环伺服系统的数控机床,采用步进电动机作为伺服驱动执行元件,数控装置将工件加工程序处理后,输出脉冲信号给伺服驱动系统步进驱动器的环形分配器和功率放大器,最终控制相应坐标轴的步进电动机的角位移,再经机械传动链,实现机床运动部件的直线位移,但不检测运动的实际位置,即指令信息单方向传送,并且指令发出后不再反馈回来,故称开环控制。

图1.13 开环伺服系统框图
由此可见,因无位置反馈,开环系统精度(相对闭环系统)不高,其精度主要取决于伺服驱动系统和机械传动机构的性能和精度。但由于开环控制结构简单,调试方便,容易维修,成本较低,仍被广泛应用于精度和速度要求不高的经济型数控和对旧机床的改造上。
(2)闭环伺服系统数控机床。闭环控制系统如图1.14所示,它在机床移动部件的位置上直接装有直线位置检测装置,检测刀具或工作台的实际位移值并将检测到的位移值及时反馈到CNC装置的比较器中,与所要求的位移指令值进行比较,用比较的差值进行控制,直到差值消除为止。可见,闭环控制系统将机械传动链的全部环节都包括在反馈环路之内,其控制精度高。从理论上讲,闭环控制方式的运动精度和定位精度,仅取决于检测装置的精度,而与机械传动的误差无关。但由于位置环内的许多机械传动环节的摩擦特性、刚性、间隙、导轨的低速运动特性及系统的抗振性等都是非线性的,很容易造成系统不稳定,严重时甚至会使伺服系统产生振荡而使机床无法正常进行加工。因此闭环系统的设计、安装和调试都有相当的难度,其对机床的结构刚性、传动部件的间隙及导轨移动的灵敏性等都提出了更高的要求,价格昂贵。

图1.14 闭环伺服系统框图
闭环伺服系统数控机床主要用于一些精度要求很高的镗铣床、超精车床、超精磨床以及较大型的数控机床等。闭环控制数控机床的伺服机构采用直流伺服电动机或交流伺服电动机驱动。
(3)半闭环伺服系统数控机床。半闭环控制系统如图1.15所示,它在开环控制系统的丝杠端头或电动机端头上装有检测装置,通过检测丝杠的角位移(转角)和转速,间接地检测移动部件的实际位移量,然后反馈到CNC装置中进行位置比较,用比较的差值进行控制。由于反馈环内没有包含工作台,故称半闭环控制。半闭环控制精度较闭环控制差,但稳定性好,且由于角位移检测装置比直线位移检测装置的结构更为简单,造价较低,同时由于滚珠丝杠制造精度的提高,丝杠、螺母之间侧隙采用了补偿方法,因此,配备精密滚珠丝杠的半闭环控制系统得到广泛采用。

图1.15 半闭环伺服系统框图
目前采用直线电动机作为伺服驱动元件的数控机床,取消了传动系统中将旋转运动变为直线运动的环节,实现了“零传动”。该传动方式从根本上消除了机械传动环节对精度、刚度、快速性及稳定性的影响,使机床获得更高的定位精度、进给精度和加速度。
3.加工工艺类型的分类
(1)金属切削类数控机床。
① 普通型数控机床。这类数控机床和传统的通用机床一样,指采用车、铣、钻、铰、镗、磨、刨等各种切削工艺的数控机床,如数控车床、数控铣床、数控磨床和数控齿轮加工机床等。而且每一类中又有很多品种,例如数控铣床中就有立铣、卧铣、工具铣、龙门铣等。这类机床的工艺性能和通用机床相似,所不同的是它能加工具有复杂形状的零件。
② 加工中心。这是一种在普通数控机床上加装一个刀具库和自动换刀装置而构成的数控机床。它和普通数控机床的区别是:工件经一次装夹后,数控系统能控制机床自动地更换刀具,连续自动地对工件各加工面进行铣(车)、镗、钻、铰、攻螺纹等多工序加工,故此,有些资料上又称它为多工序数控机床,如(镗铣类)加工中心、车削中心、钻削中心等。
(2)金属成形类数控机床。这类机床指采用挤、冲、压、拉等成形工艺方法加工零件的数控机床,如数控冲床、数控折弯机、数控弯管机、数控回转头压力机等。
(3)数控特种加工机床。数控特种加工机床是指采用电加工技术加工零件的数控机床,即电加工类数控机床。这类机床有数控线(电极)切割机床、数控电火花加工机床、数控火焰切割机、数控激光加工机床等。
(4)其他非加工类型的数控机床。这类机床有数控装配机、数控三坐标测量机、数控对刀仪、数控绘图仪等。
4.数控系统功能水平的分类
数控机床按数控系统功能水平可分为低、中、高三档。就目前的发展水平来看大体可从以下几方面区分,见表l-1。
表1-1 数控机床分类表

这种分类方法,目前在我国用得很多,但没有一个确切的定义。